The use of aluminium in wiring is unlikely to bring a smile to the face of anyone who has had to deal with it in a 1960s, or early 1970s-era house. The causes behind the fires and other accidents were myriad, including failure to deal with the higher thermal expansion of aluminium, the electrically insulating nature of aluminium oxide, and the general brittleness of aluminium when twisted.
Yet while copper is superior to aluminium in terms of electrical conductivity and ease of installation, copper prices have skyrocketed since the 1970s, and are on the verge of taking off to the moon. A big part of the reason is the increased use of copper in everything from electronics and electrical motors to generators, driven by large-scale deployment of wind turbines and electrical vehicles.
As the world moves to massively expand the use of electrical cars and installation of wind turbines, copper demand is predicted to outstrip current copper supply. With aluminium likely to make a big return as a result, it’s worth taking a look at modern-day aluminium-based wiring, including copper-clad aluminium and the use of carbon-based replacements.
How to Make Copper Expensive
In hindsight, copper prices weren’t that bad yet in the 1960s and 1970s, as we can see in the following graph of copper prices of the past 45 years:
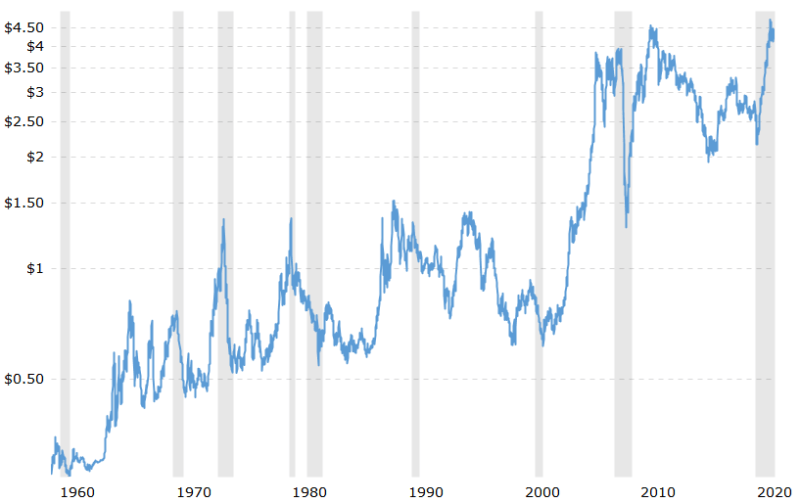
These price increases are driven largely by an increasing demand for more electrical vehicles and wind turbines, which over the coming years look to accelerate, putting further pressure on the existing supplies. Although the USGS has identified likely undiscovered copper resources, this does require for a mining operation to be established, and not all copper ore can be economically mined and turned into raw copper.
Earlier this year the International Energy Agency (IEA) released a report on the role of critical minerals in the energy transition to low-carbon sources. Taken from this report, in the below images we can see the relative metal requirements per type of source, per rated output capacity, as well as the material requirements for electrical vehicles (EVs) compared to conventional (ICE) cars:
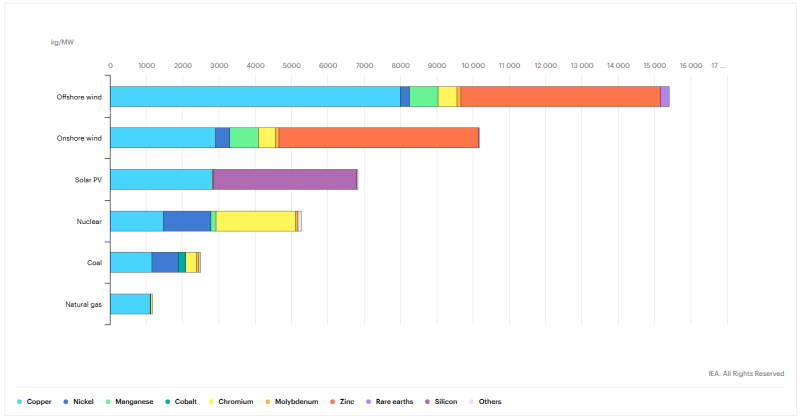
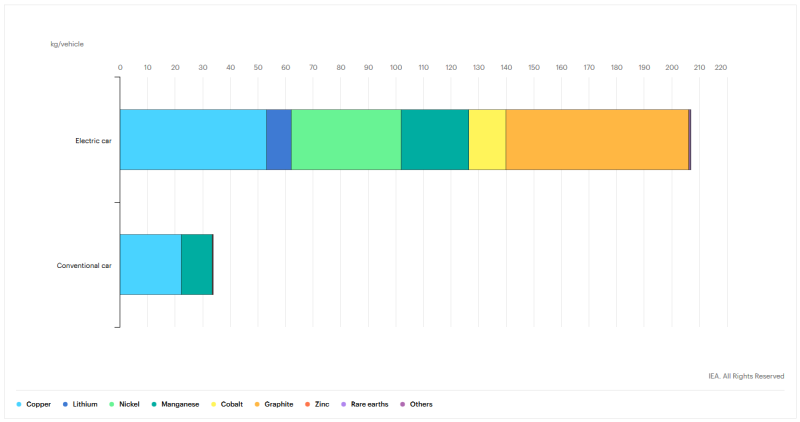
Meanwhile, the expected demand curve for copper in light of current sustainable development policies at the same time is expected to look something like the below image, contrasted against current copper mines output and expected new mining operations.
