In the last decade, the price for making a single PCB plummeted. And we’ve featured tons of hacks with boards hailing from places like OSH Park or Seeed Studio. But this phenomenon isn’t isolated, and all sorts of one-off prototyping services are becoming cheaper and looking to satiate both hobbyist and engineer alike.
Today, I want to blow the lid off a few places offering one-off mechanical prototyping services. I’ll take us through some history of how we got here, introduce a few new players, and finally highlight some important tradeoffs before you start ordering bespoke aluminum parts straight to your doorstep.
Now go get your ANSI Z87+ safety glasses, and let’s get started.
Our PCB Origins
Just over a decade ago, ordering Printed Circuit Boards (PCBs) was an expensive (nay, too expensive) ordeal for the hobbyist. Getting a single board made would cost you several hundred US dollars at the PCB fab house. The issue wasn’t the price per board. It was the up-front manufacturing cost to push the board through the factory. Sadly, PCBs just aren’t made one-at-a-time. They’re consolidated with other copies of the same PCB onto a larger panel to simplify the fixturing process when moving the design from machine to machine in manufacturing.
But soon after, a small company called OSH Park did something wildly different. Acting as middle-agent, they consolidated different PCBs from various designers onto a shared panel and sent that panel design out for manufacturing instead. The result was that hobbyists could order a single PCB through OSH Park for a fraction of the cost of needing to place a batch order directly. And what was once a professional process became available to the after-hours engineer for a few dollars and a few weeks lead time.
Of course, this process didn’t come with all the perks of ordering direct. The sacrifice was that PCB designers needed to agree on some manufacturing settings that would be common to the panel, like layer count, minimum hole size, pcb surface finish, and color, which is how we got OSH Park’s unmistakable purple soldermask. Finally, since OSH Park needed to aggregate enough orders to send out a panel, orders would take about two to three weeks to return back to customer. But, despite the constraints, the design space of what’s possible is tremendous, and the low price made the extra wait time worth it for hobbyist projects.
In the years that followed, other manufacturers caught on, especially in China. And it seemed like a race-to-the-bottom to offer the cheapest single-quantity circuit board. For the first time, electronics hobbyists on a budget were able to use the same manufacturing processes as the professionals. Now, names like JLCPCB, Dirty PCBs, Seeed Studio, and PCBWay are pretty common among this community of hackers.
Prototyping as a Service
Many of us know the story above. Heck; we lived through it! But it doesn’t stop there. In fact, something similar is happening in other domains. Other manufacturing services are opening their doors to one-off prototypes that used to require higher minimum orders, and the result is that your nearest hackerspace could be entirely virtual where parts get ordered and delivered to your doorstep.
It’s worth asking: where is this happening? Right now, we’re seeing these options emerge from 2D computer-controlled manufacturing processes like laser cutting, water jetting, and 2D CNC routing. The common theme? Each of these processes uses tools that operate on big sheets of stock material. The upshot is that, with some upstream pre-processing, batches of orders can be consolidated onto the same sheet — just like OSH Park did. In theory, this trick could extend to any manufacturing process where software can glue together aggregate orders into a batch process.
Right now, batching orders onto sheets of shared stock material makes a lot of sense. But, with some work, it’s possible to extend this concept to other processes. In the meantime, it’s time to take advantage of the added process capabilities that can be delivered to our doorstep for a fraction of their original price.
The Players
Let’s take a quick tour of who’s delivering manufactured singles straight to your doorstep. I imagine that our readers will be familiar with Shapeways for SLS 3D printing and Ponoko for laser cutting, so I’ll sidestep them to highlight some other up-and-coming offerings.
Laser-Cutting: SendCutSend
Laser Cutters for cutting metals are awesome tools, but the tools themselves can take up a significant footprint in a home garage–not to mention making a huge dent in our salary! Instead of installing a metal laser cutter and learning how to use it myself, I’ve started opting for options in SendCutSend‘s catalog.
For the brief batches of items that I’ve started ordering from SendCutSend, I’ve had parts sent back to me early the next week. Most metal parts from SendCutSend arrive by default with a characteristic rough edge, but I’ve softened those edges with a couple minutes of steel wool and elbow grease. What’s more, the holes made from SendCutSend’s aluminum line are cut precisely enough that I’ve been able to tap the holes with M3x0.5 threads. And if you’re especially lazy, SendCutSend will even do the tapping process for you.
