For those addicted to automotive thrills, there’s always an underlying lust for more power. For those chasing a bigger number, forced induction is one of the most effective ways to achieve it. In addition to more grunt, you get a whole bunch of fun new noises, too. For those with a naturally aspirated car, here’s how you go about converting to forced induction.
Superchargers and Turbos
When we talk about forced induction, we’re talking about forcing more air into the engine under pressure. With more air available, it’s possible to fully combust more fuel, creating more power. The two most common ways of doing this are supercharging and turbocharging. We’ll be using the common automotive vernacular here, so those eager to bicker about terminology from the early 20th century aircraft industry best do it in the comments.
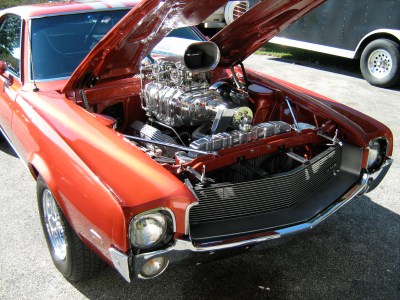
Superchargers are essentially air compressors that run off a belt connected to the engine’s crankshaft. As your engine spins faster, the supercharger spins faster, producing more air pressure, or boost pressure, thus giving the engine more air to work with.
Because the supercharger’s output changes with engine speed, they’re great for providing a power boost while maintaining a predictable, linear power delivery from the engine. Installation is also usually simple – involving an intake pipe, a few brackets and running a new belt and pulley.
Superchargers come with a drawback, however – they require a significant amount of power from the engine to run. It’s obviously less power than they add, but it is a parasitic loss that must be accounted for. They also tend to have a powerband issue. As the RPM of the supercharger changes with engine speed, if it’s set up to produce just enough boost up top, it’ll be a little underwhelming at low RPM. There’s always a tradeoff to be made.
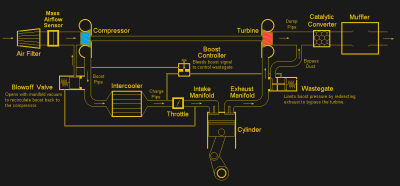
Turbochargers also compress air to feed into the engine, but instead of being run by a belt, the compressor wheel is spun by a turbine fed by the engine’s exhaust gases. This is essentially using what was waste energy to add power to the engine, eliminating the parasitic loss inherent in supercharging.
Because they’re not running in lockstep with engine RPM, turbos can create large boost throughout the rev range if set up properly, making it easier to provide low-end torque without sacrificing as much top-end power.
However, turbochargers suffer what’s known as turbo lag. This is the delay between putting your foot on the accelerator, and the exhaust gases spinning up the turbine to a level that produces boost. Choosing the right size turbo for your application and using a modern design can help reduce this, but older designs or poor part choices can produce significant lag. 80s turbo cars were renowed for this, with very sudden power delivery when coming on boost. In street and road racing applications, this can be difficult to deal with.
There’s also the case of complexity. A turbocharger install requires both intake and significant exhaust modifications, and is usually a more difficult install. You’ll also have a wastegate that dumps excess exhaust gas when the desired boost level is reached, potentially with a boost control solenoid in-line to control when it opens. Additionally, you may want to install a blow-off valve to dump excess intake pressure when coming off the throttle to avoid compressor stalls which can cause damage.
Whether supercharger or turbo is better depends on your application. Depending on your car, you may find there are more readily available supercharger or turbocharger kits, and you may have your own ideas about which you prefer. There’s no single right answer – fundamentally, it’s your build. Weigh up the pros and cons, and look at them against what you wish to achieve with the car. If you’re looking for an easy install and a moderate power bump, a supercharger may be the go. If you want huge power numbers and can deal with the hassles, turbos may be more your speed.
What’s Intercooling?
