The first modern wind turbines designed for bulk electricity generation came online gradually throughout the 80s and early 90s. By today’s standards these turbines are barely recognizable. They were small, had low power ratings often in the range of tens to hundreds of kilowatts, and had tiny blades that had to rotate extremely quickly.
When comparing one of these tiny machines next to a modern turbine with a power rating of 10 or more megawatts with blades with lengths on the order of a hundred meters, one might wonder if there is anything in common at all. In fact, plenty of turbines across the decades share fundamental similarities including a three-blade design, a fairly simple gearbox, and a single electric generator. While more modern turbines are increasingly using direct-drive systems that eliminate the need for a gearbox and the maintenance associated with them, in the early 2000s an American wind turbine manufacturer named Clipper Windpower went in the opposite direction, manufacturing wind turbines with an elaborate, expensive, and heavy gearbox that supported four generators in each turbine. This ended up sealing the company’s fate only a few years after the turbines were delivered to wind farms.
Some history: the largest terrestrial wind turbines were approaching the neighborhood of 2 megawatts, but some manufacturers were getting to these milestones essentially by slapping on larger blades and generators to existing designs rather than re-designing their turbines from the ground up to host these larger components. This was leading to diminishing returns, as well as an increased amount of mechanical issues in the turbines themselves, and it was only a matter of time before the existing designs wouldn’t support this trend further. Besides increased weight and other mechanical stresses on the structure itself, another major concern was finding (and paying for) cranes with enough capacity to hoist these larger components to ever-increasing heights, especially in the remote locations that wind farms are typically located. And cranes aren’t needed just for construction; they are also used whenever a large component like a generator or blade needs to be repaired or replaced.
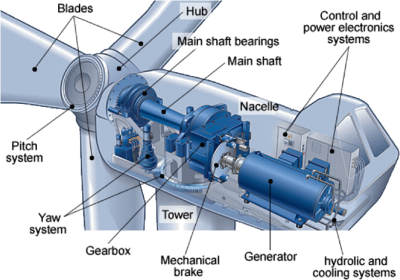
Looking at the problems with wind turbines in this era, Clipper Windpower arrived on the scene with a completely novel turbine layout which they thought would solve these issues. The main design difference was the use of four generators working in tandem rather than a single large generator. Their design was known as the Liberty turbine, producing 2.5 megawatts of power at maximum output.
In 2007, it was the largest wind turbine available in the United States. The design meant that a generator failure wouldn’t completely take a turbine offline, as they could run with less than four generators, and the generators were small enough on their own to be hoisted up and down easily by the turbine’s 2-ton crane. Plenty of other turbines have cranes for hoisting tools and smaller components, but unlike the Clipper Liberty turbine, in a standard single-generator layout the replacement of a generator would generally mean contracting out a much larger crane.
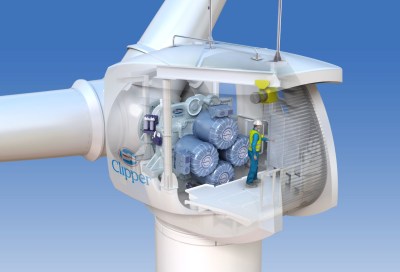
In theory, there were plenty of advantages to this design besides the physical size of the generators. The distributed loads on the gearbox meant less mechanical stresses on the turbine’s physical structure. Generators with different power ratings could, in theory, be used as well, allowing the turbine to produce energy across a wider range of wind conditions than one with a single generator. Besides the technical aspects of the turbine itself, Clipper hoped to innovate in other ways as well. They attempted to set up temporary turbine manufacturing facilities at the planned sites of wind farms, meaning virtually no transportation costs for high-dollar items like turbine blades.
What Could Possibly Go Wrong?
But problems quickly appeared with turbines shortly after being placed in service, the most devastating of which surrounded the enormously complex gearbox. To explain this, we need to first look at why a gearbox is included in a wind turbine at all. For the most part, the synchronous electrical generators often used in older wind turbines need to operate near a specific rotational speed to send energy to the electrical grid, often 3600 rpm for a 2-pole generator or 1800 rpm for a four-pole generator, in places with a 60 Hz power grid. This is orders of magnitude faster than the rotational speed of the wind turbine’s blades and hub assembly, also known as a rotor, which is somewhere in the neighborhood of 10 rpm to 30 rpm. Most turbines of this era, including Clipper Liberty turbines, relied on a gearbox to couple the rotor to the generator even if there was only a single generator in the turbine.
The difficulty of designing and manufacturing a reliable gearbox that needed to accommodate four generators was not something Clipper was entirely prepared for, though. The first issues that began cropping up involved timing issues with the gear sets inside the gearbox (followed shortly by systemic blade problems, but that’s a little outside this scope). Specific details are sparse, but similar to the timing mechanisms for the valve trains in internal combustion engines, the gears inside the Clipper gearbox needed to be in near-perfect synchronization with each other in order to drive the generators properly. The gears, produced by a third party, weren’t manufactured to the correct tolerances so after only months of energy production, the gears were beginning to fail.
Since the Liberty turbine was produced with the intention of reducing the impact of generator failures by placing all of the onus on a complex gearbox, the fact that these turbines’ gearboxes began rapidly failing in the late 2000s was a major setback. Not only does a failed gearbox take the turbine out of service, but now it was possible that a heavy crane would be needed to replace it, if a replacement from the fledgling wind turbine manufacturer was available at all. Clipper was quickly inundated with warranty claims for their gearboxes, which even more rapidly led to the financial failure of the company. The timing of this was unfortunate as well, as warranty claims for the failed gearboxes correlated with the 2008 financial crisis. Clipper filed for bankruptcy in 2012 amid much investor consternation, as many investors in the company ended up being the wind farms who had originally purchased the turbines.
