How cool would it be if there was a material that couldn’t be cut or drilled into? You could make the baddest bike lock, the toughest-toed work boots, or the most secure door. Really, the list of possibilities just goes on and on.
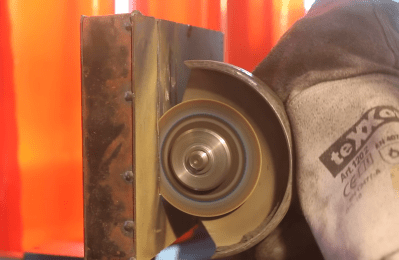
Researchers from the UK and Germany claim that they’ve created such a magical material. It can destroy angle grinder discs, resist drill bits, and widen the streams of water jet cutters.
The material is made of aluminium foam that’s embedded with a bunch of small ceramic spheres. It works by inducing retaliatory vibrations into the cutting tools, which turns the tools’ force back on themselves and quickly dulls their edges.
The creators have named the material Proteus after the elusive and shape-shifting prophet of Greek mythology who would only share his visions of the future with those who could get their arms around him and keep him still. It sounds like this material could give Proteus a run for his money.
The ceramic spheres themselves aren’t indestructible, but they’re not supposed to be. Abrading the spheres only makes Proteus stronger. As the cutting tool contacts them, they’re crushed into dust that fills the voids in the aluminium foam, strengthening the material’s destructive vibratory effect. The physical inspiration for Proteus comes from protective hierarchical structures in nature, like the impact-resistant rind of grapefruit and the tendency of abalone shells to resist fracture under the impact of shark teeth.
How It’s Made
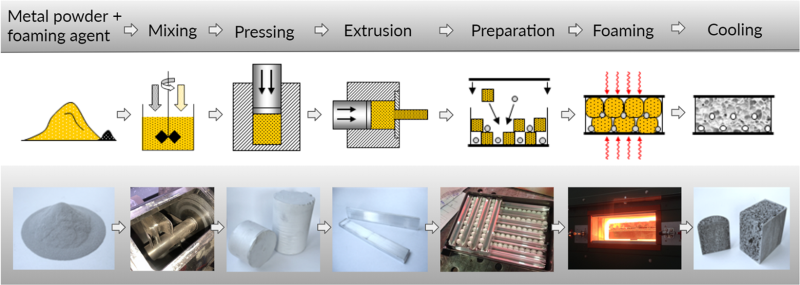
At this point, Proteus is a proof of concept. Adjustments would likely have to be made before it can be produced at any type of scale. Even so, the recipe seems pretty straightforward. First, an aluminium alloy powder is mixed with a foaming agent. Then the mixture is cold compacted in a compressor and extruded in dense rods. The rods are cut down to size and then arranged along with the ceramic spheres in a layered grid, like a metallurgical lasagna.
The grid is spot-welded into a steel box and then put into a furnace for 15-20 minutes. Inside the furnace, the foaming agent releases hydrogen gas, which introduces voids into the aluminium foam and gives it a cellular structure.
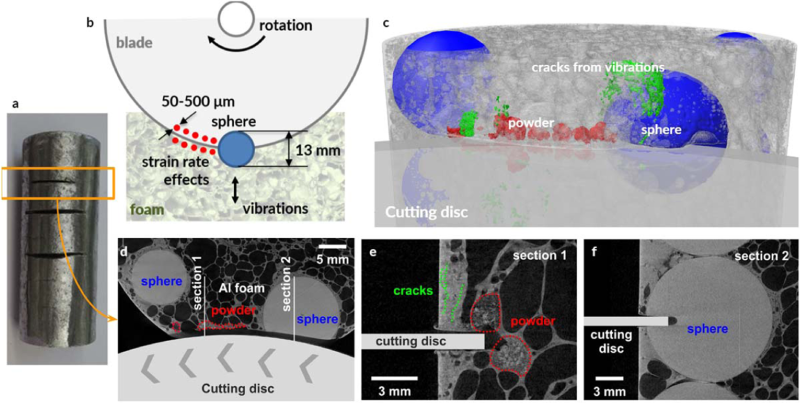
According to their paper, the researchers tried to penetrate the material with an angle grinder, a water jet cutter, and a drill. Of these, the drill has the best chance of getting through because the small point of contact can find gaps more easily, so it’s less likely to hit a ceramic sphere. The researchers also made cylindrical samples without steel cladding which they used to test the compressive strength and prove Proteus’ utility as a structural material for beams and columns. It didn’t fare well initially, but became less compressible as the foam matrix collapsed.
