[Eric Berger] has a thoughtful and detailed article explaining why Ingenuity, NASA’s small helicopter on Mars, was probably far more revolutionary than many realize, and has a legacy to grant the future of off-world exploration that is already being felt.
Ingenuity was recently grounded due to rotor damage, having already performed far beyond the scope of its original mission. The damage, visible by way of a shadow from one of the rotors, might not look like much at first glance, but flying in the vanishingly-thin atmosphere of Mars requires the 1.18 meter (3.9 foot) carbon fiber blades to spin at very high speeds — meaning even minor rotor damage could be devastating.
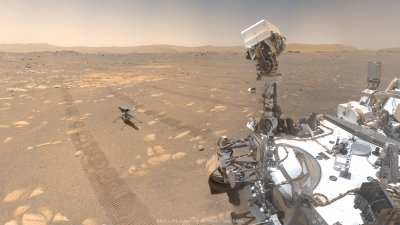
[Eric] points out a lot that is deeply interesting and influential about Ingenuity. Not only is successful powered flight on another planet a real Wright brothers moment, but how Ingenuity came to be validates a profoundly different engineering approach for NASA.
To work in the space industry is to be constrained by mass. But even so, Ingenuity‘s creators had a mere four pounds to work with. That’s for rotors, hardware, electronics, batteries, solar panel — all of it. NASA’s lightest computer module alone weighed a pound, so engineers had no choice but to depart from the usual NASA way of doing things to get it done at all. Not everyone at NASA was on board. But Ingenuity worked, and it worked wonderfully.
Powered flight opens new doors, and not just for support roles like navigation planning. There’s real science that can be done if powered flight is on the table. For example, [Eric] points out that inaccessible terrain such as the Valles Marineris canyon on Mars is doubtlessly scientifically fascinating, but at 4,000 km long and up to 7 km deep, rover-based exploration is not an option.
Loved the Scott Manley metaphorical take on what would happen if they attempted take-off now “like a brick inside a washing machine on a trampoline” (…shows three second clip of a brick inside a washing machine on a trampoline).
Unfortunately Berger’s point is undermined by technical reality: First, Ingenuity was not by any stretch the first mission to use non-hardened electronics, or even the first at Mars (e.g. the MarCO cubesats used as data relays for the Insight lander ran on the good old MSP430). Secondly, Ingenuity had a rad-hardened space-rated FPGA (MicroSemi ProASIC3L) that served as the primary processor, the Snapdragon was used for in-flight image processing only – the Snapdragon is the Navigation Computer, the Flight Computer (a dual-redundant pair of Hercules TMS570) was flying the vehicle, and the FPGA handled actuator controls and failover behaviour as well as overall command of the avionics.
I think Ingenuity may have been the first by some stretches. The cubesats you mentioned stayed in space and were only meant to be functional for a few months. They were redundant. They were also far lower profile than Ingenuity.
And just because Ingenuity had some hardened components doesn’t invalidate the fact that it had some non-hardened ones. The Snapdragon might not have been the only processor on board but it was on board and it worked.
If a NASA engineer wants to argue for using off-the-shelf hardware on a future mission, Ingenuity’s success will be a more compelling case than anything before it. That’s the point.
Keep in mind Ingenuity was a high risk project and the mission didn’t depend on it and there was no other choice. This is going to be the criteria they will have to go by. No way should non hardened electronics ever be used in mission critical applications.
“The cubesats you mentioned stayed in space and were only meant to be functional for a few months”
The MarCOs were functional in the harder rad environment of coast for half a year (they separated after launch and operated independently from Insight), with no rad-hard master controller.
Just having non-rad-hard subsystems is very very far from new. e.g. SAMPEX (1992) had an Intel 80386 running it’s data management system (and a RAD-6000 running avionics). SAMPEX operated for 8 years.
When I worked at JPL a couple years back, I knew several people on the M2020 engineering & ops teams.
