We’ve all seen cheap welders for sale from the usual online sources, small inverter stick welders for a very tempting price. But are they any good? When my local supermarket had one in its offers aisle, I took the plunge and placed it in my cart alongside the usual week’s supply of Marmite. That was some time around the start of the year.
Does Your Supermarket Sell Welders?
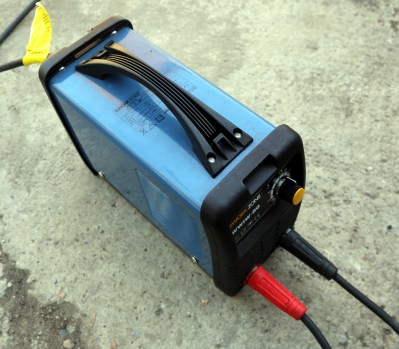
What I’d bought from my local Aldi was a Workzone WWIW-80, an 80 A unit that had cost me somewhere just over £60 (about $75), and came with welding leads and a rather poor quality face shield. The German discount supermarket chains specialise in periodic offers on all kinds of interesting things, so a very similar unit has also been for sale with a Parkside brand from their competitor Lidl. These small inverter welders are fairly generic, so they can be found with a variety of brands and specifications at a lower price online if you don’t mind forgoing the generous Aldi 3 year guarantee. The cheapest I’ve seen was about £35, or $44, but that price included only the inverter, without welding leads.
As a working blacksmith my dad has had a high-quality inverter welder since the 1990s, so my frame of reference is based upon that. He tried one of the first tiny inverters when they originally came to market in the last decade, but it couldn’t take the demands of a professional welder and packed up. I thus didn’t have high expectations of this unit, but I needed one of my own and for the price it was worth the punt. I’ve used it for occasional general purpose heavy welding tasks, repairing bits of farm machinery and fittings, and rebuilding some steps on a narrowboat in 7 mm plate. It’s acquitted itself well in those tasks, in that I am not a skilled welder and my work isn’t the tidiest, but it’s allowed me to do a satisfactory job.
How Do These Welders Perform?
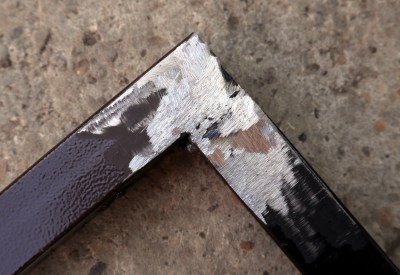
It’s now a long time since inverter welders were new, so perhaps fewer readers will be using AC stick welders than might once have been the case. For me the comparison is one of smoothness, my relative lack of welding skill reveals itself in finding the inverter less easy to strike an arc than my dad would have, but once that arc is under way it’s so much easier to draw it and control it. I can fill holes with weld much more easily with an inverter welder, and the better control of current means that I can more easily deal with lighter work where someone of my abilities would normally be better served with a MIG welder.
To demonstrate this I decided to push the limit a little, and try the Workzone welder with some offcuts of 1 mm thickness square tube from my makerspace scrap bin. These had come from an office table leg, and were the type of stock that would push the boundaries with any stick welder. Because this is a relatively small welder, I use it with 2.5 mm rods, which as you’d expect will happily blow a hole in a 1 mm tube wall at higher currents. This is why you’d normally use MIG on a task such as this, and indeed at 80 A I was rewarded with something closer to cutting than welding. Dialing back the current to 40 A, I could easily rebuild the hole, and when trying to join two pieces at a right angle I could produce a smooth weld with good integrity. To me, the ability to weld this material is nothing short of amazing, as I’ve never managed to do that on such thin metal with a stick welder. That’s almost car bodywork thickness, I’d never have imagined even an inverter could come close. It’s worth saying as an aside that maintaining an arc at only 40 A is a little more challenging.
…And What Are Their Limitations?
I’ve described my Workzone then as a capable little welder that has served me well over the jobs I’ve used it for and which has even surprised me with its capabilities. Where are the deficiencies of it and welders like it, if they’re so good, why do better welders exist?
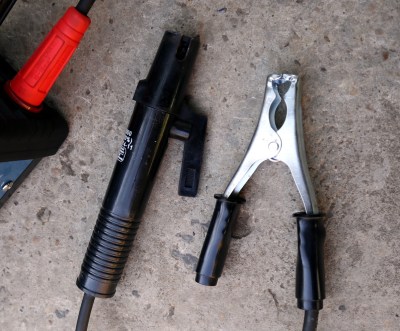
Construction-wise, these units tend to be robust enough for serious casual users. A sturdy sheet-metal case with decent cooling apertures and a fan to stop overheating, and brass locking connections for the leads. They are nothing special if you are used to other switch-mode power supplies: the usual electronics and a toroidal transformer. The leads are substantial, and on inspection proved to have copper conductors rather than aluminium as I’d feared, and because this was sold through a European distributor everything bears the European standards markings. If you buy a similar welder from an online source it may not have these approvals, so beware appliances with lax safety standards.
