Plastics, by and large, are well-understood materials. Not as strong as most metals, but often much lighter, these man-made polymers have found innumerable applications that have revolutionized the way we live. The properties of plastics have been improved in many ways over the years, with composite materials like fiberglass and carbon fiber proving to have strength and lightness far beyond the simple properties of basic polymers alone.
However, a group of engineers at MIT have been working on a revolutionary type of polymer that promises greater strength then ever before while remaining remarkably light weight. It’s all down to the material’s two-dimensional molecular structure, something once thought to be prohibitively difficult in the world of polymer science.
2D Is Better Than 1D
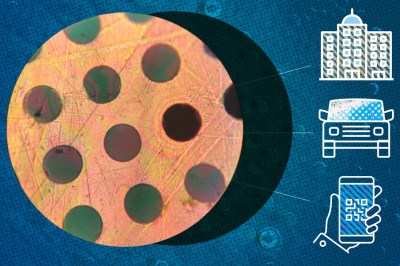
Typically, polymers assemble themselves into long one-dimensional chains, where multiple copies of the same molecular subunit, or monomer, links into a chain many times in what is often referred to as a macromolecule. These long molecules tangle together with themselves and each other in bulk, making up the polymer materials we know and love.
However, the manner in which monomers usually chain together has typically prevented any attempts to produce a polymer structure in two dimensions. If just one monomer attaches to another at the wrong rotation, further monomers will link onto it as well, creating a messy 3D structure instead of a neat and tidy 2D sheet.
With some careful synthesis, it turns out that a two-dimensional molecular polymer structure is indeed possible. As per the research paper published in Nature in February this year, this feat was achieved through the use of melamine molecules as the monomer unit. The working theory is that the use of amide-aromatic interactions in the synthesis steps inhibited the melamine molecules from rotating out-of-plane during the linking phase.
The material self-assembles into 2D sheets in solution, allowing for the creation of thin films of great strength. This structure also has the unique ability of being impermeable to gas molecules. The monomers lock together so closely that there’s simply no way for them to get through.
The resulting material is remarkable in its properties; the two-dimensional polymer was tested to have an astonishing yield strength of 976 MPa, almost four times that of structural steel, despite having a far lower density of just 1/6th as much. Meanwhile, the elastic moduli was measured to be around 30 to 90 GPa, significantly higher than traditional plastics which typically range from 3-5 GPa. This means the material is far stiffer and deforms less in the elastic regime compared to plastics like polycarbonate and nylon. This figure is far closer to that of metals like aluminium, which has an elastic modulus of 69 GPa.
Of course, thus far, only tiny quantities of the 2D polymer have been created in the lab. Testing the material’s mechanical properties had to be done on the nanoscale, using a process called AFM nanoindentation. It allows microscopic samples to be tested using a hard indentation tip on an atomic force microscope to measure the material’s properties.
Importantly, the polymer as synthesized is mechanically and chemically stable. The paper’s authors suggest it has great potential for use in composite materials as well as for use as a lightweight but strong protective coating. It’s unclear at this stage how such a polymer could be produced at the macro scale, and it will likely be some time before this material is on sale in large sheets at your local plastic distributor. However, it shows that the world of science still has amazing secrets to be uncovered that could bring us new and wonderful materials beyond our wildest dreams!
Plastics.
https://www.youtube.com/watch?v=dS-BTaysDGU
Nice weather for ducks!
Word.
One word.
Future.
Oceans
Whoosh!
Are there any toxic side effects to your reasearch for polymers leach isocyanate
976MPa is very impressive if it is true. However inferring yield strength from microhardness is far from an exact science, and hardness is notoriously inaccurate on very thin samples.
Of course it’s also anisotropic, so it doesn’t directly compare to materials like aluminum which is generally the same in all directions.
Agreed, but that anisotropic quality may also be a benefit if used properly. I could see use as a laminate structure, or interior coating since its impermeable to gasses, on something like a tank were hoop stress is important. Use a base material to cast a tank in something cheap and/or easy to work with to give the primary structure and then use this to gain additional properties in lieu of more exotic (or just heavier for aerospace) materials, or just to use less of the same base material.
This could also be similar to graphene/carbon nanotubes though where we end up only seeing it used for a long while in minimal/special applications where mass quantities of high quality material are not necessary.
I mean, the same strength is always better isotropic than anisotropic, all else equal. The reason why anisotropic materials are used so often is because all else isn’t equal.
An AFM (which I have used many times) is mainly used to brush over the surface of a material to make a 3D image. Put enough force on it to test for hardness, modulus, etc and you’ll break the tip off. Nano indentation testing is a separate test using a calibrated diamond which is driven into the surface of the material. You measure the force used, and the hardness, etc. is a calculated result depending on the diamond’s calibration. I had to calibrate a diamond tip once, when the numbers for that particular tip were from another diamond. Took way longer than I wanted to spend, but it was in a customer’s device and overnight shipping to this place was unheard of, let alone that it was in Cairo. Thin films such as this are done differently. You’ll see a change when the tip hits the surface and another when it breaks through to the supporting material. You have to extract data points where the diamond tip is only on the film itself, and your supporting material is best when it is hard and yet different than the material you want to test. The hard support material keeps you from getting false readings because the whole thing is flexing.
I’m imagining super-light tanks for holding gasses at high pressures.
Time for vacuum airships, baybee
Hilariously, vacuum airships might have problems with helium leaking into them if used in the upper atmosphere for years.
Might be a problem since it seems to be full of holes.
The actual synthesised film (purplish red in picture) is grown in the holes of the support material (gold in picture). Hence the support material’s Hole 1 has an imperfection in the middle on the second picture, while Hole 2 of support material has good grown film inside.
Maybe the holes are the secret of its strength. (“toilet paper never rips at perforated lines” joke )
I would not be surprised if that can be proved or exploited for certain materials. Steels that can be hardened or toughened by peening or forging might gain strength as a sheet material when punched in the right way, kinda losing bulk but gaining toughened rings. I would imagine some fibrous paper board products where a punching operation kinda bonds layers of fibres in a ring around the hole might have similar effects. In either case, it might be that the punch needs to be a certain state of “blunt” such that crushing more than cutting action occurs.
I’m imagining super light tanks and armored personnel carriers. This would have numerous military uses, including chemical warfare suits.
This has potential as an alternative to graphene as a filler material, or perhaps even an alternative to aramid as a fiber. But I can’t imagine it being cheaper to manufacture than either of those.
….Now they know how many holes it takes to fill The Albert Hall. More plastic…great…not.
I’d like to see a comparison vs carbon fiber.
I wonder if this would make a good dielectric?