Say what you want about the wisdom of keeping a 50-year-old space mission going, but the dozen or so people still tasked with keeping the Voyager mission running are some major studs. That’s our conclusion anyway, after reading about the latest heroics that revived a set of thrusters on Voyager 1 that had been offline for over twenty years. The engineering aspects of this feat are interesting enough, but we’re more interested in the social engineering aspects of this exploit, which The Register goes into a bit. First of all, even though both Voyagers are long past their best-by dates, they are our only interstellar assets, and likely will be for centuries to come, or perhaps forever. Sure, the rigors of space travel and the ravages of time have slowly chipped away at what these machines can so, but while they’re still operating, they’re irreplaceable assets.
engineering83 Articles
New Documentary Details Ventilator Development Efforts During COVID
What would it be like to have to design and build a ventilator, suitable for clinical use, in ten days? One that could be built entirely from locally-sourced parts, and kept oxygen waste to a minimum? This is the challenge [John Dingley] and many others faced at the start of COVID-19 pandemic when very little was known for certain.
Back then it was not even known if a vaccine was possible, or how bad it would ultimately get. But it was known that hospitalized patients could not breathe without a ventilator, and based on projections it was possible that the UK as a whole could need as many as 30,000 ventilators within eight weeks. In this worst-case scenario the only option would be to build them locally, and towards that end groups were approached to design and build a ventilator, suitable for clinical use, in just ten days.
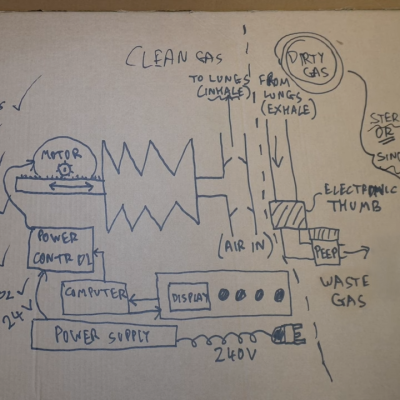
[John] decided to create a documentary called Breathe For Me: Building Ventilators for a COVID Apocalypse, not just to tell the stories of his group and others, but also as a snapshot of what things were like at that time. In short it was challenging, exhausting, occasionally frustrating, but also rewarding to be able to actually deliver a workable solution.
In the end, building tens of thousands of ventilators locally wasn’t required. But [John] felt that the whole experience was a pretty unique situation and a remarkable engineering challenge for him, his team, and many others. He decided to do what he could to document it, a task he approached with a typical hacker spirit: by watching and reading tutorials on everything from conducting and filming interviews to how to use editing software before deciding to just roll up his sleeves and go for it.
We’re very glad he did, and the effort reminds us somewhat of the book IGNITION! which aimed to record a history of technical development that would otherwise have simply disappeared from living memory.
You can watch Breathe for Me just below the page break, and there’s additional information about the film if you’d like to know a bit more. And if you are thinking the name [John Dingley] sounds familiar, that’s probably because we have featured his work — mainly on self-balancing personal electric vehicles — quite a few times in the past.
Continue reading “New Documentary Details Ventilator Development Efforts During COVID”
The Clever Design Behind Everyday Traffic Poles
Ever stopped at a red light and noticed something odd about the poles holding up the traffic lights? Look closer next time—many of them appear to hover just above the concrete, anchored by visible bolts. This video below explains it all. It’s not a job left unfinished. It is actually clever design, and all about functionality and easy maintenance. Let’s break down why engineers prefer this so-called ‘floating’ base plate setup.
At first, you might think mounting poles directly into concrete would be more stable—after all, that’s how heavy columns are often installed. But traffic light poles are lightweight, hollow, and face constant wind pressure. Instead of brute stability, they need flexibility and precise alignment. Enter the standoff base plate. By resting on leveling nuts, these poles can be fine-tuned for perfect verticality, even when the ground shifts slightly over time. That’s critical for keeping your 30-foot pole from leaning like the Tower of Pisa.
The open design also simplifies maintenance. If the pole tilts after years of wear, it takes just a few nut adjustments to fix it—no heavy cranes required. Plus, the gap helps prevent moisture buildup, reducing corrosion. So next time you’re waiting at an intersection, you’ll know it’s not just clever engineering—it’s practical street smarts. If you’re an infrastructure nut, this slightly older article might spark your interest.
