From the looks of the average driveway or sidewalk, it may seem as though concrete is just destined to crack. But if concrete is so prone to cracking, how are we able to use it in so many high-stress applications like bridges and skyscrapers? This question came about while I was researching 3D-printed thermite for an article. Thermite is often used in welding railroad tracks, and I linked a video of fresh tracks being welded that had concrete ties. I knew I had to find out how concrete could be made to withstand the pressure of freight trains.
On its own, concrete is brittle and has no give to it at all. But that doesn’t mean it isn’t strong. Although concrete has good compression strength, the tensile strength is quite poor. Around the late 1800s, someone thought to fortify spans of concrete with steel reinforcing bars, better known as rebar. Steel can stretch, adding steel bars gives the concrete some tensile strength to go along with its compressive strength. Rebar also allows for thinner slabs and other members.
Rebar Only Goes So Far
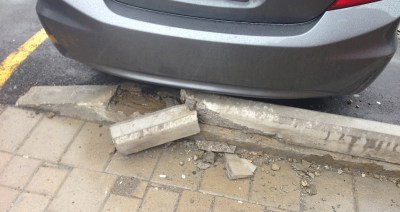
Rebar or mesh-enforced concrete is good for things like parking lot blocks and roads, but it still fails before it ought to. In fact, it usually has to crack before the rebar can chip in any of its tensile strength.
In high-stress concrete applications like bridges and skyscrapers, it’s terrifically important to avoid deflection — that’s when a concrete member flexes and bends under load. Deflection can cause the modern glass skins to pop off of skyscrapers, among other problems.
A solid, rigid bridge is much nicer to walk, drive, and bicycle on than a bridge that sways in the breeze. But how do you do make a rigid bridge? One solution is to apply stresses to the concrete before it ever bears the load of cars and trucks or a steady schedule of freight trains.
Pre-stressed concrete is like rebar-enforced concrete, but with the added power of tension baked in. By adding stress to the concrete before it goes into service, deflection will be reduced or perhaps eliminated altogether. With the addition of tensile strength, more of the concrete’s own strength is able to come into play.
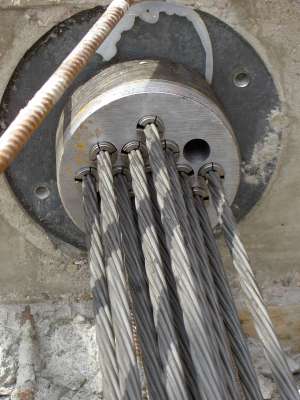
Tensioning Methods
Pre-stressed concrete is made by running tendons throughout a concrete member or adjacent to it, and then pulling the tendons taut from the anchorage points to add tension. These tendons are usually made of either high-tension steel, carbon fiber, or aramid fiber, which is used in anti-ballistic fabrics. They are arranged in either a monostrand or multi-strand configuration and act a bit like rubber bands.
The result of pre-stressing concrete is that future compressive forces will make the service member act like super concrete, and future tensile forces will make it act more like high-tension steel. In other words, pre-stressed concrete can stand up to pressure and even twisting much better than regular concrete. It is essentially programmable because it is pre-stressed in a calculated way that mimics the stresses it will bear once it’s in service.
The ‘pre’ in pre-stressing means that it happens before the concrete member goes into service. The tensioning itself can either be done before the concrete is poured, or after it has set. There are various reasons for using one method or the other, but they’re pretty equal in terms of results.
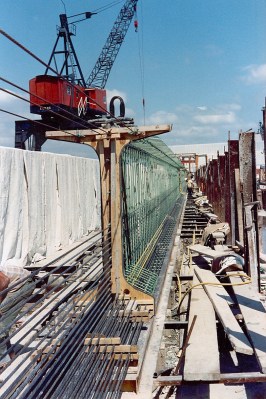
Pre-tensioning: Before the Pour
This is the oldest method of pre-stressing concrete, and it dates back to the late 1800s. Pre-tensioning is typically used in making beams, floor slabs, balconies, water tanks, and concrete pipes. Before the concrete is poured, the tendons are secured between end-anchorages whether the tendons will end up within the concrete or directly next to it.
As the concrete cures, it sticks to the tendons, and the tension from the tendons is transferred to the cured concrete. After they’re unbolted, the rods stay tensioned, held in place by the concrete. Pre-tensioning is often done in advance of a construction project and the completed pieces are shipped to the site. This way, multiples can be made at once in a large mold called a casting bed. These are set up with tendons that are several members long, and then cut down once the concrete has cured.