Where they differ from professional grade welders is in their duty cycle, and probably also in some cases in their claimed capacities. This isn’t the welder you’d use for large-scale fabrication or to build ships, it’s the one you keep in the shop for short welding tasks, or perhaps you have as a lightweight and portable backup for jobs where your shop welder is just too big to get to. If I was to hazard a guess as to why my dad’s little inverter welder broke down, I’d put the finger on duty cycle: the demands of a blacksmith fitting a piece of work on-site were probably too much for it. So if you’re an occasional welder it’ll be fine, but if you’re using it all the time it might pay to invest a little more.
Then there are the sometimes optimistic specifications quoted on small inverter welders. The Workzone unit is comparatively modest in its capacity at 80 A, but it’s not uncommon to see similar models claiming to be capable of as much as 200 A. When something that only costs a few tens of dollars is promising capacities that seem unrealistic for its price, it’s not unreasonable to assume that exploring its limits will hasten its demise. You get what you pay for, and perhaps if your needs run to more substantial currents it would reward you to pay a little more.
Among the Hackaday readership will be people whose welding skill is far ahead of mine, as well as plenty of people with experience of similar cheap inverter welders. I hope sharing my experiences will help you decide whether or not to try one of these devices, and as always it would be great to hear your views in the comments.
I was just looking at these for a totally different reason….I’m on an off-grid mostly solar homestead, but then there’s February – and fairly common use of a generator.
Chargers that will eat a couple kW of power and put it in my 24v nominal (but need up to 28v to fully charge) batteries, are hyper expensive. I’m wondering if I might get away with one of those “200 amp” $40 models – youtube tests have shown them to be good for around 100 actual amps and around the voltage I need, but no one seems to have tested for both at the same time.
I already have “real” welders – TIG, MIG, stick, oxy-acetylene. But I keep those indoors, not out at the energy shed…
Since it’s easy to pay almost 10 times that price for a 40 amp 24v battery charger for RV’s…hmmm.
“Since it’s easy to pay almost 10 times that price for a 40 amp 24v battery charger for RV’s…hmmm.”
I was thinking the same when I read on top of the Twentieth Century welder, I picked up for $50, that there is a battery charger attachment.
https://www.facebook.com/photo.php?fbid=3333883423340103&set=pcb.3333877926673986&type=3&theater
I’m thinking with another transformer to step the 24V to 12V and maybe another inductor to level the current better, that the about doubled current should make a good enough vehicle starter also… unless you have a 24V rig.
I was just looking at a $44 ebay plasma cutter. Amazing… the price point of these modern systems.
where did you see a plasma cutter for 44$ on ebay (link)? as far a i can find, the only thing you get for that money is a torch for a plasma cutter (i.e. just the torch set with cable/hose but without the actual plasma cutter device that supplies the power)
I would strongly avoid charging batteries with a welder. Batteries need to be charged under profiles based on the chemistry. Welders would not work-safely.
Speaking from experience charging a car battery with a welder is really good at rejuvenating them, a good kick in the guts and ripple desulfates the battery and charges them quite rapidly. it will prolong the life of a lead acid batter when charged this way vs tickle charging.
The low duty cycle on these might be a problem.
Some are better than others , I am a pipe welder , chillers , boilers ect . I used a maxstar 160 to test 6G and for 6 years in the field welding up 8 inch sch40 pipe . More recently repaired the bucket on a 320 cat excavator , that inverter lays in 1/8 7018 like a bobcat 225. Some of the Chinese machines are quite good as well but they start at 300$
I have a cheap stick welder and it lays down 5/32 7018 at it’s max(140amps) like a champ. Mine cost $99 with cables included, and dual voltage
You probably want a second hand forklift charger…
I have two of those. Far too wimpy and too frequency sensitive – at least the ones I have have ferroresonant transformers. I have 2500 amp hour batteries to charge here. The forklift chargers run around 20-30 amps and taper off very slowly.
EG, you’d need generator runtimes that would be quite expensive indeed.
I’m more aware of battery profiles vs chemistry – and temperature – than you might think possible. I’ve been at this – no grid, since 1980, am an EE, and get around twice the normal life out of a set of batteries compared to others and vendor projections.
Seems like you could deal with the duty cycle issue by…running the thing at its duty cycle or a little less. Temp sensing would not be a problem. I already have a raspi out there to log things and serve plots to my in-house systems, and an arduino for realtime control over the big diesel generator (for water pump and fan) I now use…but since the inverter/charger that is driving requires AC to pass through to do charging, I can’t do electronics work with sensitive stuff – that generator AC – it’s 1930’s quality noisy slip-ring AC.
Lots of forklift chargers over here run like 100A at 24V, 100A at 48V, more values like that.
Some of the inverter type chargers even run higher currents.
Don’t know about the type of transformer used in the big transformer type chargers.
Have you ever looked into a ‘flow battery‘ setup? Vanadium tech is the most mature, but others–like a zinc-iron version–are being developed. I’m not sure what your needs are, but it is the most environmentally friendly energy storage medium I can think of.
