No doubt many of you have spent a happy Christmas tearing away layers of wrapping paper to expose some new gadget. But did you stop to spare a thought for the “sticky-back plastic” holding your precious gift paper together?
There are a crazy number of adhesive tapes available, and in this article I’d like to discuss a few of the ones I’ve found useful in my lab, and their sometimes surprising applications. I’d be interested in your own favorite tapes and adhesives too, so please comment below!
But first, I’d like to start with the tapes that I don’t use. Normal cellulose tape, while useful outside the lab, is less than ideally suited to most lab applications. The same goes for vinyl-based insulating tapes, which I find have a tendency to fall off leaving a messy sticky residue. When insulation is necessary, heatshrink seems to serve better.
The one tape I have in my lab which is similar to common cellulose tape however is Scotch Magic Tape. Scotch Magic tape, made from a cellulose acetate, and has a number of surprising properties. It’s often favored because of it’s matte finish. It can easily be written on and when taped to paper appears completely transparent. It’s also easy to tear/shape and remove. But for my purposes I’m more interested in it’s scientific applications.
Here’s a neat trick you can try at home. Take a roll of tape (I’ve tried this with Scotch Magic tape but other tapes may work too) to a dark room. Now start unrolling the tape and look at interface where the tape leaves the rest of the roll. You should see a dim blue illumination. The effect is quite striking and rather surprising. It’s called triboluminescence and has been observed since the 1950s in tapes and far earlier in other materials (even sugar when scraped in a dark room will apparently illuminate). The mechanism, however, is poorly understood.
It was perhaps this strange effect that led researchers to try unrolling tape in a vacuum. In 1953 a group of Russian researchers attempted this and bizarrely enough, were able to generate X-rays. Their results were unfortunately forgotten for many years, but were replicated in 2008 and even used to X-ray a researcher’s finger! As usual Ben Krasnow has an awesome video on the topic:
In my lab however I mostly use Scotch tape to remove surface layers. In certain experiments it’s valuable to have an atomically flat surface. Both Mica and HOPG (a kind of graphite) are composed of atomically flat layers. Scotch tape can be used to remove the upper layers leaving a clean flat surface for experimentation.
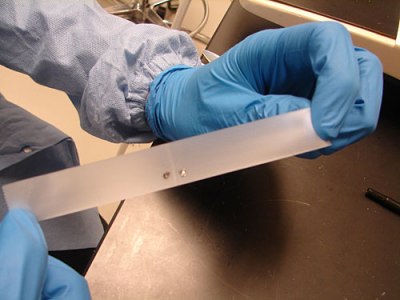
Researchers have also modified this technique to produce graphene. Graphene is composed of single carbon layers and has a number of amazing properties, highly conductive, incredibly strong, and transparent. For years producing small quantities of graphene provided difficult. But in 2004 a simple method was developed at the University of Manchester using nothing but bulk ordered graphite (HOPG) and a little Scotch tape. When repeatedly pressed between the Scotch tape, the Graphite layers can be separated until eventually only a signal layer of graphene remains.
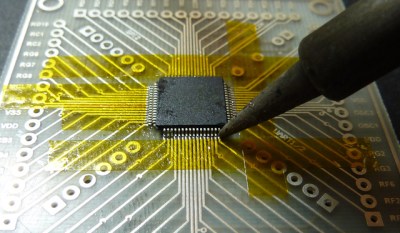
The other non-conductive tape I use regularly in my lab is of course Kapton tape. While Kapton is a Dupoint brand name, it’s basically a polyimide film tape which is thermally stable up to 400 degrees C. This makes it ideal for work holding in electronics (or masking out pins) when soldering. You can also use it for insulating (though it’s inadvisable for production applications). Typically polyimide tape is available under a number of dubious synonyms (one example is Kaptan) from a variety of Chinese suppliers at low cost.