The creation process lends some leeway for customization, because the porosity of the aluminium foam can be varied by changing the bake time. As for the drill bit problem, tightening up security is as easy as adjusting the size and/or density of the ceramic spheres.
In the video after the break, you can watch a chunk of Proteus eat up an angle grinder disc in under a minute. Some may argue about the tool wielder’s technique, but we think there’s something to be said for any material that can destroy a cutting disc that fast. They don’t claim that Proteus is completely impenetrable, but it does look impressive. We wish they would have tried more cutting tools like a gas torch, or experimented with other destructive techniques, like plastic explosives, but we suppose that research budgets only go so far.
Images via Nature
Either this has been covered here a couple weeks ago or I am having a mental malfunction.
same for me
Hmmm, I took a look but I don’t see an article where we’ve previously covered this material/research.
There definitely hasn’t been an article on this come into my RSS feed in the past year, so… ?
Mandela effect in it’s full glory.
welcome to modern hackaday
Wow, thanks for the downer.
Oi, that’s a different Dan to me!
Good article.
Mike – Don’t worry if you have an occasional dupe; you’re only human (as far as we know… I mean one of you may be an AI, who knows… :P ) the amount of submissions you get it must be difficult to track.
Yeah, it was quite noticeable when the “Benchoff” AI server was unplugged.
I’ve noticed that happening a lot lately. I didn’t take the time to look for the doubles when I saw them, I just scrolled past and imagined there was some valid reason. Next time I’ll check. Maybe the drafts are accidentally making their way to the front page then get actually published and make their second appearance?
Relax. It is called ESP …
I can’t comment on your mental health but I do suspect you’re reading Slashdot.
The trick may be to cut it using an ultrasonic blade with resonant feedback, that way you might be able to shatter the beads. Although it might be more efficient to use some sort of high temperature cutting tool, be it perhaps a laser or plasma arc, to melt your way through it instead.
A masonry bit on the end of an impact drill would probably have little trouble going through this stuff, I think.
Plasma cutter?
not a question of that
I hate to rain on the parade but this material isn’t really anything new and would not be particularly hard the cut. The safe and vault industry has used ceramics and ball bearing included “hardplate” for literally decades. Practically every modern drive up ATM has ball bearing included hardplate (NCR, Diebold, etc). The balls deflect and dull HSS drill bits and are designed to chatter and fracture tungsten carbide bits. You pack the hole with a wooden dowel or 2 part epoxy then drill right thru the stuff with a carbide burr. Ceramics were also used for years but had a fatal flaw. You just alternate punching and drilling. It crumbles and is fairly easy to defeat with the right equipment. Materials most people perceive as “hard” or drill resistant fall well short of even the most mild examples of hardplates found in the safe and vault industry. Take AR500 ballistic steel plates for example. Its widely considered a very difficult material to machine and is notorious for burning through even premium drills bits (HSS, Titanium, Cobalt etc). You can take the standard $8 1/4″ carbide bit commonly used in the S&V industry and punch a hole straight thru 1/2′ thick AR500 plate in 3 to 4 seconds. You can even keep drilling holes thru that same AR500 plate 100 or more times with that same $8 bit. This is no exaggeration. AR500 is literally 10-15 points lower on the Rockwell C hardness scale than what is generally considered to be the mildest forms of hardplate in the S&V industry (typically using high carbon tool steels such as D2).