I have a modified ATX powersupply that i can adjust the 12v rail voltage on. It came out of an old generic PC, and it pushes 40 amps at 14 volts, and it’s just a 300 watt model. I would consider server-powersupplies, as they are built for 100% dutycycle and are usually very powerful and very cheap, as they are loud and usually in a proprietary formfactor.
If you could manage something like 2 x 1500 watt PSU’s in series and modified it’s sense-wire with a potentiometer to turn them up to 14 volts each, you could probably charge those batteries at close to 3kw all day long, but keep in mind that server-grade hardware is LOUD! As in big-hovering-drone loud.
Consumer-grade ATX PSU’s work too, but will probably not like being pushed close to 100% for that long. I have only pushed mine to around 5 minutes at 30 amps to charge a dead car-battery, which it seems to have survived, but i had 2 before this that burned out when overloaded even for a couple of seconds. My guess is that the MOSFETs couldn’t handle the amperage, but the third one seems to survive being basically shortcircuited, so i guess it depends on the model.
40 amps at 14 volts and its only 300 watts? My math might be wrong but i dont think thats how it works
I smell gross overload :-) Perhaps a strong fan helps to blow the smoke away. :-)
Take a look at the MeanWell RSP-2000 power supplies. They will take AC or DC input at a variety of frequencies. They have current limited outputs with remote sense and remote output voltage adjustment. $400 will get you 2kW of charging that you can control from the Pi. They even support parallel operation so you can up the charging size by adding modules.
I wish Aldi and Lidl stores in the USA carried things like this!
I wouldn’t be surprised if the USA Aldi’s had one of these. I’ve seen some weird stuff there.
Not that I have noticed, but I will keep my eyes open.
I almost bought a huge tool cabinet for $100 at an Aldi in Texas.
They have some WEIRD random stuff, but a stick welder is something I really didn’t expect. It looks like this week in the US, the special items include a gasoline-powered generator and a cordless chainsaw-on-a-stick.
I used to joke about ALDI being the only place you can buy a MIG welder and a packet of bacon in the same place. Then, a couple of years back on a respite weekend with the missus, in Exeter I think, it happened. I popped out to the nearby ALDI for another bottle of red, and spotted a bloke walking up to the tills with a packet of bacon balanced on top of an Arc welder. Not MIG, but meh, close enough :)
I got one of these. I am jolly impressed:
https://www.aldi.co.uk/workzone-240v-portable-bandsaw/p/086075229503400
One of our local Aldi had the shelf tag for these, but had sold out.
They do. Well, Aldi at least. I just saw this exact (or very similar) welder advertised at my local Aldi last week. If I hadn’t JUST bought one from Amazon about a week earlier, I would have gotten it.
I’ve also just invested in a “cheap” inverter welder but, in my case, I shelled out £180 for a gas/gassless MIG welder. Sure, it’s three times what you paid for your stick welder, but it’s capable of far, far more. My welding skills extend to one session I did in high school, more than twenty years ago but I can use this thing to produce a decent-looking weld.
It’s amazing how this technology has changed. I remember when the farm I grew up on first bought a MIG welder; it was a very serious investment. Only a few years ago, you had to choose between the expense of maintaining a gas system versus gasless equipment. Now, you can buy a cheap welder that will do gas or gasless and a 60L disposable gas cylinder for less than £15. All the talk on the internet is whether you’ll use CO2 or go for the more-expensive Argon, but in my case the difference was 14p…
Disposable gas cylinders? I can’t say I’ve heard of those.
I’m going to be in the market for a new gas cylinder soon. Places around here want $300 (Canadian) for a new cylinder, and $100 or so to fill it (for something in the neighborhood of 40- 60 cubic feed of C25 gas).
I hadn’t heard of 60L disposable gas cylinders either, so I did a web search.
Most of the links that came up say “Unavailable”.
Such as…
https://www.amazon.co.uk/Langley-Pure-Argon-Disposable-Bottles/dp/B00GAX741O
Available: https://www.toolstation.com/disposable-gas-bottle/p35286
Why? A 10kg fill costs ~20€ and the bottles never lose value….
When I had contract cylinders it was £7 per month cylinder rental (whether I used any or not) and then £38 per fill + £15 admin charge. So even if you use no gas at all you are spending £99 per year.
There are now schemes where you pay £155 to own the cylinder outright and £45 to fill it.
If you don’t weld very often then the disposable cylinders make sense.
(They also make sense if you are transporting the welding gear by motorcycle :-)
@DooMMasteR:
Do you really mean 10kg or 10l? 10kg of Ar would be 5600l or about 28l @ 200bar. Where do you live? Here in Austria I know only a price of €39 10l/200bar (Hornbach).
Here this 1l/60bar (60l) bottles cost €19,- and on Amazon also 2l/110bar (220l) bottles are available for €39,-.
For €39,- also a 10l/200bar (2000l) refill is available. The bottle costs €119,-
I am not yet sure, how much use I will have in the near future.
