Recently, a YouTube video has been making the rounds online which shows a rather astounding comparison between two printed models of the US Capitol. Starting with the line “3-D PRINTERS CAN NOW PRINT TWICE AS FAST”, the video shows that one print took four hours to complete, and the other finished in just two hours by virtue of vibration reducing algorithms developed at the University of Michigan. The excitement around this video is understandable; one of the biggest limitations of current 3D printer technology is how long it takes to produce a model of acceptable quality, and if improvements to the software that drives these machines could cut total print time in half, the ramifications would be immense.
In only a few weeks the video racked up tens of thousands of views, and glowing articles popped up with headlines such as: “How to cut 3D print times in half by the University of Michigan” and “University of Michigan professor doubles 3D printing speeds using vibration-mitigating algorithm“. Predictably, our tips line lit up with 3D printer owners who wanted to hear more about the incredible research that promised to double their print speed with nothing more than a firmware update.
The only problem is, the video shows nothing of the sort. What’s more, when pushed for details, the creators of the video are now claiming the same thing.
A Sub-Standard Standard
The first indications that the video might not be quite what it seems can be found in the YouTube comments, where several viewers mentioned that the state of their “Standard Printer” was questionable at best. Intense vibrations are clearly visible in the printer’s belts, and issues with bed adhesion on the final printed model hint at either a poorly leveled bed or incorrectly calibrated Z axis. For those who have spent a bit more time than they may care to admit tuning and calibrating 3D printers, these issues are red flags that the machine is in a poor state.
It comes as no surprise when the video then goes on to show how prints on this machine fail as the acceleration settings are gradually increased, eventually ending up in a comically lopsided building. The severe layer shifting shown is again an obvious indicator that the printer’s belts were not correctly tensioned at the beginning of the test.
To anyone who has printing experience, it’s clear that the “Standard Print” demonstrated in the video is a poor metric by which to measure the performance of desktop 3D printing.
Replicating The Experiment
If the condition of the printer used in the “Standard Print” is in question, the next logical step is to attempt to replicate the experiment shown in the video and find how long it takes on a properly tuned 3D printer. Unfortunately, no information was given as to the model used, the scale it was printed at, the layer height, or infill percentage. If the condition of the printer itself was the first red flag in the video, the omission of this critical information is certainly the second. Had the video simply listed this information in the description, anyone with a 3D printer at home could have independently verified the claims made.
Luckily the model itself was not very difficult to identify. A quick search on Thingiverse found “The Capitol – Legislative“, part of MakerBot’s “Structures of Government” collection. But the size of the model was clearly much larger than what was shown in the video; the next step would be finding the scale factor used during printing.
Learning that the printer used in the video was a HICTOP brand clone of the Prusa i3, determining scale was simply a matter of comparing the apparent size of identifiable parts of the machine to the printing model. Knowing the heater block on the HICTOP printer is 10 mm thick, a particularly close view of the print from the side presented the perfect opportunity.
As the height from the top of the steps to the peak of the front portico appeared to be approximately 10 mm, the scale of the model could be adjusted in the slicer until the desired dimension was reached. In this way, it was determined that the scale of the model in the Michigan video was not more than 60%.
Infill was then estimated to be approximately 15 – 20% by comparing the slicer’s layer view at varying infill percentages with that of the in-progress print in the video.
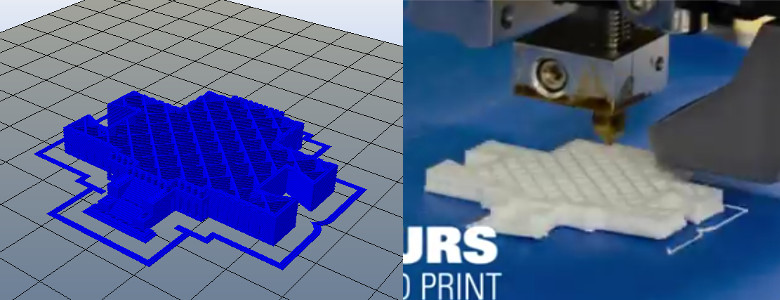
With the model, scale, and infill now known within a reasonable margin of error, the only question left was which layer height was used. Judging by the rather rough surface quality, .2 mm layers seemed likely. The model was then printed with these settings, and the process timed to see how it would compare to the two examples given in the Michigan video.
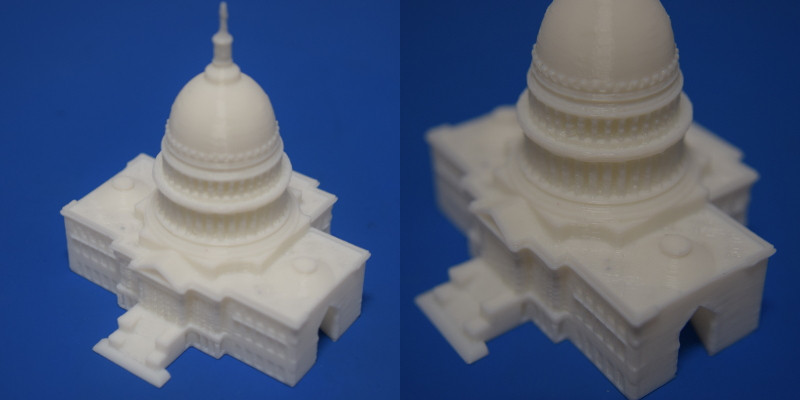
The model was printed in 1 hour and 20 minutes, nearly half the time required for the “accelerated” print demonstrated in the video, and nearly 4 times faster than what was given for the “Standard Print”. Something clearly didn’t add up.
