Machining is one of those fascinating fields that bridges the pre-scientific and scientific eras. As such, it has gone from a discipline full of home-spun acquired wisdom and crusty old superstitions to one of rigorously analyzed physics and crusty old superstitions.
The earliest machinists figured out most of what you need to know just by jamming a tool bit into spinning stock and seeing what happens. Change a few things, and see what happens next. There is a kind of informal experimentation taking place here. People are gradually controlling for variables and getting better at the craft as they learn what seems to affect what. However, the difference between fumbling around and actually knowing something is controlling for one’s own biases in a reproducible and falsifiable way. It’s the only way to know for sure what is true, and we call this “science”. It also means being willing to let go of ideas you had because the double-blinded evidence clearly says they are wrong.
That last part is where human nature lets us down the most. We really want to believe things that confirm our preconceived notions about the world, justify our emotions, or make us feel better. The funny thing about science, though, is that it doesn’t care whether you believe in it or not. So go get your kids vaccinated, and up your machining game with scientific precision. Let’s take a look.
Ditch Your Gut and Trust the Science
In the cutting edge world of modern machining, we must trust the science. We’re optimizing for the long tail of efficiency now, and gut feel doesn’t cut it anymore. On high end CNC equipment, spindle traversal speeds are in the neighborhood of 25 inches per second (about 64 cm per second). A wise machinist once said, “At those speeds, the E-Stop button is entirely decorative”. More importantly, at these speeds, physics really really matter. Crashing a spindle at full rapids on an $80,000 machine is not something your boss lets you forget.
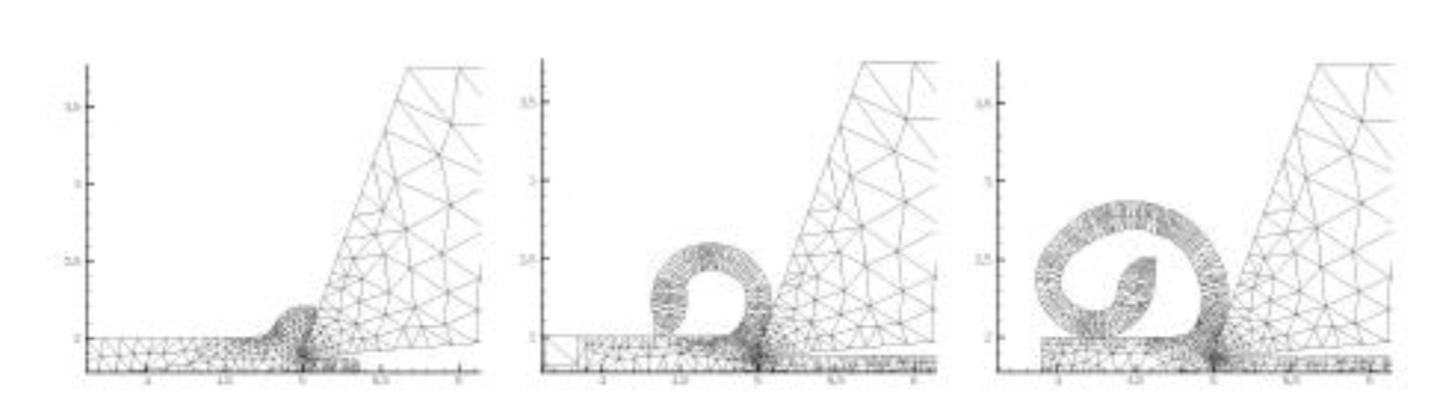
Proper chip formation is now something we understand at a very basic level, thanks to modern tools like finite element analysis. We can perform simulations of the physics that are happening at the tool/material interface, and perform experiments to determine the optimal tool angles, cutting fluids, and so forth. When you’re trying to remove material as efficiently as possible, while minimizing tool wear and maximizing surface finish quality, this level of understanding becomes necessary.
The Physics of Better Surface Finishes
For example, machinists have long known that 8-15° is the ideal back rake for a cutting edge when machining steel. On the lathe, this manifests as the angle at which the top surface of your tool bit is ground to fall away from the cutting edge.