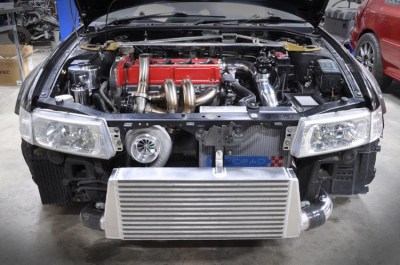
Both turbochargers and superchargers compress air to force more of it into the engine, heating the air. Hotter air is less dense, reducing power output, so ideally, we want to keep the air as cool as possible. Additionally, it increases the chance of the fuel charge detonating instead of burning smoothly, also known as engine knock. This can destroy an engine, so it’s best avoided.
To reduce this problem, many setups involve running an intercooler between the charger and the engine. This can be an air-to-air radiator or an air-to-liquid setup. This helps remove heat from the intake air charge, improving power and reducing the likelihood of engine knock. An intercooler isn’t always required, but without one, intake temperatures and the threat of detonation will limit your maximum power. Depending on your goals, this may or may not be a problem for your setup.
Getting An Installation Done
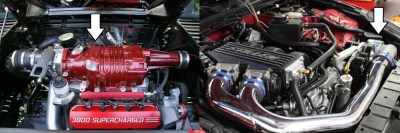
If you want to go with a supercharger, in addition to the compressor, you may need a bracket to hold it on the engine, a belt and pulley system to spin it up, and a pipe to connect the output of your supercharger to your intake manifold. Pulley size determines the gear ratio between the crankshaft and the supercharger; often several pulley sizes will be available with any kit to change the boost pressure. If a kit for your application isn’t available, you can always fabricate your own parts.
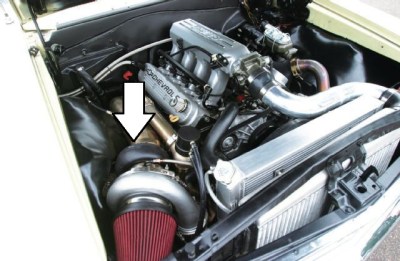
If you’ve chosen to turbocharge instead, you’ll first need a turbo. You’ll need an exhaust manifold to duct gases to the turbine, and a dump pipe to then take the exhaust from the turbo out the back of the car. You’ll need to hook the compressor’s output up to the intake manifold with a pipe too.
If your turbo has an internal wastegate, you’ll need to run a boost reference line from the intake to the wastegate actuator. If it has an external wastegate, you’ll still need to do that, but you’ll also need to install the wastegate into the exhaust. You may also choose to run a blow-off valve. This is a valve that releases pressure built up in the intake manifold when you suddenly come off the throttle. This pressure back-up can stall the compressor wheel in the turbo, causing damage, so a blow-off valve prevents this by venting either to atmosphere or back to the intake, pre-turbo. If you want that glorious “PSSHHHH” sound every time you come off the throttle, you’ll want to vent to atmosphere.
Whether you’ve gone for a supercharger or turbocharger, you’re now adding more air to the engine. Thus, you now need to add more fuel. For fuel-injected cars, the best way to handle this is by going with an aftermarket ECU. This allows fuel and ignition maps to be customized for your setup, allowing you to ensure the air-fuel ratio is correct, and that you’re not running too much ignition timing and causing detonation. Generally, employing the services of an experienced tuner is a good idea, as they’ll be able to set up your maps without blowing up your engine.
For carbureted setups, you’ll want to get yourself a carby designed to work with a boost reference to ensure the right amount of fuel reaches the cylinders. Again, the services of an experienced tuner are invaluable here to make sure you’ve got things right.
Finally, you’ll now want to only run on premium fuel. When your engine runs under boost, it’s key to use fuel with a higher octane rating to avoid detonation. Otherwise, you’ll have a boat anchor under the hood before you know it.
Potential Caveats
Switching your engine over to forced induction is a major change, and comes with many pitfalls. You may find that running boost into your engine leads to bending the connecting rods, destroying the engine. Your fuel pump may not be able to deliver enough fuel to keep up with the additional air, or your injectors may not flow enough. Alternatively, your engine may run just fine, but deliver so much additional torque that it burns your clutch out or destroys your gearbox on the first launch.