Looking For Answers
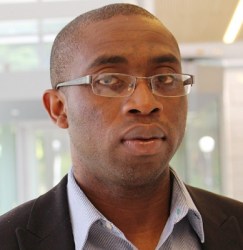
There was certainly a margin of error in the estimations of scale and infill, but not enough to account for such a huge discrepancy between our experiment and what was shown in the original video. With our video evidence and real-world testing in hand, we reached out to Professor Chinedum Okwudire to shed some light on the situation.
Professor Okwudire agreed that transparency and peer-review were critical aspects of the scientific process, and true to his word he provided us with a highly detailed statement as to the nature of the original YouTube video, the team’s research, and how they believe it fits into the current state of the art in desktop 3D printing.
At the core of his argument Professor Okwudire asserts that despite the clear language used in the video and associated press coverage, the demonstration was only meant to portray the results his team achieved within the narrow scope of their research; and not to be taken as a claim that this technology would necessarily produce the same performance improvements under different circumstances:
“A few people seem to misconstrue our work (and the 4 hr case study presented in our video) as showing the fastest printing speed of the Capitol part by ‘standard’ desktop printers. This is a very wrong understanding. Print time highly depends on the printer and the parameters used for the print.”
Further, Professor Okwudire says that the “Standard Print” was not meant to be taken as a best case scenario. In fact, quite the opposite. In the context of this research, “Standard Print” is taken to mean a poorly maintained machine, printing at minimal speed, and operated by a novice user:
“The reason is because we found out that the average non-technical user of 3D printers tends to be conservative about print speeds and accelerations. We found out from many blogs that, in order to avoid failed parts or poor surface quality, people commonly use speeds around 40 mm/s and/or accelerations around 1 m/s^2 on highly-vibratory printers like HICTOP Prusa i3. So even though, with trial and error, parts may be printed at higher speeds and accelerations without failure, many non-technical users mention on blogs that they prefer to be conservative in order to ensure that they always get reliable prints.”
Repeating the Test
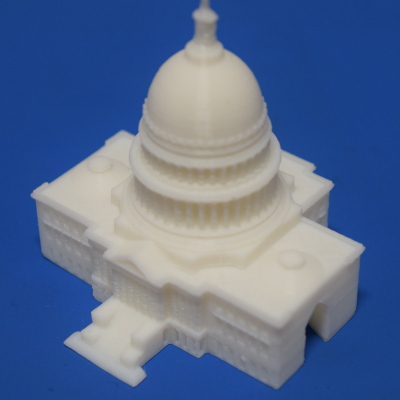
In response to our request, Professor Okwudire provided us with the scale, infill, and layer height used in the video. Our estimates of scale and infill were both within 10%, certainly not enough of an error to create a significant difference in print time. However, the layer height used in the video was given as .1 mm compared to the .2 mm we tested at, which would have a significant impact on print time. In the name of due diligence, we re-ran the print with the precise settings provided.
Using the same parameters as the test video, the print completed within minutes of their “accelerated” print, further strengthening or initial impression of the video. The “Standard Print” is anything but, and the “Accelerated Print” is the performance you should expect from a properly configured and maintained printer.
A more accurate description of what the University of Michigan has demonstrated in their video is a vibration compensation algorithm able to overcome the shortcomings of flimsy or improperly configured printers. In fairness, this may well be a valuable avenue of research as manufacturers try to drive the cost of 3D printers ever lower, but it is surely not an algorithm that doubles the speed of 3D printing.
Sensationalism Vs Science
To the credit of Professor Okwudire and his team, Hackaday received in a very timely manner an exceptionally thorough document detailing the conditions of their experiments and scope of their research. From these documents it’s clear that the original video posted to YouTube is not false in the sense that it does indeed show that under very specific circumstances the time required to print the model is reduced by half.
That being said, the clearly misleading wording used in the video, the intentionally hindered software and hardware conditions used as a baseline, and the absence of independently verifiable parameters for their “Standard Print” control are impossible to ignore. It’s hard to believe that the creators of this video did not intentionally craft it in such a way as to sensationalize the results achieved in the exceptionally narrow scope covered by this experiment.
As a more widely relatable example, imagine a YouTube video that purported to show a method of doubling a car’s fuel economy. The video starts by showing a decades old clunker lurching down the road, backfiring and belching smoke with an indicated efficiency of 8 miles per gallon; followed by the same vehicle after a tune-up and repairs, running visibly better and now managing 16 miles per gallon. In both examples, the demonstration starts from an unreasonably poor position, introduces improvements, and yet still ends with a result that is no better than a more modern or better constructed specimen.
Professor Okwudire maintains that the algorithm being developed at the University of Michigan can potentially double the print speeds of a 3D printer, assuming the printer is functioning poorly to begin with. It has yet to be demonstrated that similar gains are possible on machines which are not currently suffering from mechanical issues, though there is certainly the potential for improvement. We, along with the 3D printing community as a whole, eagerly await an expanded and more transparent study of this technology and its potential use under more reasonable conditions.
If you find the concept of peer review fascinating, consider lending a hand as a Peer Reviewer of our own journal. Yesterday we announced the Hackaday Journal of What You Don’t Know and we’re looking for submissions, Associate Editors, and Peer Reviewers.
“Seeing is believing” especially for a visually oriented species.
