Newton famously said, “If I see further than others, it is by standing upon the shoulders of giants.” For 3D printing, though, it might be the reverse. If a printer prints larger than others, it is probably using work developed for smaller printers. There are a variety of very large 3D printers out there now and you frequently see claims in the press of “world’s largest 3D printer.” Roboze, for example, makes that claim with a build volume of 1 meter on each axis.
Not to dispute them, but depending on your definitions, there are FDM printers with bigger volume capacity. There are also many other machines claiming roughly the same size, from 3D Platform’s WORKBENCH XTREME to the re:3D Terabot. Of course, all of these come with a large price. But we’ve even seen a homebrew printer with an 800 mm x 500 mm bed. In addition, infinite bed printers are not that uncommon, although they do have some limitations. In particular, they are usually only large on one axis.
Then there are the big industrial machines that print things like houses, bridges, and boats. The University of Maine, for example, has a big printer that has a 100-foot bed and prints about 500 pounds of plastic an hour! All that for only 2.5 million dollars. You can see in the video below that part cooling is done in a rather unique way on that printer.
The Problems
It is easy to think that if you can make a printer that can print the size of a postcard, you should be able to scale it up to the size of a poster board without too much trouble. But that’s not the case. Let’s focus on cartesian-style printers.
You basically have a few choices. You can move the bed around, you can move the print head around, or you can have a combination. For example, many printers move the head in the X and Z direction and then move the bed in the Y direction. Others move the bed in the Z direction and move the head in X and Y. This last scheme is especially popular for core XY mechanics.
So let’s start with the bed. If it moves, a big bed will be heavy. It is also harder to get a nice flat bed as it gets bigger. That’s OK. Just keep the bed still other than in the Z axis, then, right? It also probably requires heating. If you’ve ever had a cheap printer with an underpowered supply, you know that even getting a 150 mm bed hot can be a challenge. Unlike the heat block, you are trying to get a pretty large area that radiates heat to stay warm. When you multiply the size, you multiply that problem. To reduce the load on the power supply, maybe opt for an AC heater.
The bed has to support more weight, too. Granted, for any reasonably sized printer, the extra plastic isn’t likely to be too heavy, but if you were making something giant or printing in a dense material (like concrete) that could be another problem. Besides, we’ve seen a 3D printed part weigh in at over 1,500 pounds already, so think big. Also, if the bed moves in the Z axis, that system has to lift the bigger bed with the heavier heaters onboard.
Speaking of beds, levelling a large bed will be even more touchy than it is today, although auto-leveling can help with that. Another thing that may be worse is warping. Larger parts will have more force as they contract.
Rigidity
A non-moving bed will be easier to brace up, but you still have the mechanism to support the head. Some very small printers use a cantilevered arm to hold the printhead, but even most normal-sized printers support both ends. At some point, the head is going to need larger rails or rods or whatever you are using to support it.
Of course, any alignment issues magnify as you get larger, too. That 0.5 mm deviation at 200 mm will be a lot wider at 1 meter. Errors of any sort will add up, of course. A small wobble on a Z-axis rod or a bit of slip on a belt will add up as travel increases.
Hot End Woes
Assuming you aren’t going to do something strange like break the print bed into zones, you also need to consider the hot end. We already don’t like waiting for 3D prints on our normal printers. A giant printer probably needs a larger nozzle and very high flow rates to increase the print speed. But that takes more temperature. Some of the newer hotends are made for high flow and even heating, but this will be a bigger concern with a very large printer. But consider the University of Maine’s printer. It uses a 10 mm nozzle to produce 12.5 mm lines in 5 mm layers.
Speaking of high flow, if you are really shooting for a large object, there is another concern: material supply. If you are feeding a spool, will it run out? Again, the huge printer takes pellets which makes sense. You just have to keep the hopper full.
One answer, of course, is to use more than one hotend, although that has its own set of problems. We saw a 5-head machine back in 2017.
Design Trades
Making tradeoffs is a fundamental part of engineering. We want safe cars, but an indestructible car would be expensive to buy and operate. So you make tradeoffs. The same goes for the design of a supersized printer.