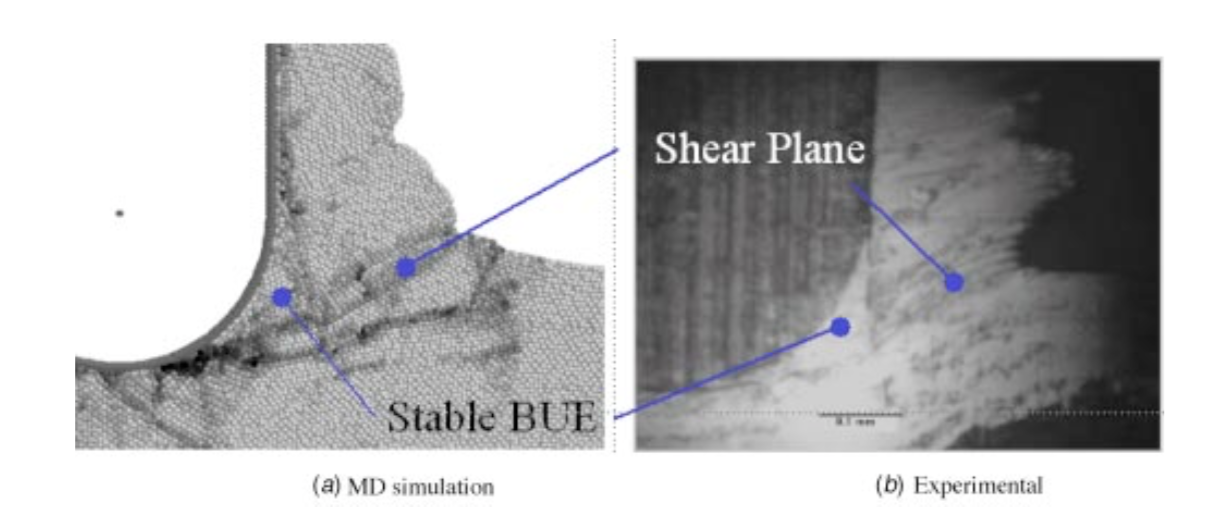
Through modern physics and simulation of the machining process, however, we now also know that, if the angle and speed are just right, the steel chip can actually enter a plastic flow state as it encounters this back rake surface. This optimizes the speed at which that steel gets out of the way, increases material removal efficiency, and prevents buildup on the cutting edge (which compromises surface finish).
We’re going to be talking more about how we know what we know in machining, so watch this space. Until then, find the oldest machinist in the room and ask them what they know, because it’s a lot more interesting than reading research papers, and gets you 80% of the way to the same place (but keep your rapids at 20% for now).
Let the chips fall where they may..
Q-D [Quinn Dunki] is all that and a bag of chips!
B^)
Chips Ahoy!
If the metal never experienced plastic flow, there would be no permanent change in its shape. The fact that chips exist is hardly a result of modern physics and simulation.
“If the metal never experienced plastic flow, there would be no permanent change in its shape”
Take a drinking glass and throw it hard enough on a concrete surface. No plastic flow. Permanent change in shape.
“The fact that chips exist is hardly a result of modern physics and simulation”
Understanding how chips are created is and it’s also what the text is about.
“Take a drinking glass and throw it hard enough on a concrete surface. No plastic flow. Permanent change in shape.”
Nope. glass breaking is not a change of shape. If you collect all of the pieces (ALL of them) and stack them correctly, yu will still have the original shape. I will say the statement is kind of tautological, as the definition of plastic flow (ductility) is that there is a permanent change of shape due to applied stress, rather than elastic deformation or brittle failure (like glass)
“Understanding how chips are created is and it’s also what the text is about.”
Absolutely.
Hmm, so those finite element analysis approaches not factoring in the buffering effects of pressurised water/oil emulsions at various temperatures as well as those of both metal temperatures and hardness stats regarding subsequent effect on dampening vibrations during the cuts – what are they playing at ;-)
IOW. A useful start but, misses a couple of secondary effects of benefit to smoothing the cut reducing tool wear…
Oh yea, heat buildup in the material causing it to expand resulting in a deeper cut and more material removed than you expected is something that all machinist mast keep in mind. I have run a cylindrical grinder and been taking parts down to tolerance when heat buildup in the work resulted in the last pass throwing things out just a little. on straight parts this is not as prevalent but with complex shapes it can cause the tin area to be within tolerance and the thick area to end up well below.
yes there is some science in this but mostly its experience and gut feeling :) Oh and measure, measure then measure again.