Post-tensioning
As you might imagine, post-tensioning is done after the concrete cures. In post-tensioning, the tendons are inside of sleeves made of plastic or galvanized steel, and the concrete is cast with the sleeves on. After the concrete is cast, the tendons are pulled taut by the anchorages just as they are in pre-tensioning.
There are two ways to do post-tensioning — bonded and un-bonded. In bonded post-tensioning, grout is applied to the tendon sheathing before tensioning, and this permanently attaches them to the concrete. This does three things: it protects against corrosion, it locks in the tendon before tensioning takes place, and it improves structural behaviors of the concrete once the member is out there doing its job. In un-bonded post-tensioning, the tendons are in a lithium grease-filled sheath and are thus allowed to move longitudinally within the concrete. These are usually prepared off-site and in advance.
Check out the the concrete experiment in the video below. The concrete members that were pre-tensioned and post-tensioned are both able to withstand twice as much force as the member with traditional rebar. It isn’t that tensioned concrete is magically stronger, just that it’s allowed to reach more of its strength potential. Be sure to stick around after the experiment for a dramatic look at the process of manufacturing concrete railroad ties.
Great Article! I feel like the diy / maker community sometimes skips over considering the availability and strength of concrete when designing things.
The DIY community doesn’t do large structures very much, at least not the hacker/3D printing/electronics sector.
When you’re building something under the several feet scale, you can afford to use wood, metal, and plastic, and they’ll be much lighter and impact resistant.
Things like Durham’s water putty(I use titebond 3 instead of water to make it less absorbant) are pretty useful in the DIY scene,if you can find a brand without any crystalline silica.
But most of the time these days, anything I build is thin wood that I scored on the Brother ScanNcut machine before cutting, or else 3D printed in PLA, because getting results of that quality with any other method would be very hard.
That’s why I want to make a concrete frame 3D printer. I got some used industrial linear rails and want to have some fun with experimenting.
“On its own, concrete is brittle and has no give to it at all.”
A slight correction… concrete is actually not that brittle, and it has quite a bit of “give” to it. It has a lower elastic modulus than steel (commonly 25-50MPa in construction vs 500MPa for the steel reinforcing it) which means it takes less stress to achieve a certain strain, and it will also take a larger strain than steel before it deforms plastically. It also has some interesting properties that steel doesn’t have such as creep.
The thing is, you never see concrete in the same dimensions as steel or other materials, but rather usually as large monoliths (because of the low tensile strength) that we don’t intuitively know how the properties compare. If you had a piece of plain concrete the same dimensions as a piece of rebar, you’ll see that it’s actually reasonably ductile. The reason it seems brittle is because of the large difference between maximum tensile and compressive stress.
Woops, as soon as I hit submit I realised I gave the figures for the strengths of concrete vs steel, rather than the elastic modulus. The correct numbers for elastic modulus are about 12Gpa for concrete and 200Gpa for steel.
Nice! Good add to the -IMO well-written- article 👍
Thanks ☺️
A fascinating graph: https://www.lehigh.edu/~intribos/Resources/chart1.jpg
“It also has some interesting properties that steel doesn’t have such as creep.” – actually steel suffers from creep as well… there are a whole industries fighting it (high temperature high pressure pipelines of power plants and rafineries etc.).
Nearly the entire (very complex) field of jet turbine blade fabrication is trying to minimize creep, albeit under the worst operating conditions we’ve yet come up with.
Look up the definition of brittle, it doesn’t mean what you think it does. Rubber is one of the most brittle materials because it suffers no plastic deformation, when it breaks you can put the broken pieces back together and see that there was no deformation. Brittle does not mean “no deformation” it means “no plastic deformation”.
What about peanut brittle?
B^)
I was surprised a few years ago when trying to CA glue a broken ceramic vase back together, that the shards did not fit completely together. In breaking the vase, internal tensions were released and the shards deformed.
Im not sure what about my comment made you think I don’t know what “brittle” means. But regardless of how you define it, concrete is not brittle, it deforms plastically before failure. Although unless you are doing plastic design, plastic deformation is still usually considered failure.
Do you have an example of that? I have never seen cured concrete deform plastically.
it doesn’t really deform plastically much at all. The steel inside of it resists the load plastically and as long as everything stays below the tensile failure point of the concrete everything returns to shape. This is evidenced in the fact that all un-reinforced concrete slabs will develop cracks from simply thermal expansion. When you talk about modulus of elasticity it is important not to look at that in isolation because failure mode is important too. If you exceed the yield strength of steel it will permanently deform but will often stay together in its new stretched state. Concrete tends to fail completely above its yield strength as its structure is torn apart.