Feature Creep
Here in the present, it is becoming rare to see an original Clipper turbine still in operation. To keep these wind farms in service and fulfilling their power purchase agreements, a much easier option is to simply replace all the Clipper components “up tower”, such as the entire nacelle, rotor, and/or blades, with those from a competitor, leaving almost no original components besides the tower. Unfortunately, unlike other single-generator turbines which use more standardized parts and can therefore survive capitalistic machinations such as bankruptcies and buyouts more readily by sourcing parts from other manufacturers, Clipper built themselves into a prison of their own making. Originally hailed as industry leaders, the complexity of their drivetrain and its single point of failure ended up being their own undoing.
While plenty might look to those behind the company, this isn’t a story of an out-of-touch investor or venture capital firm attempting to “disrupt” an industry they knew nothing about, like certain other billionaires in the news lately who have accidentally bought companies they don’t fundamentally understand. Clipper’s founder was originally the founder of Zond, one of the largest and most successful wind turbine producers of the 80s and 90s. Coincidentally, Zond was acquired by Enron in 1997, which was then acquired by General Electric after Enron suffered slight financial difficulties, making GE one of the major competitors of Clipper during the mid-00s. Instead, this is more of a story of feature creep on a massive scale, and of going out of your way to solve a problem that doesn’t really exist, and introducing much more serious problems as a result.
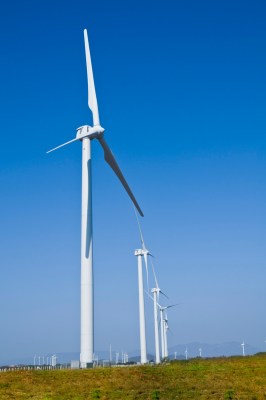
Indeed, what really happened to Clipper, which we can only see now with the benefit of hindsight, was that the designers made some questionable choices when first conceiving these turbines. For one, designing a completely new turbine layout was sure to be rife with unforeseen problems. For another, the problems they were attempting to solve wouldn’t end up becoming the industry bottlenecks that Clipper predicted. More cranes and crane operators were found as the industry expanded in megawatt ratings, larger component sizes, heights, and weights, and in the sheer numbers needed to support a rapidly increasing number of wind farms.
Additionally, most modern large-scale wind farms are built in places with fairly predictable wind characteristics, so multiple generators with different power curves didn’t turn out to have the benefit it was thought to. And generator failures turned out to not have the devastating impacts that Clipper forecasted, either. There are some theoretical benefits to multiple-generator layouts, but replacing a single point of failure in a relatively simple electrical machine, the generator, with a single point of failure in an enormously complicated mechanical device, the gearbox, turned out to create many more problems than it ultimately solved.
While there is still a company called Clipper today, with a shop in Iowa that repairs gearboxes and provides other wind-related services, it has been sold off twice since its bankruptcy and exists as a shell of its former self. At this point the Clipper Liberty turbine is nearing 20 years old, and with wind farms looking to repower their turbines they often turn to technologies that are more proven and with higher megawatt ratings rather than repairing and maintaining this niche turbine. Clipper’s story is not an altogether uncommon story either, where a company is hyped to solve a problem they claim is a major issue, only for their product to lead to disappointment when finally released. Other examples include the Segway, Google Glass, or the attempt to bring 3D televisions to mass market. These products and the Clipper Liberty turbine are case studies in the importance of understanding consumer needs, market demand, and addressing genuine pain points when developing innovative technologies. Failing to understand these ideas can result in disastrous consequences.
>are case studies in the importance of understanding consumer needs, market demand, and addressing genuine pain points when developing innovative technologies. Failing to understand these ideas can result in disastrous consequences.
I’d agree but also add it is inevitable some will fail even if they get nothing wrong at all. All it takes is for something to shift the economic landscape or some surprising or just surprisingly rapid technology developments to change everything. Assume cheap ‘room temperature’ superconductor are found in 3 years time for instance.
Wind power had been a growth sector, but not exactly rocketing away. So I actually think Clipper had a very solid idea in making each turbine able to mostly be its own maintenance crane, and produced some rather performant wind turbines for their era – if wind didn’t grow as quickly as it ended up doing finding big enough cranes out in the middle of every windy nowhere you did have a turbine wouldn’t be happening quickly. Which would then make a turbine that can mostly service itself about the only practical turbine to install, as you can’t rely on infrastructure that might be down for maintenance for a few weeks just waiting on the crane to arrive…
Much as engineers hate to admit it, a good marketing department, one that can analyse the market and predict important and relevant aspects of it, is essential.
and a quality assurance department.. I mean, “weren’t manufactured to the correct tolerances” didn’t they check? And even if it DID match tolerances, surely they would have subjected it to extensive testing…
Wish I had first hand experience with such a marketing department…. They haven’t provided any of my products with meaningful input…
If your saleweasels can do market analysis they are in the wrong department.
The skills are unrelated.
I retrofit Clippers in Utah last year, the blade cracking issues have always been cited as a reason Clipper company failed. IIRC the 4 generators provide DC to a pair of converters at the bottom of the tower, which convert to 690V AC.
Hi Cory – We are now recycling failed/ decommissioned Clipper generators for recycling of rare earth magnets. Do you have any that you’re willing to sell? We are creating a circular supply chain for these critical elements through our rare earth recovery proprietary process.
It’s interesting how the generator speed scales with size. A 100 MW hydroelectric generator turns at 72 rpm and uses no gearbox. Of course, it can afford to have 100 poles, be 10 meters in diameter and weigh 500 tons, because it’s generally supported on bedrock.