One of the coolest tricks I heard of (other than perseverance’s main algorithms being implemented almost entirely in FPGAs, one of which was reprogrammed after touchdown) was them offloading compute tasks to Ingenuity from Perseverance, since it was just so much faster.
The RAD750’s had a good run, but the future looks bright with the HPSC and the increased use of COTS in flight projects.
Yes, I think that one of the MAJOR accomplishments beyond flying a helicopter on Mars is the proof of the durability of automotive COTS electronics on the surface of Mars and that should be be capitalized upon by also using them in, for instance, a comparatively cheap, highly redundant system as an experiment (in addition to the RAD750 hardware) in a future rover since vastly more processing power is needed for fast AI and rapid image processing for AI than can be provided by the legacy hardware.
“The avionics design is required to have low mass, low power and adequate radiation tolerance. A set of candidate parts to meet these requirements have been incorporated into the design which is now described.
The Snapdragon processor from Intrinsyc with a Linux operating system performs high-level functions on the helicopter. The Snapdragon processor has a 2.26 GHz Quad-core Snapdragon 801 processor with 2 GB Random Access Memory (RAM), 32 GB Flash memory, a Universal Asynchronous Receiver Transmitter (UART), a Serial Peripheral Interface (SPI), General Purpose Input/Ouput (GPIO), a 4000 pixel color camera, and a Video Graphics Array (VGA) black-and-white camera. This processor mplements visual navigation via a velocity estimate derived from features tracked in the VGA amera, filter propagation for use in flight control, data management, command processing, telemetry generation, and radio communication.
The Snapdragon processor is connected to two flight-control (FC) Microcontroller Units (MCU) via a Universal Asynchronous Receiver/Transmitter (UART). These MCU processor units operate redundantly, receiving and processing identical sensor data to perform the flight-control functions necessary to keep the vehicle flying in the air. At any given time, one of the MCU is active with the other waiting to be hot-swapped in case of a fault. The MCU from Texas Instruments is a TMS570LC43x high-reliability automotive processor operating at 300 MHz, with 512 K RAM, 4 MB
flash memory, UART, SPI, GPIO.”
The Snapdragon 801 is 2014 tech.
Is it Wise to Fly Automotive Grade Electronic Parts in Space?
Are They an Affordable and Effective Option?
National Aeronautics and Space Administration
NEPP EEE Parts for Small Missions Workshop September 11, 2014
https://nepp.nasa.gov/workshops/eeesmallmissions/talks/10%20-%20WED/1500%20-%20Sampson%20-%20Is%20It%20Wise%20to%20Fly%20Automotive%20Electronics_v4.pdf
—————–
Perseverance rover
Processor:
Radiation-hardened central processor with PowerPC 750 Architecture: a BAE RAD 750
Operates at up to 200 megahertz speed, 10 times the speed of Mars rovers Spirit and Opportunity’s computers
That’s 1997 tech because it’s radiation hardened which, among other measures, requires much greater feature size.
Memory:
2 gigabytes of flash memory (~8 times as much as Spirit or Opportunity)
256 megabytes of dynamic random access memory
256 kilobytes of electrically erasable programmable read-only memory
I wish that instead of now developing a bigger, fancier and more expensive version, NASA would just build swarms of cheap copies and drop them off together with a stationary relay station.
No, I think they should be building a helicopter large enough to fly the first Martian ‘nauts.
NASA must send also a repair & upgrade automatic shop there (along the cheap swarm suggested by Adrian). 3D printers included. The drones must be able to connect (and fly like that) in order to share power and to pick up defective drones or heavier objects. Also redundancy must be paramount. Here a broken blade took down all available drones on Mars. If the newer ones have 8 engines and you have problems with one engine/blade, you shut it down together with the opposite engine and continue flying until more damage takes it down for good or a visit to the repair shop.
Or simply send a mini drone factory.
Coming up next, the first 3D printer on Mars…