Finally, it’s worth noting that SendCutSend applies kerf compensation to all of their laser-cut parts. That means you can send in a DXF file that’s the exact size of your part and the manufacturing process will adjust such that parts are cut as close to nominal size as possible. If you normally work with laser cutters out of your local shop or school, this is a pretty big convenience since we generally have to offset the DXF geometry to account for the spot size of the laser cutter.
I’ll mention: the minimum price for parts from SendCutSend is $30, but I was able to get a batch of 10 of the above parts made without any price increase.
Carbon Fiber CNC Routing: CNCMadness
For quadcopter builders out there, carbon fiber parts are the secret sauce to making sturdy flying frames that are both light and stiff. Unfortunately, laser cutting composite carbon fiber sheets is out-of-the-question since these sheets will spew nasty fumes from the glues they’re made from. Machining these sheets is also not just difficult, since carbon fiber eats through normal cutting tools like sandpaper, it’s also dangerous since the debris made from cutting these sheets can be harmful to breathe. Since cutting this exotic material at home is difficult at best, wouldn’t it be great if we could simply order these parts as a streamlined service?
Enter CNCMadness. I’ve used them over the years for all sorts of custom plates of various thicknesses. Normally, I’d reach for carbon fiber when saving weight is a key design consideration. But CNCMadness’s price range is so good, I’ll find myself reaching for carbon fiber even when weight doesn’t matter. On a typical order, I’ll usually get parts (ordered from the US) within the next week after ordering.
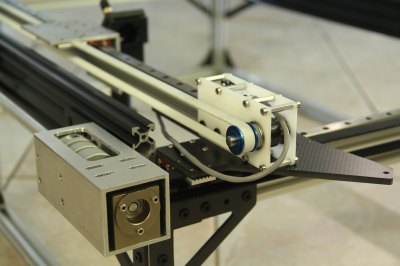
Finally, it’s worth mentioning: unlike aluminum, which can be reworked with hand tools and even recycled for scrap, carbon fiber parts are more of a one-shot deal. If I find design mistakes, these parts are off to the trash, so I usually try to keep that thought in the back of my mind before hitting the “buy” button.
Other Manufacturing Services:
Some of these next players offer something either brand new or quite niche. Nevertheless, for completeness, they’re still worth a mention since they hint at where prototyping services could grow in the future.
Resin 3D Printing: PCBWay
PCBWay is branching out and now offering various 3D printing services, including a nifty clear resin offering. While it’s still early, some of the results are starting to emerge on Twitter, and the case is compelling to give them a try. For a manufacturer that got its name in the hobbyist landscape making circuit boards, it’s nice to see them branch out while it also hints at how our relationship to prototyping services is changing.
Low Volume Injection Molding from IGUS
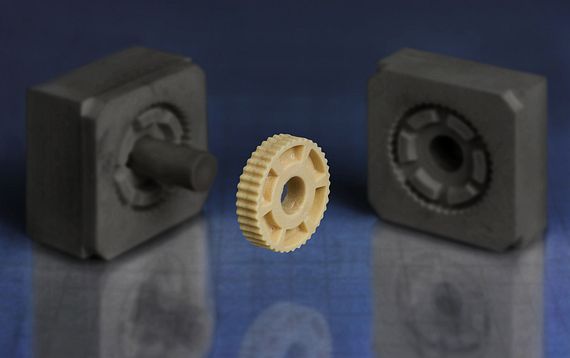
Injection molding generally has a tremendous up-front cost for manufacturing the mold. But IGUS offers 3D printed molds made from one of their specialty polymers that significantly reduces the wear on the mold and can be used for lower volumes at lower up-front costs. The quoting process is involved, but this service may be a useful resource to keep in your back pocket.
Make-it-Quick Tradeoffs
Just like OSH Park, the services above make some sacrifices for promising those fast economic part offerings. But, of course, in plenty of cases, those tradeoffs don’t matter. Nevertheless, it’s worth being explicit about the three options that get sacrificed: design inspection, specifications and tolerances.
Design Inspection
First off, we lose design inspection. With expensive manufacturing services, humans will often inspect your order to make sure what you’re about to have them make is free of glaring errors. Early in my engineering career, I had my employer’s go-to PCB fab house kindly point out some of those glaring errors with my PCB design, the worst of which was letting some printed text land on the copper layer instead of the silkscreen layer. Had they made my board as-is, I would’ve waited two weeks for thousands-of-dollars worth of useless coasters and perhaps a lightly-annoyed boss.