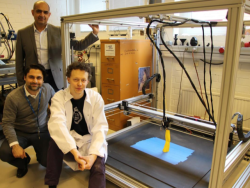
Of course, we’ve already made one fundamental decision that you could revisit: we are using a normal FDM printer. A robot arm or SCARA printer would be another option, although you’d just have a different set of tradeoffs to make. There is no perfect solution. Maybe really large printers will be mobile robots that straddle their ad hoc build plate, rising from the ground or descending from above?
What are your plans for making a giant printer? If you want detailed inspiration, there is this Master’s thesis that details the building of a large printer. The cost was a few thousand dollars, but that included some donated material. Of course, your current printer can print huge objects. Just not all in one go. Whatever you do, be sure to let us know so we can help you share your design.
I made this one in 2016. It was a challenge, but great learning experience.
https://3dprintzothar.blogspot.com/2016/11/big-fn-3d-printer.html
Yay i still use that same old reprap. :) Cant get myself to finish new printer :(
Wow! That is an awesome build.
It’s nice to see someone talking about making 3d printers as opposed to buying!
3DP made a large format leadscrew driven printer which was pretty big…not sure off the top of my head. Used the same PBC leadscrews that Trinitylabs used on the aluminatus.
Also, that titan robotics machine that was used for Autodesk’s project escher used Smoothieboards :) (Shoutout to Clay)
Personally, I think this project was on the right track for how to handle large prints. Need multiple print heads to be able to retain details while still printing fast enough for the layer to get a good bond (without a ton of ambient control).
But yeah…the larger the printer the more issues you will have…and not only that but the bigger your failures can get. It really sucks losing a 48hr print but losing a 2 week print is nearly heartbreaking.
An interesting concept, something akin to a turtle pen plotter, but that extrudes plastic filament.
Although perhaps some sort of drone might be better items with lots of layers. If it had a head that could compensate accurately enough to counter any variance in the flight.
Well the part cooling fans would be nicely sorted out in that drone powered concept… Terribly impractical, hugely inefficient (drone need a great deal of energy just to hover, add in lug a hotend and filament mass around it just gets worse), but a fun idea still… More suited to a cartoon than the real world though…
If you ever really get on to truly giant 3d printers such that flying even remotely makes sense it will be something like tower cranes around the edges with a suspended print head between their cables I would think – scales well, the towers of the crane can always be made bigger during the print for ‘infinite’ Z height too..
I tried this one.
https://hangprinter.org/
The biggest printer about a house of size and cheapest with less than 100€.
But wait for hard work with leveling and adjustment.
You have mentioned them and the ERCF a few times, but still no dedicated Voron article? DIY and open source should be right in your corner
Agreed! We don’t have anyone on staff with a Voron, otherwise, we’d surely have done a writeup.
The biggest problem I see that’s not mentioned here is the print bed itself. Trying to get a large bed to be FLAT is a problem. I’m working on a friend’s CR10 S5 (500×500) and it’s so off it’s not even funny. Added a BLTouch with UBL just to be able to use the printer at all.
>Speaking of beds, levelling a large bed will be even more touchy than it is today, although auto-leveling can help with that.
Missed that somehow lol
I wonder if it is possible to use a granite plate for the print bed, maybe coated so the prints stick better. I’ve seen granite used in ultra precise and small CNC machines or lathes because it doesn’t change size at all due to temperature or other factors and it is possible to get it very precisely made. If you used it as a print bed you would probably have a lot of trouble heating it though and it would be very heavy, but if you can sort out those problem you might have a very very flat print bed that doesn’t change or warp due to temperature. Maybe you could heat it by drilling holes through the middle and sticking heating rods through the middle of the plate, it would still take a long time to heat but the thermal mass of it should keep the temperature quite even and controlled.
Maybe something like garolite.
https://www.matterhackers.com/news/choosing-the-right-3d-print-bed-surface
Granite does move with temp changes, just not a lot. Why do you think precision measuring labs are temp and humidity controlled?
I’m designing a large printer [1], and hopefully I’ve addressed these hurdles so that I have less redesign work and inherent limitations when it is built. I’m designing it such that it’s not out of date 5 years from now, because designing a new printer or upgrading an existing one costs time and money. Unfortunately, the price of the printer I’m working on is still higher than I’d like after combing though the BOM multiple times.
[1]: https://hackaday.io/project/184184