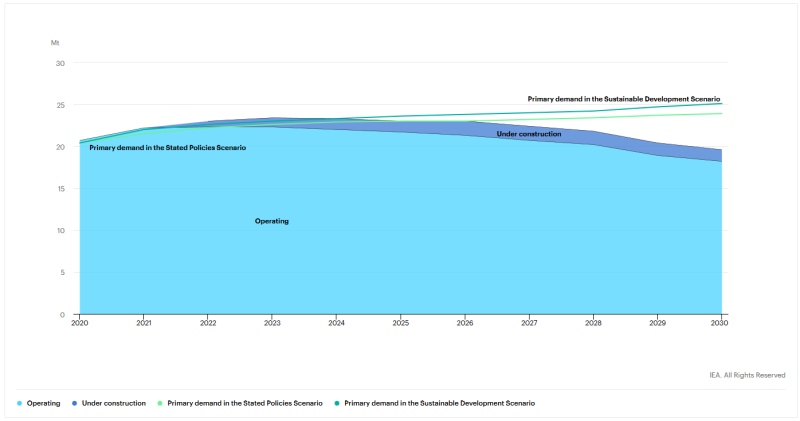
Not unsurprisingly, since many of such policies have come into effect around 2000 and alongside increasing demand from other industries, copper prices have been steadily rising, far beyond the highs of the 1960s that made prospective home owners decide between installing copper or aluminium wiring.
At this rate, we might see the end of common use and easy availability of copper in a matter of years. At the same time, as copper’s properties make it ideal for certain applications, other uses that may be fine with alternatives may have to look elsewhere. Very likely this would mean that everything from house wiring to customer electronics may soon find itself priced out of the copper market. What alternatives are there, and how do they compare to copper?
Trying to Top the Best
Copper is a favorite for electrical wiring for a number of reasons, not the least of which are its excellent thermal and electrical conductivity. This is why copper is a preferred material for heatsinks, and for electrical wiring in both houses and in electrical devices. In comparison, pure aluminium has only 61% of the electrical conductivity of copper by cross-section.
Yet aluminium has one major benefit over copper, and that is that it is twice as electrically conductive by mass, owing to copper’s density at room temperature of 8.96 g/cm3, versus 2.70 g/cm3 for aluminium. For this reason applications where weight is more of a concern such as transmission and distribution wiring. Especially when running large bundles of cables between pylons, the higher conductance to weight ratio of aluminium offers major benefits.
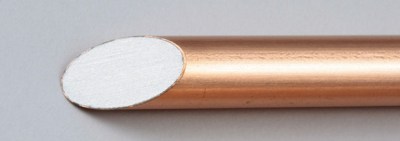
When properly installed and used, aluminium is a fine choice as electrical conductor, but that doesn’t mean that it is the only option. Something that’s commonly seen in wiring since the 1970s is copper-clad aluminium (CCA) wire. This is basically what the name says: an aluminium core that is clad in copper, making it a bimetal. The main goal of CCA is to combine the benefits of both copper and aluminium in a single wire, meaning closer to copper-like conductivity, while avoiding the pitfalls of aluminium as the installation method is the same as for copper wire.
If we take a look at the specifications which Fujikura lists for CCA (also called CAW), we can see that while CCA isn’t as good as solid copper wire, it is significantly better than solid aluminium wire. If we add to this the major benefits that a copper skin adds in terms of near-elimination of thermal creep and compatibility with copper-compatible termination methods and technologies, it would seem to form a good alternative to both.
Interestingly, CCA has been competing with both copper and aluminium wiring for a while now, particularly for building wire, as noted in this excellent write-up by the IAEI Magazine on the history of aluminium building wiring. An important detail that this article adds is that the creation of CCA is fairly labor-intensive, meaning that its popularity has always been dependent on the current copper prices.
The IAEI notes that until late 2005, copper prices were still fairly low (as noted in the earlier historical copper prices graph) , but have since risen to the point where CCA is now highly competitive with copper.
A Dash of Carbon
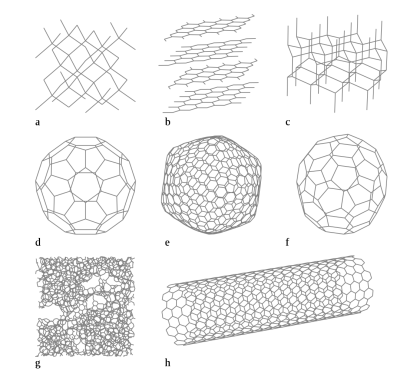
CCA is not the pinnacle of materials science when it comes to electrical conductors. Carbon-based structures, such as carbon nanotubes (CNTs) have much higher electrical conductivity than copper, as does graphene. The main issue is that making wires out of them is not exactly straightforward. Yet what if they could be merged with a metal like aluminium, or even spun into wires?
An article by Lekawa-Raus et al. published in 2014 titled Electrical Properties of Carbon Nanotube Based Fibers and Their Future Use in Electrical Wiring examines the research literature at that point in time on the production of CNT fibers, which can be spun into CNT wires. Based on the research, these wires would have superior electrical conductivity and weight, outperforming both copper and aluminium handily on all counts.