Despite my many requests for Tom to share the full transcript of my response, he has declined to. So I have decided to share it here for the benefit of people who want to get both sides of the story, without Tom’s spin: https://umich.box.com/s/wrhibd9t73tol4ndw6aaacpuoo8xhs0v
I don’t have much time to visit blogs so I will likely not visit this site again or post any more clarifications. If you have any questions about our work, feel free to email me at: okwudire@umich.edu. I’m very happy to provide more clarifications. This is what we always do as academics.
Tufte has a name for presentations that fine tune their verbiage and data selections – ‘Cherry Picking’ – that said, I do find their research worthwhile and would actually have looked at it (I will now), but the drivel I saw going around about doubling printing speed I discounted and ignored :-(
I love these kinds of smack downs; they are irrefutable. A lot of words to say “this guy is full of sh!t”, but it is so much better somehow. Good article!
It isn’t exactly a “smack-down” to admit they were being accurate and that the audience misunderstood the experiment.
I mean, Tesla was well known to give sensationalist demonstrations where he played tricks on the audience and made them believe his inventions were other than they were. Does he get the same treatment, by these same people? Of course not, they were told he’s an Authority!
Yeah, Jake, not even close to being “this guy is full of sh!t”. You want that, go view about every third Kickstarter.
Nardi was presenting a reasonable back-and-fourth with Professor Okwudire, seeming to point out ways that the video could be improved, and made clearer.
Then, suddenly, in the last three paragraphs Nardi goes off the rails accusing the authors of being “intentionally” “misleading” and “crafting” a “sensationalized” video. Pretty strong language given Tom’s overall complaints.
Further, there’s no need to fabricate a “strawman” argument with the imaginary clunker car. The discussion focused on the 3D- printer itself is clear enough.
What else would you call the video then? After going back and forth with prof, the claims made about the “standard” printer obviously don’t hold up.
The only real options were that the video was made in error (maybe they simply neglected to add the necessary qualifying info, or the PR department ran with an idea they didn’t fully grasp) or that it was intentionally made to make the claims sound better. Professor basically confirms the second case with his comments, since he still maintains that the video is fine as-is.
Just look at all the comments the professor has made just on this page. There’s a whole list of qualifications he’s now mentioning about how they came up with the “standard” print performance that simply aren’t in the video or even the description of it. Why? If they are so important that he feels the need to come here and respond to basically every comment, shouldn’t he have made sure that info was represented to begin with?
At the absolute least, the video should have clarified that they consider a “standard” print to be slower than ideal because the user might be a novice. That’s a HUGE generalization.
The video says “3d printers can now print twice as fast”, not “this 3d printer can print twice as fast”, or even “some 3d printers can now print twice as fast”.
Personally, I think the first case is probably what happened. PR department made the video and they didn’t take the time to make sure they were explaining the test fully. If professor had simply said as much, then this article would probably have gone a different way. But when he decided to try and use mental gymnastics to explain the video, it became something else.
For the record: I (nothing to do with Michigan (*) think that b-splines are the way of the future for 3D printers.
* B-splines can be quickly calculated in an incremental way.
* Full control over accelleration.
* we should move from STL to a format that allows curved surfaces. Instead of approximating a cylinder with hundreds of small triangles (if you want to avoid artefacts) you approximate it with 4 curved spline surfaces. Perfectly smooth at any scale!
* We should move to calculating the splines in the slicer program.
* We already embed lots of stuff like “max speed” into the gcode, why should something like “max acceleration” be hidden in the firmware?
(*) Except that I live in a country called the Netherlands, often incorrectly called Holland, and that there is a town called Holland in Michigan.
So, inspired by your comment, I went to look up vector graphics as a possible analogue to solving this problem. Of course, I veered way off because now I’m looking at Wikis of Minkowski space. Thank you and damn you at the same time? :-D
Do it the POV-ray way.
For someone who has worked more than his fair share with low-level Marlin, I would like to address some of your points:
– If you’re using curves in the firmware, you’re out of luck. Using a standard cartesian 3D-printer, you will eventually have do divide your curve into “hundreds of small segments”. So you’ll run into that problem sooner or later.
– Max acceleration is not hidden in firmware (at least not in Marlin). It can be configured in G-code and Slic3r even has a setting for it.
But yes, your other points might be valid. It would be great to calculate more in the slic3r, as the machines are typically run using very inferior microcontrollers (Atmegas). The problem is that you might run into problems when it comes to your specific machine, but that’s just trimming. The problem with doing it in the slicer is that you will not be able to use someone elses G-code in your machine as well. I see it as a smaller problem however, since you will most often slice your files yourself.
> If you’re using curves in the firmware, you’re out of luck. Using a standard cartesian 3D-printer, you will eventually have do divide your curve into “hundreds of small segments”. So you’ll run into that problem sooner or later.
WRONG! When you’re using curves in firmware which drives steppers directly, you can calculate a curve down to each step and you don’t need to split it into segments. It’s standard in all curve-into-pixels algorithms, it’s solved problem which is given as standard solution in graphics pogramming courses. Also one of standard gcode primitves is circle, which also can be easily calculated step-by-step in firmware. But STL requires to split everything into triangles which are then rendered layer-by-layer as segments.
I think his point is that the nature of stepper motors is you have to give discreet steps for each move, no matter how small the move. Yes, you could increase the number of moves to get a finer resolution, but you can’t get rid of them. What you are talking about would only work with servo motors, because the speed can be continuously changed so that it is a smooth curve.
You must discretise the curve but that’s not relevant because the stepper motor does not move then come to a halt between each step; it runs continuously. The system still has mass which must be accelerated/decelerated, and if you place the steps on curves which carefully control acceleration, that has significant benefits to smoothness, regardless of the drive.
