Recently, a prototype inflatable space station module built by Sierra Space exploded violently on a test stand at NASA’s Marshall Space Flight Center in Alabama. Under normal circumstances, this would be a bad thing. But in this case, Sierra was looking forward to blowing up their handiwork. In fact, there was some disappointment when it failed to explode during a previous test run.
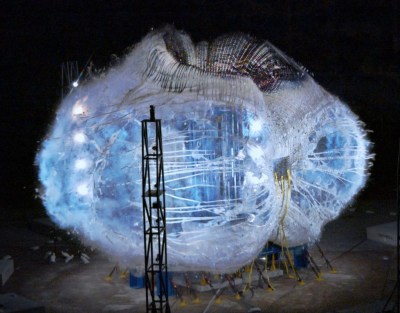
That’s because the team at Sierra was looking to find the ultimate bust pressure of their 8.2 meter (26.9 foot) diameter Large Integrated Flexible Environment (LIFE) module — a real-world demonstration of just how much air could be pumped into the expanding structure before it buckled. NASA recommended they shoot for just under 61 PSI, which would be four times the expected operational pressure for a crewed habitat module.
By the time the full-scale LIFE prototype ripped itself apart, it had an internal pressure of 77 PSI. The results so far seem extremely promising, but Sierra will need to repeat the test at least two more times to be sure their materials and construction techniques can withstand the rigors of spaceflight.
Sierra is a targeting no earlier than 2026 for an in-space test, but even if they nail the date (always a dubious prospect for cutting edge aerospace projects), they’ll still be about 20 years late to the party. Despite how futuristic the idea of inflatable space stations may seem, NASA first started experimenting with the concept of expandable habitat modules back in the 1990s, and there were practical examples being launched into orbit by the early 2000s.
NASA TransHab
As NASA finalized plans for what we now know as the International Space Station, it was understood that most of the components for the orbiting complex would need to fit inside the payload bay of the Space Shuttle. In practice, this meant that Station modules would need to be largely cylindrical in shape, and no longer than approximately 18 m (60 ft). These alone weren’t particularly difficult parameters to work around, as previous space stations from the US and Soviet Union faced similar limitations from their respective launch vehicles. The tricky bit was that the Shuttle’s payload bay was only 4.6 m (15 ft) wide.
While this allowed for modules slightly wider than what had been used thus far for Mir, it was a considerable downgrade when compared to the 6.6 m (21.6 ft) diameter “Orbital Workshop” module of Skylab. Seeing this as a potential long-term problem, engineers at NASA turned to an idea that had originally been conceived for a theoretical mission to Mars: an inflatable habitat module that could be packed into the Shuttle’s payload bay and then expanded to its final size of 8 m (26 ft) once in orbit and filled with air.
The proposed module, known as TransHab, was to be divided into multiple decks providing living and working areas for the astronauts as well as ample storage. There would have been six individual crew cabins, a dedicated workout area, medical facilities, a fully-equipped kitchen, and a large wardroom table that could be used for all-hands meetings or group meals.
Unfortunately, due to delays and cost overruns on the overall International Space Station program, NASA was ordered to stop R&D on inflatable modules like TransHab in 2000. Construction was instead started on a more simplistic habitation module which could fit inside the Shuttle, but ironically, this too was ultimately canceled.
Even today, there is no official “habitat” module on the ISS — facilities for the sleeping, eating, and exercising are instead spread throughout the Station.
Bigelow Aerospace
While NASA was forbidden by House Resolution 1654 to work on their own inflatable Station modules, the bill did include language that said the space agency could lease such a module if it was built by private industry. Having heard about the cancellation of TransHab, entrepreneur Robert Bigelow contacted the space agency and was able to secure the necessary rights to commercialize the research they had already done on inflatable modules through his company Bigelow Aerospace.
