It’s tough times for 3D-printing. Stratasys got burned on Makerbot, trustful backers got burned on the Peachy Printer meltdown, I burned my finger on a brand new hotend just yesterday, and that’s only the more recent events. In recent years more than a few startups embarked on the challenge of developing a piece of 3D printing technology that would make a difference. More colors, more materials, more reliable, bigger, faster, cheaper, easier to use. There was even a metal 3D printing startup, MatterFab, which pulled off a functional prototype of a low-cost metal-powder-laser-melting 3D printer, securing $13M in funding, and disappearing silently, poof.
This is just the children’s corner of the mall, and the grown-ups have really just begun pulling out their titanium credit cards. General Electric is on track to introduce 3D printed, FAA-approved fuel nozzles into its aircraft jet engines, Airbus is heading for 3D-printed, lightweight components and interior, and SpaceX has already sent rockets with 3D printed Main Oxidizer Valves (MOV) into orbit, aiming to make the SuperDraco the first fully 3D printed rocket engine. Direct metal 3D printing is transitioning from the experimental research phase to production, and it’s interesting to see how and why large industries, well, disrupt themselves.

Direct metal 3D printing fuses metal powder particles layer by layer into dense objects and does not require post-print infusion like binder-based methods. The selective melting of the particles can be achieved through an electron beam (Electron Beam Melting, EBM) or lasers (Direct Metal Laser Melting, DMLM, synonymous to EOS’s trademarked DMLS). Laser-based direct metal 3D-printing is currently experiencing an extreme push since it typically outperforms the previously hyped EBM technology in terms of resolution and surface finish. DMLM saves the need for a vacuum chamber, but since it requires several high power laser units to catch up to the productivity level of a single beam EBM machine, as well as an inert gas atmosphere and post-print heat treatment, it is also more expensive.
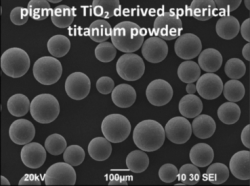
This is, obviously, not the kind of push that puts cheap devices on your desktop. DMLM machines cost about $1M and above, and besides the acquisition price of a machine, direct metal 3D-printing is also a process with a ludicrous per-unit-cost. The materials, fine, high purity metal powders have to be generated through gas- or plasma atomization to obtain consistent and spherical particles. Then there is the printing process itself, which fuses the pricey powders into solid shapes utilizing one or more powerful fiber lasers for several days or even weeks. What comes after that is a classic, manual process of cleaning, annealing, support structure removal, subtractive refining and surface treatment. The high per-unit-cost directly reflects the efforts that must go into the processing of each and every individual particle inside a 3D printed product, and while those efforts sum up quickly, they scale rather poorly.