Interesting! Any US sources that you’re aware of?
the thing about the disposable cylinders was the CO2 lasted LOTS longer(especially the double pressure ones in machine mart, notice your in the uk). As your in the UK, SRS autoparts and some other factors do rent-free cylinders, great for people who dont weld much like me, but weld enough the disposables are no use.
A handy tip is to look at machinery auctions for older heavy MIG units, thy type on wheels. They’re unfashionable and heavy, so they often go for relative pennies.
CO2 vs argon? My dad used CO2 as he could own his own cylinders. Fine for a blacksmith, not so much for thin car bodywork. I’ve never seen anyone else but my dad weld the rusty “steel” of a 1978 Austin Allegro with CO2 though.
I had a mig like that I wound up giving to a friend. It did up to 400A and used .045 wire. You could strap it for 208, 200 or 4 something. It was roughly the size of a domestic washing machine. I screwed up a bit though, I got one of the Lincoln migs, probably one of the last of the transformer based ones. I chose the 120V one as I figured I might use it away from my shop at times. If I had waited a year I could have got one of the universal power ones. Still in the grand scheme of things, there is a lot less to go wrong with a transformer than an inverter, and a gen 1 unit is bound to have bugs to be worked out.
Im a welder/fabricator by trade. At work I’ve got personal machines that are owned by the company, a Millermatic 211, Miller shopmaster 300 with wire feeder and TIG attachments, a Miller Bobcat 225 engine driven, all of them really nice machines. At home ive got 2 stick inverters among many other machines, an 80 amp and 200 amp. The 200amp is a chinese brand, 220v and cost me a whopping $120, to my suprise it runs 6010 without a single hiccup which is the true test of any stick welder. The 80amp was around $150 and could be considered a name brand, its sold under a bunch of different names though. Its 110v and runs scratch start TIG on sheet metal now days, so much so that the hot start on stick mode doesnt work at all anymore. For the money, that 200amp runs smoother than either the Bobcat or Shopmaster I have at work. The Bobcat has since become a powersource for the 200 amp inverter. I still havent hit the claimed 30% duty cycle, not even burning 1/8th inch 7018 all day.
In the 70s and 80s darning with MIG was an essential skill because of the crap steel in British cars. :)
Darning + welding,
in my ignorance, I thought darning was a process only to repair knit fabrics.
Perhaps he means the technique where you lay the wire across the gap, then press the trigger, then repeat, so that you build up a weave of wire onto which you can paint a layer of underseal paint to fool the MOT tester. Works fairly well on the inaccessible top surface of land-rover chassis :-)
Thanks Andy!
Is this wire mesh process really less work than inserting (and more or less tack welding) a piece of sheet metal? The cosmetic value would be at least comparable.
Like this?
https://www.youtube.com/watch?v=njqL8roxFr0
The problem with that is that (atleast in Europe) most of the industrial heavy duty MIG units at auctions are 380/400v. Great if you have access to that kind of power, but most hobbyists do not. (and it’s not usually possible to convert them). The ones that ARE 240v are usually quite expensive comparitively
Not really. There’s a sweet spot of single phase 240V machines from the 1970s or so that are huge and heavy compared to more recent plentiful alternatives.
The best gas mix I’ve found for solid core carbon steel wire is 75%argon 25%CO2
One advantage of these little inverters is their portability. I bought one so that I had a welder that I could carry in a motorcycle pannier. That was a long time ago, 20+ years, and it is still going strong in the hands of the friend that I loaned it to.
That doesn’t sound like much of an advantage for you though. A heavier machine might still be in your garage.
Ner-a-car owners don’t carry arc welders. They carry a portable hearth, and a load of rivets. :)
In the mid eighties a friend joind two Bedford HA vans together with pop rivets, yes pop not real rivets, when he showed me his handy work I obviously didn’t look too impressed because he said “what? It worked for the sbort brothers” there really is no argument for that kind of logic, the worst part of all this is that the van lasted another 18 months before there were “issues” whatever that meant.
It would have been nice to see some weld beads, not a bunch of grindings that don’t show much of anything.
Actually you can see things in this grinded weld: inclusion, cracks and overheating….
Looks close to what I produced with my quite cheap inverter (~€200, with TIG option) and some sticks. But in my case the reason is for sure my hardly existing experience in welding. :-) The last time before was about 25yrs ago when a friend did some welding and I just tried it out. I have way more practice with the soldering iron.
I disagree. I ground it back to see what the metal underneath was like, because that’s where the integrity of the weld is. I am not concerned with the tidiness of the bead, more the strength of the weld.
It’s not a perfect weld, as you can see. But it’s ground back and not shown itself to be a bubble of flux slag looking like a weld, so I’m happy.
This is *exactly* my take on my own welding skills. My motto is “Weld, Grind, Repeat”
Can’t remember where I first heard it, but “A grinder and paint make me the welder I ‘aint”
That would be AvE
For my first 6G pipe certification on heavy wall (16mm wall, 30mmID), the ‘G’ could have stood for grind. Ground out almost as much metal as was in the finished weld. Passed radiograph and physical properties, including Charpy, though. (Nothing in most codes prohibits grinding during a qualification test…. Up to the test supervisor, be it a company rep, Natn’l Board AI, agency rep, whomever. They needed the work done, and need welders to do it.)