TransHab development had been largely conceptual at this point, and Bigelow Aerospace spent the next several years taking NASA’s ideas and turning them into a practical test article. One of the improvements they made was the addition of Vectran to the inflatable structure. Twice as strong as Kevlar, this manufactured fiber is spun from a liquid-crystal polymer, and had previously been used in the airbag which allowed Pathfinder to safely land on Mars in 1997.
Genesis I
In 2006, Bigelow Aerospace had developed NASA’s original concept to the point that they were ready to launch a functioning prototype.
The Genesis I module had a length of 4.40 m (14.4 ft), and expanded from its original diameter of 1.60 m (5 ft 3 in) at launch to 2.54 m (8 ft 4 in) in an operation that took roughly 10 seconds to complete. Its solar arrays provided power for onboard diagnostic systems and more than a dozen cameras which recorded the inflation from both inside and outside of the module.
Designed to operate for six months, the Genesis I module transmitted data back to Bigelow Aerospace for two and a half years before finally going dark. While the onboard systems stopped transmitting useful data, the structure itself remained completely intact with no signs of pressure loss or other degradation.
Currently, Genesis I remains in a stable 463 x 471 km (287 x 292 mile) orbit at an inclination of 64.5°, and is cataloged as NORAD 9252 and COSPAR 2006-029A.
Genesis II
Following on the success of their first prototype module, Bigelow Aerospace launched Genesis II a year later in 2007. This second module was largely identical from a external and mechanical standpoint, but added even more cameras, reaction wheels which allowed the module to better orient itself in space, an improved gas inflation system, and an upgraded sensor suite.
Like its predecessor, Genesis II transmitted data for more than two years, and remains in a very similar 452 x 505 km (280 x 314 mile) orbit. It’s cataloged as NORAD 31789 and COSPAR 2007-028A.
Bigelow Expandable Activity Module (BEAM)
After nearly a decade of further development, Bigelow Aerospace finally provided NASA with an inflatable ISS module in 2016. The space agency paid $17.8 million for the module, and it was delivered to the Station inside the unpressurized trunk of a SpaceX Dragon. From there, the Canadarm2 robotic arm was used to attach BEAM to the aft port of the Tranquility module.
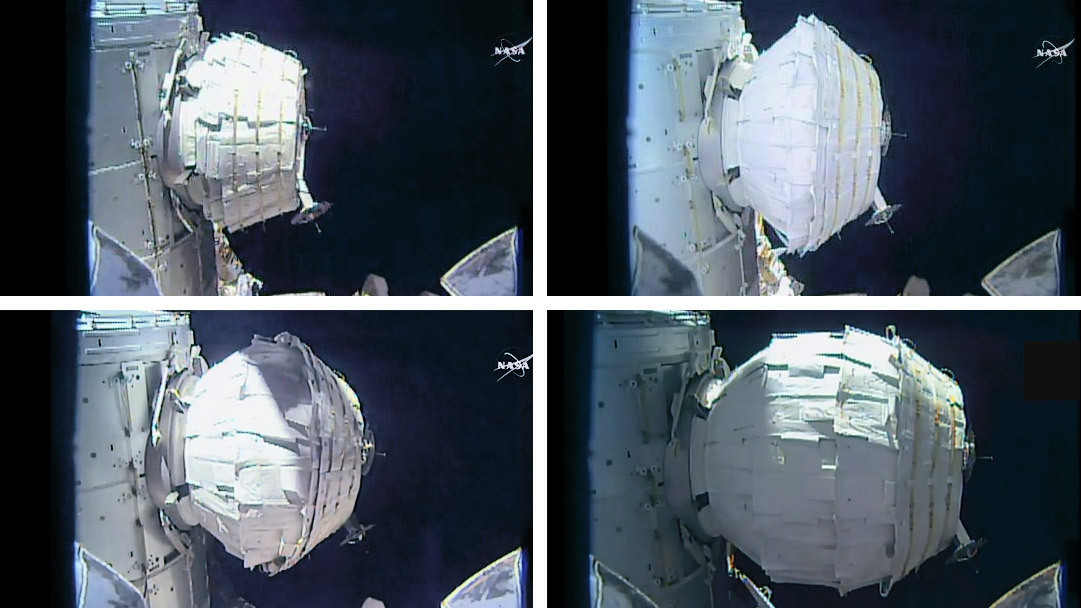
Unlike the twin Genesis modules, BEAM could expand both its length and diameter. When packed into the Dragon’s trunk, it was 2.16 m (7 ft 1 in) long and 2.36 m (7 ft 9 in) in diameter. After an expansion process which took seven hours, it measured 4.01 m (13.2 ft) long with a diameter of 3.23 m (10.6 ft).