Connecting these CNT wires could be handled with a carbon solder, which at the time was under development at Cambridge. Even so, many challenges in producing flawless CNTs with the appropriate morphology remained, especially when moved from a laboratory to an industrial setting. Many of these concerns remain in 2020, when Cesano et al. performed another review study. They note that although progress has been made in the intervening years, full-carbon wires are still a future prospect.
Even so, CNT fibers can be commercially purchased for not entirely insane amounts of money, as well as CNT composites with copper and other metals like silver and gold. Recent studies by Zhang et al. (2018), Pradhan et al. (2020) and Chyada et al. (2017) show improvements in thermal conductivity and electrical conductivity as well as tensile strength respectively for graphene-aluminium composites.
The addition of CNTs has also found use in other applications, such as the mechanical reinforcement of aluminium parts, with Nyanor et al. (2020), detailing an aluminium matrix reinforced with CNTs as well as micron-sized titanium-carbide (TiC) particles. This creates a material that has 2.3 times the hardness of pure aluminium, with significantly improved wear resistance.
The Yazaki company of Japan has filed numerous patents on Al-CNT composite materials that are intended to be used in upcoming wire products. Tirupati Graphite Plc meanwhile has made claims about an Al-graphene composite that claims to have copper-like electrical conductivity, better thermal conductivity than copper and better micro-hardness than copper.
Electrifying Changes
With sky-high copper prices a potential prospect over the coming years, it would seem pertinent to take a good hard look at the available alternatives. Whether CCA is an acceptable alternative to copper depends on a lot of factors, but with real-world usage data available for the past five decades for house wiring and other applications, it is at least a known quantity.
Perhaps more exciting is the prospect of graphene and CNT-based wiring, which offers more than just a trade-off compared to copper. Instead these may result in an alternative to copper that is actually better in all respects, with better conductivity, higher tensile strength, higher resistance to corrosion and higher conductivity for both a given cross-section and weight.
From a hobbyist perspective, CCA is probably the most likely alternative one will end up with, based on a cost perspective and ease of handling. As it behaves and can be processed similarly to copper wire including soldering using standard solder alloys, it can replace copper wire with just a small bump in diameter to compensate for the worse electrical conductance.
It would be rather cool if future generations are wiring up their projects with CNT wires and carbon-based solders, however. Here’s to more carbon in our future.
If the y axis on that historical chart were scaled properly it would indeed be a very scary scenario on the price.
Maybe. Is it adjusted for general inflation?
https://www.longtermtrends.net/copper-gold-ratio/
Was any of this inflation adjusted? Should it be?
The chart shown in the HaD article is not inflation adjusted. How much adjustment to apply for inflation is a bit of a controversial matter anyways, so I thought it would be interesting to compare metal to metal with the previously linked chart. There is no need to inflation adjust commodity ratios as currency is removed, this is simply how much of item A you can get in exchange for item B on day X. Here is an article comparing to silver, a more industrious metal. https://seekingalpha.com/article/4181917-copper-silver-ratio-range-for-thousands-of-years
That was exactly the right question. Thank you!
Copper rose above $1/pound in January of 1974. Now it’s $4.68.
A US dollar in 1974 is currently worth $5.38. Copper has not kept pace with inflation over at least that 47 year term. Calculate your own sliding window return rates… I’m too lazy this early in the afternoon. Prices spiked for a while in ’74 and they’re spiking again, so this is probably not a completely unfair comparison. I’m also very well aware that the Consumer Price Index has under-reported inflation since the mid nineties. Point is, inflation adjusted, we’re seeing copper at very roughly normal levels.
There’s an interesting concept in natural resources (trees, oil, ores, etc.) and that is “proven reserves”. The proven reserve is the amount known to exist in the wild at a given price point. When the price of oil goes up, the proven reserves go up. When it goes down, some of it is no longer economically feasible to drill for, so the proven reserve goes down. All minerals behave that way. I have gold at my farm, but at $1700/ounce it’s just not worth screwing with – I make way more money writing software.
There is plenty of copper in the Southern Appalachians that isn’t currently worth mining. A good bit is in WWII-era mines in Copperhill TN. Just thought I’d point that out.
And experience tells us that as prices increase, demand decreases. Hoarding pennies is likely to be a losing proposition.
I’m also a little hesitant to blame “renewable energy” for the increase. It’s not like we’re building fewer aeroderivative turbine peaker plants and large gas plant construction continues apace as well. Personally I blame demand – data centers, domestic air conditioning, and all the other luxuries of modern life we seem bent on accumulating. And to forestall this one, total electric car deliveries are still trivial. I saw a Tesla two weeks ago and it was notable, even in a college town.
“Hoarding pennies is likely to be a losing proposition.”
Bummer!
B^)
Especially pennies made since 1982, which are zinc with a bit of copper on the surface.
Pennies are CCZ … ugh!
Copper-clad zinc pennies don’t even make a cheap heatsink. So hoard the 1982 and older pennies but forget about the ones made in 1983 or later.
If you think you found a copper penny from 1983, might be worth checking the weight to see if the weight is 3.11 grams and not the 2.5g of the copper-plated zinc cents. Those 1983 copper pennies will be worth more.