Carbon tape is conductive in all axes. This means it you can create a electrical connection by simply taping to your devices. It’s resistance however is somewhat high. I’ve most commonly come across this when using electron microscopes. Carbon tape is used both to keep a sample in place and create an electrical connection between the sample and the sample mount.
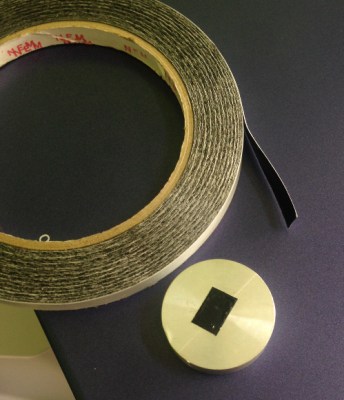
Other conducting tapes are available with lower resistance, creating a electrical connection without soldering is valuable in a number of situations. Particularly when heat might damage the device. One example of this is piezoelectric materials. Not only does solder often bond poorly to ceramic materials, but it may also depole the material removing its piezoelectric properties. I tend to use conductive epoxies in these situations, but conductive tapes appear to be an attractive option.
Aluminum tape is commonly used for (heat) insulation in homes. It’s therefore very cheap and easily available. As well as conducting heat aluminum tape of course also conducts electricity. Around the lab this can be pretty handy. While the adhesive is not conductive, making it less attractive for connection parts, I’ve found aluminum tape great of sealing up holes in shielded enclosures. It also makes a great accompaniment to aluminum foil which is used to provide ad-hoc shielding in many scientific environments. Copper tape is also easily obtained, though slightly more expensive.
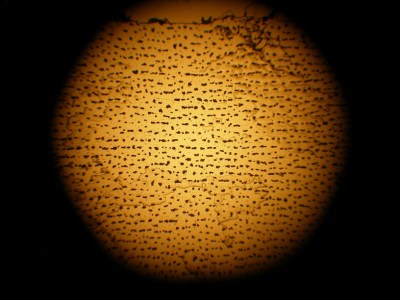
A much less common, but far cooler conductive tape is so called Z tape. This tape is composed of regular double-sided tape impregnated with spaced conductors. The result is a tape that conducts in only one direction (from the top to the bottom). This makes it similar in structure to a zebra strip, commonly used to connect LCDs. Z tape is unfortunately pretty expensive, a short 100mm strip can cost 5 dollars. What exactly 3M had in mind when creating Z tape is unclear. But it can be used for repairing FPC connectors on LCDs or in other situations where soldering is impractical.
One of the more awesome applications is Jie and Bunnie’s circuit sticker project. The kits are designed to allow kids to assemble circuits simply by sticking components together. Z tape is ideal for this, as it allows multiple connections to be made using the same piece to tape.
I couldn’t write an article on tape without mentioning the somewhat apocryphal “Invisible Electrostatic Wall” incident. A report at the 17th Annual EOS/ESD Symposium describes a “force field” like wall that appeared during the production of polypropylene film. While the story seems slightly dubious, it reminds us of the surprising applications and utility of tapes.
Next time you’re sending off a package or ripping open a package, spare a thought for the humble tape that holds it together.
Interestingly enough I’ve got a low cost X-Ray based on triboluminescence in the pipeline. Pulling a vacuum in the cassette that holds the tape will prove…interesting
If you impregnate breather cloth, with epoxy resin from max bond it will do the tribo-luminescence when torn. It is very bright visible in a garage midday.
Breather cloth?
http://lmgtfy.com/?q=breather+cloth
You can buy miniature X-ray tubes for about $100 from ebay… Since you’d be needing power for the vacuum pump anyway, it shouldn’t be problem…
Yeah but those are scary high-energy X-Rays…AKA: NOPE
The X-Ray energy is directly proportional to the voltage you apply to the tube.
IIRC, low-energy X-rays are actually more damaging to things than high-energy. That’s why the dentist puts on that lead coat — everything he gets has bounced around and “slowed down”.