There is a huge problem with sticking to just the science that we are experiencing today. There aren’t many legitimately skilled machinists out there. There aren’t many problem solvers in the field any more. They all just want to do the math , and as a recent article I read pointed out, its why we couldn’t rebuild the Apollo era spacecraft if we wanted to. 50+ year old tech and we can’t make it today because people can’t get there nose out a book and get their hands on a tool.
We need BOTH practical skills/experience and a thorough technical understanding of underlying principles. One without the other only serves to limit our capabilities and achievements. I will say though that distilling our inability to rebuild Apollo era spacecraft down just to modern engineers being overly bookish is pretty short sighted, completely ignoring the drastically different political and economic climate of now vs then. But of course it is so much more fun to unfairly generalize to the detriment of the next generation of engineers and scientists, tell them how professionals back in the day would walk to the lab in waist deep snow uphill both ways, and tell them to get off our lawns …
I get a bit frustrated with the “we can’t rebuild the Apollo” or “we can’t replace the turret on the USS Iowa” because those seem to be situations where the problem is a poor return on the investment, when newer materials and technologies can achieve the same goal. It’s like “we can’t build horse-drawn carriages the same as they used to” because we don’t have wrought iron so we use spring steel instead, because it’s fundamentally better than wrought iron in most ways. I have a machine shop and use WWII-era lathes right beside my CNC mill, and there are plenty of other younger people doing the same thing. You can do amazing stuff on an old Monarch 10EE, but you can do the same thing in 1/50 the time on a modern CNC lathe, and every piece that comes off it will be the same within your ability to measure it. But if you don’t spend a lot of time with your nose in a book first, you’re going to wreck your fancy CNC lathe. The learning curve is higher now, but experience is still vital. It’s merely different experience. When I work on the old lathe I know from how the cut sounds whether the feed is right. On a CNC, there isn’t time to set the feed by the sound: it’s already done with the cut by the time I know if the feed is okay. So I look up the feed in, you guessed it, a book, based on the material, the surface speed, and the tool type.
It’s fine to be nostalgic. I write with a fountain pen. But don’t mistake nostalgia for loss.
I agree. The -all can do- machinist, is now the all-can-do machine.
So long as we’re ready when the apocalypse comes.
Bingo! The finish tells the tail on the cnc. And if it is an old, abused unit, you can still get good product. You just have to know the machines nuances. For one offs, hard.to beat an old Monarch. We have one that was built in Nov. 1947. Still rolling along.
The problem with the Saturn V is that most of the rocket is a giant collection of parts by thousands of vendors. Half of which are out of business and 90% of the rest haven’t made that part in 40 years. And there was a reason that that particular part was specified by the designers, so you can’t just substitute a similar modern part. You have to requalify the part, the sub assembly it goes into, etc. Its a whole lot like redesigning the entire rocket from scratch.
The problem that Modern NASA has in managing large programs like the Senate Launch System naturally makes it harder.
That’s why we have GD&T so those old blueprints will still have interchangeability.
China has machine shops like the US has coffee shops. There are still tens to hundreds of thousands of experienced hands on machinists but they may not live in the US.
So does South Korea. Everything from sheet metal spinning to die makers in home shops and garages.
They ran out of the WWII German engineers and rocket scientists. :P
Do you know someone who could cut an arrow head in stone like it was done thousand years ago?
I’ve seen arrow heads made from flint that are indistinguishable from those made thousanda of years ago. The man making them made it look ridiculously simple but that was because he had spent years teaching himself how to do it.
Craftsmen can be as good and as capable today as they ever were, but there is no money in it today*. That is progress.
* Unless , for example,you are needed to show how things were done for a TV programme – then you can more or less set your own price.
Yes. My 18 year-old nephew and his cranky old uncle make both axe heads and arrow heads out of Texas chert/flint.
The process is called flint knapping, and there are there are more people doing it now than there were thousands of years ago.
Take your politics back to your cry-room, please.
Yes. It is part of many archeology grad school courses.
You know if they guys 50+ years ago did there due diligence and wrote shit down, I wouldn’t need to re-engineer all there crap now.