(1) Concrete is brittle because of its failure mechanism, not the stress or strain at failure; (2) the elastic strain limit for normal strength concrete is much lower than steel in compression (600~1000 micro-epsilon in concrete vs 2000 for steel) and basically non-existent for tension, and (2a) the failure strain for tension in normal strength concretes is around 200 micro-epsilon; finally (3) stress is better understood as a resultant property of strain. In compression or mixed modes yes you get larger deformations that pure uniaxial but if you perform a bending test on a unreinforced beam or improperly reinforced beam the failure result is way way worse than a steel beam — it will be sudden due to unrestricted crack propagation. Addition of steel allows for enhanced ductility through a variety of mechanisms due to strain compatibility around crack locations at the reinforcement — this adds ductility to properly reinforced beams because you get a tension stiffening effect on a structural scale. But the concrete itself will still suffer brittle cracking where the strain reaches the failure limit.
What he said :)
Have to point out that having a low or high elastic modulus isn’t what makes a material brittle.
A material that’s “brittle” is one that takes little deformation before failing. Many steels can be bent and stretched substantially before actually failing completely. Concrete, not so much.
Also, steels do creep, though quite slowly, most the time. And, to the guy who said “rubber is brittle”…no, it isn’t. It doesn’t matter whether it’s elastic or plastic deformation, brittle materials show little of either before failure.
Rubber’s brittle if you soak it in liquid nitrogen first!
B^)
Not really, Take a 1/4″ steel rod and a 1/4″ concrete rod in hand and try to bend them or crumble them in your hand. Concrete is pretty brittle because it is so much weaker in tension compared to compressive strength. Any bending moment puts part of the concrete in tension and part in compression resulting in failure. Any crystal bonding broken in concrete during tension remain broken permanently where steel can flex and return to its previous shape as long as you stay below yield strength.
Another way of looking at why pre-stressed concrete is so durable is: under normal usage, a beam experiences both compressive and tensile forces. By heavily loading the concrete in compression, using the steel in tension, you convert all the tensile forces the concrete beam would see into merely reducing the amount of compression it’s experiencing, keeping it always loaded in compression. When I ran across that in a mechanical engineering course, it made the whole process seem a lot easier to understand.
I don’t have much to say about this beyond “yeah, what they said”, but you’re right and it’s an important insight. The idea of pre-loading bolted joints is very similar.
Fascinating, and here I thought pre-stressed concrete just meant you had to attack the concretes self-esteem before your poured it.
“You suck! You’ll never be strong enough for this bridge! Just wait, soon as the first car drives onto you, you’ll collapse!”
“Oh yeah?! Just watch me be strong! I’ll endure! I won’t fail!”
I was a rebar detailer for 10 years in the Washington DC area and I have never seen one pre tension bridge or building project they were always post tensioned. I also detailed rebar jobs from Florida to Arkansas to New Jersey along the east coast of USA and never had one prestressed job it must be out of favor in commercial building and bridges. Like waffle slabs.
Prestressed is still rather common, it’s more likely the prestress yard use their own detailers as they do the own bending, have steel forms, pull strands, design their own concrete mixes often and pour the concrete. Then cut the strands and strip the forms, deliver the finished beams to site, often on custom designed trucks for the really long bridge beams.
I’m no concrete expert and I might be completely wrong about this, but in the Houston area, we see almost all new bridges and overpasses built with prestressed concrete beams. The pre-stressing is obvious when you see them trucked to the building site. They are significantly arched upwards.
The big concrete beams that are delivered by truck or the tractor and the aft end with the guy in the little steering pod) are pre-stressed. Small ones for bridges made of short spans are made on-side with a row of dorms and cables that pass through all the forms in-line. The cables are cut after curing with a torch or wheel.
Maybe you did not see them because they would not need rebar work if they were using pre-stressed?
I had all of the structural drawings for the entire projects. Must be that the don’t mix the two. I did a few precast jobs in my time but the cables were always pulled after they were installed. Maybe that is actually pre stressed but it was never referred to as pre. But I have done enough jobs around the country that every region has a different name for the same processes.
Glad to see you reference Practical Engineering. It’s one of the best STEM youtube channels out there, alongside Ben Eater and Technology Connections
Excellent article!