Otherwise, my thought regarding the matter is like most commodities or whatever property investment scheme… there is always some sort of “plandemic” to drive the economics of the financial instrument property value.
Seems with more and more market based derivatives vs the traditional tangible assets, so more and more market volatility like if I recall correct just prior to or after JFK’s admins influence seemed.
Anyways, that’s my two cents.
I think electric vehicles vary a lot by region.
Of the 12 cars in the parking lot in front of work, 4 are electric; on my drive into work, where I probably pass by 400 cars, about 15 are teslas. (I wouldn’t recognize an electric audi, for instance, but would recognize a Leaf.) I’m in an area with a lot of tech employment, and a lot of electric vehicle infrastructure; I can see two separate electric charging stations, one with multiple outlets, from my office window. In this town there are definitely more electric chargers than gas pumps, and that’s just big commercial ones, not counting people who have chargers at home.
There is also lots of native (i.e. already in pure copper form) copper in upper Michigan. In fact, its purity makes it a bit more challenging to mine ( it bends rather than breaking into easy chunks), which is why the mining companies moved to other places where it could be harvested easier even though it required refining. Imagine removing a car sized single piece of nearly pure copper and you have the correct picture. Once the price gets high enough, the copper is just waiting for someone to come get it.
Inflation adjustment which that graph obviously doesn’t implement: $1 in 1960 = $9.24 in 2021, so divide the 2021 figure by 9.24. Not such a catastrophe then, is it…
https://www.usinflationcalculator.com/
More like an excuse to get cheap with wiring…
“Although the USGS has identified likely undiscovered copper resources, this does require for a mining operation to be established, and not all copper ore can be economically mined and turned into raw copper.”
Depending on location, I’d say it is virtually impossible to open a new mine in the U.S. with so many NIMBYs and tree huggers around.
Processing seawater.
https://web.stanford.edu/group/Urchin/mineral.html
Again, there’s 20 times more aluminum than copper in seawater.
And…
“There’s gold in them thar waves!”
B^)
Oddly enough, if you took an amount of seawater equivalent in volume to a haystack (around 2000 cubic feet) and extracted the gold from it, you’d have enough to fashion into a small-sized sewing needle and you’d have literally found “the needle in the haystack.”
Gold is 0.000008 ppm in seawater. Your sewing needle would weight 0.00045grams.
But [Prowler50mil],
there’s LOTS of seawater.
We’ll make up for it in volume!
B^)
Prowler50mil
I think you lost a decimal or two somewhere.
2000 feet^3 = 56 634 000cc
0.000 008ppm = 0.000 000 000 008parts/part
556 634 000 * 0.000 000 000 008 = 0.004453072cc
Gold’s mass is 19.3 g/cc
0.004453072cc * 19.3g/cc = 0.0859g
Some of the smallest sewing needles are around 0.06cm diameter and 3.7cm long.
0.03^2 * 3.14 * = 0.0028cm^2
0.0028cm^2 * 0.37cm = 0.0104cc
Thus a volume of 0.01cc. So this gold needle would be about half the size of one of the smallest sewing needles and about the same mass.
Time to push for mining in space? Is there much copper up there?
Copper should be reasonably common through our solar system, but perhaps not enough to really make the expense of mining and shipping back from space worth it right now, though other rarer metallic compounds hard to find or make on Earth are also likely to be quite common indeed up there.
So mining space in general might fly even with near current space/rocket/robotic techs, at least economically, environmentally is a bit of a different story – you can shoot processed minerals to Earth from further out in the solar system with very little energy required, but if you want to actually get them through our atmosphere intact you need something like a space shuttle – a reusable re-entry platform that can intercept those inbound minerals and and then land carrying that significant mass – at the moment such a thing doesn’t exist. And the SpaceX stuff that seems to be closest to doing the job I would suggest (though can’t say categorically) would be vastly inferior trying to land with high mass on board than the now retired and rather primitive (but very impressive) space shuttle – aerodynamic lift and a runway vs having to carry and burn more fuel, and more fuel for the fuel you carry to over come gravity when landing rocket style…
Transport back is no issue. A small nudge in the right direction and it gets to the Earth just fine. Even creates its own blast furnace when it arrives ;)
I recently read about Space Mining (through a HaD link?)
The “best case” it presented for mining Nickel Iron asteroids, is to use the finished product in space.
That would/could make space stations/ spaceships? cheaper than launching the structural metals from Earth.
Indeed building heavier stuff without having to haul it out the gravity well is an obvious candidate for space mining, and finding Iron dense rocks to mine seems to be very very easy.
I would expect that to be the first serious space mining venture, as if you want to build something large enough to be more self supporting while carrying people you would spend forever shipping up tiny chunks of it via rocket at great expense, or just ship one or two large rockets worth of processing tool and make large chunks of it in space. Then give them that push to the construction site as that is probably in Earth orbit so advanced electronics etc can easily be supplied, and any human workforce can easily be handled…
My point was mostly if you want to bring stuff back through the atmosphere so it can be used on Earth you run into technical challenges, and significantly more costs.
Should be easier to achieve high quality welds and metal 3D prints in vacuum.
Starship is supposed to be able to return to Earth with 50 tons of payload.