Cool rundown Nava!
I also love fiberglass tape for that extra tensile strength, and roofers tape for sealing vacuum bags in composite layup.
Going to have to add those to my shopping list! While writing this article I also came across amalgamating tape. I’ve not used it before but it looks interesting. It basically sticks to itself almost like it forms a single piece of material. Might be useful for ad-hoc water tight seals.
Self-amalgamating tape was / is often used on coaxial cable for radio transceivers for exactly that purpose.
If you’re talking about the black coax sealant: yeah, it works. It’s rather nasty to remove, though. In some cases it might actually be easier to cut the coax and solder on a new connector instead of trying to get that gunk off.
That stuff reminds me of a toddler with a ball of sticky tape stuck to their hands.
It was called ‘mastic’ tape when I used it, but that appears to be 3M name. Nasty, gooey stuff. Definitely keeps out water, though.
Silicone amalgamation tape is used for quick pipe fixes under various brand names for that purpose. I used it last year to fix a steam condensate return line during the winter! Worked swell.
Yeah it’s one of my favourite tapes.
It also makes great ad-hoc strain relief on cables too. Rubbery and flexible, just build it up near the connector and then taper down the cable about an inch.
AKA self-vulcanizing rubber tape (also available in vinyl, I believe). Cheap at your larger electrical supply stores and sometimes at Home Depot/Lowes. For weatherproofing connectors, it can’t be beat. Good stuff.
Self amalgamating tape is really useful when you need a continuous insulating layer like for high voltage work. It is not only sticking to its self it actually does eventually become a single mass of silicone based material. It may not be as removable as standard electric tape but is removable if needed. This stuff is a level above the sealant used on coax by ham radio operators , which is sort of a cross between silly putty and tar! and is a sticky black material that gets stickier with increased heat. The self vulcanizing/amalgamating tape is a smooth not so sticky (except to its self) product that is much cleaner and less tar like than the coax seal product. I have used both. I also recommend checking out 3m branded structural adhesive double sided tape with foam center. it comes in different strengths and thicknesses if applied to clean solid substrates and firmly pressed on assembly this stuff is supposed to be as good as a welded seam! Its used to assemble airplanes and some parts of cars.
Using vinyl “electrical tape” as an insulating tape was a firing offense in my shop. It has marginal utility as a marking tape, it’s passable as an overwrap for silicone “self-fusing” tape, and in a pinch can be used to make a running shoe into a slider for curling. But under no circumstances is it acceptable to use as electrical insulation.
Word of advice: Never visit Paraguay (or most South American countries) :-)
https://www.flickr.com/photos/flyinglow/14499888349
Well 3M Scotch 33+ is listed as Dielectric Strength‎ ‎of 1150 V/mil, and 7mils thickness, even 3M Economy Vinyl is rated for 600V.
Without knowing why PVC/vinyl electrical tape was considered unacceptable it seems a strange offense, I know that electrical tape isn’t perfect, but its dielectric strength suggests it is suitable for low voltage insulation.
It’s not the tape, It’s the glue. the vinyl tape has horrible glue. the isolating aspect is ok
yea, it’s horrible stuff. I’ve never attempted professional electrical work, but for my own stuff I’ve always assumed that correct approach is just to properly terminate the cable.
Basically the problem I’ve found it that the glue is poor and the Vinyl has a tendency to pull itself off. So it doesn’t really create a tight seal round the cable (which means it’s easy for moisture to get it) and might even fall off (which is just dangerous).
The sort of “electrical tape” you are talking about was never intended to be an insulator. It’s for wrapping a collection of wires together for form a harness so that the collection of wires (or harness) can be restrained so that the insulation on the wires isn’t damaged by movement or vibration.
A side effect of ever decreasing skills in the labor force I suppose.