A fully developed inflatable module would have included internal fixtures and equipment, but being a test article, the inside of BEAM was essentially just open space. After monitoring the module for a year, it was decided to use it for storage, and the inside of BEAM was outfitted with cloth bags. Following an engineering assessment in 2019, NASA decided that the module would remain attached to the ISS until at least 2028.
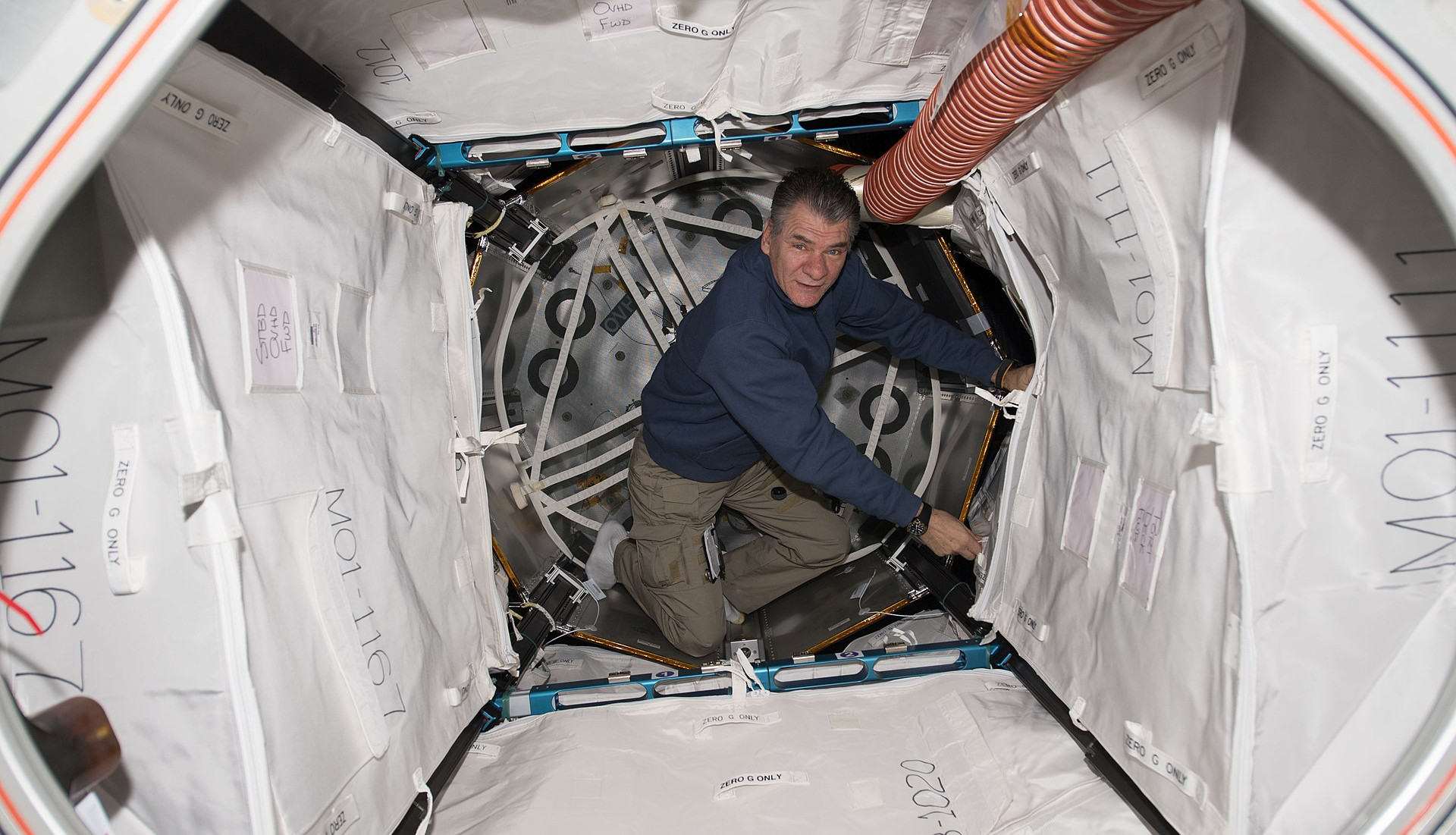
Unfortunately, Bigelow Aerospace laid off all of its employees in March 2020, and the company suspended operations entirely in 2021. While no official announcement was ever made, the company is now considered defunct.
Sierra Space
With Bigelow Aerospace out of the running, Sierra Space has emerged as the new industry leader for space-bound expandable structures. Spun off from Sierra Nevada Corporation in 2021, the company is focused primarily on developing not just the Large Integrated Flexible Environment (LIFE) module, but also the Dream Chaser spaceplane. The end goal is vertical integration — with the Dream Chaser bringing crew and cargo to a space station comprised of LIFE modules.
Sierra’s multi-layer inflatable technology includes a Vectran “Restraint Layer”, which the company says makes their modules harder than steel once fully inflated. They’ve also developed a way to place openings, such as for windows or air locks, in the