Is doesn’t use a gearbox because power in is a constant. Wind not so much. I miss Zond, wonder how Mr D and Ken are doing
Can you elaborate a bit on that? Because the gear ratio doesn’t change to match wind power available (the blade pitch does): the transmission just increases the shaft speed to that required by the relatively small, light generator.
They change blade pitch to control rotation speed. If the wind speed is too low or too high for the pitch change to be able to make it turn at the right speed, a brake is applied to stop rotation, usually with the blades fully feathered or edge on to the wind.
Input power is not a constant – it’s directly related to wind speed. Turbine speed (and generator speed) can be made constant by feathering the blades.
It’s occurred to me that a less complex system would use an alternator with field control and rectifier to provide DC power to the windfarm grid. Field control could be adjusted for maximum output (similar to solar panel MPPT), while blade feathering would control turbine speed for safety and for maximum mechanical power to the alternator.
The turbine has an optimum point at a certain tip speed ratio, which is basically the ratio between the wind speed and the RPM of the turbine. By making the turbine speed constant, you cause the turbine efficiency to sweep from zero to max to zero as the wind speed changes.
I worked on clippers last year. IIRC the generators feed DC to converters at the bottom of the tower. The converters convert the DC to 690VAC.
Roesel generator perhaps?
https://cordis.europa.eu/project/id/JOUR0086
This was one of the better articles I’ve read on this site.
More like this!
clipper wind turbines multi-output gearbox design was not that novelle at the time. It was the evolution of the kenetech KVS33 wind turbine circa mid 90’s. it was a 1 to 2 design vs the 1 to 4 design of the clipper. Additionky gearbox failures were the demise of several wind turbine manufactures in the 90’s to early 2000’s regardless of design.
Good article. Take it from an insider in renewable energy NGOs: these kinds of shenanigans are endemic to the whole sector. It’s a huge problem. It’s why renewables are a laughingstock and people have a point when they shun them as unfeasible.
One reason I’ve noticed is that we get way too much participation from the tech sector, whose attitude of “minimum viable product” is shameful and should be basically treated as fraud. This is why solar panels and wind installations all wear out in five years. Do you think other civil engineers have this attitude? The wastefulness of the infrastructure lasting only for the blink of an eye before falling to pieces and tumbling down completely offsets any sort of efficiency gain or renewable nature, and utterly discredits claims of being interested in environmentalism. You look like hucksters, wasteful charlatans, people trying to squeeze a quick buck out of people’s fears. And if you engineer like this, that is exactly what you are.
What the hell kind of sense does it make to run a bunch of tiny rinky-dink generators off a complicated gearbox instead of building a large one to proper specs and having efficiency gains associated with it being monolithic? Who looked at that gearbox and thought it would stand up under load long-term? This reminds me of that motorcycle somebody built by putting 20 leaf-blower engines on a single gearbox to make all of them drive the rear wheel. Ridiculous.
If people really think their biosphere is at stake, they should take these slapdash “move fast and break things” silicon valley engineers and put them in the unemployment line where they belong. The engineers who actually built national infrastructure would never allow this. Think the guys who built Hoover dam would design this? Hell no.
Never climbed a tower then to replace anything? 300 ft up makes life exciting when lifting a couple ton. Exciting even for small stuff
I think the problem with the “minimum viable product” idea is that too many people pay so much attention to the “minimum” part that they miss the “viable”. I’m looking at marketing an item in a niche where there’s already a bunch of shoddy products – and the buyers know it. So to bring a product that’s truly viable, I need to come in with something that establishes “I know how to build these with a level of quality, features, and craftsmanship that the competition doesn’t offer.” Anything less, and the product would be too much minimum and not enough viable.
“This is why solar panels and wind installations all wear out in five years.”
Citation, please. Projects may have challenges, but you are making it sound like plants simply stop working around 5 years in, which simply isn’t true. Not the clearest example, but there are many 5+ year old solar sites included in this study: https://doi.org/10.1002/pip.3566.
20years minimum for solar as reported in todays press
Technical lifespan is different from practical lifespan. Usually the practical lifespan of a wind turbine, or in some cases solar panels, is defined by the length of the subsidy period.
When the owner of a wind turbine stops getting tax breaks, feed-in tariffs and other price guarantees, they face the problem of having to sell power well below the average market rate, which is hardly profitable.
Sure, the producer has made the investment back many times over already through all the incentives, but they no longer make as much profit trying to extract the last bits of energy out of the turbine. The owner has also deferred all except the absolutely necessary maintenance to keep it running, which means there is a huge repair bill looming on the horizon should they wish to actually reach the full technical lifespan.
So, most owners simply choose to let the turbines break, tear them down and replace them with new, bigger turbines, preferably with new subsidies and price guarantees that last for another 12 years (depending on the region).
For example, the US PTC is valid for 10 years after the equipment is placed in service. Coincidentally, the average age of a wind turbine in the US is just 7 years. Whenever one breaks, it is replaced to renew the PTC and various other state level subsidies instead.
And this is reasonable and responsible, when we are at a point of rapid improvement on the technology curve.
Long life is desirable once performance has stabilised (for example my wood fire is ~30years old, and there has been little improvement recently)
It is not an advantage when the state of the art is improving rapidly, and also when the actual field problems (like gearboxes) have yet to be discovered. In that case a minimum economic life will probably be best.
Hell of a lot of unsubstantiated claims in that comment there fella, care to cite any actual facts?
[upvote]
5 years? Rinky dink?
Wind plants are 20 year service life. Solar is 20-30.
