Artfully-crafted wooden joints that fit together like puzzle pieces and need neither glue nor nails is fascinating stuff, but to call the process of designing and manufacturing them by hand “time-consuming” would be an understatement. To change that, a research team from the University of Tokyo presented Tsugite, a software system for interactively designing and fabricating complex wooden joints. It’s named after the Japanese word for joinery, and aims to make the design and manufacture of glue and fastener-free joints much easier than it otherwise would be.
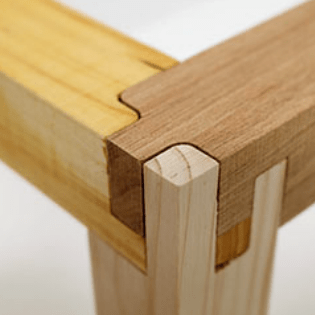
It looks like the software is so far only a research project and not something that can be downloaded The software is available on GitHub and the approach it takes is interesting. This downloadable PDF explains how the software deals with the problem of how to make such a task interactive and practical.
The clever bit is that the software not only provides design assistance for the joints themselves in a WYSIWYG (what you see is what you get) interface, but also generates real-time feedback based on using a three-axis CNC tool as the manufacturing method. This means that the system understands the constraints that come from the fabrication method, and incorporates that into design feedback.
The two main limitations of using a three-axis CNC are that the cutting tool can only approach the material from above, and that standard milling bits cannot create sharp inner corners; they will have a rounded fillet the same radius as the cutting bit. Design can be done manually, or by selecting joints from a pre-defined gallery. Once the design is complete, the system generates the toolpaths for manufacture.
Currently, Tsugite is limited to single joints meant for frame structures, but there’s no reason it couldn’t expand beyond that scope. A video to accompany the paper is embedded below, it’s short and concise and shows the software in action, so be sure to give it a look.
We love the idea, and it reminds of the Matchsticks project, which also used CNC specifically to ease the fabrication of joints.
[via SciTechDaily]
I am a little surprised that the CNC-machined version is so untidy compared to hand-cut similar things.
See, for example, Dorian Bracht’s YouTube channel.
https://www.youtube.com/watch?v=r-uAaNpAdgA
I just discovered this channel in the last couple of weeks. If anyone’s looking for some zen background noise, this is it. Every once in a while you glance over to see some beautiful work being done.
Square results, circular tools. Though I dont really get the “untidy” bit.
Maybe they mean loose tolerances? Which, if these weren’t just proof of concept, I might agree with.
nothing that can’t be fixed with copious amounts of glue, sawdust and clamps.
In reality, I completely agree, when I do stuff with wood by hand the tolerances are awful but the results are fine.
But in fine woodworking land, there seems to be an aversion to that kind of thing, it’s almost a sports-like quality of people wanting the end product to reflect skill without any cheating.
This is also why I don’t have any interest in that kind of furniture, it usually requires a lot of care to maintain, and is somewhat delicate, just like it takes a lot to make.
But it’s sure impressive to watch on YouTube!
If you can slip a cigarette paper into the joint…
B^)
Hmm… Now I wonder about a CNC razor / chisel to make perfect corners where necessary. I’m aware of a sort of articulated arm for the cutter to finish inside corners and underhangs, but either have their merits, I think.
CNC is capable of making sharp corners with rotating tools: https://youtu.be/PtD9w6lp8n8?t=126
Hey! It was not necessary to hand cut with chisels afterwards, or to use a special milling bit that can cut sharp inner corners. Instead, outer corners are rounded to exactly fit the rounded inner corners.
Check this 15 min presentation video: https://www.youtube.com/watch?v=q00_XpfHYuA
Detailed explanation about corner rounding starts at 9min30s into the video.
And the tolerances are very precise…the pieces fit together better than a hand cut joint, I would argue… :)
I wasn’t saying that CNC wouldn’t be expected to be as precise as hand-cut, quite the reverse (I do a lot of CNC stuff). My comment was just that the photo in this article appeared to show an example where the accuracy benefits of CNC had not been fully exploited.
And I rather imagine that the point of this exercise was to make some really cool code, not to make some really cool wood things?
The accuracy benefits of the CNC are fully exploited. Again.. check out this 15 min presentation video: https://www.youtube.com/watch?v=q00_XpfHYuA
Towards the end of the video we show results, assembling individual joint samples. That will give you a feel for the accuracy.
(The video in the article is just a 30s preview video).
There are also tolerance controls, so you can choose how hard/loose you want the joint to be. If I set the tolerance to 0.00 – I usually cannot even assemble the joint, even with a hammer. The ones in the video above are fabricated with a tolerance of 0.15mm. tolerances are defined here as how much it over cuts the joint. That being said, if you are very picky on the friction feel, there is no other way than trial and error. Mill a joint, feel it, adjust the tolerances, mill it again. Because there are factors that cannot be generalized across multiple fabrication setups, such as the wear and type of milling bit, which does have a small but noticable effect on the tolerances.
I’m happy to hear that you think that my code is really cool in itself :) But I do like to make cool wood stuff equally much.
http://ma-la.com/tsugite.html had the link to the software
Thanks for that! There’s even a GitHub repository, thanks for the tip!
Thanks for updating the article! (Btw the “had” above is a phone keyboard typo).
OMG. Go through her long video there! This software is significantly more amazing than I first thought.
It evaluates constraints, which then lets it enumerate all possible valid joints. So as the user is making something that won’t be millable, it points out the nearest-neighbors that _are_ millable.
I love wooden buildings built without nails or glue, and it is quite a long established art in Japan from what I understand. I would like to see this program applied to making prefab buildings that just slot together like lego, I’d buy one.
For those complaining that the results look less than stellar, here’s a couple of links to Mirock who does some truly beautiful joinery with CNC. https://www.youtube.com/watch?v=mSxCIMVJXOA or this one https://www.youtube.com/watch?v=XBSbHhXXn_E
One of the LinuxCNC developers is a professional wood carver and uses LinuxCNC for ornamental turning. His work is stunning. http://www.deweygarrett.com
I’m struggling with getting the Tsugite s/w functional. The app populates BRIEFLY and then closes in ~5 seconds. Is it possibly a matter of dependencies Thoughts on troubleshooting?
Hi! There is a new version that can be downloaded form the project website: http://www.ma-la.com/tsugite.html Does it work better?
Am I the only one who finds this program to be so slow as to be unusable, even with a Core i7, 18GB ram, and launched from SSD? It takes several minutes to update after ever single change…