inflatable walls of the module while still exceeding the pressure ratings required for certification by NASA. This capability promises to greatly expand the potential functionality of inflatable modules, which previously had only been designed with openings on either end of the cylindrical structure.
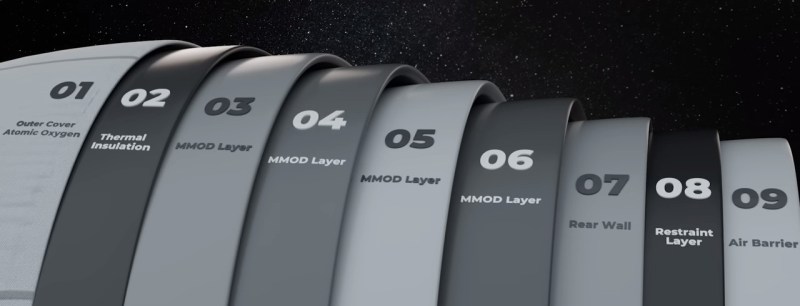
The module that Sierra Space destructively tested recently was a full-scale prototype of what the company calls LIFE 1.0: a structure with an inflated volume of 300 m³ that is 6 m (19.6 ft) long with a diameter of 9 m (29.5 ft), and can be launched in a standard 5 m (16.4 ft) payload fairing. This would make it compatible with rockets such as the SpaceX Falcon 9 and the newly debuted Vulcan from United Launch Alliance.
The next evolution will be LIFE 2.0, which will double the length of the module to 12 m (39.3 ft) to achieve an inflated volume of 600 m³ while retaining the same diameter to stay compatible with current launch vehicles. Sierra Space also has long-term plans for a LIFE 3.0, a massive 1440 m³ module that would have more usable volume than the entire International Space Station. With a length of 16.2 m (53 ft), an inflated diameter of 11 m (36 ft), and a packed diameter of 7 m (23 ft), putting LIFE 3.0 into orbit would require a next-generation launch vehicle such as NASA’s SLS Block 1B Cargo, the SpaceX Starship, or the New Glen from Blue Origin.