Continue reading “The Clever Design Behind Everyday Traffic Poles”
The Many Leaning Towers Of Santos, Brazil
If you’ve ever gazed at the shoreline of Santos, Brazil, and felt like something was tugging at your inner eye level, you’re not alone. In fact, you’ve spotted one of the world’s most bizarre architectural phenomena.
Santos is an interesting contradiction—it’s a sunny coastal city with pristine beaches that also plays host to a bustling port. What draws the eye, however, is the skyline—it’s decidedly askew. This isn’t a Photoshop job or some avant-garde urban planning experiment, either. It’s a consequence of engineering hubris, poor planning, and geology just doing its thing.
Continue reading “The Many Leaning Towers Of Santos, Brazil”
Engineering Lessons From The Super-Kamiokande Neutrino Observatory Failure
Every engineer is going to have a bad day, but only an unlucky few will have a day so bad that it registers on a seismometer.
We’ve always had a morbid fascination with engineering mega-failures, few of which escape our attention. But we’d never heard of the Super-Kamiokande neutrino detector implosion until stumbling upon [Alexander the OK]’s video of the 2001 event. The first half of the video below describes neutrinos in some detail and the engineering problems related to detecting and studying a particle so elusive that it can pass through the entire planet without hitting anything. The Super-Kamiokande detector was built to solve that problem, courtesy of an enormous tank of ultrapure water buried 1,000 meters inside a mountain in Japan and lined with over 10,000 supersized photomultiplier tubes to detect the faint pulses of Chernkov radiation emitted on the rare occasion that a neutrino interacts with a water molecule.
Continue reading “Engineering Lessons From The Super-Kamiokande Neutrino Observatory Failure”
Help Wanted: Keep The World’s Oldest Windmills Turning
While the Netherlands is the country most known for its windmills, they were originally invented by the Persians. More surprisingly, some of them are still turning after 1,000 years.
The ancient world holds many wonders of technology, and some are only now coming back to the surface like the Antikythera Mechanism. Milling grain with wind power probably started around the 8th Century in Persia, but in Nashtifan, Iran they’ve been keeping the mills running generation-to-generation for over 1000 years. [Mohammed Etebari], the last windmill keeper is in need of an apprentice to keep them running though.
In a world where vertical axis wind turbines seem like a new-fangled fad, it’s interesting to see these panemone windmills are actually the original recipe. The high winds of the region mean that the timber and clay structure of the asbad structure housing the turbine is sufficient for their task without all the fabric or man-made composites of more modern designs. While drag-type turbines aren’t particularly efficient, we do wonder how some of the lessons of repairability might be used to enhance the longevity of modern wind turbines. Getting even 100 years out of a turbine would be some wicked ROI.
Wooden towers aren’t just a thing of the past either, with new wooden wind turbines soaring 100 m into the sky. Since you’ll probably be wanting to generate electricity and not mill grain if you made your own, how does that work anyway?
Continue reading “Help Wanted: Keep The World’s Oldest Windmills Turning”
Halfway Between Inspiration And Engineering
We see a lot of hacks where the path to success is pretty obvious, if maybe strewn with all sorts of complications, land-mines, and time-sinks. Then we get other hacks that are just totally out-of-the-box. Maybe the work itself isn’t so impressive, or even “correct” by engineering standards, but the inner idea that’s so crazy it just might work shines through.
This week, for instance, we saw an adaptive backlight LED TV modification that no engineer would ever design. Whether it was just the easiest way out, or used up parts on hand, [Mousa] cracked the problem of assigning brightnesses to the LED backlights by taking a tiny screen, playing the same movie on it, pointing it at an array of light sensors, and driving the LEDs inside his big TV off of that. No image processing, no computation, just light hitting LDRs. It’s mad, and it involves many, many wires, but it gets the job done.
Similarly, we saw an answer to the wet-3D-filament problem that’s as simple as it could possibly be: basically a tube with heated, dry air running through it that the filament must pass through on it’s way to the hot end. We’ve seen plenty of engineered solutions to damp filament, ranging from an ounce of prevention in the form of various desiccant storage options, to a pound of cure – putting the spools in the oven to bake out. We’re sure that drying filament inline isn’t the right way to do it, but we’re glad to see it work. The idea is there when you need it.
Not that there’s anything wrong with the engineering mindset. Quite the contrary: most often taking things one reasonable step at a time, quantifying up all the unknowns, and thinking through the path of least resistance gets you to the finish line of your project faster. But we still have to admire the off-the-wall hacks, where the way that makes the most sense isn’t always the most beautiful way to go. It’s a good week on Hackaday when we get both types of projects in even doses.