And bear in mind that solar degrades nice and slow, 0.5%-1% per year. So the 20 year service life is really just the time until 70%-80% performance. If you’re not space-constrained, you’re still pulling in energy.
https://www.semprius.com/how-long-do-wind-turbines-last/
and check out Will’s awesome link for solar.
20 year life _with_ service, maybe. And lots of it.
I believe solar is maybe better but I’ve heard some stories, replacing the same component in the same turbine every year, random frequent blow ups etc.
Quality German engineering.
Have you seen any German cars less than 20 years old?
Hot garbage! Worst of class. Make (Italian/British/Moroccan/American) cars look good.
I blame China. 40% of German cars are sold to China, where they are simply status symbols. Germany has chased that market, now their chumps are paying. No lube in the oil change finance office.
Simple rule: Never buy a water cooled German car.
Here’s some more good data on wind: https://emp.lbl.gov/wind-technologies-market-report. And solar: https://emp.lbl.gov/publications/plant-level-performance-and (concludes more like 1.2% degradation, but that includes potentially recoverable losses like unwashed soiling).
Several commenters here are acting like wind and solar performance trends are allegedly bad but ultimately unknowable, and anyone claiming wind and solar generally work should be doubted.
*But* most large generation facilities in the US have to report monthly energy to EIA and/or FERC. So, it takes digging, but anyone can see for themselves (or let LBNL do the hard work and read their summaries instead).
Wind and solar have had some challenges with meeting all performance and financial assumptions all the time, but in general, they work. And they work pretty well.
“clipper wind turbines high lonesome nm”.
https://www.google.com/search?q=clipper+wind+turbines+high+lonesome+nm&oq=clipper+wind+turbines+high+lonesome+&aqs=chrome.2.69i57j33i160l4j33i299.25343j0j7&sourceid=chrome&ie=UTF-8
c/c++ wind turbine software hackable?
Phoenix and Cristie seeks c/c++ programmers?
I had several deep discussions about the Clipper Liberty gearbox with the man who designed it. He is a legend in the industry. Call him X.
The author of this article does not explain why the gearbox was a failure.
He is not wrong about it in principle. It was a timing problem. But if he has knowledge of the details, he does not present them.
“Design” has two meanings here. It can mean inventing the device. It can also mean drawing the parts for manufacture using one’s expertise in that discipline so that the thing will work as intended. If it would have worked.
I doubt that most inventors can produce detailed drawings for the machinists who will make the parts and put the invention together. The inventor of this gearbox certainly could not.
X did not invent this gearbox. He did not even like it. But he was one of the foremost experts in the field, so the inventor hired him to design the parts so that they would work together as the inventor intended.
X told the inventor what was wrong with the idea. The inventor told him to shut up and draw.
I feel a rant coming on.
I for one would enjoy hearing more about this. Rant away.
Thanks for the invitation. I am glad to oblige.
First, thanks to Ostracus for the reference to the Roesel generator. I had never heard of it in my forty years of looking into these things. I have learned that the principle of this generator works in a motor, which Roesel also patented, and that Single Phase Power Solutions is using it.
So far as I have been able to determine, the Roesel generator has not become important because it can’t tolerate a speed range of more than 2:1. I am still learning the details. Joseph F. Roesel, Jr. died in 2013 at the age of eighty.
The main point of this rant is that Bryan Cockfield has used the Clipper Liberty gearbox fiasco to diss wind turbine gearboxes in general and to promote the folly of direct drive. “Just get rid of the gearbox and everything will be fine”, says the direct drive cult.
It would take too long to explain here everything that is wrong with direct drive. The primary fault is that it will always require an inverter. Wind power can never reach its full potential if the industry continues to rely on those Rube Goldberg contraptions. I could rant on that subject alone.
The only way to eliminate the inverter in a wind turbine is with a special gearbox. That is, provided that the Roesel generator is not suitable for the job. I am looking into it.
DeWind proved that it is possible. See their D8.2 and D9.2 turbines. But Daewoo bought the company and ran it into the ground. It is a terrible waste of the most important development ever in wind power.
If wind power is on a dead end road because the industry is prejudiced against gearboxes, then I must resist any attempt to reinforce that prejudice, such as this article by Bryan Cockfield. I know he meant well, but he doesn’t know enough about the subject to write about it.
At first. the Clipper Liberty gearbox looked very good to NREL and some other big outfits. That is why Clipper become a sensation with investors and managed to sell a lot of turbines before the trouble showed up.
What was wrong with that gearbox? Why didn’t anyone see the problem until these gearboxes started to corn cob by the hundreds after the turbines went into operation? If Bryan Cockfield knows, he has not explained it. His purpose in writing this article was different, as I have stated.
Yes, the problem had to do with the timing of the gears. This is a complex subject, but for instance, the gearbox did not use the NASA gear timing method. Even if it had, it would have been a failure. The NASA technique is not suited for wind turbines, and it is not suited for much else so far as I can tell. I don’t know of any gearbox manufacturer that uses it.
In a split power path gearbox like the Clipper Liberty units, there must be a way to equalize the loads among the power branches exactly, at all times, under all conditions. That is where the inventor of this gearbox failed. He did not have a reliable way to equalize the loads. He tried, but his method was worthless. The details are too many for this comment.
If he had succeeded, so would have the Clipper Liberty wind turbine. It is fine to use split power path gearboxes and multiple generators, and it is possible to design reliable gearboxes for wind turbines, if you know what you are doing.
And it is possible to design a gearbox to get rid of the inverter [DeWind].
