[FloweringElbow] aka [Bongo] on YouTube is certainly having a go at this, and we reckon he’s onto a winner! This epic flatbed CNC build (video, embedded below) starts with some second hand structural I-beam, with welded-on I-beam legs, DIY cast aluminium side plates and plenty of concrete to give a strong and importantly, heavy structure.
The ideal machine is as rigid as possible, and heavy, to dampen out vibrations caused by high-feed speed cutting, or the forces due to cutting harder materials, so bigger really is better. For construction of the frame, steel is pretty strong, and the mass of the structure gives it additional damping, but triangulation was needed to counteract additional twisting. He stitch-welded the pre-heated frame in inch-long sections to limit the heat transferred into the metal, minimizing the subsequent warpage. [Bongo] used hacky Vibratory stress relief (VSR) constructed from a washing machine motor and eccentric weight, clamped to the frame, with feedback from a mobile phone app to find the resonant frequencies. There are other videos on the channel devoted to that topic of such stress relief techniques.
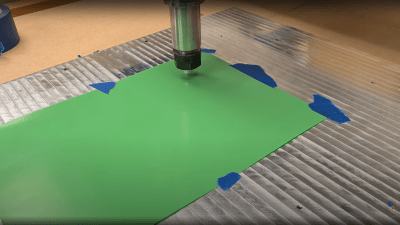
When it came time for adding even more mass, a priming coat was made from a mixture of bonding epoxy and sharp grit, intended for non-slip flooring. The concrete mix used Portland cement, pozzolan (Silica fume) polycarboxylate superplasticiser and 1/2″ glass fiber threads. A second mix added crushed stone for additional mass. A neat trick was to make a handheld vibratory compactor from a plate welded onto the end of old drill bit, mounted in an SDS hammer drill.
Once the frame was flipped the right way up (collapsing the overloaded hoist in the process) it was necessary to level the top surface to accept the linear rails. This was done using a super runny, self-leveling epoxy, and checked by flowing water over it. Once the epoxy surfaces were adequately flat and coplanar (and much scraping later) the linear rails were attached, after creating some epoxy shoulders for them to butt up against. End plates to attach the Y axis lead screws, were added by bolting into the frame with a grit-loaded epoxy bond in between.
The gantry design was skipped for this video (but you can see that here) and once mounted a quick test showed the machine was viable. One curious task was making their own cable-chain from ply, on the machine itself, rather than buying something expensive off-the-peg. Why not? Once the machine was working well enough to mill a flat sheet of steel to nice reflective surface, it was used to mount a DIY drag-knife to cut out shapes in some vinyl, so it has the precision. We did like seeing an XBox controller used to manually jog the machine around! So much to see in this build and other related videos, we reckon this channel is one to watch!
We’ve featured CNC builds many a time, there’s a build whatever your needs and budget, but here’s a good starting point to build a machine, just good enough to build the tools you need. If you don’t happen to have a source of structural I-beam to hand, you can do something quite capable with wood, and if you fancy a go at 3D printing a knee mill, we’ve got that covered as well.
this is epic,kudos for bringing ancient skills forward and melding
them with latest bits and bobs,phones and vinyl.
surface plates made 400 years ago have been checked for
flatness and are +- less than a millionth of an inch,very simple
process,use three castings,and scrape flat,compare two by
putting a marking compound between and scrape the spots that
are high,keep randomly swapping plates and scraping till nothing
more can be done,similar processes are used to hand make large
high quality lenses and mirrors
The surface plate was invented in the 1800s and the highest grade is +- 40 millionths (more for larger plates). Most have twice or four times that grade’s tolerance.
“keep randomly swapping plates”
Not randomly / A->B , B->C , A–>C
Three plate method I believe it is called.
For best results, rotate one of plates 90*C after each loop, otherwise they can still have some slight saddle shape.
I started watching the video to answer the question “Can it handle a 4×8 sheet of plywood?”
He answered the question immediately, and I stayed to watch more.
^This
If all youtubers made this the world would be better and people will actually watch more of their videos. Asking a question in a video title and answering it only sometime randomly in a 10+minutes video just is innervating and will maker the viewer skip into the video (or skip the video altogether for another one) and will prevent the uploader to gather monetization since the viewer haven’t seen the whole video.
TL;DR for youtubers : answer core questions and deliver interesting tidbits at the very beginning of your video and elaborate on the details after if you want but don’t hide all of those into the video.
It’s so previce in fact that it’s actually just a knee
I’ve watched this machine grow for some time, and it is great to see how far it has come.
This one is certainly not a build that any person would tackle. Most sane people won’t go to the extent of casting metal, but it certainly a great project.
There is a large community of hobby machinists who absolutely have done large metal castings as the base for Gingery lathes and other scratch-built machine tools.
Have you ever met a sane machinist?
Its like pure theoretical mathematics, the sort of thing you have to be a little warped compared to the boring old normal folk to enjoy.
All the journey to an end result being largely the challenge, the fun, and the point… Not the most normal thing in the world these days, and as sanity really can’t be defined except as a relation to the boring old ‘normal’ folk with their rubbish TV…
I have access to a blast furnace for cast iron in Pittsburgh where I live. At some point going forward I will cast small Machinery frames for some custom machines that I cannot buy. Once you learn to cast metal and make sand molds it’s not really that much of a stretch to do basic machine frames you just need a team of people to help you pour when you have a real blast furnace
Hi all, Bongo here (the machine builder). Just wanted to say nice write up Dave, really appreciate that, and thanks to everyone taking the time to watch the video – it’s really pleasing to see people get so much out of it.
@elmesito – so true, most sane people wouldn’t :)
Great work. Wish I had your time or skills. Was happy to see that the vacuum attachment finally got added. Watching him manually follow along was having the part of my brain that does such things screaming “build a vacuum attachment so you don’t have to follow that spindle with your shop vac.”
This is after hours of following the spindle on my 3040 CNC with a shop vac. Still need to finish my attachment.
The reason for the more commonly used extruded aluminum is lack of DIY resources.
DIY resources:
Once-in-a-lifetime ebay deal.
Well equipt work shop.
Enough money to buy ‘cheap’ 10 foot long lead-screws, milling head, etc.
Internet job to pay the bills.
Assistant that supports and helps you with your interests.
Enough free time to just buy the thing you’re making.