The need for rigid (and definitely not underdamped!) kinematics with high acceleration is unavoidable anyway, because one still needs to be able to do a sharp edge in a model. B-Splines are great for curves but things are not all-curves.
Note that the most common curve is a circle, and circles are supported by G-code. The main reason we have nasty segmented curves in 3D printing is because of the triangles in STL and not because of any limitation of G-code or stepper controllers.
Yeah, for steppers it makes sense to evaluate the curve at each step instead of at specific distances.
For servomotors, it makes sense to evaluate the curve at each servo loop iteration, against the current timestamp.
Splitting the curve to fixed length segments is just a poor approximation for either of those, even though it does provide almost as good results at less coding effort.
Different comment: It sounds to me as if they actually tried to make it look better than that it is. Professor whats-his-name made the smart decision to simply tell the truth instead of sticking with the implied claims.
Is that news? The PR departments likes to make (sometimes extremely) extrapolated claims that while technically true only for a subset of cases. And sometimes they even lie.
So, basically what these algorithms are is an overly-complex solution to a simple problem.
“Hey, is that 3D printer you did no research on and barely know how to use not printing like it should? Fear not, you don’t need to do any, y’know, simple maintenance or adjustments, that crap’s for chumps. Just upload this measly little software patch and your crummy, out-of-shape printer will be just as capable as if you’d, y’know, done simple maintenance or made some quick adjustments. It’s that easy!”
“SHUT UP AND TAKE MY MONEY!”
In all seriousness, I’m totally on board with exploring where this anti-backlash/vibration business with the GCode can take us, but this is a very clumsy first step on that road.
A software patch that tightens up the slack belts and levels the bed on a $140 printer would be a interesting bit of code.
It’s kind of sad that researchers are under ever mounting pressure to produce “sensational” results. Problem is: you can’t force the universe to comply. Science is slow and tedious and the closest that can be achieved is often sensationalist. It happens a lot everywhere in science and the main reason is that the system is structured in a way to emphasize competition. The prof might be out of a job if he fails his tenure review etc. Under these conditions, who would honestly expect that cherry picking isn’t normal?
As far as the vibration cancellation goes: even a well tuned printer would benefit. The shitty printer vibrates at lower speeds, but at higher speeds a better printer will also vibrate. So you could then double the speed of this, for example.
Your test is kind of meaningless. Nobody would doubt that there are differences in print time between printers. My TAZ 4 is half as fast as my Printrbot for equal quality. So what? In any case, both printers could maybe go faster with the Michigan algorithm… I just wonder how practical the whole thing is and how well it would work under real world conditions.
I think it’s more than just an over emphasise on competition but the high demand on professors to draw in funds (certainly in the UK, having had friends going through post-grad research path), be that via research grants, overseas students, industry funding or whatever – money talks.
This all culminates in a general disinclination towards reproducing other’s results (a key part in science) because there’s no funding and an over-sensationalism of results. And we’re not talking of necessarily telling fibs, such as the above, but being, er, “economical with the truth” in order to garner publication in the general press (because let’s face it, in a world of reality stars and Hollywood films, this is hardly an engrossing subject for the wider world).
Richard Feynman wrote (in an appendix to one of his books IIRC) about people not repeating the results of previous papers, because; little funding for repeating an experiment, or it may be considered dishonorable to challenge the results of a “famous” scientist, or such. So, if there is a flaw in the original outcome, that flaw will be a part of all research that builds off the original experiment. The downstream experiments may not even be published if they “fail”, which if they were published, it could trigger an investigation into the original experiment(s).
“Your test is kind of meaningless. Nobody would doubt that there are differences in print time between printers.”
I don’t know about [Tom Nardi] but several hackaday authors who have covered 3D printing have mentioned having printers based on the Prusa i3 just like the one in the video is. True, different manufacturers will result in differences in the printer, but assuming [Tom] did use a printer of the same design then the test does have meaning.
Only in the sense that what they did was not pushing the envelope in terms of speed possible with a tuned printer. But the claim in the video is: vibration correction can push a fixed printer to twice its speed. And that might be 40 mm/s for on printer and 200 mm/s for another. They don’t claim that their untuned printer was already at the leading edge.
The analysis presented here really only critiques the ‘control’ case shown in the video, and not the effect of the vibration-compensation algorithm. Sure, you can do that and maybe get a clearer view of some of the claims others made about the video, but you need to get your hands on the algorithm and run your own tests if you really want to evaluate it for yourself. So, this analysis feels like it falls short of a real peer review. The other issue I see is confusion about what precisely is a good target for peer review in the age of viral videos. The answer is probably not the hype generated by a video or comments posted to the video, or even the video itself. Another question is who is responsible for making a high-quality peer review possible? Is it the staff of hackaday who should be expected to chase down an author and convince them to share details of the processes used in the video? That feels like it places a large burden on the peer reviewers, and I think it potentially aggrandizes those seeking publicity through deception (think of all the hits that ‘free-energy’ videos get but yet without providing details that make the effects replicable). Really, I think it should be the authors responsibility to provide details.
Isn’t that exactly the point? We have to be critical of the control, because that’s where the 2x claim is coming from. But the control is BS, and they knew that when they made the video, which is why no info was given. If the video was honest enough to give the size and layer height of the model, anyone who saw the video could try it on their own printer and see it was way off the mark.