Here is sufficient proof that the direct drive wind turbine is a foolish idea. The biggest wind turbines today use hybrid drive. That is, a medium speed GEARBOX driving a medium speed generator. This makes the assembly as small and light as possible, and extremely rigid so that it can resist external forces, while powerful enough to generate as many megawatts as the blades can deliver. See the latest wind turbine from Ming Yang, which has been using hybrid drive for a long time:
https://www.offshorewind.biz/2023/07/18/mingyang-commissions-16-mw-offshore-wind-turbine-with-260-metre-rotor-diameter-in-china/
No need for any thousand-ton direct drive generators. They were never needed.
If the US wind turbine industry had had the good sense to develop the DeWind concept, they would be leading the pack, not the Chinese. The future of wind power would have been secure. Anyone who still promotes direct drive is way behind the times.
I learned in the marine industry that if a ship’s reduction gear [GEARBOX] is treated with respect, it will outlast three ships. Salties, anyway, the hulls of which last about twenty-five years. There are hundred-year-old ships still operating on the Great Lakes, that is, in freshwater. I suspect that their reduction gears have never required a serious overhaul. Although there is no reduction gear in the old up-and-downers.
Gearboxes can be the most reliable equipment ever designed. I feel a rant coming on whenever anyone disputes this fact.
I’ll dispute that, if only to hear rant part 2! :)
I’d take an inverter over a gearbox any day, and that’s even with my background (and inherent preference for) mechanical engineering. Power electronics may have historically been a barrier for direct drive machines and more complex control strategies, but that’s fallen away in the last decade or so from what I’ve seen.
Same here, and for same reason. I also second the inverter, ofc you need a good one, not a sheit Siemens or so. One that actually works.
And either way, gears or not, odds are an inverter would be needed either way to be able to match and stabilize the grid.
Although with good control and a synchronous generator that might be possible without inverter?
Always cited as a weak point for wind, either way.
According to conventional wisdom, Hybrid Drive is the best technology for wind turbines. Academic studies show it, and Ming Yang and other manufacturers believe it.
But Hybrid Drive requires both a gearbox and an inverter. Therefore, your inclination to choose an inverter instead of a gearbox is moot. It would make no sense unless you include direct drive among the possible configurations , and Hybrid Drive is eliminating that technology.
That leaves only geared turbines, and all geared turbines require an inverter. True, it is possible to design a hydraulic drive train for wind turbines that uses no gearbox or inverter. Look up the Sea Angel. Never heard of it? You will learn why if you search long enough.
The current technology for geared turbines, with its requirement for inverters, is the result of conventional wisdom. That Overton Window is fixed. Talk about a rut.
I am gearing up for a rant on inverters.
Seconding that dispute just to get a rant part 2!
Though I do agree the electronic side has become it would seem perfectly capable.
So really like many things it seems to be down to picking the engineering compromises that suit your needs best.
Gearbox can last ages with a little care, especially fixed ratio boxes. They probably work out much cheaper in the rarer raw materials than pushing everything onto the electrical side, so probably cheaper in money to, at least for similar and suitably large scale production. But at the same time they do require that little extra care and the extra mechanical friction created probably impacts the low windspeed performance meaningfully. And the cost to fully develop the product and its production line for a more mechanical system is probably much higher as most electronics is taking off the shelf electronic Lego to build what you need with very short turn around between the prototype iterations where the mechanical system is almost always rather more job specific and probably needs even in the affordable CNC age weeks more time between each iteration.
Sea Angel windmill
https://www.windpowerengineering.com/hello-seaangel-hydraulic-drive-train-could-provide-7-mw-offshore-turbine/
Here is a video that shows the complexity of the Sea Angel wind turbine:
https://deepresource.wordpress.com/2017/04/23/mitsubishu-hydraulic-driven-7mw-offshore-wind-turbine/
I believe it shows why no one ever built another one. Assuming that they would have worked as intended, even in serial production they would have cost too much. The inventors did good by eliminating the gearbox and inverter. But it is foolish to replace them with an even more complicated and expensive technology.
To continue my comments about inverters and gearboxes in wind turbines, I will make a new post.
Google Glass is a terrible example. It never came to market. It saw limited beta testing. The first gen should never have had a camera. It is textbook case of killing a new idea.
Central electrical generating stations produce power of the highest possible quality. They have complete control of the power they generate, and how it interacts with the electrical grid. If there is a disturbance on the grid, the central stations deal with it. They form the grid, maintain it, and produce the cleanest possible, pure sine wave, constant frequency power.
Suppose you put one of those central stations on top of a tower and used the wind for the power input. That is what DeWind did. The only difference, aside from the power rating and the source of the shaft power, is that a central station changes the power input to the generator to meet the power demand. A DeWind turbine changes the power output to equal the power input.
Otherwise, on the electrical side, the systems are identical in their design and operation. That is why the Dewind turbine produces electrical power equal to that of a central station, and can maintain the grid just as a central station does.
Unlike conventional wind turbines, central stations do not use inverters. Neither does a DeWind turbine. DeWind eliminated the inverter by using a special gearbox to convert variable rotor speed to constant generator speed. Constant generator speed is the basic requirement in a central power station, and DeWind achieves it in a different way.
If anyone is still interested, I will explain why the future of wind power requires the elimination of the inverter. That would make all current wind turbines obsolete. Maybe we could convert many of them to the DeWind concept, but we ought to stop producing them. It would save a lot of money in the long run.
The future of wind power requires the addition of battery buffers, which require an inverter.
The reason why central stations can maintain the grid is because they can adjust their power output to need. No fancy gearbox in a wind turbine can do that – they can’t change how windy it is. To provide true “central station quality” power that you can use for frequency regulation, you need batteries.
