Throughout the spring, some Bay Area residents from Marin County to the Presidio noticed a sustained, unplaceable high-pitched tone. In early June, the sound reached a new peak volume, and recordings of the eerie noise spread across Twitter and Facebook. Soon after, The Golden Gate Bridge, Highway, & Transportation District, the agency responsible for the iconic suspension bridge’s maintenance, solved the mystery: The sound was due to high winds blowing through the slats of the bridge’s newly-installed sidewalk railing. Though a more specific explanation was not provided, the sound is most likely an Aeolian tone, a noise produced when wind blows over a sharp edge, resulting in tiny harmonic vortices in the air.
The modification of the Golden Gate Bridge railing is the most recent and most audible element of a multi-phase retrofit that has been underway since 1997. Following the magnitude 6.9 Loma Prieta Earthquake in 1989, The Golden Gate Bridge, Highway, & Transportation District (The District) began to prepare the iconic bridge for the wind and earthquake loads that it may encounter in its hopefully long life. Though the bridge had already withstood the beating of the Bay’s strong easterly winds and had been rattled by minor earthquakes, new analysis technology and construction methods could help the span hold strong against any future lateral loading. The first and second phases of the retrofit targeted the Marin Viaduct (the bridge’s north approach) and the Fort Point Arch respectively. The third and current phase addresses the main span.
Bridges Fight More Than Just Gravity
A suspension bridge is meant to support its own weight and the weight of all the automobile and pedestrian traffic that it carries. The road deck is supported by vertical suspenders, which hang down from the swooping suspension cables. These suspension cables, loaded entirely in tension, transfer their weight into the towers (of which there are typically two), acting in compression and sending the force into the ground.
Suspension bridges are very efficient in resisting those gravitational forces, but like all other above-ground structures, they must also resist the horizontal forces applied on them when the wind blows or the ground shakes. When the wind blows perpendicular to a bridge’s span, the road deck has a tendency to sway like a clothesline in the breeze. In extreme cases — most notably in the 1940 collapse of the Tacoma Narrows Bridge — the rocking of the road deck in the wind can start a feedback loop that eventually causes the bridge to twist itself apart. (With the Tacoma Narrows collapse in mind, The Golden Gate Bridge was reinforced in the 1950s with a series of trusses to help provide additional torsional rigidity.)
Resisting the Wind (and Dodging It)
While the Golden Gate Bridge has safely resisted eight decades of winds whipping from the west into San Francisco Bay, engineers were still concerned about the long term viability of the bridge’s lateral system. The District’s public affairs manager, Paolo Cosulich-Schwartz indicated that the bridge is currently safe for winds of about 68 miles per hour, but the area can sometimes experience gales that exceed 100 miles per hour. Therefore, any reduction in drag or exposed transverse surface area would be beneficial to the bridge’s lateral system.
Replacing the original, chunky pedestrian railing with something more svelte was a relatively simple way of reducing the surface area exposed to wind. The work could be completed at the level of the road, without temporary scaffolding, and without even disrupting the majority of the bridge’s traffic. Even this seemingly minor modification, when extrapolated across the length of the bridge, would have significant structural benefits: The new railing decreases the exposed surface area by thousands of square feet, meaning a likely reduction of hundreds of thousands of pounds of lateral wind loading.
However, the design of the new railing had more than just aerodynamic considerations. Cosulich-Schwartz explained, “When bridge engineers designed the original railing, they wanted pedestrians to feel secure, but they also wanted motorists to take in the majestic views of the ocean to the west and the city of San Francisco to the east. So they came up with this slatted design that is solid, but when you’re driving by at speed, they appear to be transparent.” The new railing had to meet the functional and aesthetic requirements of the original design, while still reducing the surface area.
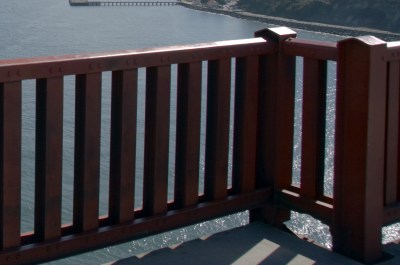
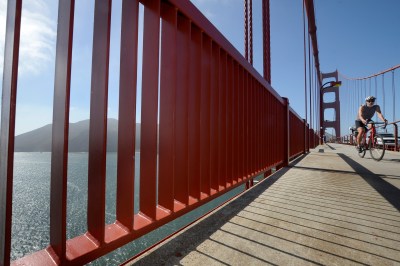
Prior to construction, The District performed a wind tunnel analysis of the new road deck, including the modification to the westmost railing (visible in the Golden Gate Bridge District’s wind tunnel testing video, on the left at the roughly 2:53 mark). However, the one twentieth scale test did not provide sufficiently fine-grained results to predict that the railing would shriek in high winds. “In our study and analysis, it was revealed that there would be some sound, but at no point was it shown that we would hear the level and degree of sound that we heard on June 5th,” relayed Cosulich-Schwartz.
Bridge over Trebled Water
That sound you may have heard:
The Golden Gate is whistling. 💨pic.twitter.com/ItOMTm8Z08
— Brodie Brazil (@BrodieNBCS) June 6, 2020
The District is well aware of the public response to the bridge’s new vocal stylings. Regarding their plans for addressing the issue, Cosulich-Schwartz disclosed, “We’re doing more analysis and engaging experts in the field to better examine precisely and under what conditions the sound can be expected to occur. And we’ll also be investigating any mitigation efforts to address the sound.” The District may even conduct another round of wind tunnel testing with a full-scale segment of railing, which could then lead to an in-situ remediation program. A retrofit of the retrofit.