For a video that VERY CLEARLY states they are doubling the speed of 3D printing, they had to make sure their starting point was as slow as possible. That’s misleading, plain and simple.
The doubled the speed of printing for this one particular printer, but who cares? It was running dog slow to begin with. I wonder how much faster they could have run the thing if they just tightened up the belts?
“For a video that VERY CLEARLY states they are doubling the speed of 3D printing, they had to make sure their starting point was as slow as possible. That’s misleading, plain and simple.”
From a science perspective, to state that their algorithm doubles the speed of 3d printing they would need to show that their algorithm works under a multitude of varying conditions. Good printers, bad printers, good maintenance, bad maintenance ect.
You’re adding an absolute. You say they said they are “doubling the speed of 3D printing,” which they did. But you’re doing your analysis as if they had said, “doubling the speed of all 3D printing,” which is not a claim they made.
If our language is sloppy enough to add phantom absolutes it gets really easy to see people as being “wrong,” even professionals doing legit research.
I think you are really taking the wrong message from the research.
If specific software algorithms can reduce the importance of a well maintained machine then they can improve the quality or speed for the large number of people that do have crappy and poorly maintained machines. If it works generally on bad printers and not just on their specific machine then that does have value in it’s own right.
Perhaps the gains will translate to a good machine too, perhaps they won’t. But that is a different question.
Maybe that’s the goal of the research, at least it seems that the professor is now claiming as much when pushed for details, but it definitely isn’t what the video shows. This article calls BS on the video which is making the rounds, not the research itself.
It even ends with the same message that you’re making in this comment: Maybe it works on non-broken printers, and maybe it doesn’t. If they had made a video that answered that question, we wouldn’t be reading this right now.
Of course it works on “non-broken” printers. Why wouldn’t it?!?
Without them showing data for a series of printers in various conditions, we can’t tell what the benefits. My guess is that the benefits at higher quality levels in the series would show a power law curve (i.e. 2X at the low quality end and slightly greater than 1X at the high quality range).
We did not “change our claims” when pushed for details. Instead, in our detailed response to Hackaday, we showed them many resources that we had put out with the Video giving context to our claims. Unfortunately, it does not seem like they had not done their research before approaching us – it appears that they just watched the video and reached their own conclusion. Now they want to claim that they made us change our claims. This is why they don’t want to release the full transcript of my response. It will show that their so-called peer review article was a fool’s errand. This is so disingenuous.
How wonderful it is to live in such an age of scientific progress that peer review is extended to youtube videos. Sarcasm aside, this is really cool research. And, as others in the comments have pointed out, this doesn’t really address the researchers claims in any substantial way — they found a new method to double print speed.
Admittedly, it was tested with a poorly maintained printer. That’s how science works, it starts with a clear problem (vibration from a poorly maintained printer) and solves that. Then, the same methods can be applied to other printers. That’s how science advances – one small step at a time, solving one very specific problem, and adding to the pool of knowledge.
You’ve got to be kidding. What science works that way?
That’s like saying the first step to curing cancer is to cure somebody who has the common cold. The printer they used in their control didn’t need some advanced algorithm, it needed somebody to tighten the belts and level the bed. They created a problem, and then “solved” it in the most complicated way possible. If that’s your idea of science, I don’t know what to tell you…
There’s no reason that this same algorithm couldn’t be demonstrated with a properly working printer instead of a broken one, outside of the fact that the results wouldn’t have been exciting (or potentially not even worth the effort, we simply don’t know).
Look at the space shuttle. First steps toward that were an idiot with a large hill and a hang glider, or maybe someone tying a cow to a hot air balloon. Or cancer, since you brought that up. It’s not a single disease, so curing it will involve dozens or hundreds of solutions that each individually look pretty insignificant. And the vast majority of that work won’t be cheered on by marathoners with pink ribbons. If you just want to see the one cool trick that will cure cancer or double your print speeds you want magic, not science.
You’re introducing apples and oranges to try to prove that a small part of the problem is not worth solving first, it doesn’t seem very convincing. Surely poor print quality is a real problem in the 3d printing world, and it is often caused by operator error or poorly maintained machines.
The existence of cancer does not in any way diminish the usefulness of improving the quality of 3d prints in the presence of operator error and poorly maintained equipment.
+1
Eh, it’s a youtube publicity generating video produced by the university multimedia department, not a peer reviewed journal entry written by the professor. The print details will surely be included in the paper where it belongs.
Their algorithm did increase the performance of the build on that shitty printer, that’s very valuable in many ways. I would love to see if that translates to better printers, vibration is a problem for all printers at some speed..
I very much agree. On point. The multimedia department probably is also quite involved in hyping these stories.
How about a “Hack-a-Claim” section devoted to critic of internet posts and urban legends?
I smell a Snopes partnership.
… Starting with many of the in-house Hackaday generated articles.
“if improvements to the software that drives these machines could cut total print time in half, the ramifications would be immense.”
No they wouldn’t. That’s just unfounded sensationalism.
Don’t get me wrong, 3d printing it awesome. In the hobbyist environment it makes all sorts of results possible that would otherwise be unavailable or at least impractical. In the professional environment it changes the turn-around time on prototypes from days to hours.
Halving that print time would be nice but the ramifications wouldn’t be “immense”. Hobbyists aren’t going to start producing things in 1 hour that they wouldn’t have produced anyway even if it took 2. Likewise professionals aren’t just “winging it”, going directly to production with things they would chose to prototype first if only they could do so in half the time. Nothing really new would come from that change of speed and that’s why it’s ramifications are not immense.
