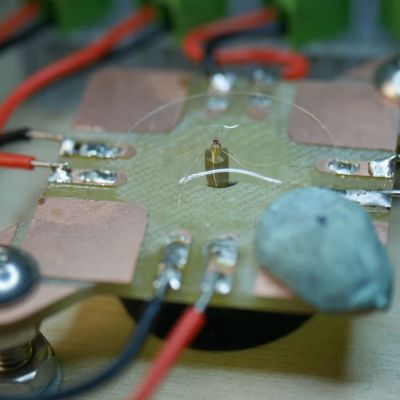
How small can an electric motor be without resorting to manufacturing methods like lithography? In a recent video, [Chronova Engineering] on YouTube tries to replicate the 1960 McLellan motor that fulfilled [Richard Feynman]’s challenge requirements. This challenge was part of [Feynman]’s 1959 lecture titled There’s Plenty of Room at the Bottom, on the possibilities of miniaturization. A $1,000 reward was offered for anyone who could build an electric motor that was no larger than 1/64th inch cubed (~0.0625 mm3), with the expectation that new manufacturing methods would be required to manufacture a motor this small.
As reported in the December 1960 issue of The Month at Caltech, [William McLellan] walked into [Feynman]’s lab with this tiny marvel that took him 2.5 months of lunch hour breaks to build. Weighing in at 250 micrograms and consisting out of 13 parts, it was constructed using a microscope, a watchmaker’s lathe and a toothpick. Surely replicating this feat would be easy today, right?
The main challenge is that everything is incredibly small. The rotor shaft is 90 micrometers in diameter, and the four coils require winding incredibly thin wire at scales where typical manufacturing methods do not apply. Suffice it to say that it takes massive amounts of patience, creativity and the best (stereo) microscope you can get, yet even with modern optics and materials this first attempt mostly failed.
At the end we’re left with SEM shots of this replication attempt and an immense amount of respect for the skills of [William McLellan] who made a working version in 1960 using much more basic tools during his lunch breaks.
Thanks to [J. Peterson] for the tip.
“Infamous”?
The details of this story are truly wonderful. McLellan started opening a large box which prompted Feynman, who had lately been pestered by people who didn’t understand the challenge, to object that anything requiring such a large box couldn’t possibly meet his requirements. McLellan then explained he was unpacking a microscope so Feynman could see the motor he had built.
Feynman also hadn’t bothered to actually budget $1,000 for the prize because he assumed any successful entry was years if not decades away. His wife was not happy.
Wow $1000 in 1960 is $10,600 today.
Painful.
Feynman was simultaneously very impressed and disappointed. The whole point of the challenge had been to inspire someone to invent new manufacturing technology. Unfortunately he misjudged the limits of conventional methods for someone as skilled as McLellan and set the goal just inside the realm of possible. If he had just requested a little smaller, say 1/100th of an inch, he might have gotten what he wanted.
Reminds me of the subject of Technology S-Curves, in that despite the creation of a new, disruptive technology, some organizations can still squeeze a lot of life out of existing methods.
No to mention the effect where new disruptive technology actually comes out worse than the prevailing state of the art, because of the hype curve effect that pushes it onto the market too soon before all the kinks have been worked out, forcing compromises and caveats.
Early entries to the market over-promise and then perform badly, but they get the early investor/adopter money to grow the business ahead of the competition. They simply bet that somebody is going to solve all the problems for them before they run out of business.
Think you might have gone lost with the unit conversion…. 1/64th Inch cubed is aeons smaller than 0.256cm^3, more like 0.064mm^3.
Is it (1/64 inch)^3 or (1 inch^3)/64?
I’ve noticed in that in some dialects (any non-Canadian??) that you wouldn’t call m^3 “metres cubed”, only ever “cubic metres”; even moreso for imperial units where you see the unit symbol “cu. in.” more often than “in^3”. So there wouldn’t be any ambiguity between “(1/64 inch) cubed” and “1/64 (inch cubed)” because the latter would never happen.
It seemed off to me when I threw it in a few online converters, but I’ll admit to having absolutely no sense of scale when it comes to non-metric units.
Yeah, “only 1/64th inch cubed” should be parsed as (1/64th in)^3, not 1/64 (in^3). In Rational Units, that’s a cube 0.4 mm on a side, 0.0625 mm^3, not 1/64th of a cubic inch (256 cubic mm, or 0.256 cubic cm).
While we’re on conversions: 2.5 months of lunch hours would be 50 hours. $10,600 for 50 hours is decent return on investment…
It seems so easy when it’s expressed in Earth Units :) I’ve updated the article correspondingly.
Of those lunch hours, don’t forget that you still need to do some eating in them too, so that makes for even fewer hours worked on it. Supposedly the guy had some help with winding and assembly, but even then. Great return and skills.
The word ‘eon’ is about time. Accuracy is useful with words and numbers.
You also chose the most pretentious spelling possible, which makes it worse
They literally said .0625mm³. I think you may have gotten lost in the reading.
If this is the guy who appeared on I’ve Got a Secret or What’s My Line he went way beyond the challenge’s smallness requirement. “No no Dr. Feynman, I’m unpacking a microscopic so you can see it.” That am badass right theres. Like a Bond villain.
Wish my lunch breaks had been that awesome.
to help with handling and final machining, once the rotor shaft has been turned, I’d be inclined to try embedding it into some kind of dissolvable support (possibly casting wax, although there are very large number of different materials you could use)
also, as far as the assembly issue, I’d be inclined to make a small jig that would bring the parts into alignment. it will be rather easier to put the rotor in initially
… now you’ve got two problems.
Or three, if you use regular expressions to design the jig.
I’m amazed at the determination of the maker of the video!
I wonder if a permanent magnet stepper motor, which is basically what this is, is the smallest motor you could build. Apparently, the drive circuitry isn’t limited in size, so maybe the motor can be smaller, at the cost of a more complex drive circuit. I was thinking an ionic motor could be very small, but that small size limits the maximum working voltage, which may be so low that it’s not expelling electrons sufficiently to work.
Maybe (electro)chemical etching could be used instead of conventional machining to make the tiny parts?