Where do you need a pipe with a wall thickness > than half it’s ID? More than 1000bar of pressure?
I used to work in a lab that was able to set up any triaxial stress in to a tubular specimen. By a combination of tensile and torsional forces for two of the axes, and then differential internal and external pressures for the through-thickness and circumfrential stress. I noticed that the pressure controls went up to 16,000 bar, though looking through the literature I can’t find the actual working pressure. ( https://www.astm.org/DIGITAL_LIBRARY/STP/PAGES/STP36214S.htm desribes the actual machine and mentions 700Mpa / 7000 bar). I recall seeing the spare hydraulic lines, 18mm OD, 3mm bore (or thereabouts).
Current common-rail diesel engines use >2000 bar.
Martin: The job was parts for a very high pressure boiler. Material strength is derated due to temperature and the pressure is very high. Add in safety factor and corrosion/erosion allowance, and so on, you get some applications for mighty heavy material, but in this case it was for welder qualification purposes only. The job involved larger tube with that wall thickness, and tube that size and smaller with thinner wall (8mm wall was pretty typical fro the smaller tubing/pipe, with heat exchanger, wall, and superheater tubes being about 3mm Cr/Mo alloy)
Guys look at my weld
>Grounded flat
LOL !!!!
“A grinder and paint make me the welder I ain’t”
I can’t really talk though, I’m a pretty crappy welder myself…
It’s only grounded while the clamp is attached, though.
Ground flat to see what the weld looks like underneath. My dad taught me to do that, because a good beat on top can conceal all manner of nasties underneath.
That’s not grinding for cosmetic purposes, in other words.
“…because a good beat on top can conceal all manner of nasties underneath.”
Agreed. You may want to do a cut and etch test, too, to see the depth of penetration. I’ve laid down good looking beads that were later shown to be basically solders for how little they penetrate the base material and none into the root (T-joints).
Quite frankly inverter make welding easy, as long as the weld is flat anybody with two good hands and common sense can weld correctly (following polarity and current advice).
But when going out of flat it’s another story (angle, upward, downward, ceiling…)
Who buys Marmite on a weekly basis?
Someone who can’t stomach Vegemite.
According to Wikipedia both are yeast extract based spreads. How do they differ?
Someone going cold-turkey on their Twiglet addiction.
Having an Anglophile mother with a Twiglet addiction… I LOL’d!
Cheers
food of the gods
+1
Poor substitute for Vegemite
You are confusing Marmite for Vegemite Mate!
You can keep that Vegemite stuff south of the Equator thanks :)
A small Marmot.
I just went through this. I bought one with good reviews on Amazon for $115… and WOW. Worth every penny. I wrote a blurb about it on my site, along with the results of its work (my recumbent trike) if anyone wants a link and some comments about it. Duty cycle? 60%.
https://miscdotgeek.com/september-trike-and-welder-update/
TL;DR: Don’t get the bottom of the barrel.
I put that TL;DR there to say don’t get the bottom of the barrel because there ARE $80 versions out there, or less… and their duty cycles reflect it. A few more dollars increases the quality some.
So, when do think you’ll get the welder mounted on the trike?
Later this year, probably. Once the trike is built, it will have two cargo boxes in the back, one of which will have plenty of room for a welder. And 115v power is ubiquitous, so a power source shouldn’t be an issue.
Neat to see and read (other than your wife… hope she heals whatever the issue. Start with healthy inputs that are real ag for starters and be critical with specialists is about the best advice from my experience). I was just at the farm yesterday thinking about my recumbent trike that is a tandem, cargo and racing somewhat style though to haul more in saddle bags in the rear design that I wanted to be able to have a goal of mounting a certain size mountain bike frame to (I have a Mongoose Black Diamond Double). With the welding resources I’ve acquired lately and am getting back into, I’ve been trying to go through all the projects I wanted to complete over the last 10+ years.
I’ve gotten to this point so far and had a bit of tragedy occur also, including my father passing forensically clean and not only me:
https://drive.google.com/open?id=13bh6_Rnt3nGF_SHeJeXDMoG1Iz7yAU5l
Ditto on the Aldis in the U.S. not having cool stuff. I was in one a few days ago.
As ever, the goody isle had nothing spectacular.
Mostly the usual laundry hampers and ironing boards, and blankets. A few desk sets (pen and scissors) and some boost pack batteries for cell phones.
For $75 USD, I’d probably have grabbed one also!
I have to cut & weld out of doors (fire hazards and no garage), so a stick welder that you can carry back inside when done, would be nice.
As it is now, I’m limited to a small MIG unit, for the portability reasons.
Funny how I would likely pick up one on impulse while in a store, but yet I haven’t just gone online and looked for something.