Even as a “harness”, I felt it was a very poor product. Especially over anything resembling long term applications. My father used to use it and taught me the correct (I suppose) way of applying it. Over time, the adhesive loses its grip, turning into a gooey mess or a superbly lacquer-like substance impossible to scrape off while the vinyl itself falls apart. Worse, my mother has used it to “repair” book spines. Aaaaggghhhh!
It is relegated to the same place in my tool box as *real* duct tape. Excellent for immediate, emergency, or MacGyver repairs and nothing more.
The common $2 electrical tape is not like the original and will fall apart very quickly. It has too low a temperature stability range and as soon as it gets any heat the bonding agent turns into lubricant and the whole thing collapses.
The original had far less elasticity and the bonding agent was stable over a wide temperature range.
When used properly – most of the force holding it together is rotational and the bond doesn’t need to be as strong but the wrapping *has to be done* the right way.
The real version is still available but be prepared to pay much more than the $2 a roll you pay for the rubbish tape – for example –
http://www.tesatape.com.au/industry/automotive/electrical_systems/wire_harnessing
I had the same idea until I tried 3M Super 33+ (and later Super 88). It’s glue doesn’t have these issues, and it works much better than cheap tapes when it’s cold. By the way, the motorbikes I’ve had (Honda XR250 and Kawasaki KLX250) had their entire wire harnesses wrapped with vinyl tape.
PVC electrical tape exists for only one purpose – to comply with NEC code. The code dictates that you replace bare wire insulation / covering with the same material and rating and electrical tape satisfies this requirement. Electrical tape is probably one of the most misused tapes on the market. Every other use of electrical tape in the original article and in these replies is a misuse of electrical tape. Electrical tape can be used to wrap a collection of wires together into a harness but it only works well this way because as you wrap the tape is overlapped and stuck to itself just like it would be if you were insulating a bare wire.
Electrical tape leaves a sticky residue because it’s not designed to be applied and then removed. Electrical tape is designed to be applied and never removed. The adhesive is designed to adhere to itself. When properly applied by wrapping the tape around a wire with plenty of overlap so that it bonds to itself, electrical tape will stay where it belongs for many years.
Self fusing tape is also a product driven by the same NEC code that states that you replace bare wire insulation / covering with the same material as the original insulation. The tape, or more commonly called compound by old Electricians, was originally applied to cloth covered wiring then the wire was wrapped with cloth tape. The compound replaced the rubber part of the original insulation and the cloth tape replaced the fabric cover of the original insulation. Even today, if an Electrician comes across older cloth covered rubber wire he is supposed to cover any bare wired with compound and then cloth tape.
It’s only suitable for securing & streamlining your wires to the fish tape, pull string, etc.
buying 33 was grounds for termination for my employees.
I once worked with a guy that bought a dozen rolls of 33 just to get a 3M cooler. Boss let him go for that!
We used real Scotch 33+ to wrap exterior coax connections (on ham radio antenna installations), and, if you apply it per instructions, found it held up well and kept the connections (relatively) weather-tight. Not as good as self-vulcanizing with a vinyl overwrap, but better than leaving the connection unprotected.
BUT…you have to apply it per the directions, which emphatically tell you not to tear it off the roll at the end of the wrap. Stretch it all you want as you wrap it, but CUT it off the roll and make sure that the last 2-3 wraps are not stretched.
The no-name stuff you get for $2/roll is junk and only the Scotch 33+ brand survives exterior exposure. The cheap junk just unrolls off the connection a few weeks after you put it on. Guess how I know this :-)
Exactly. If you follow the instructions, it works great. They also say: “The tape shall be applied in half-lapped layers with sufficient tension to produce a uniform wind (for most applications this tension will reduce the tape’s width to approximately 5/8 of its original width).” Once I got this down, my tape-wrapped motorbike wire harnesses (after troubleshooting some issues) looked better than factory.
It actually makes a great band-aid and has magical healing properties (*grin*), probably just the glue and pressure holding the wound closed.
I find super-glue to work the best for me.