Man, this comment triggered me. I’ve been cleaning up after redneck shit that was done 30 yrs ago for too long.
Sorry, I used to have better things to do than “write shit down” unfortunately I’ve recently learned that my son also needs to know which back gears to fit for specific threads, and which lathe is better at metric or imperial, the raglan has a metric lead screw and the leblond has an imperial lead screw and is more powerful and can hold bigger stock, but if you cum metric threads, depending on diameter after about four inches the thred pitch is 10thou out of tolerance. This is the shit that needs to be written down, ideally before I move on to the next world.
If I cum metric threads, will it be more or less painful than imperial threads?
I don’t know what all this “imperial” stuff is on HaD, but ANSI threads pass smoothest (depending on prostate of course).
The have, its called the Machinist Handbook. its expensive but well worth keeping around.
Machinery’s Handbook?
No.. we can’t do it today because it 50+ year old tech. That was dare devil level work. We can do better. Have you seen the Falcon Heavy? I do agree that our trade is lacking those with exceptional skill. But that started with the push to replace the Tool Maker with the Engineer. Bad idea.
I don’t see people as simply tool makers or engineers, I see people who have a certain set of skills and those who have other skills that may or may not overlap. I really dislike the idea of only going by a label applied to you as a means to somehow separate what others perceive you can or cant do. I measure people by what they can do and what they know, not by what they are called.
Blame the PHB’s and the bean counters as to why people want to just do the math. Problem solving takes time and if the problem has already been solved then why waste more time trying to solve it again, time is money and no company is going to pay someone to experiment (make mistakes) on company property on company time. Ive seen quite a few machine shops with one or two skilled machinists and a dozen machine babysitters, and really if you are doing production scale work then you really don’t need to waste money on having a skilled problem solver machinist at every machine
Then there is the other argument that the problem solving has moved on to more complex problems that require a deeper understanding of a wider breadth of subjects, thus cutting out a large portion of the population from being problem solvers. Take the fea example up above, not only does that require a through understanding of metallurgy but an understanding of FEA, the formulas used and a level of math required to put it all together.
The thing is that we don’t really need all that many skilled machinists out there, thats because a skilled machinist is already behind the times. Now that person needs to also be a welder, metallurgist, electrician, programmer and math wiz as well, modern machines are infinitesimally more complex than their predecessors from 50 years ago (think machines that combine additive and subtractive machining)
As for why we cant build 50+ year old tech… why would we want to? the world has progressed in the past 50 years and you either get with the times or get left behind. Its only when you are at the forefront of any field that you can change the direction of progress. So stop living with the past and maybe stick your nose in a book to see how things are done now a days, that way when you see something theoretical that could be wrong, you can be a positive influence in getting to the truth instead of being a “get off my lawn” kurmudgon
We have some very experienced and knowledgeable machinists at the Milwaukee Makerspace. They are constantly maintaining and upgrading the machines at the space. I love to watch them work and to pick their brains about how to do things. Every time I need to do something I haven’t done before, they explain it, demo it, and then I practice it. It’s a great way to learn to do things. Oh, and the specialized tools they have for absolutely everything is just amazing.
The article talks as if this is something brand new…. I was taught the technical aspects it speaks of 45 years ago! But then I learned “old school” in a union ”’mil spec” shop. The first year in the trade my Foreman called me everything but a man. But he sure taught me A LOT!! Old English machinist who started his apprenticeship in 1929. I wish I new what that man had ‘ forgotten’ by the time I went to work there!
Old timers often stare down their noses at young folks because the old timers simply can’t remember when they were young and didn’t know anything and don’t remember learning things – like they were born with the knowledge of the universe. Yet it 30+ years the kids of today will know more than any 70 year old of today knows. It’s just a matter of fact. My 72 year old father who worked in construction his whole life can tell how to build a house from the ground up and roof the thing and put on a ridge cap – but can he set the clock on his VCR or set-up a simple home wi-fi network? NOPE.
My favorite is when old guys attack the “hippy liberal know nothings in California” in on-line social networks from their iPhones or Macs…
And as for the guy spouting off about the “Apollo program”: Nah, its just private companies building rockets that can fly back and land on their tail on a barge floating in the middle of the sea – automatically…. No skill there! *face palm*
And as for that picture… Yikes… Roughing pass?