With these new low-cost prototyping services, it’s unlikely that any human will intervene to tell us what’s wrong with our design file. It’ll just get made as-is. That said, even if we order some scrap aluminum, the cost of doing it wrong the first time is much cheaper. Heck, let’s just say we get to make more design iterations.
Specialty Specifications
At the price of speed, these services sacrifice specifications. That is, we don’t get all the options available to us that we would otherwise get when quoting with a more traditional machine shop. Among these sacrifices, we lose out on specialty materials, surface finishes, coatings, heat treatments, and other post-processing tasks like deburring sharp edges. If we’re seeking out these shops, we probably knew about this tradeoff beforehand, but it’s worth making explicit. Finally, if there’s some special post-processing technique that you need but don’t see offered, reach out to them. They might be willing to make an exception for you for a fee. And with enough folks inquiring, it might become the next specification they roll out.
Tolerances
Finally, we have tradeoffs in dimensional tolerances. This one is by far the most important tradeoff to consider. The sad reality about machined parts is that they’ll never be the exact dimensions that our file specifies. As designers, we need to design for this quirk, making sure our design works over a small range of size deviations called dimensional tolerances.
With a high-end machine shop, dimensional tolerances are just specs. You can specify how exact the part dimensions need to be, and the shop will try to make the part within those tolerances, increasing the price for tighter specs. But with these low-cost services, we don’t get to specify how exact our part dimensions will be. Instead, they will either list fairly coarse tolerances up-front, or won’t list any manufacturing tolerances altogether.
Without dimensional tolerances, we have two options. Since most processes are made from CNC machines, we can probably expect reasonable relative tolerances between features but slightly coarser tolerances on those features themselves. In other words, the spacing between two holes might be fairly tight, but the hole size may be a bit too small or too big. One option here is to simply live with these coarse tolerances as-is and design around them such that they don’t matter.
If tight part dimensions do matter, the next option is to do some at-home post-processing. For instance, if we want to ensure a tight tolerance on a small hole, we can order parts with undersize holes and then drill them out at home ourselves to a much tighter specification. This option isn’t always practical, though. While it might be cheap and easy to drill holes out of aluminum, post processing materials like carbon fiber can be much more impractical since it requires specialty carbide tools to be able to drill through without instantly dulling the drill bit.
Finally, it’s worth noting that thickness and flatness tolerances are also not available specifications with these low-cost services either. That’s especially important for laser-cut plastic parts where the process of laser cutting the part can actually cause it to warp or curl upwards slightly. All that said, once we know about these limitations, we can put them to use in a way that consistently yields parts that meet our expectations.
Where We Came From; Where We’re Going
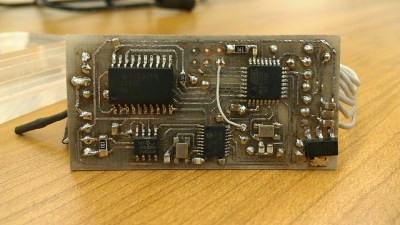
About a decade ago, it seemed like understanding the dirty process of etching PCBs in your garage with nasty chemicals would make you the coolest hacker on the block. But nowadays the dirtiest part of the craft of circuit board making has been replaced with an ordering process that’s too convenient to overlook. What may have been garage sorcery has been reduced to a few clicks away. But the result has been an explosion of hardware projects that all rely on what used to be an either commercial or boutique process for those with money or patience.
It’s worth asking: how is our relationship to hardware design going to change as we start to leverage these services for our after-hours hobbyist projects? I’d say that, just like OSH Park did, these mechanical prototyping services open up new doors to the complexity of the projects we can make at home. Now we need not rely on strictly 3D printed parts. We can work in metal sheets too! And with added complexity comes a proliferation of new ideas that I hope to read about here.
But something is lost. And that’s my intimate relationship spent working with the raw materials themselves. There’s something quite soothing about that sweaty machine shop ritual of leaning over your part while chips fly off into the corner. But not all projects need to undergo this ritual to have meaning. And since these new services only continue to multiply the effect of my project efforts, you can bet I’ll keep using them.
What nasty chemicals? All it takes to etch a PCB is a bottle of ferric chloride which can be reused over and over again.
Ferric chloride is pretty nasty to be pouring around if you don’t have a sink you’re not worried about permanently staining.