I’m actually surprised this company went through all this development effort without doing a bit more research into other “uncuttable” materials that might be used in other industries or fields of work. This type of stuff is honestly old news in the safe business. If you’re really looking for what are truly some of the most “uncuttable”/drill resistant materials then look back at some of the numerous carbide embedded hardplates that have been patented over the years – names like Relsom (Mosler), MaxAlloy (Schwayder) and Impervium (Diebold). And those were being used 40-50 years ago. Diamond drills were eventually developed for even these impenetrable barrier materials and these are now standard equipment in any serious safe technicians drill kit.
Over the years as the price of tungsten has increased (thanks China…) the industry has seen a continual trend of safe/vault manufacturers moving away from tungsten carbide materials and towards more “active” types of hardplates to reduce cost. These active plates use spinning/rotating/moving elements to bind and chatter against cutting equipment which effectively turns the tool against itself (originally hardened ball bearings). This approach is often used alongside a reduced amount of carbide in order to maintain the total drilling time within an acceptable range. Glass “relocker” plates have also started to make a comeback for the same reasons.
In my opinion the most drill resistant (“uncuttable”) materials presently being manufactured are found in US Govt “Red Label” GSA containers typically used for storage of classified materials. All of the current GSA manufactures pretty much use the same two designs and suppliers for hardplates. Both types utilize a tungsten carbide matrix material and one type also includes strategically placed freely spinning balls impregnated within that hardened matrix. Most hard-to-machine or ‘wear resistant” materials have to make a compromise between hardness (eg. ceramic) and toughness (eg. AR500). You typically can’t have both at the same time and in the safe world a good understanding of this compromise helps technicians determine the proper equipment and opening methods to use on a particular opening. Get it right and it’s just another quick and routine job. Get it wrong and you could end up spending several days on that safe because Plan A is now off the table. The current GSA “red label” stuff is so formidable because it is both extremely hard AND insanely tough which seriously limits your potential opening options. No shortcuts truly exist which is exactly per the govt spec. You’re going to be drilling for quite a while and could very easily end up burning through several hundred dollars worth of carbide/diamond drill bits. It’s so insanely difficult to penetrate the 6- sided hardplate box surrounding the internal lock mechanism that the government has approved procedures that call for using carbide hole saws and chop saws to destroy the entire face of the container to gain entry (Fed STD 809). It’s truly impressive stuff and probably the closest thing to an “uncuttable” material currently being produced.
Thank you for sharing your knowledge on this subject. Perhaps you can confirm or deny my one suspicion – is the material brittle when flexed?
Interesting, thank you for the context.
Do you think the usefulness of this material is it’s lightweight? For bike locks, being able to have the performance of an ATM plate (or approaching it) while not having the weight or size needed for ball bearings would be very handy.
Looks like we found a pen tester folks.
As a machinist who has worked with solid monocrystalline diamond tooling and everything in between this is pretty cool information.
I’m already trying to think of how I can destroy all this stuff with CBN and exotic geometry or portable water jet cutters loaded with CBN grit (if it even exists or is done yet- betting it has)
The nastiest stuff I have ever personally heard of that been around me is a high manganese alloy plate material used in industrial shot tumbler machines and other things like that, and I found the name of the alloy at some point but I can’t remember what it is right now. Supposedly destroys carbide anything instantly, It lines some of the industrial tumblers we use for tumbling titanium forgings in a Goff tumbler
I used to work on ATMs and can vouch for what he’s saying. Myself and two Diebold techs spent most of a day and 15 carbide bits getting into an ATM who’s electronic combo lock had failed.
You’re not loosing the plot Somun.
Same material, different linked article.
Having been here since the beginning, never presume.
I wonder if this stuff would have much tensile strength. I can’t imagine a bike lock made from aluminum foam would be all that effective under strain applied by crowbar (which doesn’t need to maintain a cutting edge to work, obviously).
That’s just what I was thinking. The sustained contact of a rotary tool might have feedback weaknesses that aren’t present in an impact tool (hammer family) or sustained pressure tool (prybar family) or heat.
