While we’re big believers in 3D printing here at Hackaday, there’s no denying that some things just aren’t meant to be printed. For example, most of us would agree that it’s not the first choice for making rims for a passenger car. We imagine that [Jón Schone] from Proper Printing probably feels the same way, but that didn’t stop him from trying to do it anyway.
A couple of months ago [Jón] got a test subject in the form of an older Mercedes with 19-inch rims. The first two challenges are bed size and warping, so he modified a Creality CR10 S5 with a heated chamber capable of reaching 70 °C to reduce warping with the ABS filament he intended to use. Another challenge is the amount of filament required for the print, especially since [Jón] wasn’t keen on babysitting the machine to replace the spool every so often. His attempt at building a filament joiner ultimately didn’t work out, so in the end he simply sourced the filament in bulk size rolls.
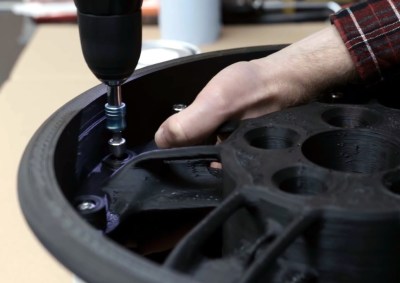
Eventually [Jón] managed to print a complete rim in two halves, bolted together around its circumference. Unfortunately, even with the heated chamber, the parts still warped all around the edges. This left a gap at the seam, but to fit a tubeless tire, the rim had to be airtight. So the entire inside surface was painted to close any small gaps, and the larger gaps were filled with sealant.
In the end it was still unable to hold pressure with a tire mounted, so it was test fitted to the car just to see if it would carry the weight. This test also failed, splitting on the thinnest part of the rim. [Jón] has headed back to the drawing board to try again in 2021. We probably would have moved on by now, but you have to admire his tenacity. We hope to see success in the new year.
Printing large parts brings its own set of challenges, but if you stick to good old PLA it’s not too difficult. [Ivan Miranda] has made a name for himself with massive 3D printed projects like a ride-able tank, and also built a supersized 3D printer for future projects.
It’s not healthy to encourage these quixotic ventures. He hasn’t documented the impact on his family life or those close to him. God be with him
Are you seriously posting on Hackaday to tell us nobody should be pushing the realm of what’s possible? I feel like you might have missed something important about the community here.
Dude may as well be making it with Lego. If it’s not possible with structurally superior methods of working with the material in question, it’s not possible working with structurally inferior methods of working with the material in question.
This guy has a death wish.
Also, there’s no way those dinky $2 safety glasses will protect his vision when a huge piece of his rim rips through the air and nails him.
I too have the same type of glasses in my lab (though I only dab with light dremeling and some tin soldering (with air filters)). Which glasses would you recommend ?
When dealing with the kind of energy a car tire can impart when going to pieces, a heavy steel cage is usually recommended.
Those glasses are fine for shrapnel protection up to and including machining. Any wrap-around polycarbonate glasses are essentially identical and will give a great deal of protection.
Modern safety glasses are made from polycarbonate, which does not shatter very easily and will bend instead. It’s sort of like a transparent version of aluminum. (As opposed to other plastics like acrylic that shatter glass-like.)
There are specific glasses you can get for specific purposes: laser protective glasses have a tint that’s specific to the laser wavelength you’re using, chemistry goggles (for liquid) are airtight with louvres for ventilation to prevent steaming up from sweat, full facemask with auto-dim window for welding, full facemask clear high-temp plastic for casting (in case of steam explosion), and probably a few more I’m not familiar with.
But for general all-around shrapnel purposes, any of the polycarbonate wrap-around glasses are fine.
Project Farm did some safety glasses testing, the guys testing procedures aren’t beautiful sometimes but they appear fairly effective.
https://youtu.be/0EwraSl1aPI
If you want more protection, try a fencing mask over the glasses. The mesh will protect against large blunt impacts – 1600N is a typical rating for a HEMA sparing mask (go for HEMA ones rather than sport fencing ones); that will take a steel rod lunged at you with the full force of a human behind it.