Besides, AC synchronous generators have a tendency to fall out of sync in gusty winds and drop offline for safety. Even if the gearbox is adjusting for turbine speed and torque in real time, rapid transients in the power input cause the generator to run up and down against the grid load, and this sets up oscillations in the RPM of the generator. If it exceeds the maximum allowable frequency slip, the generator has to disconnect from the grid or risk mechanical failure. This is another reason why manufacturers have gone for inverter operation, since they don’t have to keep the generator synchronous to the grid – it can run up and down to absorb transient wind conditions.
Note also that an AC generator isn’t really a constant speed device. It runs slightly faster than the grid to push power into the AC grid, and if it drops below the synchronous speed, it turns into a motor and consumes power. This is called slip, and it’s usually around 2-5% of the synchronous frequency. When the generator exceeds the maximum amount of slip it can handle, the load-torque curve becomes inverted and the generator speed surges, and bad things happen.
It is difficult now to find information about the DeWind D8.2 and D9.2 turbines. Maybe that is why Dude claims that they couldn’t work as described. If anyone wants to investigate, look for Voith WinDrive. This CVT is what makes these DeWind turbines unique. It is what allows them to operate in the same way as a central power station, even with varying wind speed. Dude should look into the matter.
Dude is also mistaken about generators. The generators in central stations and the DeWind turbines must operate at constant speed because they are directly connected to the grid. This locks them into the grid frequency, which must be held constant. If these generators aren’t running at a certain constant speed, they can’t be connected to the grid. If they don’t keep running at that constant speed, they will trip. I have direct experience in this matter. Since Dude mentions “slip”, it is clear that he does not understand the technology.
Since Dude is mistaken about these points, it is no surprise that he doesn’t understand what I have said about inverters. Wind turbines can operate much better without them. DeWind has proved it. Dude has taken my statements to mean that there is no use whatsoever for inverters.
Of course we still need inverters to convert DC battery power and solar power to AC for the grid. I don’t know of any way to get rid of the inverter in these applications. That is, no better way. We could use the rotary converter:
https://en.wikipedia.org/wiki/Rotary_converter
but it would not be an improvement.
What I have tried to explain is that wind power does not require inverters. This is not just my opinion. It is current technology, although an almost totally neglected one.
And Dude, batteries are not the only way to store energy. They are not even the best way. They are just about the worst way:
“… Batteries are ideal for powering cell phones and toys. But there are legitimate questions about the extent of their contribution to our future energy needs…”
https://www.powermag.com/blog/californias-big-battery-bet/
I have not shown to my satisfaction how confused Dude is about these subjects. It would take too long.
[George] mentioned “CVT” for the first time in any of the comments (I think).
I was wondering how constant generator speeds would be maintained without a “gearbox”.
I know lots of cars use CVTs for a long time without trouble, but some cars with them had lots of problems.
Because of that, I am concerned about the lifetime of CVTs in a windmill.
To The Commenter Formerly Known As Ren:
While it is not easy to figure this out anymore, because the information has almost disappeared from public view, the Voith WinDrive [CVT] is entirely different in design from a typical automobile CVT. But the purpose is the same. I suppose I don’t need to explain why a CVT is different from a multi-speed gearbox, and why it has some advantages over a such a gearbox in an automobile.
However, you can find a lot of information about other Voith machines, most of which are speed converters of some kind, usually of a very high power rating. Voith is an old company with the highest reputation in its field. It has few competitors.
Voith used its expertise to develop the WinDrive. It is a hydraulic device. Precision control of speed is not easy, and the inventors said it was the most difficult problem they ever tried to solve. But they did it.
The WinDrive would outlast a good many wind turbines. That is how reliable it is, and Voith would not have produced a machine of lesser quality. That is another reason it is different from automobile CVTs.
But it was expensive, and so far as I have been able to determine, that is one reason that the DeWind turbines did not sell. Another factor is the extreme conservatism of the wind turbine industry. It is the result of cutthroat competition. Most of the manufacturers are making very little or no money, even losing it, so most of them will stick with what they know. They believe that they can’t afford to try anything new.
And another factor. If one is not the inventor, then the invention can’t be any good, as is well-known.
Thank you [George] for your response!
I wasn’t challenging your knowledge (if that is how it appeared) just attempting to satisfy my curiosity.
And my surprise that no one, including the author, did not mention the use of CVTs in windmills.
[George], all the comments about the difficulty of matching different generators to one input shaft reminded me of the difficulties the US Navy has experienced with the Arleigh Burke destroyers, but in reverse (sort of). There they hooked 2 different sized power sources through a “gearbox” to the output that attempted to optimize power and fuel consumption over the output range.
As a result, the $4billion+ destroyers may be retired well ahead of their projected lifespans.
P.s. I am not sure if my earlier response to your comment is stuck in the transmission or dropped completely, but thanks for your response and bringing up the CVT information
Your comment about a problem in a class of US Navy ships is interesting:
“…The Navy has determined a flaw in the Freedom-class Littoral Combat Ship’s combining gear, a complicated gearing mechanism that links the engines of the ship… The fix involves replacing the two high-speed clutch bearings with a different bearing version that would not fail as easily…”
https://news.usni.org/2021/01/19/navy-calls-freedom-lcs-propulsion-problem-class-wide-defect-wont-take-new-ships-until-fixed
The problem, then, is not that combining gears are no good. It is in a faulty component of this particular gearbox. It shouldn’t be difficult to fix.
While looking into this, I found a funny story about Arleigh Burke [31 Knot Burke]:
“…During World War Two, Burke mistakenly led his destroyer squadron into a Japanese minefield. Admiral Halsey radioed to ask what he was doing in a Japanese minefield. ‘Thirty-one knots,’ replied Burke…”
https://en.wikipedia.org/wiki/Arleigh_Burke
For most of the twentieth century, steam ships used a reduction gear that combined the output of two steam turbines, high speed and low speed, or high pressure and low pressure. It works fine.