I don’t know how the technology works but there are bicycle U-locks which effectively resist saws but can easily be popped by a car lift jack. I expect there to be a similar weakness here.
I was actually thinking going the other way with a temperature attack, freeze the lock with a can of “canned air” duster, then give it a blow with a hammer.
I’m also wondering how this material responds to torsion or blows.
Maybe the ultimate bike lock has a conventional high-strength steel core, and a layer of this stuff to resist battery-powered angle grinders with cutting discs.
I’m curious how the ceramic would affect the thermal properties of this. It seems the heat would all go into the aluminum initially. The ceramic would heat up slowly but I wonder if it would then give it’s heat back to the aluminum keeping it hot for longer than expected. The counterpoint is that the foam has lots of surface area to radiate heat off.
I was thinking “if it is so tough on angle grinder blades, make the angle grinder blades of this stuff”
Solution for bike theft would be get rid of material and mount saw blade on this grinder. Then cut with it a few thiefs hands and plobrem might dimish a little.
A good solution for bike theft is a $30 bike.
I would apply Gallium. Or hand saw.
alum or an electrical arc could make light work of it. it’s only metal after all. I first heard about it from a dominatrix on twitter who wanted to make chastity cages from it.
You may have the only legit comment that has ever made me curious to join Twitter.
Materials science dominatrix feed is a combination of things I never thought I’d find appealing separately, until they were together, much like this material, which is creative stuff
I wonder how it would fair against a sledge hammer or other generally brute force attacks.
The article makes it sound like it has similar properties to a non-newtonian fluid.
“The ceramics embedded in this flexible material are also made of very fine particles which stiffen and resist the angle grinder or drill when you’re cutting at speed in the same way that a sandbag would resist and stop a bullet at high speed.”
This makes me wonder about something that could cut at lower speed. But the only thing I can think of is a shaper.
The real is what happens if you hit it with a bullet? Considering it hasn’t been touted as a new body armor material that it probably doesn’t stand up to a single high impact like that.
At a guess, I’d say spalling, dissipating energy laterally.
Are you american by chance?
Or Russian?
B^)
Given the difficulty of cutting or reshaping it, you’d have to make it to order in the exact size and shape needed. That could get expensive.
Exactly. Makes machining the material tough. Drop-forge would perhaps be effective for shaping it, while at the same time turning the ceramic spheres into powder, and so strengthening it.
My guess it that it may be possible to mold it a bit like sintered metal parts.
Given it isn’t mentioned, who else thinks this is probably shatter-prone?
I don’t think so, possibly under the same conditions you can get aluminum to shatter, i.e. douse it with LN2 then whack it. It’s kinda like glass filled resin. It’s tougher than the resin, and not brittle like the glass.
It sounds like the spheres will shatter, but then they will find their way deeper into the aluminum foam. This is discussed in the article, and it makes the material stronger.
“The physical inspiration for Proteus comes from protective hierarchical structures in nature, like the impact-resistant rind of grapefruit and the tendency of abalone shells to resist fracture under the impact of shark teeth.”
I came across the abalone shell example in a piece about metamaterials a while back. Basically it’s like bricks are laid, offset layers, stopping fractures from running so easily. Anyway, got me thinking then about maybe leveraging it for 3D printing, making sure layers are offset to improve strength. Was something I was going to test when I got a round tuit and a 3D printer of my own.
Layers are usually at 90 degrees angles from the one above or below. That’s basically the same thing, no?
Offset layers is not enough. You need an interface that will create an alternative path for the fracture and ideally that layer will be tailored so that the crack will bifurcate.
In 3D printing, you could probably achieve this by having a deficient aggression between the layers. Since pla is a brittle material, you’d probably get a stronger part of you can control this effect successfully. You can find more information on https://www.researchgate.net/publication/228413471_Development_of_Failure_Tolerant_Multi-Layer_Silicon_Nitride_Ceramics_Review_from_Macro_to_Micro_Layered_Structures
Aggression=adhesion on my phone
I cannot picture how that would work. You mean alternating layers of different materials? In my experience, PLA fails exponentially faster once a layer has been compromised, regardless of how good or bad the layer adhesion is. Perhaps impact resistance is a different animal compared to tension/compression resistance.