Some or all of these may happen to you, or yet another fun and terrible calamity may befall your car. The best way to avoid all of these is research. Almost every car out there has had someone poke around under the hood, and there’s plenty of knowledge out there on the limits of common parts. Everyone knows that the 5.0 in the Fox Body Mustang likes to crack the block around 500 hp, just as everyone knows the B6 in the Mazda MX-5 tends to bend rods when putting out high torque below 4000 RPM. Your community will be a great guide here. If you’re doing something unique and nobody knows, then good news – it’s your job to find out and share your results with everybody!
Going for forced induction isn’t easy. YouTubers will show you a $150 turbo and make it look like a cinch, but in reality, there’s a huge amount you’ll need to spend on supporting components. Mighty Car Mods did a great job busting this myth recently, revealing their eBay turbo install on a Toyota Yaris came in at an eye-watering $13,579 AUD when all was said and done. Oh, and it blew up within a few launches, anyway.
Despite the difficulties, there’s plenty of gains to be had if you’ve got the money and the mettle. Do your research, and be prepared to triple your initial budget when things start to go wrong. But most of all, grab your wrenches and a few pals, and have at it!
And then there’s the occasional Electrically Operated Supercharger, which is basically a brushless motor with an ESC driving a ducted fan.
Rig up a leaf blower to blow air into the carb?
The previous owner of one of my weird cars built a DIY supercharger using rotors from two shopvacs, driven by v-belts, into the existing unmodified carburetor. He said it worked surprisingly well except for the gasoline spraying out of the sides of the carb as a result of the boost, so after the second fire he discontinued that line of experimentation.
It’s fairly easy to calculate how much horsepower is needed to compress air at a given flow rate to a given pressure. Any electric supercharger that doesn’t require you to install two or three more batteries for the current required isn’t actually pressurizing the air.
48VDC to get the amps down to a reasonable level.
Tad more efficient to use a 48VDC in place of the alternator to just support the engine, as some commercial applications show. Though they do switch them off and utilize turbochargers after a certain RPM threshhold.
The roadkill guys did exactly that with 4 or 5 backpack style blowers. Results were somewhat disappointing, turns out leafblowers move a lot of air but don’t put out a ton of pressure.
Eventually they moved onto the ultimate version of this, which was to put a second engine on a trailer powering a supercharger, which compressed air for the first engine via a long tube.
I never said it was a sensible idea…
buuut, to be of any use it need several kW of power…
I seem to recall a setup that paired a turbo and an BLDC on a common shaft. Underboost (turbo lag) was dealt with by using the motor as a motor, overboost used the motor as a generator thereby adding drag and keep the boost within sane levels. I wish I could recall where I’d seen it. It seemed to be the best of both worlds.
it is basically the main idea behind the current Formula one power unit regulations
Exactly. Maybe HaD should do an article on the MGU-H. It operates at 40khz. Crazy tech!
Audi put something like that in the one-off they called the TT Clubsport aswell, though their electic compressor was separated from the actual turbocharger.
Two videos testing a commercial version of this:
https://www.youtube.com/watch?v=7a_J2X88fSE
https://www.youtube.com/watch?v=_yrxbcB4CwA
An electric supercharger is epically dumb. Why invoke several power conversion steps rather than a single 1.
Electric – to spinning thing that’s never quite optimised – to compressed air – inefficiently burn it – use its expansion to push a piston in a linear way – connect this to a rotating thing and away you go
Vs
Electric – to rotating thing
Perhaps I’m just pro big electric motors…
I’d like to stress how important important it is that you should always, always, always research first to see if anyone has boosted the motor you’re looking at. Aside from all the great points in this article, you will run into other things like the way in which your car meters air going into the engine. In some instances you can use a piggy-back computer to adjust your air/fuel ratio and other times you may need install a whole new air metering system because the stock one just can’t do it. Also, will the stock transmission cooling setup be able to keep up with your new cooling needs. In my experience it’s always best to start with a motor that is already turbo/super charged and then upgrade from there, unless you have deep pockets and/or a ton of time on your hands.
This is pretty much what I thought of, when I read “you get a whole bunch of fun new noises, too”.