>Nah, its just private companies building rockets that can fly back and land on their tail on a barge floating in the middle of the sea – automatically…. No skill there! *face palm*
BTW: There is a much smaller start up in China trying to do that. Not so unique after all.
https://www.inkstonenews.com/science/last-wonton-chinese-start-ups-are-developing-cheap-rockets-and-tiny-satellites/article/3008524
I thought it was homespun stock and crusty old machinists.
Love your work and articles, thanks Quinn.
There used to be a manual that came with the old “Atlas” lathe. Anyone have a link to a digital version the manual and those old machinists guides?
There are copies online through Yahoo Groups, on both the Atlas Lathe and Atlas 618 groups.
https://coffeeshopmath.files.wordpress.com/2014/10/manual-of-lathe-operation-and-machinists-tables1.pdf also appears to be a decent copy, although it’s not identical to my printed copy.
Instead of those whacky triangles, go watch some real action:
https://www.youtube.com/watch?v=mRuSYQ5Npek
AKA “Iscar chip formation”
OMG.
There was a similar video series (we must have covered it on Hackaday) done by a Japanese researcher about optimal chisel angles for wood planes. Same setup, different materials, strikingly similar results.
I’m loving the interplay of the old get off my lawn crowd, vs cerebral engineers, and people in the middle.
First off- we don’t make rockets anymore not because we can’t, but because we love to praise NASA but keep cutting their damn budget, because science seems worthless to Americans now unless it can earn them a buck. Case in point- we pay Russia to launch us, the USA. It is not any lack of machinists that keep rockets from happening. We could make 100x better rocket right now with people we have, and I say this as someone who recently had parts I made on display next to THE Columbia module in an exhibition.
To all the old farts- you taught me, in between swearing at me and ignoring me, thinking I was to stupid to understand what you were doing when you didn’t think I was watching what you did- including when you screwed up.
When you weren’t teaching me by good or bad examples, I went home, machined on my own, and studied. Everything from metallurgy to mechanical engineering, chip flow, you name it.
I am not a journeyman, and I had no apprenticeship, because practically noone wants to offer them anymore, but I work as a tool and die maker. I am in my mid 30s, and I got a college degree in Language to boot for good measure, after learning watchmaking professionally for 2 years.
To all the polymaths like me that know how to make chips and tools from scratch, program, use antique lineshafted stuff to modern swiss CMMs- to hell with papers. You don’t need papers to be a real machinist, you just need to know what you’re doing, and prove it on the spot to anyone with them. I actually got paid to tutor another machinist last week on something, a man whos been machining longer than I’ve been alive.
If anyone tells you you’re not a machinist without papers- and you know you know what you’re doing, and can prove it- to hell with them.
Age does not automatically equal skill, nor does an apprenticeship. Intelligent application of skill does.
Back in the day, the Tool and Die makers in our shop, spent the swing shift making quarters. (Yes, it was that far back)
I hired in at several aircraft outfits, and managed to catch the “Christmas Layoff” each time. (Union Rules? )
At the Hughes machine shop, the plating shop was always glad to gold plate your silver ring, (for a beer) and the odd belt buckle. I left those fine companies, and drifted into automotive/tractors/race cars. Fun times. After a while, the movie industry needed a gas/diesel mechanic.. (My 15 minutes of fame) Worked on the Godfather, and many TV shows.
“Age does not automatically equal skill, nor does an apprenticeship. Intelligent application of skill does.”
After intelligent application of my learned skills, I joined local government, did my 20 years, and retired.
Next step, college professor. Yes, I chose to teach those learned skills to the great unwashed masses.
As Program Director, I built curriculum for our campus, and was even recruited by the state of California to vet other colleges. Moved on to another college, training fire and safety personnel on alternative fuel vehicles.
Amazed am I to accomplish all that in only 80 years.
And, not done yet..
And modesty, for that matter.
Is there anyone who tried glass machining by single point cutting tools?
It’s called etching..
You can do glass machining with diamond tooling, especially if you do all the work underwater. Glass is surprisingly tractable if it’s wet. I’ve cut standard taper plugs and sockets for organic chemistry glassware on a lathe, using abrasive-loaded copper. (This is bad for the lathe unless you are scrupulously careful about cleanup.)