From https://en.wikipedia.org/wiki/SpaceX_Starship
“In November 2019, Elon Musk estimated that a Starship launch might cost US$2 million”
$2,000,000/100,000lb=$20/pound. Plus other expenses to get these 50 tons. That’d be some really EXPENSIVE copper.
If you’re only launching to bring that return payload, sure. But if you pay to launch up to 100 tons to LEO, then the return payload is almost free, since the ship is coming down anyway.
You need fuel to brake, so you can’t both launch 100 tons and return with 50 tons with the same launch.
Though you’re right: the ship is coming down anyways. The question is simply whether you want it in one piece or not.
16 Psyche is what you want to have a look at.
“copper prices have been steadily rising, far beyond the highs of the 1960s that made prospective home owners decide between installing copper or aluminium wiring.” The reason why so many homes from the 60’s and early 70’s was aluminium was the vietnam war. All nato bullets at that time were full metal jacket because of the geneva convention. The full metal jacket is copper over lead. If you ever cut one apart the copper layer is fairly thick. My brother in law lives in such a subdivision in kansas city. The subdivision has 2-3 fires a year electrically caused usually after someone replaces an outlet or does other work on the electrical. You have to use special wire nuts with silicone grease inside to prevent the aluminium oxidation.
NoAlOx is your friend
Since NoAlOx breaks the thin oxyde layer can’t it be used to weld aluminium without the help of high frequency (using MIG instead of TIG) ?
The high frequency isn’t what matters: it’s the argon blanket and the alternating current to burn off the oxides on the surface. The high frequency is used to start the spark, but after that the operating frequency is between 30-200Hz. (and for most of us it’s fixed at 60Hz.) You can weld aluminum with a MIG if you have AC and argon.
Still, a breakdown agent would be really cool for pressure welding.
My understanding also is a major advancement in welding aluminum was the offset AC duty cycle where the adjustment of the more accurately described pulsating DC waveform in some optimized ratio of DCEP to DCEN provided a sweet spot for removing oxidation (DCEN) in the one cycle and welding in the other cycle (DCEP).
Then tuning the frequency outside of the traditional 60Hz signal was an added bonus to further improve, whether a offset since wave or some other pulse train waveform that I don’t recall offhand since I do seem to recall more than square waves being used in certain applications.
There used to be a great article detailing the process I noted above, though I’m not finding the Miller webpage detailing at the time being.
There is perhaps more than enough copper hanging up on telephone poles across the world that has become obsolete due to fiber optics and wireless. It would be great to have some environmentally friendly way of separating the plastic insulation from the copper and being able to recycle the plastic along with the copper.
There is a environmentally friendly way, but it require very much work.
When I was a kid, we went on a junkyard and there was some local alcoholics peeling of the insulator from the copper wires. They then sold the copper to get daily bottle. Only tool they had was a knife, so their carbon emissions was not much.
Today in here some drug addicts do the same, but they burn the copper…
There’s another use for copper which we may see more of as water supply and quality falter. Desalination.
https://www.copper.org/applications/marine/seawater/seawater_corrosion.html
Get’s me thinking of smelting copper ore, though more flammable. Maybe a greenest chemical processing method?
I could imagine, that you could heat the old cables in an airtight container until the plastic melts without burning. It is probably helpful, to shredder the stuff before.
Possibly just dissolving it sulfuric acid and then plating out the metal? Although I’m unsure if dissolving of the insulation material would affect plating process, if whatever various insulations are even dissolvable. If not then basic pre-shredding would be enough to expose enough of the copper surface to the acid solution.
I wonder if there’s a meaningful amount of copper sequestered in landfills?
Millions of wall-warts in the dump. Millions of washers, dryers, box and ceiling fans, millions of kitchen appliances, TVs and monitors, PC power supplies, millions of electronic this-and-that. Yes, one would think there was a veritable mine of copper in any major landfill.
The question of extraction always boils down to the same thing: Economic feasibility and government permits.
Even the way ordinary landfills were done, electronics and anything “heavy” was probably already removed for scrap metal. Old transformers and electric motors are a good example of stuff that was and is routinely removed from the waste stream because it’s easy to do. The rest of the metals are in tiny bits and pieces among bulk waste consisting of plastic, paper, wood, glass, biomass and dirt – so highly diluted.
The most economic recovery of metals from landfills occurs at places that deposit waste incinerator ash. It’s easier to handle for one, and all the hydrocarbons have been removed leaving a high concentration of all the interesting stuff.
There is a meaningful amount of just about everything modern life is built off in landfills… You just have to actually get people to be willing to deal with them and probably find efficient ways to separate the more biological elements from the plastics and metals…
Though if all you want is the metal I guess burning the buggery out of it till the metal flows out for refinement would work… Just seems like a terribly messy waste of other valuable resources.
Metals, chips in short supply, etc. Plus look for the copper theft problem to grow bigger.
I once heard that copper wire was made from only new copper. I had to do some research just to make sure. it looks like this is true as impurities reduce the conductivity. Any recycled copper goes into other things.
Copper isn’t pure when it comes out the ground.. It needs a great deal of processing to become at all close to pure, and there is no reason I can see recycled copper couldn’t end up just as pure, it just costs more to make it so, and while a constant supply of newly refined ore is coming in…
This is actually more of a reply to Foldi-One.
