Who else remembers Spirograph? When making elaborate spiral doodles, did you ever wish for a much, much bigger version? [Fortress Fine Woodworks] had that thought, and “slapped a router onto it” to create a gorgeous walnut table.
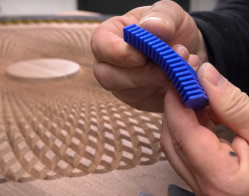
The video covers not only 3D printing the giant Spirograph, which is the part most of us can easily relate to, but all the woodworking magic that goes into creating a large hardwood table. Assembling the table out of choice lumber from the “rustic” pile is an obvious money-saving move, but there were a lot of other trips and tricks in this video that we were happy to learn from a pro. The 3D printed sanding block he designed was a particularly nice detail; it’s hard to imagine getting all those grooves smoothed out without it.
Certainly this pattern could have been carved with a CNC machine, but there is a certain old school charm in seeing it done (more or less) by hand with the Spirograph jig. [Fortress Fine Woodworks] would have missed out on quite the workout if he’d been using a CNC machine, too, which may or may not be a plus to this method depending on your perspective. Regardless, the finished product is a work of art and worth checking out in the video below.
Oddly enough, this isn’t the first time we’ve seen someone use a Spirograph to mill things. It’s not the first giant-scale Spirograph we’ve highlighted, either. To our knowledge, it’s the first time someone has combined them with an artful walnut table.
They were fun with those multicolor pens.
I can’t be friends with anyone who doesn’t understand why someone would do this without using a CNC.
I would not go that far. But I did see this video several days or a week ago, and he mentions himself several times that he should have done it on a CNC, but he does not have one (yet). If he does 2 or 3 similar projects to this, he probably gets tired of this and buys a CNC machine anyway.
A table like this would have been impressive if it was made 200 years ago, at a time when the only available tools were a hammer and a chisel. And up to some handfuls of years ago it still would have made sense to do this with a spriograph. But now, even though he put many hours into it (how many?) the end result still looks like it’s made with a CNC machine, with little added value (to me).
But still, for some people the beauty is in (the effort?) of doing it. Some people make elaborate “paintings” by laying individual grains of sand next to each other, and make beautiful intricate artworks. And as soon as it’s finished they wipe it off the table. (or was this with pencil, those round things, I forgot their name). There is also “diamond painting” which was apparently some kind of rage a few years ago. Such activities are all pretty harmless, and probably more beneficial then playing computer games.
In the interest of being pedantic, he did use a CNC. The CNC (3d printer) made the jig
This is spectacular! I’ve done something similar, albeit with CNC, and cleaning up the little fuzz on the backs of each cut was by quite a bit the most difficult part. His sanding jig is so cool.
My wife’s Gammill longarm quilting machine has an accessory called the “Design Center” that is capable of moving the (motion triggered stitching via x, y encoders) machine around in spirographic patterns, thus quilting in those patterns. It’s pretty cool but certainly not capable of something as big as the subject table. It’s capable of moving a pretty high mass machine around, so could probably move a router. Maybe with an enlarging pantograph setup, I could replicate the table. On the other hand, there’s no way I’m doing that much sanding.
I love this 🙂
It reminds me of Specimens of Fancy Turning
https://publicdomainreview.org/collection/fancy-turning/