I think he failed before he started the delamination right of the printer would have been a good Indication something was wrong.
Possibly redo the design with the bolts to hold the whole thing together might help
It really is time to change: “you wouldn’t steal a car” to “you wouldn’t download a car”
You’ve been able to do that for at least 20 years, the free option is plans for the “Locost” Lotus 7 type cars, the paid option is the plans from RQ Riley of commuter cars and campers.
Without an FEA analysis, there is no way to know if the wall thicknesses are sufficient to handle the expected loads, both from the air pressure and the driving/car loads. You can’t just copy a steel rim in abs and expect it to work. Having said that, there’s no reason this couldn’t work if redesigned correctly to the right tolerances. Maybe some post processing is needed after the print to smooth out the sealing surfaces.
It has not been possible to make an injection moulded car rim, that a manufacturer would be comfortable selling, with conventional injection molding plastics and techniques. FDM 3D prints have proven under optimum conditions to be 80% strong as injection molded parts. Therefore the absolute best you can do is 80% of not good enough. New injection molding plastics have been introduced a few years ago with an eye to making injection molded rims a reality, but we’re not seeing them take the market by storm yet.
Largely because when plastics don’t creep, they become brittle. There’s a very narrow temperature window where a plastic rim would work anyhow, and you’d have to jack up your car on stands when you’re not driving it. It’s the same reason why airless tires have never worked.
Yes, for the requirements of steady temperature, limited UV exposure and benefits of corrosion resistance, this could be the ideal rim to use for vehicles in salt mines… and pretty much nowhere else.
As long as the stresses were low enough, it wouldn’t be a problem = if the surfaces were thick enough to lower stress.
ABS exhibits some amount of creep even at 5 MPa, but it gets progressively worse with temperature. The maximum working temperature is around 60 C, so braking hard once would destroy your rim by the heat of the brake disc.
That’s a great tidbit about airless tires and made me remember a video from Engineering Explained that may help understand the issue.
https://youtu.be/PT2odY3C6Og?t=150
Those pliable spokes in an airless tire to work well across the entire range of temperatures from the cold of places like Finland in winter to the summer heat of a place like Saudi Arabia seems like a very challenging task if it’s even possible. And if it is, it seems like the part of a tires performance based on its springiness will be drastically impacted as the plasticity of the materials used go through that temperature range. It seems like it would act a bit like increasing a suspension’s spring rate in the cold and reducing it in the summer (with a number of other side effects).
Agreed. This is a great example of proper design vs try it and test. Or put another way: engineering vs tinkering.
“This doesn’t feel safe.”
Boy, oh boy. It’s hard to imagine a worse idea. Remember tire cages, which were cages built from tubular steel in which to put a tire mounted on a split rim, to keep from killing the technician, because it was so easy to screw up the mounting process and then have the tire explode on initial inflation? Yeah, that’s what he doesn’t have here. Consider how much potential energy there is in an inflated car tire, Now imagine the wheel splitting at a layer line. The only reason this didn’t result in personal injury is that the pressure it was inflated to was clearly not enough to be useful.
But he’s wearing safety goggles! /s
The goggles do nothing!
Yep, saw a split ring come apart once. Sounded like a bomb went off and bent a steel tire cage.
LoL!!! Thank God he’s not working with acid!
I’m pretty sure 3D-printed rims can work somewhat well, but why would you design it like this? This rim has obvious weak points that you can immediately see without even doing any kind of analysis. This just looks like a regular rim designed to be cast in aluminum, but 3D-printed. That’s obviously not going to work for even a second when it’s holding up a 1500kg car.
I mean, it’s a funny video, but we learned nothing from this attempt that we didn’t already know ahead of time.
Plastic is, uh plastic.. if it was a success his lug nuts will come loose and bring him instant regret
Maybe if the rim was printed as a solid cylinder, with a heat treating step in the oven so that the layers fuse together, and some acetone smoothing, if everything stays in spec enough for a tire to be placed it may hold the car weight for a while but driving would probably destroy the mounting holes.