To get ramifications that are “immense” you need to pioneer the printing of new materials or merge the printer with a pick and place machine allowing it to produce active devices or something like that. To get “immense ramifications” out of a mere increase in speed you need to start matching the rates of traditional production methods which means many more than just 2 times the speed are required. (not gonna happen) Besides, even if you could print that fast you would also need to increase the reliability before 3d printing would be viable for mass production.
Yah, I know, nitpickey. But… 3d printing is sooooo over sensationalized I think many people, once they experience the let down after the hype lose track of the fact that what 3d printing actually is good for is still enough to be really cool!
CONSUMER 3D printing, sure. The earliest desktop “printers” were pretty jank too.
Now, consider the high-end commercial 3D printers, tuned to a perfect set-it-and-forget-it with print finishing in full color in only a few minutes.Too expensive for consumers, but so were laser printers once.
Ok. I just considered it. Nope. I still don’t see “immense” ramifications, not from a speed upgrade. In a factory an injection molding machine would still make dozens of parts in those same few minutes.
That doesn’t seem to be what you are talking about though. If you are talking about “set and forget high quality printers at reasonable consumer prices then sure, that would be “immense”. What does that have to do with a speed upgrade though? That’s price, reliability and ease of use. Fix those three things and sure, it could be revolutionary because ordinary people could print their own stuff instead of buying it. Granted, doing it faster would be better but that’s true with or without the speed upgrade. If the machines were reliable enough one could just walk away from but still slow people would just have to plan ahead a little better.
Sounds like people want 3D printers to follow the same development path as regular printers.
Why would you write an article like this and not bother to read the research paper?
https://umich.app.box.com/s/n9cvs27ckehdr64gzv5igtmboykymgk6
It’s free to read, and would have answered many of your questions (printer type, print object size, etc.). This Hackaday article fabricated a mystery, and unfairly led at least one of it’s readers to conclude “this guy is full of sh!t.” That negative spin makes the Hackaday article more sensational, but it’s not responsible.
Uh oh guys, looks like we found the UoM staffer…
The only information that doc clearly shows is the printer type, which doesn’t seem was up for debate. Nothing about infill or layer height, which is most important factors in repeating the control.
It doesn’t directly give the scale either, as far as I can tell the only concrete information about the model in this doc is a picture of the capitol that shows it’s 47 mm long, which naturally means it doesn’t come up if you search the text; not exactly the most helpful formatting.
Point is, AT LEAST the scale and layer height should have been given right in the video. Even somebody who’s only used a 3D printer once or twice can understand how critical those pieces of information are in determining the speed of a print.
Why try to imply he’s biased? I’m don’t work there, and I agree with him.
Maybe it is possible it is even true!
In our detailed response to them, we explained why we did not think it important to add information about the part printed. We explained that true replication of the work is not really dependent on the part printed. The algorithm improves the printer not the part printed. Things like layer height, in fill and scale only scale the print time proportionally. What is more important is printing the same part on the same printer with and without vibration compensation. Of course, this fact is lost on them. They take the part, print it on another printer that may have vastly different vibration characteristics and then compare it to a part printed on another printer. They clearly do not understand what is important here. If they’d release the full statement, others can read our response and judge for themselves.
If you want to accurately control your printer at double speed, you need four times the acceleration for the same cornering ability, and a frame and gantry that can handle the extra force.
As for oscillation, you just need to keep jerk (derivative of acceleration) down to an acceptable level. I’m not sure if printers actually do anything special for handling forces during acceleration and cornering, but they really should.
(controlling jerk sounds easy but isn’t)
Controlling jerks are never easy. They are usually a pain to be around.
Don’t try to control them, just find the door.
If what they claim is right, can you run a test with twice the acceleration, using their “bspline” engineering stuff and get a piece in 1h only on your top-notch printer ?
For me, that would conclude if there technic is reproducible and efficient, proving that your printer does it well in 2 hours only does not (in)validate their claim, as I understand it.
No, you’d don’t double your print speed.
You compensate for vibration. How much improvement you would get would depend on how much you’re being slowed down by vibration. It would have the least impact on the most accurately setup and tuned machine.
That’s why this type of research is typically done on machines that are NOT accurately setup and tuned.
It is the same with any other type of industrial vibration damping research; you don’t want to research how to reduce the vibration of machines that don’t vibrate, you want to reduce the vibration of machines that DO vibrate!
I agree with your point – and we already showed this to them in our detailed response (which they conveniently chose to omit). I agree that the HICTOP printer is a low-end printer. I also agree that the belts could perhaps be tightened some more and maybe marginally improve its performance. However, the idea of the specific case shown in the video is that a lay (non-technical) person buys a cheap printer like HICTOP Prusa i3 for about $300. They assemble it as best they can (because it a self-assembled printer). They are likely not to do the best job of tightening the belts. However, they install a firmware upgrade and all of a sudden they can print at 120 mm/s and 50,000 mm/s^2 accelerations without losing print quality when before they would carefully stay around 1,000 mm/s^2 and low print speeds to avoid failures. I think they’d be pretty happy with this. Moreover, they do not have to worry about tightening belts every time they print – i.e., low maintenance. Of course, it does not mean that one could not take a much better tuned printer, add the algorithm and show large improvements – we’ve already shown this on Taz 6, for instance. They want to take a case study made with the lay user in mind and claim that we were being deceitful. We posted the video for a lay person and we added context in our paper and other articles we put out to explain more fine details to the techies.