So, does that mean labeling additive manufacturing as an efficient and waste-free manufacturing method is naively wrong? That depends on the application. The Yb-fiber-lasers commonly used in DMLM machines are a surprisingly effective way of fusing metals and can stay in continuous operation for more than a decade due to their very long MTBF. However, even at very high, experimental build rates of up to 500 cm3 (30 inch3) per hour, their advantage mostly unfolds in high complexity and low quantity applications. So on the one side, 3D printing a simple steel component that was formerly mass-manufactured in a casting process will still cost 10 to 100 times more with DMLM. On the other side, a 3D-printed functional group that combines tens to hundreds of cast or subtractively manufactured parts into a single piece can be significantly cheaper than its traditional counterpart. Eventually, what makes companies like SpaceX, GE and Airbus buy into the technology are the non-trivial implications and cost lever effects:
Lightweight Construction
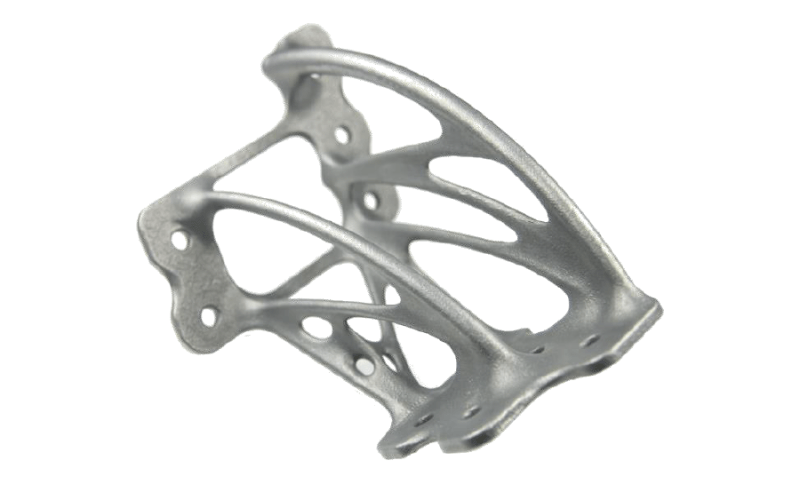
Additive manufacturing allows for complexity. Its ability to generate arbitrary shapes and structures enables lightweight construction techniques, where excess material is shaved away from a design based on mathematical and natural models, often referred to as „bionic design“. Since in aviation, even minor weight savings accumulate to massive fuel savings over the course of a single long-distance flight, aircraft manufacturers are going to great lengths when it comes to weight reduction.
Compliance And Quality Assurance
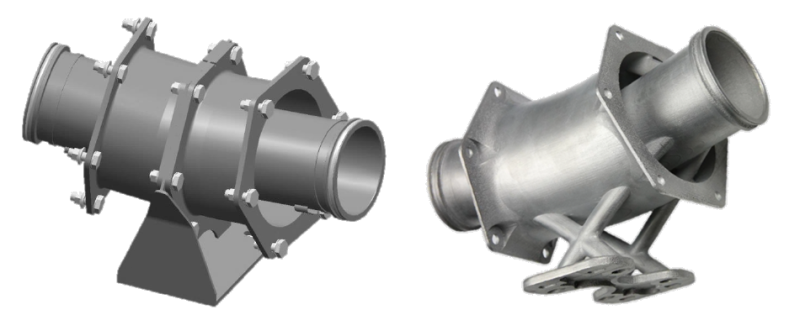
A single functional group in a passenger airplane can contain hundreds of individual parts, all of which undergo the internal process of quality assurance and must obtain FAA approval going into service. Baking a few dozen functional parts into a single 3D-printed unit helps to reduce costly and time-consuming compliance and QA efforts.
High-Temperature Materials
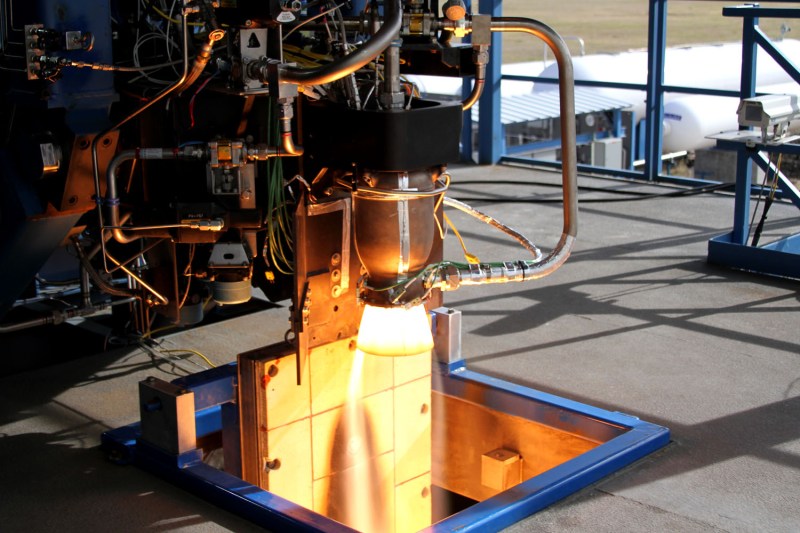
Extreme temperature applications, from cryogenic fuel valves to white-hot engine bodies, require very temperature and corrosion resistant materials, such as cobalt-chromium and nickel-based superalloys or titanium and titanium-based alloys. These materials are very challenging to machine subtractively while they can be almost effortlessly processed via DMLM.