Diesel power plants have made that technology obsolete. Diesel power is more efficient, and the huge low-speed diesels, some of 100,000 HP or more, turn so slow that they do not need a reduction gear.
We have known how to make a simple combining gear since 1940. See US Pat. No. 2,225,863, Halford et al. Maybe in another hundred years the industry will finally notice it.
The DeWind turbines use both a fixed ratio gearbox and the Voith WinDrive. The gearbox increases the speed of the rotor shaft, then the higher speed shaft power goes into the WinDrive. This keeps the WinDrive as small as possible. Also, high input speed to the WinDrive makes for faster speed control. Here is an excellent article about these wind turbines, one of the few that still appear on the internet:
https://www.windpowerengineering.com/a-turbine-that-supports-the-grid/
Thanks!
It appears I was confused between the Arleigh Burke destroyers and the LCS problems.
A large portion of my career has been in gear manufacturing in the industrial and aerospace sectors.
My impression is that early big wind turbine designs game out of the industrial power transmission world. They used big heavy pancake gears and thick robust gearbox housings. Weight minimization consisted downsizing the gearbox to deal with the shock load that would go to the system, when a turbine that was spinning up would push against the grid. Miners rule was employed quite a bit to takes this into account as part of the design criteria. My understanding is that these shock loads where not well understood initially and lead to many premature failures. (I once had a designer show me a picture of a key used on a gear and the shear deformation that it had from the cumulative shock loads from me hooked to the grid. (They needed to go to hardened keys in the design))
One thing I wonder about is what wind turbine design would look like today if these initial designs would have been given helicopter transmission design engineers instead. These guys live in a totally different world that is all about power to weight. Industrial gearbox designers just don’t think in those terms. Helicopter guys would do crazy stuff, like taking to account the flex in a gearbox housing so that the gears would be in full mesh at full torque.
I haven’t researched what the percentage of weight a gearbox is relative to the blades, but I it make me ponder what the standard design template for wind turbine transmission would be like if the problem was worked initially by aerospace power transmission design engineers. Would a lighter gearbox on top of a tall tower require a thinner tower? It’s something I’ve wondered about for a long time.
You’re suggesting wind turbines be completely torn down and rebuilt every 2200 hours of operation?
Turbine gear boxes are neither roller mill gears or aircraft gears.
Weight isn’t going to be a big issue, designed for wind loads, gravity loads checked after. Rotating inertia is high already.
Hardened key? Yikes.
That makes the shaft and the gear the soft parts?
That’s a quality engineering fix! I smell MBAs.
Before the shock loads where understood there was a lot of that going on in the early wind turbine drives there was a lot of premature failures. Good point on the rebuilt… (Split the difference and have a combined designed team locked in a room with lots of beer)
Question from a layman: why is having a gearbox with four generators (much) more difficult than a gearbox with one? It seems to me that you can have a gearbox with one output shaft, a gear on that, and four generators with a gear meshing with that main gear. Just add clutches if you want to take generators offline.
What am I missing here?
I will attempt to answer with the caveat that I am an electrical engineer, not mechanical.
As I understand it, the gears in the Clipper turbine had too much slop, or play. Since the generators aren’t going to behave 100% identical to each other, that means that each generator will push or pull slightly compared to the others. The more slop in the gears there are, the more these unbalanced push and pull forces from the generators will wear on the gears.
With a single generator you won’t have the tug-of-war going on that you do with multiple generators.
Yes, except “slop” conveys a gross manufacturing tolerance. The issue of load-sharing among parallel gearing paths (eg planetary drives) is a more subtle issue about tolerances that are actually very close to start with, then elastic deformations etc, etc. 4 parallel paths as implemented by Clipper was never going to achieving good load sharing and thus was asking for trouble. If you know what you’re doing on this issue (eg using Ray Hicks’ patented flexpin solution) you can get good load-sharing with up to 8 planets. But this wasn’t a planetary system and Clipper clearly didn’t understand the load-sharing issue.
Clipper pulled the audacious move of displaying a full nacelle at the 2006 AWEA Conference in Pittsburgh. It was huge, and was by far the biggest item on the show floor. Rumour had it that the weight of the Clipper nacelle cracked the loading dock at the convention centre.
The whole industry was dancing around ways to avoid the GE variable speed patent at the time, and Clipper’s approach — at least on paper — looked pretty decent. Too bad it didn’t work out in the field.
The DeWind synchronous machines were a nice concept, but having all that complicated hydraulics in the tower top made them expensive to buy and potentially complicated to maintain. At least they weren’t the Samsung wind turbines …
Voith is the master of controlling speed using hydraulics. Their units, including the WinDrive, are the most reliable in the industry. The mean time between failures of these machines is decades long. “Complicated hydraulics” is not the reason the DeWind turbines did not sell.
Regarding complication, the WinDrive, an extremely reliable device that allows the turbine to produce power of the highest possible quality, eliminated the far more complicated inverter, which is an unreliable, inefficient and expensive contraption that produces dirty power. The WinDrive made the DeWind turbines far superior to conventional turbines.
If cost was the reason the industry rejected the DeWind arrangement, it is because the true cost was never calculated. If it had been, DeWind and its copiers would now be the only wind turbine manufacturers in operation.
Sounds similar to Windflow Technologies here in New Zealand that developed a synchronous wind turbine that worked really well but could never compete against the giant producers in the industry. https://www.renewable-technology.com/contractors/wind-turbines/windflow/. It was a good fit for high wind isolated applications and apparently quite reliable but not every good idea makes it.