This article is a hit job. The author has cherry picked my words. He should post my detailed response so that everyone can judge for themselves. Otherwise, I will post his email to us and our detailed response to him to expose him for what he is. Tom, please post my full response not your cherry picked version. I showed you our results where we have printed at 120 mm/s speed and 50,000 mm/s^2 acceleration on a printer that could not go more that 3,000 mm/s^2 acceleration without our software. The result was a print time of 1 hr 27 minutes. Did you print your part on a HICTOP Prusa i3. Remember that vibration problems vary depending on the printer. Post my full comments!!
This article is a critique of the video posted to YouTube on November 1st, 2017. Research conducted since that time and not included in the video are immaterial to the argument presented here, as it is simply beyond the scope of the discussion.
As stated several times in the article, the research itself is promising, and we are eager to see more. We would be more than happy to cover the latest developments in your research in a future article.
So would you say the article only portrays the critique of the results within the very narrow scope of a youtube video, and is not a claim that this research would necessarily be misrepresented on different websites?
Tom, your article is not just a critique of the video – it makes some general claims about the research. What does this statement mean? “It has yet to be demonstrated that similar gains are possible on machines which are not currently suffering from mechanical issues, though there is certainly the potential for improvement. ” We showed you results on Taz 6. We showed you that these results have been out there along with the video. We also showed you results on the HICTOP where we have reached 120 mm/s and 5 g accelerations. However, you still make this false claim. Actually, the claim is not false it’s just misleading. Why should a vibration compensation algorithm be used on a printer without vibration (mechanical) problems? I think, by your statement, what you are suggesting is that the algorithm gives significant benefits only if the vibration problems are caused by mechanical negligence (or intentional mistuning) – which is a falsehood. I’m not sure why you won’t put out the full transcript of our response. I give you the permission to. Of course, I can put it out myself but I am giving you the chance to if you have nothing to hide. If this is your notion of peer review – I think we have a problem
This is typical around here, sorry to say; the users also attack people who make videos about how to generate electricity “for free” (as in, without spending money) as promoting perpetual motion.
There is a culture around here of “defending science” by having arrogant laypeople make confused and ignorant analysis of media reports from a science page, or deciding that people’s ideas are “impossible” or “proven wrong.”
Thank you so much Chinedum Okwudire for standing up to them, for standing up for the scientific process!
Thank you very much, rubypanther. I really took them seriously and provided a very gracious response to them (despite a very accusatory email from them) explaining in detail that a journal article and other articles were put out with the video to give more context – basically, I showed them that we had nothing to hide. I won’t have bothered to respond to this hit job article if it was just randomly put out there – I have better things to do. However, why I am so disappointed is that even after treating him with respect and taking time to explain to them, they still went around to put out this hit job article. They don’t even seem to know the difference between a 100 second video and a scholarly article. If one watches a pharmaceutical commercial on TV presenting a case study won’t they understand that they need to look into the details to understand the full context and that the result may vary from patient to patient? How can one give proper context in a 100 second video – its just a soundbite. That is why we provided the details. Anyway, I should just let them go ahead with their shenanigans. I think I’ve spent a bit too much time responding to them. I’ll just continue to work on the algorithm and let people test it and see for themselves. The proof of the pudding is in the eating. We have already tested it with excellent results on a couple of printers – and, of course, the result varies depending on the printer – but the 2x number is a good ballpark number.
I gave a detailed response also explaining the Youtube video and the fact that a lot of details were put out together with the video to give the reader/viewer more context. To conveniently omitted those details. If he has nothing to hide, he should post my entire response for everyone to read and judge. I have no problem with him posting my full response not his cherry picked version.
Moreover, Tom, you have not answered my question. Did you print your part on the HICTOP Prusa i3? Remember that there are many versions of Prusa i3. Please show the results on HICTOP Prusa i3. In fact, if you want to be fair, you should print on the exact version of HICTOP Prusa i3 we used (after you make whatever mechanical adjustments you think need to be made). The printer we bought almost two years ago may be different from the ones currently sold on the market – they may have improved. As many have pointed out, your argument is fallacious if you take another printer and compare with ours. Vibration behavior is not uniform. We explained all this in detail – please put out my detailed response.
BTW: Tom made it look like we did not discuss results on other better printers. In our detailed response, we presented him with preliminary results obtained on a brand new Lulzbot Taz 6 (with factory tightened belts and all). The default acceleration on the Taz 6 (set from the factory) was 0.5 m/s^2. This is because, despite the tightened belts, the printer still suffers from serious vibration issues because it has a large print volume and heavy nozzle. We easily raised the acceleration by 20x to 10 m/s^2 by using our algorithm (and we can do even more – this was just our first, rough, pass). We have put this information out there on Youtube at the same time the video was released (see: https://umich.box.com/s/ram468peq4a3wxu0hl9jdusvphj4z0gi) However, he claims in his hit job article that: “It has yet to be demonstrated that similar gains are possible on machines which are not currently suffering from mechanical issues…” If a $2500 Lulzbot Taz 6 is not a high-end desktop printer, I’m not sure what is. It is obvious that if the printer does not have vibration issues our software cannot help but it is wrong to suggest that vibration issues are purely a function of poor maintenance or a problem with the lowest-end printers. I designed $400,000 CNC machines that suffer from serious vibration issues and would benefit from out algorithm. In fact, the idea to create this algorithm did not come from problems with low-end 3D printers, it came from my experience with the $400,000 machine we designed when I worked in industry. Please put out my full response!