…must be an age thing? :^P
–
And Let’s see if this comment links to “Bill” remarks. Been having that function fail ever since the site changed to akismet.
The thing is that they don’t have them all the time. The non-food offerings are time limited and cycle through. Sometimes is laundry hamers and office supplies, sometimes it’s welders, grinders, circular saws and hammers. I don’t know about the US, but in North-Western Europe you can keep an eye on the website to find out what is on offer this week (and next week).
On the comments: we’ve been using Akismet for years, but WordPress recently swapped the comments up to Jetpack, which seems to require something in cookies or scripting that’s messing up the parent-child relationship for a couple people with strong blocking on their browsers.
Sorry about that.
Looked it up, Yeast based spread.
Sounds nasty lol.
Beer is yeast-based beverage. Not so bad, eh?!
Of course not. But would you like a curd or cheese based beverage? Probably not, although with some spices this is a perfect base for a spread. So the comparison is a little off :-)
For my friends in the US, I’ve had the Harbor Freight 80A inverter welder for about a decade now, and I’ve been very pleased with it, within it’s capability range. With practice you can lay down a pretty nice looking weld, and it will actually have some penetration unlike the cheap-o flux-core welder in the same price range. Granted, doing sheet metal is pretty hard, eventually I lucked onto a flux-core unit for that. I hate cleaning up that spatter though, I much prefer chipping the scale off of the stick welds to see how much I have to grind off, hee hee.
I have a little Forney unit that looks about the same as Jenny’s. A TIG attachment is available, but I’m sure it’s pretty rudimentary.
Catering to the Forney enthusiasts is Forneycatering!
B^)
I spent a number of years repairing welders, ranging from the cheapesd Chinese crap, to decent Chinese gear to top of the range ESAB pulse MIG machines worth 10’s of thousands of dollars each, and everything inbetween.
I saw the cheap Chinese crap grow from almost complete junk into something I’d consider purchasing for occasional garden shed use.
Two points to watch out for with the cheap Chinese units is parts availability and duty cycle.
Many of these units are clones of each other and if you are lucky, parts substitutions are possible, and even upgrades are possible with spare parts from a higher spec unit (customers were always happy with that one when our replacements were higher rated with the full board worth of MOSFETs and stuff populated :) ) BUT many machines have subtle differences that can make spare parts hard to find or even render a unit scrap if none are available.
The almost ubiquitous at the time ‘200AC/DC TIG’ machines were like this, all clones of each other with slightly different revisions and features inside. I counted something like 20 different variations come across my bench…
Then there is duty cycle. This is expressed as a percentage of minutes the unit can run over a 10 minute period.
Ie. A 50% duty cycle means 5 minutes on, 5 minutes off.
A good ESAB, Kemppi, Lincoln, etc unit might be rated at full current output at 80% duty cycle (8 monutes on, 2 minutes off), but the cheap Chinese unit, even though it has the same output rating, might be specified at a 30% or even less duty cycle.
That’s where the extra cost comes in. To get that increased duty cycle of the higher end unit, you need bigger and more MOSFET’s/IGBT’s, bigger heatsinks, better fans, etc etc.
And if you are in a production environment, the initial increased cost of the better unit is more than saved by not having to waste time standing around waiting for the cheap welder to cool down….
Nice post and very informative. So it’s down the the MOSFET board and cooling then?
Number of MOSFET’s and transformers etc.
I often saw lower rated models using the same PCB’s as the higher rated models, just with a few banks of MOSFET’s and transformers missing.
Adding a higher rated board has the expected increase in output capability.
Firmware would sometimes still limit the upper curent limit, but the duty cycle was increased along with the reliability due to parts sharing the load and not being run so close to their limits.
Stuff has to stay cool, so if there’s less stuff, it’s run harder and closer to its limits and gets hot quicker.
You have two options, increase the cooling, or increase the rating or number of MOSFET’s etc to spread the load.
One trick I used to see on-site was the guys using the machines would remove a side panel and put a shop fan right next to the welder. :D
Some of the cheap MIG welders don’t even have a fan fitted even though there is a vent hole cut out for one, such is the extreme nature of the cost-cutting on some cheaper units.
Adding a fan (a mains rated axial fan is fine) dramatically improves the duty cycle on these units.
Are heat pipes used in any systems? I’ve been wondering about using more CPU style heat sinks with more elaborate heat pipes to transfer the heat faster as well as potentially liquid cooling (which would be more risky I’m thinking).
I also assume using more transistors in parallel to reduce the working current load as I’m finding the challenge is finding high current cost effective components to manipulate the waveforms, more the challenge coming from a newer to electronics and RF engineering amateur radio and basic electronics background. Is this thinking correct?
I was thinking with the fan and/or cooling system to not use the welder transformer tap so not to adversely impact that process performance as an upgrade I saw or read about somewhere online, is that correct?
I was looking into some SCR’s from a electroplater that are way over rated to experiment with. Any thoughts and comments regarding SCR’s?