Copper ore is mainly copper, iron and minerals/non-metals (sulfur, etc.) Brass, bronze, copper tubing, etc are mixed with metals that may be harder to remove than the iron is. So simply saying you can make new wire from recycled copper might /not be as easy as making wire from copper refined from ore (I don’t really know either way but I know some metals are like that where it’s harder to extract from an alloy than from the raw ore.)
Never said it was ‘as easy’ Mike, but its very definitely doable, it just hasn’t been done much if at all as ever increasing demand for a higher total capacity of copper and its alloys means its always being mined and the mining refinery is always running (at least till the mines run dry) – which means its probably never been economically worth refining old copper to that level of purity when the stuff that needs really pure copper has a ready supply of ‘brand new’ copper, and there is a huge market for the less pure copper and copper alloys for other purposes.
>Just seems like a terribly messy waste of other valuable resources.
A lot of the time the separation and re-refinement of these “valuable” resources costs more resources than just making more. Most recycling isn’t even recycling, but simply shifting the waste to a different landfill through inferior throw-away products, because the society pays for the recovery of the materials and hands them over to private businesses with the illusion that they would substitute primary materials.
E.g. a plastic bottle is not recycled into new plastic bottles (less than 10% are), but instead go into making cheap fiber for the fashion industry, from where it ends up in a landfill, dumped as “donations” somewhere in the developing world, or gets burned as unsold stock. The point of that industry is that the materials and labor are effectively subsidized to be far cheaper than the business infrastructure, so it doesn’t matter that you’re pushing millions of tons of rags that nobody ever wears.
In a bit of irony, the Swedish city of Västerås has apparently made a switch to fossil-free heat and power generation by burning H&M surplus clothing stock among other stuff.
We pay for the recycling through various mandates and surcharges, or mandatory waste separation instead of directly burning it for energy, while the industry is unable to utilize the materials, so the cost of recycling is wasted and ends up as a net negative – more CO2 emissions and primary resources are used up to “save” on materials. It ends up pushed to extremely low value products such as plastic pavement tiles or wall insulation, or indeed to landfill and incineration by a slight detour.
Valuable resources left in landfill but that isn’t available after you burn the buggery out of it isn’t all plastic, there is a heap of useful materials in landfill, and perfectly good parts, and all the living soil like decomposed organic matter is pretty useful really. Yeah its probably simpler to just burn the buggery out of it, still better at metal extraction than opening a new mineshaft, but it still seems a waste.
Though Plastic really annoys me – if you made it a legal requirement for all short lifespan plastic object to be made of ONLY one type of the many plastics that recycle really really well, and then gave them bloody colour codes they must stick to so all HDPE is Blue, etc it becomes trivial to sort by machine, and the quality of recycled plastics goes way way up and the bulk of the plastic waste becomes useful resource, rather than bulk filler.
You still have heaps of plastic that wouldn’t be covered under those rules, but that isn’t the end of the world, as much of that plastic would be wrapped around electronic goods that should be recycled properly for all the other valuable parts, and some energy reclaimation of the oddities like lunchboxes, power tool handles etc that are often composite plastics isn’t too bad (and being multicoloured should be easy enough to pick out of the initial plastic stream if everything else was single colour)…
Also why are we using so many plastic bottles, make them in glass and it is trivial to sterilise and reuse them as milk bottles have been for eons, and those bottles are pretty easy to recycle to good quality glass again.. (its not like its a safety thing – as it if was the people impairment juices would be in plastic bottles and the fizzy pop rubbish and fruit juices would be in glass)
>make them in glass
More expensive, less efficient to handle. You’d basically spend a dollar to save a dime. Glass bottles are only useful where the product needs an absolute barrier against oxygen, such as in beer bottles and milk bottles, to prevent it going off too quickly.
@Dude,
I prefer my cooking oils in glass as well, I don’t trust plastics leaching into them.
The dichotomy challenge of survival requirements vs profit motives.
Glass is heavy and fragile.
Martin Glass is hardly fragile – yes to be thick enough to make good bottles does need them to be heavier than plastic, but still not really fragile, perfectly good for decades of use even – there have been suggestions that the milkman delivered bottles are on average over 10 years old – not sure where I read that, but it stuck with me..
And that endurance makes them CHEAPER @Dude, at least if you don’t insist on destroying them over cleaning+reuse, sure it will add a tiny amount to the shipping volume, though probably not enough to make any difference as external sizes are similar – glass and plastic bottles tend to be carried in the same crates, and definitely somewhat to the weight shipped.
But again adding a little weight to perhaps as many as 4 trips – bottling plant – store, store – you, you – bottling plant (the clean/sterilise side) probably via a recycling collection step rather than the huge con job full of transport that is plastic ‘recycling’ where ultimately its just going to end up shipped off to clog a river in the Far East…. Its a clear winner to not use plastic…
Also most Milk bottles are PLASTIC… In the UK most of them are HDPE if memory serves – barrier against oxygen pfft, its not a good reason – beer comes in glass because it does, probably mostly marketing social values type stuff – cheap sugar crap the kids love is in those garish neon coloured plastic bottles, us mature manly folk want solid bottle type reasons, certainly no one good reason that is universal – I’ve seen beer in plastic, and plastic lined cardboard before…
Although CCA looks like it has some great benefits, what are the risks? With typical electrical installation practices, how easy is it to damage the copper layer when twisting wires together, locking in with screws (esp. the “screw down” type you often see in the busbars of load centers) and winding up making your connections at the aluminum layer rather than copper? Even if original install is done carefully by trained electricians, subsequent repairs (replaced socket, etc.) might be done by untrained homeowners or tradesmen who don’t know the characteristics of the wire.