Nothing beats super glue … if you intend to glue your finger together.
When I was in my teens and 20’s (and of course knew everything) thought that the rat-tail or pig-tail splice was normal since Twist-on wire connectors were a common appearance. And naturally “Electrical tape” was to be used when you didn’t have twist-on connectors.
upload.wikimedia.org/wikipedia/commons/thumb/6/69/Array_of_twist-on_wire_connectors_aka_wire_nuts_in_different_sizes.jpg/330px-Array_of_twist-on_wire_connectors_aka_wire_nuts_in_different_sizes.jpg
The resulting mass was an abomination that required duct tape to keep it together. (Hedge Trimmer. Extension cord. Moment of inattention. Moment of surprise.)
I even got to the point to “refine” the rat-tail to have the cut ends of the wire off-set the end twists before taping. Then hook and twist technique.
Finally learning a connection that we SHOULD be using.
https://upload.wikimedia.org/wikipedia/commons/thumb/f/f7/Western_Union_splice.jpg/330px-Western_Union_splice.jpg
That said, Heat shrink tubing is expensive. Local “shop” Fry’s sells 1 yard/.913 Meter run for $1.99.
I got an assortment of sizes (total count 150pcs) from fleabay for a mere…..$3
Anisotropic conductive tape like the Z-tape are designed to connect chips to footprints on a circuit (glass, flex or a PCB)– particularly for connecting chips and flex circuits directly to glass (LCD displays). It allows bonding chips to glass or flex to glass (or really any combination of chips, flex, glass and PCBs) without bulky connectors.
It’s not clear to me what level of miniaturization requires anisotropic conductive tape (cell phones? Google Glass?). I’d guess it’s used somewhere in cell phones as they’re the most obvious driver of LCD display miniaturization. If a display has any chips on the glass or flex-on-board connections, they’re either being accomplished with anisotropic conductive tape or a similar anistotropic conductive epoxy (that is applied like a tape and then heat cured).
hmm… can Z-tape be used instead of soldering for BGA components?
Try it and report back?
My guess is no. The problem you would have is placing the chip precisely enough, without the surface tension of the solder to “pull it into place”.
No. Example: WLCSP36 has 6 by 6 balls with 0.4mm spacing. You’d need very small contact points and a well-defined tilt of the chip against the direction of the tape and then you’d end with something like 32µm trace width / 32µm clearance.
Stacking of the tape might barely work which would permit to stretch the ball pattern in one direction and yield a stretched and mirrored contact field.
Finally you want supply rail bypass capacitors close to the chip (opposite PCB side or right next to the package on the same layer) which renders the Z tape approach for general BGA fanout quite useless.
Don’t forget Pb tape. It is useful in chemical environments which will attack Al tapes.
You can still get that? I thought they stopped producing it due to “environmental concerns”.
I still see sheets of lead for house roof flashing on sale at the hardware store. No warnings about it being pure lead lol and no packaging – just sitting there exposed, waiting for the next kid to wipe his hands on before putting his hands in his mouth.
[RĂ–B] I’m hearing a “Think of the children” vibe from this post, to each their own opinion. Lead is excellent material to work with if common sense is involved. So is Arsenic. Fact of the matter is we vilify materials only after learning. Anyone raised in the 80’s can attest most playgrounds were log based structures made of “green wood” aka pressure treated Chromated copper arsenate. We can thank Dr. Seuss and his work on Green Eggs and Ham for that. But now our modern society, Political correctness and SJWing… doesn’t allow for public scolding, “keep your hands to yourself”, “don’t touch things that aren’t yours”, “this isn’t the playground”. Observing a ill-raised child doing round-house kicks and screaming bloody murder in a department store is a natural occurrence now. I say let them lick the lead roof flashing.
lol – well I am pretty complacent with lead as I still use tin/lead solder. But apparently for kids it can cause development delays and a reduction in IQ so that to me would be a bad thing. For older people I causes sanity issues but hey that’s not an issue for me.