Thanks in advance for your time and comments… neat to read regarding as I’m being reluctant to invest in the newer cost effective equipment since I’m finding transformer units for $50 or less… though just noticing the latest 50% reduction in pricing that is catching my attention.
Here’s my latest find: https://www.facebook.com/james.analytic/posts/3343589319036180
I never saw heatpipes being used, but watercooling is a thing.
It’s more common for cooling the business end of the TIG torch or MIG gun on high current applications, but I have seen watercooled heatsinks inside units too. Not as common as aircooled due to cost and complexity though.
Paralleling MOSFETs and IGBT’s is definitely a thing, many inverters will parallel up to 10 or more MOSFETs per bank to achieve the required current capacity.
For auxilliary power, I would either use a dedicated winding on the main transformer if available, or just add a small extra transformer just for the job. An extra transformer is probably the best way to maintain isolation and reduce interference, noise and brownouts/spikes etc to your added gear (although a simple fan doesn’t care much about a bit of noise anyway).
SCR’s are also used, they are very robust and well suited to welding applications.
I most often saw them used on large (1000-1200 amp) 3 phase transformers as a synchronous bridge rectifier, and acting as a ‘dimmer’ of sorts to vary the output current. They were always followed by a decent inductor and a BIG bank of capacitors (sometimes 100’s of thousands of uF rated at around 100V, and high ripple current rated too) to smooth the DC output as much as possible.
It wouldn’t be tooo difficult to use a few SCR’s on a single phase transformer in the same way to produce a variable DC output.
My Chinese TIG died. I was astonished when I looked at the main PCB, it’s like something from the 1980s, all discrete logic, op-amps and analogue switches: https://photos.app.goo.gl/p5GN2GYZ5c5VCTPq7
Either a genuinely old design, or perhaps microcontrollers don’t work well in the electrical environment?
Yeah, that looks pretty much par for the course for Chinese gear.
It does make board level repairs a bit easier when you can just replace a few through-hole components rather than junking a board because you need to reflow a new micro that you don’t have the source code for anyway. :)
In regard to Duty Cycle.
I looked at a Horror Fraught stud welder about a year ago.
https://www.harborfreight.com/stud-welder-dent-repair-kit-61433.html?
I was surprised to find its duty cycle was one stud every 8 minutes!
I ended up taking my car to the local body shop.
He said his stud welder could apply studs continuously.
It looks like with a duty cycle of 2% (wow that’s low) and a 1 second cycle time, it is rated for 12 studs in quick succession. A few more if you take your time before you have to let it cool for the rest of the 10 minutes.
Not great, but it is only $100. I’d rather spend that on a stud welding rig for my MIG welder….
“I saw the cheap Chinese crap grow from almost complete junk into something I’d consider purchasing for occasional garden shed use.”
I’ve seen that too (for many different products) over the past 20-30 years.
I guess once the people contracting the Chinese manufacturers got over the initial shock of finding their products built “too cheaply”, they learned to specify in greater detail what they really wanted. If you ask them to make your product “as cheaply as possible”, they will.
Once they learned that it wasn’t enough to specify “No Lead Paint”, they learned they had to specify “Do not incorporate hazardous substances in the product” -followed by an extensive list of hazardous substances.
I believe the dryness and quality of the stick you are welding with has a huge influence on the strike and weld bead. I have used mine to weld stainless steel with very good results. Great for light jobs and DIYers.
Very much so on the sticks. Mine live in the warmest and driest place I could find, and only come out when I need to use them.
I plan to keep my sticks into the 3d filament drybox. Damn this things is going to weight a lot now…
It’s in the same bracket of foodstuff as English mustard. I don’t suppose you know what that is either with your sweet spread American mustard. :)
Interestingly Marmite cannot be imported to Canada and quite a lot of other places. I think they have reformulated it for export but we still have the real stuff in the UK.
I eat the neon yellow mustard in the US. If that’s sweet…I don’t want to know what sour is.
Dang!
If I’d known English Mustard was so different,
I would have brought back a bottle for my friend who collects mustard.
English mustard is very similar to the Chinese sort – I’ve heard the stuff made for American Chinese restaurants is usually an English recipe.
Residents of the USA need not be deprived of proper mustard: https://www.amazon.com/Colmans-Original-English-Squeezy-Mustard/dp/B004AVG4Y6
Or, for that matter, Marmite: https://www.amazon.com/Marmite-Yeast-Extract-pack-125g/dp/B011D5LEVY
No it is not worth it,stick welders are better for higher amperage applications ,heavier sections.Typically the super market stick welder is low amperage and very difficult to control on thinner metal ,but they imply one can weld thin sections with it.
One can’t ,unless you are a very highly skilled welder.MIG is probably the best way to go for a hobbyist.
Of course other people may use the supermarket unit for specific purposes,where they may be very useful ,tack and spot welding for example.
That’s not my experience with this welder. Certainly it was my expectation, but I’m surprised an pleased to have been proved wrong.