You can also etch PCBs using a 50-50 solution of vinegar and hydrogen peroxide.
Yep it’s what I do, works pretty great. Technically the leftover liquid is not great because of the dissolved copper, but it’s easy to let it evaluate in a waste container.
No, ferric chloride is very much a consumable. A miserable one too.
Use muriatic acid and hydrogen peroxide. Much nicer. Prettier colour too.
It’s an exciting future! more and more is being offered for a lower price. Soon we will be part of a dot com like gold rush in hardware startups as it is becoming much easier and cheaper to get started.
Perhaps eventually we will see all in one companies, you just send them a list of what you want and some payment, then it arrives next day.
https://www.youtube.com/watch?v=Spr5PWiuRaY
Wow, that video is lovely. And the comments…
Although it makes me a little sad about the current state of science education.
I’ll just mention protocase.com — custom enclosures, cnc manufacturing, laser cutting & marking, multiple materials, powder coating, many other operations. Very responsive and super-fast. I’ve no skin in the game, just a very happy repeat customer.
It seems high precision, detailed, 4 and 5 axis machining isn’t quite on the race to the bottom yet. I do medical and aerospace prototype machining, and my clients are choosing me over Protolabs, which is only a few miles away.
I work similarly in a prototype shop with 5 axis, all geared towards robotics & aerospace. There will always be a need for real machining where everything is spec’d, but people who can do it properly are becoming fewer and fewer. This means if you know how to do it and you have the capabilities and you position yourself correctly you will always have work.
I can definitely attest to how nasty carbon fiber machining is. I still do it, and I used to have a customer having me make custom quadrocopter parts out of a special form of carbon fiber but they may have gone to this company above to have them done in en masse. For once I’m glad- dragonskin is horrible stuff to cut. I don’t miss that job one bit
I did a few parts from Rock West CF plates a number of years ago. Didn’t seem too bad, but I didn’t do it in an enclosed machine; I used an old Prototrak with a shop vac duct taped to the spindle. I also didn’t make enough parts to notice tool wear.
5 axis, that’s not easy as we are bulding for robotics I am aware of the difficulty.2 colleagues are finetuning the codes,3 engineers are responsible for the construction,2 weeks have been passed while the situation is behind the schedule. Estimated the project could only be finsihed in 3 weeks. our parts from http://www.dold-mechatronik.de & https://www.toco.tw. While I am thinking how to improve the efficiency by other means.If anyone could provide some advices.
Would be cool if you could also add some european based companies, for the people on the other side of the pond.
For laser cutting in steel, aluminium etc: http://www.laserboost.com is Barcelona-based
For extrusion profiles: http://www.motedis.com
For mechanical parts (not at the level of mcmaster-carr): http://www.dold-mechatronik.de
In FRANCE laser cutting: http://www.laserouest.fr/
Fractory.com for sheet metal they are UK/Estonia based. They will cut, bend, and paint for you. Pricing is good and they have a standard 10 day lead time. From using them quality is good but your surfaces might have some extra scratching from handling, I haven’t used their painting service.
Protolabs for machining, very expensive but if you want it shipped next day they will ship next day.
There’s also eMachineShop – probably the granddaddy of online retail prototype services. They’ve been around longer than OSHPark, even. Similar business model in that they’re an intermediary that contracts out the prototypes to various shops.
But. But.. I want to like doing things the hard way, with my own hands. As an amateur, I want to develop skills, I want to evolve (like an Eevee, hi). I want to learn new techniques (cable lancing etc) and educate myself, be an autodidact (like MacGyver, hi). I would like to explore new craftmansships on my way, too, not just electronics. Learn about chemistry, wood work, etc. I’m from the 90s, am I really the last of my kind ? 😨
In my day (’70’s) we did most of that _at_ school, woodwork, metalwork, chemistry, electronics too.
I suppose with the move of western economies away from manufacturing, less of this is done at school age and they now do more service-economy stuff.
So yes, you’re a dinosaur, and about to go extinct! Like me, I expect, but maybe a decade or two later.
Indeed. Try hiring an entry level machinist these days. It’s hard to find someone who knows the right direction to turn a screw. A few years ago I was looking for an assistant and called Dunwoody (reputable tech school with a good machining program.) I asked if they had any promising students I might talk to about a job, they laughed at me and told me they ALL had internships lined up the moment they registered for classes. Two big name shops had cornered the market on their students.