Cooling channels
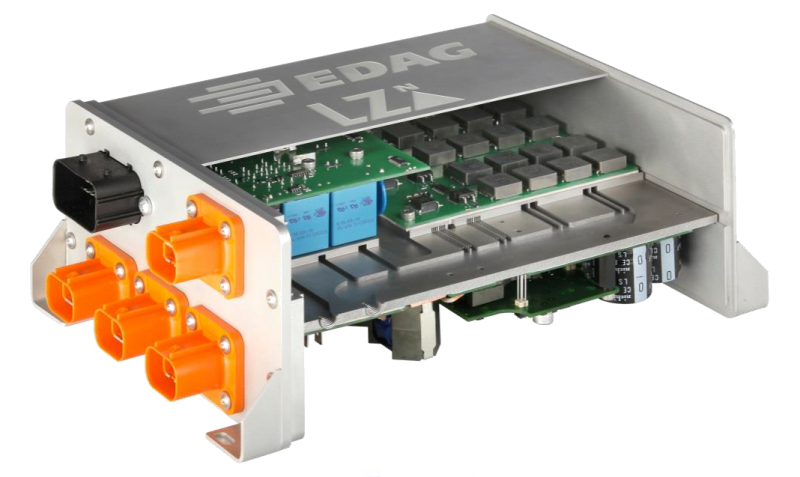
3D-printing allows internal cooling channels to be embedded in thermally stressed components, extending part life and improving efficiency in electronics and thermodynamic applications. Internal cooling channels also can also help to increase the throughput of injection molding tools.
It’s what you make of it
There are clearly a number of products, such as implants and prosthesis, efficient cooling solutions for power electronics, and lightweight frame construction in automotive which are uniquely suited for direct 3D-printing in metal. Currently, they aren’t in the cost-effective operating point of direct metal printing. But they will eventually get there, either by piggybacking on larger industries or on a wave of innovation driven by makers and hackers.
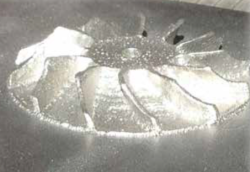
Just like MatterFab demonstrated, low-cost DMLM machines are – somewhat possible, but need drive, ideas, the the right applications and funding to become productive and viable. Still, others continue where MatterFab seemingly left off. Aurora Labs — a startup team that happened to have invested more time into their technology than into their cancelled Kickstarter campaign — recently released some footage from their DMLM printer, and it looks like they are getting there. I leave you with this short snippet of a scratch built Ti6Al4V printing DMLM machine, printing a quite decent impeller.
It is rather simple math.
In production.
For parts for rockets, planes, jet engines this makes sense.
For parts for car (outside of low volume exotics) washing machines, and so on it does not.
Frankly even for rockets, planes, and jet engines it will only make sense some of the time and only for some of the parts.
For rockets, every bit of weight counts. If you can make your engine a bit lighter, you have quite a decent win. Due to the https://en.wikipedia.org/wiki/Tsiolkovsky_rocket_equation
So more efficent/lighter engines for rockets with 3D printing will stay in that area, as you will win it back in delta-V (fuel)
The key is – rocket motors are a low volume (mostly) disposable products where the cost of the 3D printing is relatively negligible compared to the rest of the budget. So 3D printing parts makes sense if it brings additional benefits.
For pretty much everything else casting and machining will be both faster and cheaper.
I can see this changing eventually. If a reusable first stage became popular, as SpaceX is already proving possible, it may be plenty advantageous.