100% agree. When these first showed up in the early 2000’s, maybe, but they now have sufficient control and capability for thin materials that when I started welding was still gas territory. When your top-of-the-line machine bottoms out at an unstable 20A, you can’t consider thin material without a LOT of skill. These machines will hold quite steady down to below 10A and allow a decent job even on sheet. A basic valved TIG torch and they are ok there as well.
Not the welder I would select for commercial use (I spend the dosh almost 20 years ago for for a Miller 150A, and haven’t regretted it) but in a pinch or for lighter use, suitable from thin to thick. Certainly not the class of machine I would select for full penetration groove welds on 50mm wall pressure vessels, but it’ll do it if you ave the time.
“A basic valved TIG torch’
What do you mean by that?
(I’m confused by what you mean as “valved”, vacuum tubes? B^)
manual shielding gas valve on the torch handle, rather than a gas solenoid (automatically controlled gas valve) built into the machine. They can be used with any constant current machine (stick welding power source; MMA welding in Europe, SMAW in the US) for scratch strike TIG.
Thanks Cliff!
You might post a photo of one your fillet welds on thin sheet metals onto the site;I would be interested to see that, because the welder is a very good price.
OK, but with the advent of digital cameras, photography has gotten incredibly cheap. I’d wager you could have afforded to post both a pre-ground and post-ground photo without having to adjust your budget at all.
I successfully converted my welder to a plating power supply, there is a short circuit cutoff that has to be fooled by passing a minimum spoof output voltage to the sens circuit via 2 diodes. This worked well enough to provide the 48 hours of 100A at about 5 V needed to plate a large rocket motor outer.
Do you have this written up anywhere? A friend of mine has been wanting those kinds of power levels to heat TI and other metals for the sake of changing their color- he makes things like metal dice and bottle openers- essentially fidget spinners for full grown men :p
I have not, but will consider it. I’ll load it on my website opend.co.za give me a month, I’ll have to re modify it.
One thing DC welders have a problem with is welding close to those 90 degree welding magnets. The field dramatically redirects the plasma resulting in terrible weld.
I tack if this becomes a problem, then finish the weld without the magnet.
Post pictures of actual weld beads please. Grinding them doesn’t show us anything unless you cut across the weld bead and show us what kind of penetration you get. Bottom line is show us the actual welding performance of the unit, not your grinding technique.
As the wise man said “Are you a Grinder, or a Welder?”
A grinder and paint make me into the welder I ain’t.
However, in this case the picture appears to provide a good idea of how much of the material was joined underneath the weld bead. I’ve seen a number of examples where somebody laid a perfect row of overlapping nickles without any real penetration.
As I’ve explained above at length, a tidy exterior means nothing and it’s what the weld is like inside that matters. As it happens there are problems with that weld if you look closely. But I am not the world’s best welder.
On a whim I bought an 80 A inverter stick welder (runs from 120 V AC) from Princess Auto (canadian equivalent to Harbor Freight) when there was a sale 18 months ago. I’m still learning to weld with it, but it’s encouraging to hear that they can produce good results.
Can anyone recommend some good beginner tutorials that feature this size of welder? I hope someday to be able to make nice welds on stainless steel.
I bought a couple of welding DVDs from Northern Tools a number of years ago (~$24?).
They are probably Out-of-Stock. They are at home, so I don’t have more info, maybe by a company that makes electrodes or welders.
Informative, they are able to let you hear the proper “sizzle” for various welds as well as showing good v. bad welds.
The cover art on these look familiar, so maybe these are the ones.
Also check the video section of your local library.
https://www.amazon.com/Arc-Welding-II-Steve-Bleile/dp/B004G8BKDS/ref=sr_1_13?gclid=EAIaIQobChMIpZjco9Hp5AIVl6DsCh3VLAWFEAAYASAAEgKY0fD_BwE&hvadid=241944633485&hvdev=c&hvlocphy=9019667&hvnetw=g&hvpos=1t1&hvqmt=e&hvrand=727800148287591101&hvtargid=kwd-3711639277&hydadcr=24663_10400925&keywords=welding+dvds&qid=1569334160&s=gateway&sr=8-13
Went to the comments to scan for marmite references. Was not disappointed.
I aim to please.
I’ve lazily been considering an inverter welder for a few years for mobile work, my mid forties murex affair is too heavy to move and too hungry for my Chinese generator, I took the cowards way out and bought a mid seventies diesel driven welder.
Your experience with the inverter has sold me on the inverter route for car repairs, the murex just eats cars.
A cheap welder will work if you are not using it for serious project. For a serious project, you have to take it seriously. Anyways, if anyone’s budget doesn’t fit, can buy a cheap welder but buy after good research. It is possible to buy a cheap and good welder as well.
For inexpensive leads, get a car jumper lead set; pull the cables apart for two leads, and put the welding connectors on.
A lot of inexpensive jumper leads are made of very thin wire with very thick insulation.
Very unlikely to be a useful upgrade on even cheap welding leads.
Basically copper is expensive and you are paying for the copper, so decent leads are going to cost decent money.
Looking on the website of my local electrical wholesaler they have 35mm2 welding cable for £5 per meter, just as a guide