Thanks for your excellent comment. I had forgotten about the Windflow turbine, invented by Geoff Henderson. His company did go bankrupt a few years ago, despite the great value of his technology. But he formed a new company to continue the work, SyncWind Power Ltd, although the new Web site still uses the WindFlow name:
https://https://www.windflow.co.nz//
Henderson’s Linkedin page is a rich source of information:
https://www.linkedin.com/in/geoff-henderson-b8400036/?originalSubdomain=it
In particular, see the article by Henderson et al. in this publication, cited in his Linkedin page comments and free on the internet:
https://www.nxtbook.com/nxtbooks/pes/electrification_march2022/index.php?mkt_tok=NzU2LUdQSC04OTkAAAGDE5I2j8v8Wlw6d8bxon7cL-wvpzybUpeqTWauRppLABR-O3IE3qZGFyTJzlkhb-sFoCkccdUx0u2TfUvybRgJao1E0yWrtBx2rjlqMmnxP3s#/p/54
Henderson is proving that wind power cannot reach its full potential if it continues to rely on inverters. That is what I have tried to show with my comments here.
Thanks for the plug. Incidentally Windflow did not go bankrupt. It went into solvent liquidation – there is a difference. All the creditors were paid. And yes the 46 MW wind farm of Windflow turbines in New Zealand is still running, providing synchronous power to the grid.
The problem with the Voith Windrive is that it is heavy, expensive and inefficient. This is because it is a hydrodynamic torque transmission, which transmits 100% of the power. In addition to the above disadvantages, I strongly suspect its Achilles Heel (and a reason it did not take off in Inner Mongolia) is that a post-fault synchronisation pole-slip event can destroy it. And it is a very expensive thing to have to replace.
The Syncwind solution, by contrast, is a hydrostatic torque reaction system, which handles only 5% of the power. Pole-slip (which is a very rare contingency that comes with the territory of being a distributed form of power generation) is not an issue because the hydrostatic pump is the only thing adversely affected and is cheap to replace – because it is rated at only 5% of turbine power.
The latest version (which we call LVS for “low variable speed”) has the great advantage of providing broad-band variable speed while still only handling 5% of the power in its hydrostatic components.
I believe it has a future and would like to see the Syncwind solution adopted by multi-MW turbines going forward.
PS – I quite agree with George’s analysis of the Clipper gearbox. It was a silly idea from the start which any decent gearbox designer could see was never going to achieve proper load sharing.
re: “The problem with the Voith Windrive is that it is heavy, expensive and inefficient. This is because it is a hydrodynamic torque transmission, which transmits 100% of the power. In addition to the above disadvantages, I strongly suspect its Achilles Heel (and a reason it did not take off in Inner Mongolia) is that a post-fault synchronisation pole-slip event can destroy it. And it is a very expensive thing to have to replace.”
I have more of a mechanical background than an electrical, so I’m trying to understand what you’re saying.
I was looking at some technical information on the voith system.
http://files.messe.de/abstracts/43453_1_Reimesch_Voith_Turbo.pdf
You where saying that it transmits 100% of power, but I don’t think that’s accurate… The coupling has Fottinger slip, which (if memory serves me would have ~3% power lose inherit in it’s design..)
What I don’t understand is you’re statement about it’s Achilles in a s that a post-fault synchronization pole-slip event? What get blown up in this kind of event? I don’t understand what the failure mechanism would be in that situation?
Regarding: “The latest version (which we call LVS for “low variable speed”) has the great advantage of providing broad-band variable speed while still only handling 5% of the power in its hydrostatic components.”
I was trying to get a quick 50K understanding on how the LVS system works and I felt like I was going down a google rabbit hole. (Any chance there is some source material you can point me to?)
Just thinking out loud(and probably a stupid idea) I wonder if the clipper drives had slip couplings between the generators and the gear train, if that would have resolved some of the load issues… (Although, at this point, apparently I don’t understand what happens with pole slipping.
Thank you for your honest consideration. I have recently US Patented a wind turbine design. Perhaps someone will share some insights? Bladeless “Cone” wind turbine. 75-300 kw… mikersunday@gmail.com I will try to post on a website. :o ) later. If you are looking for an investment type? I just need one? Utility patent, also. 11/04/24 Think California/Texas/NY/.
The clowns who came up with the Clipper design must have been ignorant of the details of gearbox design in terms of load-sharing between multiple outputs. It was always obvious that they were not going to get good load-sharing.
The great disgrace of this venture was how they raised $250 million or more on the back of such gearbox design ignorance.
I worked for Clipper at a Texas site, on the briefly mentioned blade failure problem. I was a Mechanical and Electrical Engineer but never studied the intricacies of drive systems.
So I have to ask. Why not have a sprocket up at the nacelle and a very long “bike chain” down to the ground and locate all of the gearing (as/if needed) and generator there?
I also wonder if the disdain for inverters is warranted with modern electronics. It seems to me a much easier problem than extremely rigid AC speed synchronization of a variable source.
I looked at using roller chains a while back. Given the extremely low rotational speeds at which they must operate, their horsepower capacity is so low that there would not be nearly enough room in the tower for them. It would also require plenty of sprockets and not enough room for them either. Even if chains would work, the weight of the drive would be enormous. I believe we can let the idea go.
I don’t believe that a continuous, multiple loop wire cable would work either, for the same reason. Fatigue alone would probably rule it out. The cable would fail early from the continuous bending under load.
Concerning power electronics, there are credible studies showing that one of their main disadvantages is that they must handle at least three times the normal current when there is a disturbance. This greatly increases their cost. That is far from the only reason to reject them for wind turbines. In general, it seems foolish to rely on power electronics when there are simpler, cheaper, more efficient, and more reliable means for converting wild AC to a fixed frequency for the grid. Geoff Henderson has been doing it for years.