By the way, does it remind anyone else of the “Foam Metals Corporation” in Frontier Elite and Frontier First Encounters? Said to manufacture the foam metals used in starship hull construction and rumoured to contain buckyballs.
It does now! Although had I played Elite when I was a bit older I probably would’ve associated those with Aerogels.
All this vibration relations got me thinking: where is “the most versatile substance on the planet, and they used it to build a Frisbee” joke?
Very cool materials research. But the way to get through this would be a hammer and chisel.
The whole idea looks a lot like the the proverbial hidden nail in the timber to me. That one eats wood saws like this one disk grinders. I wonder if a disk for chopping ceramic tiles would cut this stuff easily ?
Yes, it probably just needs some work developing a good blade type, otherwise it’s like using your wood rip blade on angle iron and going “WTFBBQ!!! Cut proof!!!111”
Lol
That’s actually a cool idea for a bike chain. Embed D2 rods inside soft wood and watch as all the thieves dull their blades. However I think it would also act like a saw/blade guide, so win some lose some? Well, the weight would give it away anyway.
This reminds me: one time we were chopping down a dead tree with a chainsaw and had to resharpen the chain several times, for something that was about 30cm in diameter (1ft). The chain was actually sparking against the dead tree carcass. Later found out it was some sort of exotic and really expensive hardwoord, forgot which, used mostly for sculptures. The initial owner had died and we were clearing out the garden, in case anyone is wondering.
I think that a sodium hydroxide solution would work to dissolve the aluminum foam that holds the ceramic spheres.
Perhaps mentioned in a podcast you listen to?
I wonder about hand saws.
Me too. Any reasonable hacksaw makes very quick work of aluminium, and aluminium foam even more so. Given the ceramic balls are large (13mm) it’s hard to see you couldn’t work around them with a hacksaw.
Also, a strong dust extractor to remove the ceramic dust might change things?
cant be cut proof if its liquid.
(brandishes thermal lance)
If this was as good as they are trying to imply, they would have tried cutting it properly with an angle grinder.
The disk seems to have no problem cutting into the material, and only has issues when immersed – and they have problems with normal steel doing that!
They should have started at the top edge and moved down, and the fact they didn’t shows that they are trying to hide what it is really like…
Looking at the start of the cut I’d say it is no more difficult (and maybe easier) to cut that a reasonable steel in the same sized block. So what exactly is the story?
What about using diamond disc in the grinder? I beleive they can even be used to cut stones, concrete, ceramic and steel if you don’t push too hard and proper cooling is in place…
If it’s as difficult to cut as steel but the weight of aluminium foam, that’s the good story.
>any material that can destroy a cutting disc that fast
You CAN destroy a cutting disc that fast when you’re doing it wrong. What they were doing is just shoving the disc into the metal, overheating it deliberately without even trying to cut it.
I don’t see a bike lock constructed of this material doing well versus a set of bolt cutters.
Yup, would be good to see a test on that. Though depending on where the plan to use it, that may not be practical.
I’ve seen cutaways of commercial safes made this way with zero fancy materials – just steel/metal balls embedded in a concrete or other sort of material inside the safe walls making it harder (but by no means impossible) to cut or drill with a single regular tool.
EG: Metal drill bits hate concrete, masonry drill bits hate metal. Metal grinding discs hate concrete, concrete discs hate metal… and sledgehammers hate the steel outer that’s keeping it all in.
I have doubts about how wonderful this material really is and I suspect the difficulties of working with it will outweigh the benefits in a lot of applications.
By the way the guy weilding the angle grinder applied so much pressure as to stall the motor says that it was more a demonstration of showing a wheel being intentionally chewed up more than the material resisting being grinded.