Getting a solid block of ABS and machining it would be faster, cheaper and a lot stronger, especially if it’s reinforced with carbon or glass fiber.
The problem is that 3D printed layers are strong when pressing down on the layers, but weak from any other side. Since the wheel must turn, there’s no single side that the layers are strong. Maybe if you could print concentrically it would be stronger.
3d printed wheel
https://newatlas.com/hre-3d-printed-titanium-wheel/57374/
you’re missing the point. This wheel is the result of a journey taken to see if it’s even possible to create the tools to create a wheel this size that *might* work.
The next step of the journey is designing and printing a wheel that probably will work.
This is more a milestone along the journey than the end result.
Go, watch all his videos, the guy is an inspiration and this is a fantastic resource in iterative design and learning as you go.
I think it’s all arm chair engineering and nay saying. His first step was to build a friggin giant water cooled printer. His content and engineering is pretty amazing, even if the wheel never works.
I’m a little surprised people are taking this so seriously. From what I’ve seen, this guy isn’t suggesting everyone goes out and 3d prints a rim because it’s just that easy TM. He’s spent nine months making this thing from designing it, customising his printer to have a large enough volume, trying (and failing) to splice spools together, and ordering in extra long lengths of filament. It seems like this is an excuse to do some yak shaving and maybe test the limits of current 3d printing along the way.
Think ahead a few steps:
1. Show 3D printing a plastic rim.
2. People copy-cat and put these on their cars… without doing a thorough and correct design analysis, stress testing, failure analysis, etc. Maybe because they haven’t thought about it, don’t know they should, don’t know how, ‘don’t have time’, it’s not fun, their buddy made it for them and they trust their buddy, etc.
3. Rims split when inflating the tires. Projectile hazard. 30 PSI × a few hundred square inches of sidewall = thousands of pounds of force.
4. Rims come apart when people are working on their cars. Feet, hands, torsos, etc. crush hazard. Rim projectile hazard.
5. Rims come apart on the freeway. Drivers lose control, heavy spinning tires are projectiles, rim fragments are shrapnel.
Do a risk analysis:
– What could go wrong?
– What would the consequences be?
– What can I do to prevent it or reduce the frequency and severity?
– Assume you are at a future time, and someone was injured or killed. How did it happen, how can you prevent it, reduce the probability, reduce the severity? E.g. for those wanting to put guns on drones, start with “oh ****, I shot a kid” and work backwards from there.
Don’t get me wrong, I’m all for making big printers etc. — for projects that are not safety-critical structural components.
“I can” is not the same as having good judgement about whether or not TO do something.
Obviously an SLS process would work. I also suspect that some of those fancy filaments with the continuous carbon fiber or aramid strand would work (although the design needs to support a continuous extrusion because you can’t cut off those single strand filaments in a start/stop fashion). Not sure what the advantage would be over more conventional methods however. I think the next revolution in home 3D printing will be affordable SLS that allow you to make real structural parts.
Have you considered fully all the aspects that “would work” needs to mean? Forming a piece is only one piece of the puzzle. Having it be suitable for the intended purpose is another.
For example, someone prints a set of these, puts them on their car, they don’t immediately fail, “yay, it works!”
Then they park it in sunlight in Texas in summer for a while (heat, UV damage), take it on the freeway, and hit a bump while passing a semi at 100+ MPH. A front rim fails.
Can you understand why some of us might be concerned?
This is so dangerous it really shouldn’t be promoted. Tyres are generally inflated in cages, some rim types such as split rims can fly apart from the pressure and have been known to be fatal. It’s blindingly obvious a printed one is likely to let go at a layer level. Rims are specified to standards, surely this guy is aware of that?
And not only is he himself at risk, at 7:51 and thereabouts in the video the rim face points directly toward the cameraperson, endangering them too.
I can only hope he does not take it out for testing onto public roads.
Tyres are generally inflated in cages? Or surely by the roadside, if you’ve had a flat?
Tires on split rims (e.g., on big tractors) are. A rim held together with bolts isn’t quite as dangerous – the problem with split rims is that it is possible to put them together wrong and have them explode as they are inflated.
