[Billy] has a special interest in passive hydroponics (also known as the Kratky method), which is a way of growing plants in nutrient-rich water that does not circulate. As the plant grows and liquid level drops, only the tips of the roots remain submerged while more and more of the root surface is exposed to oxygen in a harmonious balance. However, “thirsty” plant types (tomatoes, for example) throw off this balance, and the system needs to be modified. To address this, [Billy] designed and printed a passive float valve system that takes care of topping up the reservoir only when needed, without using pumps or any other electrical equipment.
Commercial or industrial float valves are too big to use in his small tanks, which led [Billy] to test dozens of DIY designs. He used everything from plastic water bottles to pipe ends, but nothing quite measured up. With 3D printing, [Billy] was able to create a sealed, lightweight float that exactly matched the housing and tube locations.
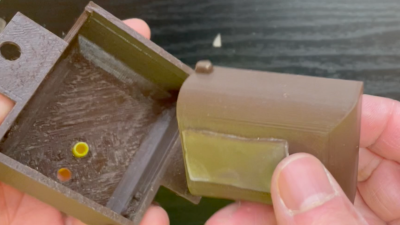
The way [Billy]’s float valve works is by using a hollow object as a kind of buoyant plug inside a housing. When the water level is high, the buoyant object rises up and presses a strip of silicone against an outlet, preventing water from flowing. If the water level is low, the buoyant plug drops and water is free to flow. With a reservoir of fresh nutrient-rich water placed above the grow tank, gravity takes care of pushing a fresh supply down a tube, so no active pump is needed. Combined with a passive float valve, the system pretty much runs itself.
Watch [Billy] give a tour of his system and valve design in the video embedded below. He’s got a lot of experience when it comes to working with projects involving liquids. Only someone as comfortable as he is would make his own DIY dishwasher.
I think this can still be optimised further to have no moving parts, like those self-fillong dog bowls that use a sealed container turned upside down to set the water level at the container opening. When filled to that level, no more air can get into the container and the flow stops.
Use a TIF distance sensor to measure the water depth, such as one of the ones at SparkFun that measure up to 250mm in increments of 1mm.
The water has a different index of refraction, and will show a different sensor distance based on the amount of water.
No moving parts, and nothing comes into contact with the water. It’ll even work through a protective glass window.
You can put a TOF sensor on the side of a tank with transparent walls and measure presence/absense of water for a binary level indication.
The goal is not to measure the water level but maintain it at a setpoint.
If the goal is not to measure the water, a simple drop-off tank can be used (similar to a a couple of steps of a staircase) with the plants on the top, and the reservoir at the bottom. A simple drain and flush method can be deployed here, further oxygenating the water using simply gravity. If the plants need a constant soak, a skimmer ledge could be weld-on’d or siliconed to the top. This would allow for both standing water, skimming filtration, and oxygen replenishment. You could take it a step further by adding a third layer and making the middle ledge with a deeper compartment. Pack it with polyfill for a algae filter. This helps to filter the scum and costs only pennies each time you change it. It’s also readily available at most stores. The bottom would the reservoir, make it as deep as you want, and you could even make it mostly covered to prevent evaporation. Bonus if the lid prevents light from entering. Use a nano sized protein skimmer pump with an impeller wheel/venturi to induce micro bubbles on the top tier for even more oxygen. If you pick the right pump, you can lift and induce micro bubbles at the same time. Make sure you dont go too big on the pump because it will actually end up separating the nutrients from the water (thats what proten skimmers are designed to do after all). You don’t have to add more failure points to the tank, you just need to make a better designed tank with equipment suited for the job.
That’s great, but it’s not going to shut off the water. That would require moving electromechanical parts.
You WILL know when it’s overflowing, though.
Or just make some kind of pressure regulating valve. Water level is directly proportional to the water pressure. if your supply hose provides 10cm of water pressure, it will not overflow 30cm container (given the hose pressure is measured on the bottom of the container).
Air in and water flow out is deceptively difficult. I’ve tried a few times over the years but the only reliable thing I’ve found is a glass (inflexible) bottle installed at exactly the level you want it at. Adding hoses never work right, and gaskets, fasteners inevitably leak. This means only small containers, which means frequent replenishment.
Anyone that has ever dabbled in hydroponics, knows of the troll boogers that are left inside the overflow, pumps, plumbing — everything. 3d printed parts by design have layer lines which are crevices for the nasty stuff to hide, get trapped, and flourish. I didn’t watch the entire video, but the plastic used can also be subject to degradation from the chemicals as well: h202 for cleaning, ph buffers, nutrients with proprietary blends, etc. The project is neat, it works, but it is far from a solution. The solution lies in RO/DI floats combined with solenoids and redundant optical overflow sensors like those used in salt water reefs. I have been down the road before with hydroponics. Having maintained a salt water reef for 15 years, its difficult to express the importance of reliability, accuracy, and repeatability. Overflows that fail create water damage, chemical stains, smells, and are very costly. I’ll admit the cost and water volume is usually much smaller hydroponics. I do remember around 6 years ago I had a clogged float that didn’t engage while I was on a weekend vacation. The pump ran dry and burned out. I had alerts in place, but unfortunately I couldn’t buy a pump either locally or online (much like finding a GPU is today) and I lost all of my plants.
Which, with the allowance figured in for failures in the system, one could enact a predisposed system, that is known to work around system fails, if for even only a few days, (ie, a week), … so if the source water component fails to open, replenishing the water supply, should be allowed for such as a bell siphon to act as a high water mark, allowance, much as the drains in a bathroom sink, … or tub, … the water gets to go down a drain, returning to the source tank, … much as any gravity fed system works, … if balanced properly it should allow the source tank, to allow the roots at the lowest level to be wet, and to open a drain after the additional amount of water to find its way back to the tank, by using another bell siphon, in reverse, … as it were, so that the allowance for the 2 distances remain at an either fill me, drain me levels, … much akin to a push me/pull you resource, … therefore no pump necessary, …
Autopot had something like this, but with a two state schmitt trigger design: https://www.hydroponicsolutions.com.au/knowledge-base/smart-valve-secrets I remember they were effective, but pricey.