The installation of the west side railing is already about 75% complete as of this writing, and The District has no plans to turn back. In addition to the railing work, the District is working to give the bridge a more aerodynamic profile by installing a new quarter-circular fairing at the base of the western sidewalk. Similar to the one installed on the Whitestone Bridge in 2003, the fairing would reduce the wind load on the bridge by covering exposed flat surfaces and streamlining the bridge deck’s wind-facing side. So if the Golden Gate Bridge develops a bellowing baritone voice in the coming weeks, you already know why.
Even with state-of-the art design methods, our biggest structures sometimes surprise us once they’re complete. None of the facade consultants at London’s 20 Fenchurch tower predicted that it would be melting cars on the streets below. And in spite of thorough wind tunnel testing, skyscrapers still produce deafening tones of their own. The engineering team behind the Golden Gate Bridge’s retrofit seems to have exercised due diligence, but sometimes the difference between plans and reality can be heard loud and clear.
My father in law worked on this one after it failed in 1940.
https://www.youtube.com/watch?v=j-zczJXSxnw
It remembers me whales singing, that along with the bridge remembers me Star Trek IV. May such things be really related?
Only because of the Dora episode with the singing rocks and because of the Eleanor chase scene in original Gone in 60 seconds. Then of course whales are sometimes accompanied by a bow of petunias, and it was aunt Petunia that was roasted by Dumbledore’s howler, Illuminati confirmed.
Cute list. I see that today Star Trek is above your age grade, but don’t be sad as some day you’ll grow up to watch movies from the higher shelf.
Don’t hurt yourself when getting off that high horse
Transparent aluminum!
I always thought Scotty picked up the keyboard and interface for that chemical design software pretty quickly. I guess that’s why he’s Chief Engineer.
May the script writers be ever in your favor.
Pretty sweet. Design in some pleasing harmonics next time.
Better specify “pleasing” in some detail, lest you discover that it’s now pleasing to a fan of opera, acid rock, or fingernails on a blackboard…
What amazed me about the ‘Walkie talkie’ Fenchurch Street debacle, is that they gave a building a concave face, covered in glass, and DIDN’T think that it would focus the sun’s light somewhere. First sunny day, and it was melting cars on the streets below.
Had to look that one up. The “Fryscraper”. XD I love it.
It’s the U.K. We don’t expect sunny days.
I’ve heard that..
You can hear the same sound at any truck stop on a windy day. The wind blowing around the trailers does this.
Those tie-down straps that are used to secure loads on flatbed trucks must be twisted a turn or two if there is a section that is in the airstream lest it vibrate so bad it will self destruct at some point. It’s already strained to hold the load and now it has the peak of the sine wave added to that. If the slats had some variance in spacing and angle it might spoil further problems unforeseen.
Much like the varying sizes/pitch of the blocks making up a the tread of a vehicle tyre.
The link to the howling buildings had Beetham Tower in Manchester,
my family stayed in its hotel several years ago.
(no one mentioned its howling history)
Looks like the fix should be rounding the edges of all those flat bar stock slats. Could do it with a handheld router with a diamond grit roundover bit. If the railing sections are powdercoated instead of painted, that will present a challenge to such a procedure.
An in-place fix could be gluing on some rounded plastic edging to the windward sides of the slats. It would have to be tough to withstand windblown grit and sunlight exposure. Then there are people, some of whom will pick at the edging until they rip bits off, just because they like being destructive.
If there’s no readily available off the shelf edging, the amount required should make the cost reasonable for a custom production run, plus additional for years worth of maintenance. But will the long term cost be more than the short term cost of removing the railing sections, stripping them, reshaping the edges, recoating, then reinstalling?
I don’t think a simple hemispherical edging is going to solve the vortex shedding that is likely causing this issue. What might have worked if they had done it from the start is wrapping a thin steel cable in a spiral around every slat (or possibly every other slat) embedded in the powdercoating. Similar to many car antennas.
I’m a little surprised nobody caught this. Aero acoustics is a fairly well known, if at times poorly understood, phenomenon at this point. There’s even special windtunnels with echo dampened measurement sections to test such things.
Perhaps the lowest bid got the job.
That’s resolved something I’ve Always wondered about my car arial!
I agree with you. Came down to the comments to say the same thing. But I think the more appropriate tool would be the one they use to chamfer the edges of plates in preparation for welding.
They could have simulated the acoustics. If you can afford a wind tunnel, you can afford to feed the fluid dynamics simulation data, which you likely have, into an acoustics code. That will probably become more of a standard practice. All this was discoverable with modern tech. They just chose a firm that did not think about that scenario.
They don’t need to simulate acoustics. Why throw money at a scale model and a wind tunnel if you can simply install a short prototype life-size railing section on, hm, let’s say, the Golden Gate Bridge?
I guess in Germany one would simply mount the prototype section on a small flatbed truck and go for 100mph ride on the Autobahn. Well, did that actually myself, with a series 3 BMW and the railing on the roof (which limited the mass of the railing including mount to 50kg; the mounting was good for 125mph).
I’ m somewhat surprised that they didn’t adopt the staggered rail approach.
In the UK they put these pedestrian safety railings near schools.
Drivers can see thru’ at an angle for small children, shorter than the railing.
https://www.irishfencing.com/wp-content/uploads/2015/06/F02-Pedestrian-Guardrail-PG2-50.jpg
maybe use a few types of fence posts that have more notes , at the right wind and driving speed you could get a little tune going….also need a diving board.
Only in Democrat run places can they screw up infrastructure “repairs”.
Testing a small section of full-scale railing seems a no-brainer as an engineering precaution.