Yeah…the noise a spun bearing makes, for example. Or the one of a rod punching a hole through the engine block.
Not all engines are built like a tank, most N/A ones will throw rods, pistons and headgaskets all over the place with forced induction, because the compression ratio doesn’t fit, just as an example.
There are two general ways to use a carburetor with forced induction: put the supercharger/turbocharger in front of the carb and modify the carb to handle pressurization, or put the carb on the front of the super/turbo. The latter is vastly easier, because the carb needs very little modification, but then you have a big hot pressurized air/fuel charge in and behind the sup/turbo. That’s a significant safety hazard, and that rises to a huge safety hazard if you try to use an intercooler. There were a ton of kits for inline engines that replaced the intake manifold with a supercharger, and bolted a slightly larger carb on the front of the supercharger, for a very tidy installation.
Some carbs aren’t too difficult to modify to run under boost. It’s also possible to enclose the carb inside the intake, so the only pressure differential it handles is the one it’s used to in the venturi.
If you want to get experimental, historically many aircraft mechanically coupled the turbocharger to the engine crankshaft, so rather than having a wastegate, you dumped your excess spin into the engine and increased the power. These were called turbocompound engines and they were extremely successful in the last days of large commercial piston-powered aircraft. As the automotive writer LJK Setright once wrote, if you get particularly enthusiastic about turbocompounding, pretty soon your mechanical engine is mostly just serving as a source of hot air for your turbocharger, and then you’ve reinvented the turbojet engine. People also did a lot of research on using an epicyclic gear train to attach the compressor, crankshaft, and turbine, to make a system where you could source or sink power between the three elements at will.
It’s surprisingly easy to build your own intercooler. Companies sell intercooler cores as bulk material, so you size it for your application and weld on header tanks for the charge and coolant paths.
Current formula one power units does all that. motor-generator on the crankshaft, motor-generator one the turbo charger. Engine braking can charge battery, excess turbo energy can charge the battery or compound the engine, battery energy can compound the engine or spin the turbo charger
Rate of charge for the battery is a problem, that is why a few batteries have a portion as super caps to make an “electronic flywheel” used for take off energy when starting next from standstill.
the turbocompounding is not reinventing the wheel, it allows you to get fairly high compression ratios that are today matched or exceeded only on very large turbofan engines. Also because the piston engine has a fixed compression ratio, you get much better efficiency compared to pure turbines when you run the engine at lower speeds.
If you are interested in some really exotic super/turbocharger ideas, https://en.wikipedia.org/wiki/Turbonique is fun reading: tiny rockets attached to supercharger rotors or to the differential, burning monopropellant. They apparently worked pretty well, too, aside from sometimes exploding, more than doubling horsepower in an extremely small package size.
Well, that little rabbit hole introduced me to highside and lowside flips.
Thanks!
A turbine driven by a propellant is how cartridge starters for jet engines work
many liquid fuel rocket engines start their turbomachinery with a pyrotechnical cartrige.
The F-16 figher gets it’s emergency power from a monopropellant driven turbine…only downside is that it uses hydrazine.
I love how “common use” of terms redefines the terms… A supercharger is simply an air compressor feeding an internal combustion engine. A turbocharger is a type of supercharger that sources its power from the exhaust stream.
Intercooler is another casualty of “common usage”. Inter- means between, as in between serial stages of compression; to cool the air prior to the next compressor stage. Usually seen on 2 stage air compressors you find in a shop.
Aftercooler is the technical term for cooling after the last stage of compression
Oh, but the piston(s) supply the next stage of compression!
B^)
my mechanic buddies get mad when i call it a charge air cooler
Have we talked about insurance yet? I’ve heard horror stories about insurance companies refusing to pay when the car they covered was modified. Any truth to that?
these day not having the extensive emissions approval required of cars now is probably almost as big an issue
I’ve never understood how extracting power from the exhaust is ‘free’ — doesn’t putting a turban in the exhaust path contstrict the airflow and make it harder for the engine to push out the exhaust gasses ?