Soo…
I really think the research is important. Finding math methods for improving sub-standard machines, be it vibration or other form of control, is always good and very important. Not all machines will be high-precision and well mantained ones. If software can compensate for a lot of the machine´s weaknesses, that is a very good thing.
But, considering we should be talking about results for research / science :
The youtube video, that is what many people will see first ( and only ) is just generic. Why doesn´t it say in the description that it shows a way for improving quality in bad printers ? Not as something implied, but as something very explicitly described, as it ( improving the quality in common printers ) seems to be the target of the research ?
More, why doesn´t the video and its description describe clearly what it is and is not ? Many of your later explainings make sense, but why are they not in the video ? Many people will not read or have access to the rest of the article.
The article didn´t discredit your original research. I´m sure many people ( I´m one of them ) saw it as a good improvement. Compensating for vibration, even if not that big in a perfectly adjusted printer, can signify some important gain when, for example, one needs to squeeze a last bit of performance / quality in a print. When all the mechanical improvements have already been made, this software improvement could make a diference.
What they seem to complain, and in that I would agree with them, is that throwing a video “out there”, without the proper quality explanations, gets ugly if justified ” the marketing department did it”.
You seem a reasonable person, from your responses to Tom and your posts here. So, why not fix this the better way ? Redo and repost the video, including in it and in the descriptions the important details that were left out of the original one ( and delete the old, incomplete video ) Make a scientific quality video, without loose ends, so that it cannot be taken for what it isn´t., and that also demonstrates the usefulness of your research.
You are mistaken… It is wrong to claim that the algorithm is only for “bad printers”. Is Taz 6 a “bad printer”? Please read my responses and see that various levels of machines suffer from vibration problems. Why focus on a video and not the real science. Are people afraid of reading? This is why “fake news” prevails in today’s world – people don’t want to read and critically evaluate things beyond 100 second videos or soundbites. We posted all kinds of articles for people read. We tried to put a lot of explanations on the video but the multimedia people said that it’s not effective to fill a short video with a lot of details. The average viewer will be overloaded. If you are the kind of person that wants details then please read. I never said the “marketing department did it.” What I did was to point out that details were provided along with the video. A 100 s video can always be taken for what it isn’t if people don’t care to read.
Hackaday readers are certainly intelligent enough to click past the youtube video and read an article or two to get to the scientific results. It seems whoever wrote this article either vastly underestimated the attention span of readers, or intentionally omitted information; most of the claims made in this article (and the comments) seems to be addressed on the researchers website. Besides that, it sounds like the author intentionally omitted parts of an email from the researchers that answered the rest of the questions here. That is far more than misleading than the original video. Maybe the “hack” in hackaday refers to the quality of the articles now?
Framing the standard print as sub-standard is rooted on misconceptions and not carefully watching the video. The so-called “peer review” of Tom Nardi is not a peer review. His motivation is very questionable. It reads to me as if he wants to make this page viral so that he can lure more traffic into this page.
1. Our experiments never failed from what is seen on the video. The timing belt vibrates on that video, but the printer never fails in that direction. It actually fails (skips the stepper counts) in the build platform direction. The video never shows how that belt is doing, so I don’t know how anyone can claim “the printer must be a junk, that’s why it fails”. We tested our algorithm in a much better maintained (brand-new) and mechanically more sound printer. The better printer has tighter belt tensions, more powerful steppers, more damping in the bearings, and etc. The way it fails is still the same. If the acceleration is kept increasing while the feedrate is fixed, the printer eventually fails once the stepper is overloaded with the resonance.
2. The vibration comes from the x and y movements. That means, build adhesion and not so perfect leveling of the build platform are out of scope. Tom Nardi wants to attack the video, so he found un-relevant excuses and used that avenue to discredit our work and presentation. Nice job framing.
3. Framing the standard print as sub-standard is based on the fact that Tom Nardi can print as fast as the accelerated print. What he misses is the feedrate. It will be interesting to see if he used much higher feedrate than ours (60 mm/s). Tom, please tell us what feedrate and acceleration settings you have used. Also, mention what printer you used. Tom is barking on us that we are not transparent, but it is him, who are not transparent at all when it comes to “replication” of presented work.
4. Tom spent meaningless hours to analyze the video and used that to fill up his post with that information. He could have asked us what settings we were using in the first place before jumping on the criticism bandwagon. I don’t see this ill-conceited effort constructive at all.
Is “DY” for Deokkyun Yoon, the second author of this paper? If so, I have a few questions:
(1) I understand that the 3D-printer is characterized by measuring the machine response using accelerometers (in a manner not detailed) and the results used to derive the parameters for the LPFBS algorithm.
(a) Are those parameters then good for any and all machines that are the same model?, or
(b) Must each individual machine be separately characterizes,
(c) Must the machine be re-characterized periodically as it ages to compensate for such things as pulley stretch, worn bearings, or stepper aging?
(2) Do you anticipate a dynamic driver that would use LPFBS for most accelerations, but revert to a baseline approach for low accelerations (for maximum print quality)?
(3) Fig. 10 shows the LPFBS approach as indistinguishable from the LPFBS approach at 3m/s^2, whereas the LPFBS technique excels at 7m/^2. However, the print time improvement is only modest between those two accelerations (improves from 60-minutes to 55-minutes). (a) Would that improvement be typical of most objects to be printed, or are their examples of specific objects or designs that would benefit more from the LPFBS approach?
Y Knot, I love that you took the time to read the paper for yourself! These are GREAT questions!! If DY does not answer your questions soon please feel free to reach out to me via email: okwudire@umich.edu and I’d be happy to.