Not the 10^6 one covering how to add LEDs to your underpants or whatever…
There are so many science/engineering topics apart from electronics that are worth writing about.
Hmm, underpants. You could go all Nigel Tufnel and add a speedometer.
Great article. I have warm memories of of my 1950-60s childhood marvelling how people talked a his a bit of “re-oh” made all the difference. Now I understand a bit about it.
Good lord that railway sleeper video is hard to watch. Quit it with the jumpy cuts and the lens flares already!
The article did say it was ‘dramatic’.
What?! It was awesome! Actually showed the interesting bits of the process.
A couple of other methods of reinforcing concrete are mixing in glass or steel fiber, or both. Getting towards 30 years ago the building across the street from me had new sidewalk and parking apron poured with glass fiber reinforced concrete. Despite some surface erosion there’s been no cracking.
Hmm. So – can post-tensioning be used to reduce de-lamination in 3d prints? More to the point – how would you go about doing it? Maybe zip ties … actually, that could totally work.
Or screws/bolts/rods. Besides just holding 2 or more pieces together, they can also add strength to a single piece. Of course, you’re mostly getting more strength by using a stronger material.
Stick a bolt in it is my go to for reinforcing things like those large threaded broom handle ends. Works a treat.
You could use a bit bit of rebar, and cut it down to size afterwards… wait, I’ve reinvented a CNC mill…
I’ve been reviewing again using for the Dobsonian style mount horizon/azimuth rail instead of a free trampoline circle pipe as a rail, maybe PVC pipe rail from watching a Nighthawkinlight video on the PVC roller coaster. Even received some great data from Paul Gregg regarding, since I was wondering about maybe adding rebar and/or concrete to make stiffer. Brittleness came up though might not be so much an issue with the 10ft satellite dish application. Differences in thermal coefficients of expansion can be considered also.
Well, as of late, the bending of the PVC circle had me thinking about making a form using a pipe driving into the ground and then attaching a radius 2×4 bar with a fork at the other end for the pipe to fit between. Then I started thinking, why not just make a rough circular trough form and then instead make the rail with concrete. Basically taking a 90 degree elbow at the end of the 2×4 instead of a fork and using as the cement form to make a circle track contour, that if I wanted to later set a rail into I can, and just use with not machined roller caster wheels.
Now wondering all the ways how I can stress a circle rail?
The simplest way to put this is that you must keep concrete always in compression. Any tension loads are taken up by the steel which takes the tension load that the concrete does not like. Rebar does the same sort of thing but causes its own issues in that the rebar is not easily serviceable after installation where tension cables could be replaced. The steel rebar becomes expansive when it corrodes and also does not expand and contract at the same rates as concrete in temperature cycles leading to stress and failures at the concrete steel interface. The same process is at work in high rise buildings with steel frames and concrete floors.
I worked as a designer/detailer at a precast plant back in the ’80s, and have fond (and out of date) memories…
The first project I worked on was a building for on a local college campus- we had nearly 90′ clear spans over some big lecture halls. It had 3 big rooms facing a central core where they did AV/presentation displays, a pretty cool setup for the time.
We had “double T” floor deck members around 90′ long to cover these rooms, we would cast 3 of them in a time in a 300′ long casting bed. There were something like a dozen 1/2″ high-tensile strength cables in each leg, each stretched to several tons of force, I don’t remember the exact numbers anymore. Anyway, after they cured and we cut the cables free from the abutments anchoring the cables at the ends, and all that force was released into the concrete, these members would “camber”, meaning they would arch-up in the middle, by something like 7-9″. Initially when they were cut they would often just sit there still in the form, and after a few seconds (sometimes minutes) they would break free of the of the form and pop up- 90′ of concrete suddenly jumping up by almost a foot in the middle and then bouncing up and down for a few seconds. It was unreal to witness this, just crazy. Of course at the time there were workers (affectionately referred to as “yard apes”) working on/around them, sometimes actually standing on them pulling off the insulated tarps they were covered with. They thought nothing of it.
Because of their size they had to be delivered to the job site before 6am with police escort. We’d have convoys of several trucks with police with their lights on at each end. On some members, some beams in particular, they had to drive slowly and watch for resonance- these 80-90′ long pieces of concrete would start vibrating and could damage themselves if it got out of hand. Vibrating is an odd term to use, because what comes to mind is a something like a tuning fork or a guitar string at a frequency you can hear- these would be more in the 0.5hz range, with an amplitude of inches…. amazing and a bit disconcerting to watch.
A very specialized product, but quite amazing in it capabilities.