I still think the lead sheets should packaged – young parents most probably don’t know that roof flashing is made from lead.
If I see it again then that can be my memory cue to ask about it being better stored. I will probably be looked at like a dotty old man but perhaps hey will still do something.
Oh yes, it is still used by hard chrome electroplaters among others.
Hello clueless – you can still buy lead based solder too. Lead isn’t outlawed as some clueless people like yourself like to claim, the controls are in place for mass produced items not exempt (special purpose where lead works better, military stuff that are to be working in 40-50years). And that is a good thing.
Here’s some tape used for an artificial muscle. A plastic structure is covered by a stretched VHB4905 tape by 3M, this in turn is covered by carbon paste, by passing some kilovolts in the carbon paste it squeezes the tape acting as the dielectric and gives it some slack in the other direction, the structure tries to get flat and moves, repeat…
https://www.youtube.com/watch?v=p9WZIJWQVqE
Personal favorite is aircraft “speed tape.” Of course, getting some to play with is a little difficult as it’s supposedly very expensive.
It’s only expensive because it’s certified, which of course you need if it is being used on an aircraft. Sometimes you can get some time-ex rolls from an FOB, if you know someone, and they trust you. Mostly they don’t, and I had to destroy many rolls over the years because the place I worked didn’t want them finding their way back into the market.
Is that the stuff that looks like heavy duty duck tape? (strong rubberized fabric, with good adhesive) I saw airline ramp employees use it, to patch damaged freight containers.
Ahh Duck Tape – my favourite. I use it to stop my ducks from flying away.,,,,
ROFL – Still laughing – made my day
This stuff?
http://www.uline.com/Product/Detail/S-20343/3M-Single-Coated-Tapes/3M-8671-Polyurethane-Protective-Tape-3-x-36-yds
Without Z-tape we would still be using elastomeric connectors to connect circuits to LCD on glass. Thanks to Z-tape or so-called “Anisotropic Conductive Film” (ACF) flex circuits can be attached to chip-on-glass circuits. They are practically everywhere today due to being extensively used in LCD modules to touch panels.
Besides gaffa, my most essential tape is double sided. It makes it super easy and quick to mount/build things: Attach the part you want to mount temporarily with double sided. Then it stays nicely in place while you really fix it with some screws.
Very High Bond 3M Foam Tape saves the day so many times.
There was one tape I omitted as it’s not an adhesive tape, but is kind of interesting. That’s PTFE tape. Also known as plumbers tape. PTFE is well known for it’s excellent dielectric properties, and is therefore a great insulator. But it also has some interesting scientific applications. By stretching it out and applying a spark across it you can create micron sized holes easily. By placing this between two water filled chambers filled with a salt solution, you can create an ionic current (in the presence of a bias voltage). The micron sized aperture can then be further restricted by creating a bilayer (called black painted bilayers in this case) and embedding a protein nanopore. You then have a nanoscale aperture to experiment with. This can be used for either investigating the properties of nanopores, or as a basis for single molecule analysis techniques. Each time a large molecule passes through the nanopore you see a blip as it blocks the ionic current.
Also adhesive backed teflon tape. My uncle gave a roll to me as a kid and I put it on the runners of my sled. Whee…
One possible cause for the “invisible wall”:
https://en.wikipedia.org/wiki/Plasma_window
Triboluminescence is a phenomenon in which visible light is emitted from elastic and plastic deformation of various substrates as well as fracture of crystals. Triboluminescence is distinguished from electroluminescence – light accompanying an electric discharge. “Static cling” and pulling “Scotch” tape from a dispenser will result in electroluminescence. The aurora borealis is a grander example. Triboluminescence is not associated with an electric discharge, chemical oxidation (burning), or chemiluminescence, although such separate effects may occur with some materials that also exhibit triboluminscence. Measuring a change in the electric field in the vicinity of the luminescence is one way to distinguish electroluminescence from triboluminescence.