Just think of the number of times you’ve stripped the insulation off of a wire, and the tool stripped some of the conductor off as well.
That’s why I use a tool made for the job. Better strips too. Nicking conductor weakens wire.
I have never seen a reasonably priced wire stripper that accurately cut the insulation but didn’t nick the wire every so often. Angle you hold it at relative to the wire, wear, whatever…they’re all imperfect. Some good, some bad, but none perfect. And with CCA, it looks like you need perfect.
Now, what about flexing? As you bend the wire to move it through walls, boxes, etc, is the aluminum core going to weaken? Are the differing thermal expansion rates going to cause delamination of the copper cladding? How about over time, moisture effects?
Not a fan of CCA until there are some best practices developed. Chinese manufacturers seem to have gone all in on it though (and, predictably, you really have to look carefully to see whether that cheap cable is copper or CCA)
ABout $US10 for a basic hot wire stripper. No nicks, but ventilation is strongly recommended.
GOOD CCA holds up as well as pure copper. There isn’t as much good out there as one would like, though. The cladding should never separate. Properly clad, the copper and aluminum form a couple atom thick alloy region without significant growth brittle intermetallic phases. (see, for example, Lapovok, et al, 2019 for more information about the bond strength and the effect of annealing) There re best practices. They don’t help with poor quality or misapplied material.
Poorly made CCA will have gaps in the cladding, may have the cladding separate or from the aluminum, and may be work hardened too much without appropriate annealing, leading to flaws in drawing (I’ve dealt with these specifically in material acceptance, There are a number of other way to go wrong, like excessive alloy and intermetallic formation during anneal, leaving a layer that is both brittle and has poor conductivity between the cladding and core)
How you use it also matters. Proper joints are a must (in the applications I deal with, crimp with the proper lubrication/anti-oxidation compound). Soldering is problematic unless the proper wire is used and the proper solder, and terminations that don’t fully capture the circumference of the conductor, and support/strain relieve, can be problematic. THey must be properly designed.
I was service manager at a large sat installer the cable strippers come with their own Allen wrench to adjust the blades. Of course some techs would adjust themselves and cut the wire, I had to remove all the Allen wrenches and just adjust the blades every other day or so and gave them 2 strippers for the cable. Solved quite a few service calls. Using anything else as a hammer to drive in a ground rod was a fireable offense, would have copper marks on almost anything made of metal because somebody didn’t want to carry the “heavy” sledge hammer! Use the right tool or don’t do it, if you left it at last job call!!
I won’t use CCA, especially for audio and power applications. I don’t care how anyone tries to justify it… it is pure garbage.
I guess I’ll start hoarding my choices of wire…
Anyone who claims CCA is a viable alternative to pure copper wire has never tried to actually work with the stuff. Saying it is pure garbage is being too kind! The description of it in this article is dead wrong. It breaks easily, is very difficult to solder, it does not play nice with crimp connectors, much less insulation-displacement connectors (RJ-45 jacks for example). But worst of all, it corrodes into [non-conductive] aluminum oxide dust in nothing flat! I installed several thousand feet of it near the beach and had to replace it all in less than 6 months due to the salty air. And that was despite all connections being covered in marine-grade adhesive-lined heat-shrink tubing and run thru conduit. The copper wire I replaced it with is still working perfectly after 7 years. But even inland and indoors it doesn’t last long. I had to learn this the hard way and it has cost me a fortune. Antron Argaiv says the Chinese manufacturers seem to have gone all in on it, and that is true only to the extent that they are pushing it heavily as rolls of wire for sale in other countries. You will note that NONE of the electronic products they produce and sell use it internally. Too unreliable, even for their low quality control standards. CCA is EEEVIL! Avoid it at all costs!
If the copper clad becomes damaged and exposes the aluminum, there is a very bad thing that happens. When there is an environment where corrosion is possible, the aluminum becomes the sacrificial anode while the copper remains. Imagine the heat generated by a “poor” joint that is created by corrosion due to the copper clad layer being damaged/removed. I’d never use CCA in an electrical application. Very bad idea!
100%, right there with you! Thanks for expanding a bit there, it’s “nice” to see some practical applications where using CCA would be, at best, dangerous as hell. Workability aside, I’ve personally experienced CCA failures, overcurrent due to the copper layer becoming even barely nicked… leading to fires and exploding batteries. I refuse to use it in power or signal applications.
I’ll keep shelling out for (or reclaiming!) copper at all costs.
Low voltage installer here: Never install Copper Clad aluminum for I wall Ethernet. It is usually half the price. Even here in Arizona it corrodes quickly and causes unreliable connections. CCA is fine for factory made patch cables( connections are with stranded cable, using connectors meant for stranded wire, usually hermetically sealed in plastic). It and viper clad steel are also fine for RG-6 cabling(it uses a different style connection). But when left in the open air the solid core CCA Ethernet wire is junk. Additionally if a long run with POE is used a fire can break out, or at the very least it can burn itself up and the cables around it.