Then again, the Space Shuttle was originally touted as cheaper and reusable and a whole host of previously unknown issues popped up. Could be completely different though, who knows.
“I can see this changing eventually. If a reusable first stage became popular, as SpaceX is already proving possible, it may be plenty advantageous.”
Not really. It is all about the numbers and a reusable first stage will decrease the number of engines built.
Even if rockets become as popular as jet aircraft the volume will stay low compared to cars or smartphones.
It is a question of time == money when you are in mass production.
The issues with the Space Shuttle were basically the US Air Force adding extra demands, for things like reaching the orbits they wanted to put spy satellites in. They were putting in quite a bit of the budget, so they got their way. That meant major changes, and a few ugly kludges, the Solid Rocket Boosters being the main one.
The original design for the Shuttle might well have lived up to it’s intentions. And spy satellites got much lighter later on, and of course the Soviet Union collapsed, so the poor Shuttle was carrying a lot of Cold War baggage every time it flew. It’s a real shame. Space might’ve been a lot different with the original design.
No doubt that’s what they said about the anvil and hammer, and look at us now.
Actually the anvil and hammer is a pretty good comparison: great for making a single, somewhat complicated part, but far more expensive than regular mass production (per part).
All you have to do is to reintroduce slavery. Problem solved!
(/sarcasm)
There is one point where 3D printing would make sense for cars, washing machines etc. and that’s in replacement parts for old models. Instead of having to sunset and just stop providing the replacements manufacturers could use printers to provide parts as they’re required.
I’m sure Jay Leno would love one of these things for his garage! (Or anyone else trying to rebuild a 19th century Austro-Hungarian horseless carriage!)
He already has!
http://www.popularmechanics.com/cars/a4354/4320759/
Only if the companies put out files that people can use. That would be FANTASTIC but I don’t see it happening soon. They won’t release those specs as long as they can make money off the parts, and then afterwards they don’t care enough to release the specs
Haha. We will get the specs. And we will fix our broken washing machine. We will step on toes just to have clean socks.
It was the best of times, it was the worst of times…for filament producers. What used to sell for $40/kg is now $20/kg and I doubt that production costs saw as much drop. It’s not tough times for 3d printer manufacturers.
Tough times as in “we cant rape people on price anymore”? yes. It costs the $2.00 per KG to make the stuff… Boo Hoo they cant make 10000% markup anymore.
For pushing melted plastic through a nozzle, they’re kindof taking the piss to have higher profit margins than people making entire products. Of course demand comes into it, quite a lot, but still.
I think you need a little help there:
How to determine markup percentage:
1) subtract cost from sales price…simple enough: $40 – $2 = $38
2) Divide the difference by the cost: $38 / $2 = 19
3) Multiply by 100 to get percent: 1900
Only 1900% markup in the heyday of 2012 if we use your cost figures (which are way way way below the actual cost).
But you forget that they have to buy the raw material, proces it, put it on a reel, in a bag, in a box.
Add the documentation, put it in warehouses, handle it when ordered ….
You think it is lucrative, but many businesses go bankrupt on such overlooked costs, that for cheap stuff is worth more than what they actually sell.
Don’t forget overhead (building rent, electricity, water & sewer, as well as sales, engineering, sales, marketing, purchasing, QC, and supervision), taxes (including annual inventory tax) and payroll (direct labor costs are typically base rate x 1.5 to cover payroll taxes and minor costs like healthcare), also don’t forget capital costs like the actual extruder, and any QA tools. And last, don’t forget compliance costs, from both government (OSHA, EEOC,) and non-government (ISO-9001). And don’t forget maintenance.
You will find plastic pellets are not your only cost in calculating markup.
Haha. Time to jump in and print now!
Raw PLA is $4 a KG. Then you need some additives including colors. A simple extruder sets you back 10k. Getting your process right, about 3 man months.
I don’t know the time-per-roll-per-extruder right now. So that makes it a bit hard to calculate the running costs.
