If one has a multi-material printer there are more options than simply printing in different colors of the same filament. [Thomas Sanladerer] explores combinations of different filaments in a fantastic article that covers not just which materials make good removable support interfaces, but also which ones stick to each other well enough together to make a multi-material print feasible. He tested an array of PLA, PETG, ASA, ABS, and Flex filaments with each in both top (printed object) and bottom (support) roles.
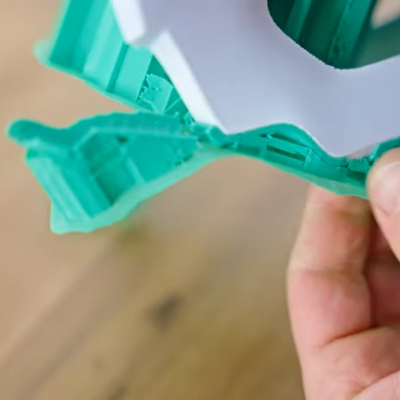
People had already discovered that PETG and PLA make pretty good support for each other. [Thomas] expands on this to demonstrate that PLA doesn’t really stick very well to anything but itself, and PETG by contrast sticks really well to just about anything other than PLA.
One mild surprise was that flexible filament conforms very well to PLA, but doesn’t truly stick to it. Flex can be peeled away from PLA without too much trouble, leaving a very nice finish. That means using flex filament as a zero-clearance support interface — that is to say, the layer between the support structure and the PLA print — seems like it has potential.
Flex and PETG by contrast pretty much permanently weld themselves together, which means that making something like a box out of PETG with a little living hinge section out of flex would be doable without adhesives or fasteners. Ditto for giving a PETG object a grippy base. [Thomas] notes that flexible filaments all have different formulations, but broadly speaking they behave similarly enough in terms of what they stick to.
[Thomas] leaves us with some tips that are worth keeping in mind when it comes to supported models. One is that supports can leave tiny bits of material on the model, so try to use same or similar colors for both support and model so there’s no visual blemish. Another tip is that PLA softens slightly in hot water, so if PLA supports are clinging stubbornly to a model printed in a higher-temperature material like PETG or ABS/ASA, use some hot water to make the job a little easier. The PLA will soften first, giving you an edge. Give the video below a watch to see for yourself how the combinations act.
As there is a Bambu Labs P1S with AMS under the Christmas tree right now, this is handy information.
Thanks
This doesn’t work that well with a Bambu printer, the reason is that there’s only one nozzle and you end up with cross contamination. So the filament that your object is printed gets contaminated with the support material that by design is not compatible. Its subtle but does affect the properties negatively. People have had this happen even with quite insane amounts of flushing. I have an X1C and filed this in the “not for me” category…
Maybe have a spool of nylon cleaning filament loaded, and use that to flush the nozzle between changes? It’d slow things down considerably though.
I have a tutorial of sorts here, you are able to use the AMS printers with many different materials! You just need to set the flushing values to around 800. This is a whole profile, but you can download the print and take a look at the settings. Also note, that you need to check the flushing values each and every single time that you changed the filament. It resets it each time.
Yes, dual nozzle is better for this. But, you don’t have to deal with alignment issues this way. You waste some filament, but it’s not that much waste.
https://makerworld.com/models/620864
Whatever happened to PVA supports? Those seemed like the ideal some they could just dissolve away.
PVA is a real pain to print – it pops off the bed if you look at it to hard. BVOH is slightly better, but very expensive…
What about using it just at the interface between the supports and the print?
They’re still used in commercial/business use, as sometimes they really are the best option, but they are also comparatively, super expensive. Haven’t looked recently, but last time I did, ~$50USD for a 250-300g mini roll vs $15-20 for a 1KG roll of PLA/PETG.
We use PVA quite a lot but it’s crappy to print with. Breaks up a lot.
AFAIK there’s HIPS too, which dissolves in D-limonene. But unfortunately it’s as horrible to print as ABS.
Really? I’ve found HIPS to be great even for general purpose: Easy to print, extremely stiff and tough part, excellent layer and bed adhesion, minimal warping. Only downside is its intolerance for some solvents, but that also makes it easy to glue. Interchangeable with ASA for temperatures: 110 C bed, 60 C enclosure, 240 C nozzle.
I’ve been excited to try PVA for a while, and recently had the chance to now that I have a printer that’s capable of true multiple materials to prevent cross-contamination of filaments in the nozzle.
Long story short, it kinda sucks. I chalk it up to a combination of “maybe I got the cheap stuff”, “maybe it’s too wet”, and “maybe I’m too dumb for this”, but I wasn’t really impressed. Sure, it works, but it’s very particular about printing speeds and temperatures – it’s finicky about what it wants to stick to, and doesn’t like specific paths/geometries when being printed (it really liked to curl back on itself, sticking to earlier traces of the same layer instead of what it was being printed on). Thorough drying helped, but not by much.
It worked well enough for me to get the parts I wanted made, but since then, it’s been sitting in my desiccant box waiting for the day when simple PLA/PETG interfaces won’t do the trick. It’s likely professional machines would do a better job, but those aren’t in my budget as a hobbyist.
Is there something about him I haven’t heard?
Hips ils great as a cheap support for asa on pro printer like the stratasys
Context please?