Same here, I am from Eastern Europe and in almost all school years (80s and 90s) we had a lot of practical work with wood, metal, electricity basics etc. Now in my 40s and I still use this knowledge on a daily basis. Sometimes it’s not about economy, it’s about the ability to do something, and that’s especially important these days when you can’t expect to order overseas and get it in a few days.
Don’t worry, nobody is making you order your stuff from professionals. You just aren’t required to do it yourself if you don’t want to. I taught myself PCB etching in the past year because I don’t like paying or waiting for shipping, and I like being able to do things myself. It’s good to know how to do things, but when you don’t want to, it’s nice to be able to order things.
Wasn’t sparkfun first to the game not oshpark? Batchpcb goes back to 2005 and oshpark came around in 2011?
Olimex were making cheap PCBs before anyone else it seemed. At least in 2001.
Indeed. SparkFun created BatchPCB, then in 2013 sold it to OSH Park.
OSH Park were soooo late to the party – no way on earth did they start this. Pcb-pool – now beta layout in Ireland started in 1994. I believe they were the first and created this concept. I was ordering from these guys way before there was anything comparable on the market. It was a total game changer at the time.
1994 is very early indeed.
I think Sparkfun also had an early service around the same time that OSH Park was getting off the ground.
I guess it’s pretty good times we are living in with all these affordable services. Still, I sense a danger of offloading too much to the pay services. Eventually we might find ourselves paying someone else to have all our fun for us too! I wish there were more DIY PCB articles again like the old days.
In Wired’s recent interview with James Dyson, he mentions a caution of using a prototyping service, if you you are planning to patent. It can be argued that if you’ve sent off for the prototype that the company that built it was the original creator, and not the person hiring them.
I am not a lawyer, but did generate several patents in my professional life. Essentially, the creator of a work must be on the provisional application paperwork even if the IP rights are assigned to a company. This legal agreement is implicit in some places like Canada, but must be noted in your contract on US soil. i.e. if you are a novice around NDAs/Contracts, than your employer can indeed claw away any hobby work you may think is unrelated to your job.
There is also a limited number of NDAs one can issue before a work is considered published. As a small entity, most contract manufacturers and factory owners will likely tell you to pound sand if you push the NDA issue.
I have dealt with the issues you raise and wish Hackaday would do an article series on cya if you work for someone else, like most of us, but develop an idea you want to patent, and don’t want your employer to have the power to go after that. I’ve been in this situation several times and it’s never fun and it’s kept me from trying to patent some things.
The old image of people holding their inventions while lining up at the patent office (i.e. First to invent) no longer exist.
Patents are under First to file (EU) or First inventor to file (US). https://en.wikipedia.org/wiki/First_to_file_and_first_to_invent
>In a first-to-file system, the right to the grant of a patent for a given invention lies with the first person to file a patent application for protection of that invention, regardless of the date of actual invention.
You can file a patent without having a prototype, so do that before you outsource the work.
That’s true, but if you can ahow that you invented* it first, you can probably prove the first-to-file invalid. It doesn’t mean that you get issued the patent, but ir does mean you’re unlikely to get locked out of your own invention.
* “Invented” in this case really just means “documented the idea.” e.g, published it here on hackaday.
I am not a lawyer, this is not legal advice etc etc :-)
To me, the comfort of knowing that i will get a professional looking item to accompany my electronic projects makes me want to consider doing anything mechanical at all, so it clearly widens the possibilities for me.
The disappointment from my own poor mechanical attempts is then spared. I do admire those lathe movies but it requires different skills and tools that i have.
Currently waiting for the results of a first order with pcbway, but love to see experience with EU cnc shops as well.
Even just a decade ago you could still order cheap pcbs through ebay and aliexpress. You just worked with someone directly through translating chat apps. It definitely wasn’t as fully featured as the great websites we have today. but it was still pretty cheap and painless
If a prototype shop had a path from one-off prototypes that included electronics, case, packaging, etc. to production including white-label shipping, you could rule this space.
If you’re thinking of starting such a company (or pivoting into the space), talk to me and I’ll share what I know.
I use a normal PCB Service for front panels, if I could just get them to offer aluminum or plastic instead of fibre-glass that would meet 100% of my 2D mechanical requirements
Boz, JLCPCB offer aluminium PCB substrate that might meet your needs. I haven’t tried it myself.