Single point diamond turning is incredible. Make lenses and reflectors of any shape.
45 years in the machine trade. It sure has changed. Manual and CNC machines dwell side by side and all have their uses.
Cnc machines have gotten better/cheaper easier to program. Sadly the manual tools have not. Cheaper yes, but not better.
Those old manual machines built by the “greatest generation” are WAY better than what is built now with the exception of a very few companies.
today’s cutting tools are great! I can run at feeds and speeds my father could only dream of. The materials modern bits are made of plus the geometry they are cut to and the coatings allow very high material removal rates…its amazing
I came in about the time that cemented carbide tools were gaining favor. Here it is, 38 years later, and they call me Toolmaker/Machinist. Every high school had a metal shop. There were community college courses where you would get job offers at the end of the class. Now, it takes about 1/2 a day to find a good job, most of the time, nobody else even applied. I’ve worked with some old guys that had a real negative view of CNC machines and the guys who run them (I do CNC too, although currently, I’m 100% manual in a prototype shop, Defense Industry), in fact, I’ve had a few of them tell me they were faster and more accurate than a CNC mill ( they weren’t, they were either lying or just delusional). For a while there, every satelite that went up from Vandenberg had some of my parts on it, the second Rover, too. But here’s the thing. Nobody is going into machining any more. The guy I work with is almost 80, and is the strongest manual guy I’ve ever worked with (he has 60 years exp), and even at that age, he puts out more work than I do. He cannot be replaced. To me, if you are into hotrods, dirt or street bikes, guns, racing cars or motorcycles, building your own airplanes, anything like that, machining is where you want to be. Many of these hobbies are being priced out of most people’s pay grade, at least if you want to be competitive. And paying someone to make parts for you or build an engine is getting way out of hand as far as expense goes. So I have to do it myself.
It’s a very good trade. It’s fairly difficult, especially at first. There is a lot of job satisfaction. Most people can’t do it an do not have a clue what we do. And a lot of machinists are arrogant assholes
As a 70 year old retired AI company executive, I’m having a great time learning machining, making those race car parts you mentioned.
The “This is a Finite Element Analysis of the three stages of chip formation” image takes me back to studying civil engineering when I was learning the details of State and U.S. code regarding seawall and retaining wall restoration and construction requirements.
The house I had on the river had a seawall the if was sloped or still standing and didn’t slide into the dredged man made river basin… wasn’t anything but vertical when I had at it. Had to put a slope on the face to make sure ice didn’t smash into the face to cumulatively stress and the ice would roll up to break apart.
Looking forward to reading more. Neat article and similarly as noted above… every time I go to ask to have something machined now days since I’m not connected with a shop where I can machine for myself or have machined on their/my budget… I do a little math and the cost benefit analysis, since I have time is to machine the part myself, says to upgrade the cheap Harbor Freight 7×10 for now and built that into a mill… and larger eventually if needed. Received the angle plate and waiting on the Timkin 30206 tapered bearings. Next month will be the next phase of tooling to invest in that I can’t make myself as cost effectively.
Forget the modern machines. They are not worth buying until you get into the tens of thousands of dollars. Buy old iron. You can pickup very decent machines for under $1000. My lathe is from 1942 and my mill is from the late 60’s. Both work great. Neither machine is perfect but much better than anything I can buy new. You just need space that can handle the weight. My machines are over 6000lbs each. Smaller machines go for more money as there is more competition to buy them. Don’t be afraid of 3 phase either. You can either swap out the motor, install a VFD or build a rotary phase converter.
You can save lots of money these days by importing tooling directly from China on aliexpress. I’ve had pretty good experiences so far with inserts and tool holders. I’m able to find stuff at like 1/5th or even less that works just as good as the brand name stuff. At the local dealer I can buy inserts for like $10 each, or I can order a 10 pack from China for under $30. It’s not so great for larger stuff like a vise or chuck as the shipping gets very expensive on heavier items.
In the end it really depends on what you need to do. I am an engineer & com sci guy. I got myself a used lath for about $500. It has been fascinating learning how to manually use it. It is fun! Now if I needed to make 10’s or hundred; we are talking about something else.
Anybody can recommend a good book about the physics of machining?
YouTube Knows All
https://www.youtube.com/watch?v=ckknLkwx9Sw