Absolutely. Taking an untested, non-design-reviewed, safety-critical part on the road needs to be illegal (and probably already is, but how could a cop spot this?).
When it’s been in the sun (UV) for a few seasons, there’s a heat wave, brakes have been used (extra heat) and it lets go while passing on a curve (as if it would last that long, but still)… I suspect the appropriate terms include “negligent homicide”, “manslaughter” and “Darwin award”.
After narrowly avoiding a collision in my teens because I had saved money on tires, and much later because (overloaded) pickup brakes faded, I came to some conclusions:
1. There’s cheap, and there’s inexpensive. Cheap parts don’t cost much. Inexpensive parts help avoid wrecking your car.
2. I cannot afford tires with less than an “A” traction rating.
3. I cannot afford anything less than good ceramic brake pads and appropriate (non-slotted, slotted are for rebuild-after-every-race racecars) rotors.
4. I cannot afford steering that doesn’t work.
5. Engine is relatively optional. If it fails, I can pull over and stop.
Now adding:
6. I cannot afford rims that can fail.
Are we all just going to ignore the elephant in the room here? or rather the middle of the wheel. Even if he suceeds in pressurising the wheel it’s about to get mounted around a brake. A part famous for getting so hot race cars have theirs made of ceramics to stop them melting. One way or another this project is doomed to failure, let’s hope he survives long enough to come to that conclusion too.
While I salute the enthusiasm here, have to agree with the masses, metal wheels are the way to go. A blow out on a motorway convinced me that 4 functional wheels are quite useful, essential even.
The printed wheel could get exciting if it bust. Though 3D printed pressure parts can be OK for short term use. Much fun has been had with water rockets at way higher pressures than car tyres (comp runs out of puff at 10 bar). Admittedly more avoiding getting wet than shredded.
Since PLA doesn’t like to be warm, and compressors output quite hot air – I can attest for satisfying whoosh noise as parts fail.
I would have printed a pattern to create a ceramic cast and then fill it with molten steel. If nothing else, it would take a lot less time to print.
I feel like most of the people commenting on inflation pressure and the potential energy thereof didn’t watch the video. He can’t get the bead to seat, and in my opinion it’s because he was never going to get this to hold air. I’ve tried to make small FDM prints airtight, and it’s quite difficult in my opinion. This big rim was always going to be a bear to make airtight. So the bead doesn’t seat, so the thing isn’t even inflated. Yeah, he tried, but it didn’t seat.
OK, however I would look ahead and assume that he figures it out. Maybe he uses an inner tube (which was the commercial mass-produced solution to this problem, is still available and used for bicycles and trucks) or fix-a-flat goop or something. What happens after that?
If what happens can include losing a front rim while passing on the freeway or when you hit a bump on a curve, this needs to be illegal. Otherwise it’s not fair to the passengers in the car, the occupants of the other vehicles who can be involved in the wreck, pedestrians, and so on.
There are very real hazards here:
“In 2019, an estimated 38,800 people lost their lives to car crashes – a 2% decline from 2018 (39,404 deaths) and a 4% decline from 2017 (40,231 deaths). About 4.4 million people were injured seriously enough to require medical attention in crashes last year – also a 2% decrease over 2018 figures.” — https://www.nsc.org/road-safety/safety-topics/fatality-estimates
Assuming a design can even be produced which holds up under pressure, there is 0 chance the wheel will stand up to the heat of any real world braking. Especially if the 3d printed wheel is mounted up front where most of the braking force is applied.
I’d say one hard stop from ~60 kph and they’re melting…. and only able to test that if they don’t hit a small pothole at modest speed first.
These would be pretty sweet to use on a Rimbarrow or an 18-rimmer. I’d love a 3d printed steering rim too
In all fairness 3d printing your own hubcaps is perfectly safe and much more feasible. I admire his try but even if it didn’t work out it’s inspiration for what you can do.
I would suggest the use of a carbon fiber based filiment, it yeids on the average *60 percent more strength, and is less reactive too heat. Very nice work just a open-ended thought.