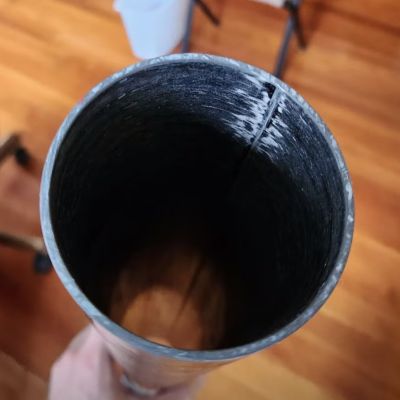
Carbon fiber (CF) is an amazing material that provides a lot of strength for very little weight, making it very useful for a lot of applications, ranging from rods in CoreXY 3D printers to model- and full-sized rockets. The model rocketry hobby is the reason why [Andrew Reilley] developed his own CF tube winding machine called Contraption. A tutorial video (also embedded below) shows how this machine is prepped for a winding run, followed by the winding progress and finalizing before admiring the result.
The entire machine’s design with 3D printed parts and off-the-shelf components is open source, as is the TypeScript and NodeJS-based Cyclone software that creates the toolpath specifying the parameters of the tube, including number of layers and the tow angle.
As a wet winding tow machine, the carbon fiber strands are led through the liquid resin before being wound onto the prepared mandrel. During winding some excess resin may have to be removed, and after the winding has been finished the tube is wound with shrink tape. This is followed by a heat gun session to shrink the tape and letting the resin cure. Following curing, the tape and mandrel are removed, resulting in a rather fancy looking CF tube that can find a loving home in a lot of applications, except perhaps ones that involving crushing outside pressures like those found deep below the ocean surface.
That is a damn sweet result! Good job!
Weird flex but ok
“No” your flex is weird. Sometimes people state facts and opinions, then others like you Troll them because you can’t help but spread your negativity around. Please try to keep things positive
It was positively an advert.
Use to make these in an industrial setting, finishing and fitting them to be specific, 20′ with a variety of sizes and densities. The telecommunication sector is actually very reliant on grp pipes for laying cables these days. The process we would follow in factory evolved in over a decade and is very inefficient, with sub par quality. Don’t let people undersell the value of a system like this, that multi-million Dollar factory is just result of one man’s hobby of winding pipes in his garage, and as the state of the industrial set up is, a system like this at scale could out compete any player in the industry by miles.
Can I make a submarine with it?
Anything can be a submarine once.
an iceberg?
For about 90%
Only if you promise to take a few billionaires with you on the first dive.
Dude. Come on. People died.
Too soon?
That’s not that funny brother
Would that be good enough for a bicycle frame? That could be an interesting project.
This is nice.
I do wonder what the material costs are compared to ready made tubes.
But of course this becomes really interesting when you’re not making standard round tubes, but custom parts. A good example would be an arm for a quad copter. Something like an oval tapered tube with some integrated flange for the motor mount.
A few remarks though:
@01:50 The first cylindrical wrap is a waste of carbon, because the fiber direction is wrong for any application except pressure vessels. It may be useful to lay down some thin yarn (any material) in a cross pattern to create some “roughness” to keep the carbon fiber in place during curing.
@02:50 One of the most interesting details is how the turn around is done at the end, and this is unfortunately not visible.
I think the part he was making was a rocket motor casing in that case it would have to hold up to a bit of internal pressure, thats probably why he did the hoop wind at 1:50.
Builder of the machine here! Thanks! I commented on another post about the costs. If I wanted to use premade tubes directly from China they can be had for pretty cheap, but tubes customized for my application (wind angle, high temperature resin) quickly end up costing more than the machine cost me to build… per tube.
I would like to play with winding on non-cylindrical mandrels eventually, but haven’t had a reason to yet. I want to make a bike frame on the machine someday, and that would probably involve winding on a oval-profile mandrel.
You are absolutely right that hoop winds are only useful for pressure vessels… I included that layer because that tube will be a pressure vessel! My application for these tubes is as rocket motor casings, and I’ve hydrostatic-tested them to >2500 psi without failure. I have another video that shows more details about the motors I build with these tubes, and also has more footage of the winder, including a turn around: https://www.youtube.com/watch?v=tLMQOUrY6_g
Amazing!
Nice! But I think you would save money (and a lot of time) by just buying a pre-made carbon fiber tube of the correct diameter, thickness and weave for your application.
Builder of the machine here! Custom carbon tubes are expensive, especially when you get to this size. I just used the pricing calculator on http://www.rockwestcomposites.com to get a quote for a similar tube (2.75 ID, 0.08″ wall, 36″ length, high temp resin, low wind angle for pressure vessels) and they would be $800 a piece! That’s close to twice what the materials for building my winder cost, and >20x the cost of my materials to wind this one tube. These tubes are single-use in my application (rocket motor casings) so I would be burning money quickly if I spent $800 a motor on just the case.
Also, for me it is as much about having a project and learning as it is about the final product.
You could shape your mandrel and make alot of interesting things!