Next Steps
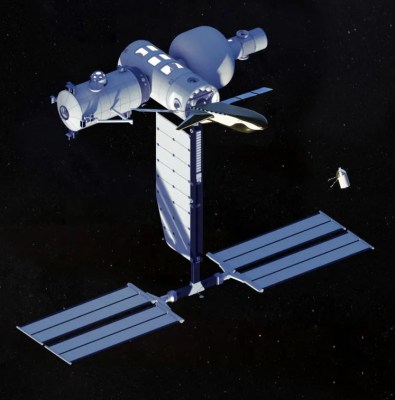
According to the press release from Sierra Space, 2024 will be a busy year. There will be several more tests, with both full-size and sub-scale articles, and they’ll also be working on the Micrometeoroid Orbital Debris (MMOD) layers which will be critical to protect the module from the inevitable impacts that will come with long-duration spaceflight.
As for the first practical application of the technology, Sierra Space and Blue Origin are working together to develop the Orbital Reef commercial space station, which is slated to have at least one LIFE module as part of its baseline configuration. NASA awarded the Orbital Reef project $130 million in December of 2021, with the goal of having it operational by the time the International Space Station is retired, which is currently scheduled for sometime in 2030.
While it looks like it won’t end up happening on the ISS, with a bit of luck, NASA’s dream of having astronauts living and working in an inflatable space station may finally become a reality before the end of the decade.
There have been a couple companies that have been experimenting with inflatable concrete and cement shelters for a while now. I know concrete is water intensive, but aggregate materials like that make for excellent ballistic armor, which is needed in our cluttered LEO and MEO zones.
The main drawback of all this is weight. Even with modern advances in rocket tech we’re still looking at between $5000 to $25000 per pound (0.45 kg). Lunar cement/concrete is a thing, so that may be a workable option at some point.
Now that I’ve rambled all this out I realize I’ve logged way too many hours in Kerbal Space Program.
Theres plenty of building material IN SPACE no need to export.
And why bother with concrete when theres so much metal out there?
What we need is a a fleet of robotic spiders gobbling up and reforming type M asteroids into Stanford tori, O’neil cylinders and other such centrifugal pseudogravity stations.
I foresee a few tiny problems with your plan. I think it is the right path, but there is much new research that needs to be done to make it viable.
How do you separate the desired metal from the the other elements, on earth some of the processes currently used would just not work or not work very well at all in space.
Some mined ores we grind to a fine dust in massive ball mills which harness the power of gravity to smash the rocks into dust. Lots of water is used by most processes to help separate the desired elements from everything else. And then you have massive amounts of acids that are used to extract elements.
Basically you need a massive space based chemical industry, to process ores at an industrial scale.
Just wondering out loud here.. since iron- nickel chunks land on earth from space maybe there would be more available “raw metal” in alloy form available from asteroids than the ores that require all the messy wet processing here (oxides, sulfides, etc)?
If so maybe they could be separated from melts or plasma distilled, or gas difusion or just cooked with carbon taken from the nearest carbonacous asteroid? Maybe just melted and cast with solar furnaces. But yes a long way to go yet.
I agree in general. Although this might be mitigated by (at least at the start) only mining high quality ores that would need less processing.
Part of the problem on Earth is that most of the high-grade ores have been collected already, leaving us needing more complex processing methods to extract resources for lower grade ores.
I have a fragment of the Campo Del Cielo Meteorite which feels like and odd shaped piece of processed metal. For reference the composition is 92.9% Fe, 6.7% Ni, 0.4% Co.
We may also discover or invent new alloys which are better suited to off-world industrial uses.
Theres quite a bit of clean raw metals in space
Theres also 60 gazillion metric shittons of metal oxides already ground to a fine powder all over the moon, floating around the belt, and on every asteroid large enough to have even slight gravity.