There is some restriction but the airflow is already restricted by the exhaust valves and the turbine is a mixture of impulse and reaction. The energy you get for free is the energy that is no longer used to make noise out of the exhaust
Shoving a turban up an exhaust pipe would probably kill the engine.
It might kill the person wearing it too!
B^)
A well designed turbo is allowing the hot, pressurized exhaust stream to expand and cool down, while extracting energy from the process, rather than just dumping it into the atmosphere. In a standard exhaust, you dump heat along the length of the entire exhaust pipe and quite a bit out of the back. With a turbo you extract most of the heat at the turbine through expansion. There is back pressure associated with a turbine, seen at the turbine inlet. But, you’d kind of expect that since there’s well above ambient pressure going into the piston as well because of the compressor.
I am currently turbocharging my “Locost” that uses a 99 Miata motor. The turbo and plumbing is quite cheap using Ebay parts. It comes to around $500 for the parts with an intercooler. I did the fabrication myself. The turbo may only last a couple of thousand miles but at under $100, and given that I will probably only drive that much in a year, I can simply replace it when needed. The hard part is the ECU. I have spent a few weeks on that so far. I decided to build a Megasquirt 2 kit but it required a lot of mods even for such a common motor. It would probably have been better to get a “plug and play” ECU. I am now tuning the ECU and that is going to take a lot of work especially getting the A/F mixture right for turbocharging. Just getting the motor to start has been difficult. I was expecting a good base tune to be available for the Megasquirt. Now I am thinking I should have gone with rusEFI or Speeduino given the amount of work I have had to do anyway.
Speeduino will probably be more work than megasquirt because there are way more users for megasquirt, so you’re much more likely to find a reasonable configuration file close to your system.
I am turbo-ing my car, but the engine and transmission are made of glass, I can’t wait to install and get a turbo fabricated, im thinking my budget will be about $5,000 since I don’t know what I’m doing and I’m planning for maybe 20hp over stock. By the way, anyone know what tuning is?
I saw the video where some guys used a handful of backpack blowers to try supercharging a car engine. It was doomed to fail by their design.
They made an ab-so-lute wreck of the manifold for the blowers.
Hard corners and too small of a “main” pipe as it progressed from the blowers.
I’ve worked a bit with just one blower for my yard work. A small difference in the pipe size and bends bends have a dramatic effect on the airflow and pressure at the end of pipe.
Take a look at engine manufacturers efforts for intake tracts (from filter to cylinder port) if you have any doubts as to this.
doesn’t matter what you do, such a blower is useless as a super charger
Good of you to give a shout-out to the MCM guys! Love their work. Also, while you’re correct in mentioning that turbo lag is no good for racing and smooth power application, you did fail to mention that it can still stick a stupid grin on your face when you boot it… nothing, nothing, nothing, ALL THE POWER!
There’s another parameter you can tweak: cylinder compression. Lowering the compression allows you to increase the boost pressure while lowering the risk of engine knocking (premature detonation).
As always, it’s an optimization problem. You bolt on all the stuff and then tweak and tweak and tweak all the parameters until you get the maximum power with the best throttle-reaction and the maximum reliability.
Reliability is the relative thing. For a drag car, you only need the engine to be reliable for 1/4 mile and a bit. For a racing car you need it to be reliable for the length of the race plus a bit. :)
You can also use water injection to cool the intake air.
Basically, if you Inject the fuel before the compressor, it also helps with cooling the intake air.
methanol is a better choice, as it’s flammable, increases the octane rating, will cool the charge and there’s a fair bit of water from burning it, which helps with expansion.
+ 1 for water injection, I have a supercharged Rover V8 in my TVR, that’s where I am going next. You can also blend in the methanol so use a mix of water/methanol (which in itself isn’t flammable so one less thing to catch fire under the bonnet).
Then I was thinking how about ethanol/water, as I do homebrew I could easily brew up (read: hack) a few gallons of weak ethanol from sugar really cheaply, and freeze distil it. Making sure the yeast is filtered out first of course!
That would also be biofuel -win-win! (As if I’m worried about emissions from a 4l supercharged V8….)