*in wall Ethernet
*Not Viper, meant copper
HackADay took away the edit feature
CCA, as a building wire, is indeed a viable alternative to CU. It’s being installed all over the country, with some installations dating back 50 years to when it was first recognized as a allowable conductor in the NEC. Made to ASTM B566, the conductor forms a metallurgical bond that prevents galvanic corrosion and thermal creep (relative to that of AA 1350 used in the 60s/70s) and works flawlessly with CU rated terminations. It is, by mounds of testing data, an excellent alternative for building wire.
Time to invest in commodities?
Better late than never?
Anyone else getting a strange optical illusion that the image at the top appears to move as you read the text?
Hackaday is experimenting with subliminal messaging.
B^)
I suggest looking at where cobalt and other rare earth metals are obtained, Back in the late 70’s most of the rather small amount of cobalt, critical to the metallurgy of jet engine turbine blades, produced annually came from the Katanga complex in the Congo. Many exotic metals are a by-product of copper mining.
Rare earths are not rare. They just don’t occur in concentrated form in nature. So unless there are other metals to be recovered at a profit, mining them is often not viable. Here’s a link:
https://pubs.geoscienceworld.org/books/book/1998/chapter/16272577/By-Products-of-Porphyry-Copper-and-Molybdenum
Those really large open pit mines that the environmentalists object to are copper mines. Ore tenor is less than 1% Cu by weight. That’s a lot of rock that has to be crushed to a powder. That process takes a lot of energy.
Throwing copper wire in a landfill is a crime against future generations.
I recall the Cuban’s even had a Military mission in that part of the World, albeit not blatantly, somehow related to Cobalt international interests.
Recycling in general seems needs advances in automation and maybe even robots.
I was literally talking about this topic, that began with the discussion of recycling plastics, a few days back with the gentleman I purchased rather fittingly to the topic… a 200A old fashioned transformer manual design battery charger. Later I found the windings to be copper plated aluminum… however if required in the future… I can technically rewind and adjust the diameter of the enameled copper wire accordingly for the output.
One of those, homebrew ferrite polymer material core transformer builds or mods that I’m not certain how will perform at ~60Hz… or just find a nice larger than a MOT or other ideally toroidal high wattage core? I jumped on the probably overpriced for my interests $50 made in ¿Mexico? rescue. Forgot to ask before the long drive if was made in the USA or not. Anyways…
He reminded me in our lengthy discussions about the use of Penal labor to do the trash sorting for plastics. Seems fitting also for the role. Basically, have the jail and prison systems perform the work as slave labor or lower cost labor that no one in society wants to perform anyways so there is not lobby preventing/discouraging their capabilities to be productive somehow and wasting labor.
I had a long reply, with exhaustive detail that seems to have got lost..
But in short Plastic is not Metal – vastly different recycling and extraction costs and environmental impact comparisons…
And Plastics could be made much better if effort was put in to make short lived plastic objects out of plastics that recycle well, and mandate a colour code for each one of those plastics to make machine sorting trivial. Suddenly most of the plastic waste recycles to much higher grade end plastics..
One piece of the solution is to change electrical codes to permit lower current circuits. With LED’s being standard these days there is no need to run 14 gauge wire for lighting. 18 gauge with breaker at like 5A would use less than half the copper. In reality we could even go to a lower current rating and even smaller wire. Most LED’s draw less than 0.1A at 120v and you don’t have all that many in a typical house. All the LED’s in my house draw maybe 1.5A total.
Trying to bring POE+ lighting home I see. Plus there’s the idea of light-based communications.
https://www.versatek.com/5-poe-lighting-platforms-powering-the-lighting-solutions-of-tomorrow/
or ditch the 120v, 240v is already “not enough”, so three phase 410v is a must.
@400Hz
B^)
It’s not just copper for use in home wiring, but also for plumbing – it’s superior to non-metallic plumbing when is being subjected to heated water as in time that will weaken and crack non metallic plumbing causing extremely expensive to remediate household plumbing disasters. Copper is the superb choice in that scenario.
And then there is the specter of what a copper scarcity will do to all the concerns that get published about on Hackaday – could really start to put a crimp in the Maker world too
And copper scarcity is just the tip of the iceberg so far as materials problems that a hyper spike in electrical generation/motive technology is bringing on. A huge one are the materials concerns that underlay battery technologies. The irony is that so-called carbon-free green tech may be an Armageddon disaster for longer term environmental concerns – as the Earth gets raped in the frenzied effort to claw at all these less bountiful and/or more difficult to recover raw materials (which also have negative downstream environmental consequences if they’re not reclamated in some manner).
Maybe in 30 years the internal combustion engine automobile tech that Toyota has prototyped might not look so wrong-headed. Build out hundreds of new Thorium nuclear power plants and start generating hydrogen to power transportation – there have also been break-throughs on hydrogen fuel storage tech. Sure, could go with hydrogen fuel cells, but that would imply electric motors, etc., and so back to demands on copper (unless a carbon nano tube wound electric motor can be devised).
Copper as a common heatsink metal? Not in this universe!
It’s a shame we scattered so much copper and tin all over Vietnam.
It’s still there…