But if you insist on dragging boring ancient earth techniques to space with you. Speed up your ball mill and rely on pseudogravity.
Once youve dusted your ores, run them through staged centrifugal separation to isolate individual components.
Forget the massive amounts of acids and focus on electrodeoxidation instead. Plenty of NaCl on Europa and CaCl2 on Mars to use as the molten electrolyte. The FFC method has already been applied to reduce a large number of metal oxides to the metals, including titanium, zirconium, chromium, niobium, silicon, tantalum, uranium and nickel.
Youre just stuck thinking in the box. Its not your fault, humanity has been banging their head against this limited rock for its entire history. Once we get serious about space the science needed to unlock the ENDLESS possibilities will fall into place.
I foresee that large orbital colonies will be 3D printed by sintering metallic material onto an inflatable form. The material would be crushed and enriched via centrifuges and heated using solar mirrors. You’d be right that it wouldn’t be as strong as pure, refined metal, but as a thick enough shell, or reinforced, it might be fine.
Great article, inflatable spacecraft always sound weird and never seems to appear in sci-fi, but makes a lot of sense! Also thanks very much for including metric measurements pretty much everywhere!
+1 on the metric
I can assure you that whole design was done in freedom units. Conversion to metric to please nasa requirements. 😂
I can assure you that whole calibration of those “?freedom?” units, that were mostly inherited from the British empire, are today calibrated against metric standards held by NIST (National Institute of Standards and Technology)
The “balloot” aerobraking maneuver in the movie “2010: The Year We Make Contact” doesn’t get enough credit.
Nor does Shatner and his ghost writers for adopting the balloot for James T Kirk-style orbital skydiving…
“ballute”
Q: What’s the difference between voting and reentering the atmosphere?
A: An “o”
/g
Some of Niven’s sories contained some inflatable sections to the lige pods i think
Life pods
Neal Stephenson’s great novel “Seveneves” includes individual inflatable habitats built in a rush. Wow, now I want to read that book again!!
I can’t help but wonder if they will add a water (ice) layer in order to improve protection from cosmic rays. I’ve read about plenty of ideas about using water like this and it seems like it could also help with micro-meteor impacts.
Where would you put it? Not pressurised, and outside the thermal layer? I wonder if there might be some benefit to keeping it liquid.
Yeah, I remember the old proposals where it would’ve been stretched into shape with internal carbon fiber struts, a mid-layer inflated with water to act as radiation shielding and water storage, and then an extra outer layer of polymer foam added to act as an ablative impact shield; all before the hab was filled with air. Everyone who worked on that proposal got fired (so far as I know) after the project was shut down. Yet another piece of tech to die to the “cost plus” model of funding.
There was a “rocket helicopter” orbital vehicle project that had a similar fate but potentially could’ve resulted in much cheaper launch pads and safer landings.
I wonder, Has there been any research into Deflating these modules so that they can be re-packaged?
Have always thought that these have an application in the Blended Wing Body aircraft which are hard to pressurize.
This paragraph,…
“Sierra is a targeting no earlier than 2026 for an in-space test, but even if they nail the date (always a dubious prospect for cutting edge aerospace projects), they’ll still be about 20 years late to the party. Despite how futuristic the idea of inflatable space stations may seem, NASA first started experimenting with the concept of expandable habitat modules back in the 1990s, and there were practical examples being launched into orbit by the early 2000s.”
…., Shows a Lack of Research done by the author, and a phrasing more common to mainstream right wing media dirt diggers.
NASA shelved the TransHab technology while waiting for materials science to catch up to what was needed, and then sold the rights to it to Bigelow. When Bigelow moved to close shop, Sierra bought the rights from them for the technology and what had been developed to that point.
Sierra is not “Late to the party”, they are the most recent investors in developing the technology, building on what has been achieved and learned by NASA and Bigelow.