Electroluminescence occurs when the bonds are broken as the material is crushed. Electron charge may preferentially exist on one side of the fracture relative to the other and then discharge across the gap giving a spark.
In some cases, both phenomena may occur at the same time.
Prof. John T. Dickinson of Washington State University, who has published over 50 papers on triboluminescence, has given a demonstration in his classroom where he ignites a methane/air mixture using the electroluminescence coming from Scotch tape being pulled rapidly from its roll. Prof. Dickerson has also described a technique he has used to distinguish triboluminescence from electroluminescence. It requires using a UV spectrophotometer to examine the light from the reaction. If there is a broad band of emission over the UV/Vis region, it’s triboluminescence. If there are specific UV peaks associated with nitrogen lines, it’s electroluminescence from the electric discharge exciting the nitrogen in the air.
According to Dickinson, a number of years ago at the Huntsville, Alabama plant where they mix dry components for solid fuel rocket propellent, someone installed a window in the mixing chamber to see how the blending was progressing. When they looked through the porthole, they noticed there was a glow coming from the rocket fuel. Following an investigation it was determined that triboluminescence, not electroluminescence occurred during the mixing of the rocket fuel… accompanied by a huge sigh of relief, I suspect. An industrial glass crusher also emits triboluminescent light.
One of the oldest references to triboluminenscence is from Francis Bacon in Advancement of Learning (1605) on light emission from cane sugar. However, the phenomenon was probably witnessed much earlier. Sugar had been prepared in India and Persia for centuries and was only introduced into Europe in the 12th century, although its use was not widespread until the 16th century. Scientific tests on various materials (sugar, rock salt, alum, coral, jasper, potassium nitrate, granites, etc.) for triboluminescence were being conducted as early as 1657. Robert Boyle reported on some of his work on triboluminescence in 1663.
Some references of interest:
1. E. Newton Harvey. A History of Luminescence: From the Earliest Times
Until 1900, The American Philosophical Society, Phil. PA, 1957.
2. G. Alzetta, et al. “Excitation of Triboluminescence by Deformation of
Single Crystals”, Phys.Stat.Sol. (A), 1, 1970, pp. 775-785.
3. J.T. Dickinson and E.E. Donaldson. “Autographs from Peeling Pressure
Sensitive Adhesives: Direct Recording of Fracture-induced Photon
Emission”, J. Adhesion 24, 1987, pp. 199-220.
4. Ma Zhenyi, Fan Jiawen, and J.T. Dickinson. “Properties of the Photon
Emission Accompanying the Peeling of a Pressure-Sensitive Adhesive”,
J. Adhesion 25, 1988, pp. 63-77.
5. E.E. Donaldson and J.T. Dickinson. “Autographs from Peeling Fiber
Reinforced Pressure Sensitive Adhesives: Correlation with Failure
Mechanisms”, J. Adhesion 30, 1989, pp. 13-23.
As I read, everything I thought of that I could possibly add, was eventually mentioned. Spectacular article!
And I’m so glad to find a reference to the “invisible wall”. Read about that many years ago, forgot where. And mentioned it just a couple of days ago to my lady, while explaining why her Scotch tape sucked most of the glitter off her project at a short distance. She thought I was making the story about the “invisible wall” up. Can’t blame her, I’ve pulled her leg before. But now I can show her the article. ;)
Gaffer tape is a matte cloth tape that usually comes off cleanly, great for temporarily securing cables. Eternabond tape is used for repairing RV roofs. VHB tape (mentioned in another comment) is good for securing solar panels to RV roofs.
+1 for Gaffers tape! I swear by that stuff in some applications.
Unfortunately some members of another department over use it and I’m left cleaning off gunk when doing repairs.
When I was in the Canadian Army as a Field Engineer. We were on a exercise in the Rockies. It was so dark that you could see the green blueish glow of the high voltage lines But.
It was when I started ripping some paper towels that I saw that they gave off little with sparks.
That all was so cool.
You mentioned Ben’s “X-ray Tape” video, but not his “Gecko Tape” video? https://www.youtube.com/watch?v=9XQfYKYO380
Still a good article, though ;)
My favorite tape is the two-sided adhesive foam tape. Together with corrugated cardboard from boxes, it’s the perfect prototyping material for all sorts of robots and similar mechanisms, and much more convenient than hot glue.
Those of your downplaying electrical tape using it as a weather sealant…really? You thought that stuff sealed for moisture intrusion?
In the industries in which I’ve been lucky enough to be employed it was never used as the primary adhesive or termination. It comes in handy to install connections as an additional strain relief used with wire nuts for electrical connections. Properly deployed (which is the only deployment I know how to do) the stuff will last for years. Even when it does lose adhesion, the wire nuts that are properly installed hold the connections.
It’s not the material, it’s the deployment. If you’re using it as a permanent sealant without the benefits of other connections, you are using it wrong. If you use is as a weather seal, you’re kidding yourself.
U don’t try ferrited tape(VHS tape)? #FerromagneticTape
Testing this thing
</HTML that doesn’t work>
I seriously just recently thought about doing a video or something on different tapes I use in my hobby and professional careers and then here’s this article. Some of them have been covered here and by other posters. But I’ll recap my go-to tapes anyway. And the caveats are they must be used according to the datasheets.
3M scotch 130C linerless rubber splicing tape – We use this for all kinds of stuff, self vulcanizing to an extent, but mostly used for temporary HV insulation. We use good ol’ 33 for temporary insulation over gator clips or banana plug ends when extending banana cables. But only to the taps rated voltage, then we opt for 130C
Kapton is good for the things in the article and for making a low voltage isolation buffer under a PCB that’s mounted over metal shielding, wrapping transformer windings, soldering, etc.
3M Scotch 411 and 414 “heavy duty outdoor mounting tapes” similar to VHB (which just stands for “very high bond”), but more like super glue on a roll. Think reattaching fenders to a car.
Adhesive transfer tape. Its like basically just adhesive on a roll, once you pull the liners away, you basically have a super strong layer of glue. It’s what you would use to attach a membrane touchpad to a surface or even making membrane touchpads themselves. You can get it in “repositionable” which is like post-it note glue, to “you’re not getting this adhesive off without a blowtorch” strength. You can buy huge rolls on your favorite online auction houses of china made stuff and save a bunch of money.
As mentioned before I like the double sided foam tape. Great for attaching PCBs or batteries to things!
Yes I completely forgot about that when writing the article. I generally use the little pre-cut squares, they’re particular great when assembling kits.
I use a lot of masking tape or painter’s tape. It can hold wires/parts together until they are affixed, has decent thermal stability and pretty high tensile strength. Since it’s does not stretch so much it’s also useful for prototyping with cardboard or other 3D shapes (enclosures). I also use it on my heated 3d printer bed.
It also protects finished parts from scratching.
In a pinch for insulating live nodes from accidental touches while working on stuff.
Of course its main advantage is that it leaves little residue.
Gaffer tape…..because duct tape is for amateurs. it is my go to tape for any short term repair. doesnt love water. sticks really well to its self but removes easily from other surfaces…unless it has been applied for a few years…then the adhesive turns to hard dust.
https://www.hollywoodreporter.com/news/ross-lowell-dead-oscar-recipient-inventor-gaffer-tape-was-92-1190871
The other workhorse of the concert touring business is e-tape…used for marking/labeling and temporary dressing/attaching/bundling cables. Personally, i find e-tape the biggest offender of avoidable waste produced on a show. Not uncommon for a large tour to blow through a few dozen rolls every tour stop. Our shop used to have a solid ball about 10″ of e-tape removed off of trusses and cables. It must have weighed 10 lbs. someone drilled finger holes in it.