The fact is that they simply earned back their setup costs now, and the volume has increased a LOT meaning the setup costs and running costs are less per roll.
And the people running these companies also want to eat. (Yes, horrible, people earning money. I know HaD hates that)
You did hear that zinger, “nobody owes you a living”, right? It stands for poor, poor capitalists entrepreneurs too…
“We” don’t hate people earning money from good products at all! Things we love (a non-exhaustive list):
1) Clever hacks, well-presented.
2) Open source hardware and software.
3) Companies that support and facilitate the above.
Which means that we love you, and we hope you can continue earning a living writing open slicer software, because it benefits us all.
Given the number of our products that have been copied in China, I feel our company is “open source”.
why spacex print rocket? they reuse engine so what problem of time? conspiracy?
Rapid iteration of improvements? Or, more likely, the tiny bit of weight saved in printing parts that need fewer fasteners and less excess material will have a substantial impact on fuel costs over the lifespan of the rockets.
Also the creation of structures like embedded cooling channels which cannot be created using conventional manufacturing/machining techniques
I saw some video about 3D printing metal, for aircraft. You can get shapes that are impossible to make otherwise, particularly if you want holes and gaps inside things, in an otherwise solid piece, no welding etc. You can make parts much lighter, but tested to be equally strong.
Weight’s very important in rocket. Each unit of engine needs extra units of fuel to lift, which themselves need more fuel etc. Saving a kilogram in one place, can knock many kilos off the finished product. All of which saves lots of money.
Fewer production steps means fewer opportunities to mess up. A 3D printed complex part may not only be lighter it is more likely to work.
It’s not just weight – some materials simply cannot be successfully cast or fabricated by subtractive methods for certain geometries, and preform as required. I suspect that is the driving impetus in the case of the fuel nozzles mentioned in the post.
Rapatan has been working on the Metalicarap for years:
http://reprap.org/wiki/MetalicaRap
Could use a good set of brains to help progress the effort.
the solar data and calculations on that site are painfully wrong. No wonder he needs brains. Not often you see bad 1) bad data 2) bad assumptions, 3) bad arithmetic, and 4) unit problems combined in a single calculation
Nice Idea, but I think solar cells have to become (or are already) a mass produced “commodity” because then you have economy of scale. Producing solar cells in a huge amount of mini factories will not yield a high volume of cheap and well performing panels. There is not much customization necessary or possible. And the knowledge of successfully operating a high vacuum sputtering machine is not that wide spread. It doesn’t make sense that every one who wants to operate a solar power installation has to go up the learning curve of producing the cells himself.
I can’t help having to point out that 500 mm³ (0.5 mL) is equivalent to 0.031 inch³, not 30 inch³.
500 cm³ (500 mL) would indeed be approximately equal to 30 inch³, if you ignore the improper rounding.
Thanks! It’s a typo, it’s 500 cm^3 and 30 inch^3. Fixed it.
For the record, Stratasys didn’t get burned by Makerbot, Stratasys burned it down all by themselves.
also, there’s Velo3d ( http://spectrum.ieee.org/view-from-the-valley/robotics/home-robots/is-stealthy-velo3d-poised-to-revolutionize-3d-printingand-robotics ) which hasn’t made any announcements yet, but did have a recent patent get published: https://patents.google.com/patent/US9254535B2/en (found via Spencer Wright’s metallist)
Hey! Very cool, thanks for sharing this!
Ok, this is awesome!
I suppose they can do “print time” alloy creation by melting different metal powders to create the allow while creating the object. Do they as well use magnetic and electric field to ensure, where possible and/or needed the alignment of the underlying atomic structure?
I’m surprised to hear that laser sintering is higher resolution than electron beam melting.
Electrons will follow magnetic and electric fields (the printed part will be creating both of those), photons happily ignore them ;-)
There were some interesting metal printers on display at RAPID in Orlando that I got to see. Most of them were commercial machines in the price range of $500,000+, but were advertising very tight tolerances for the prints. Two different machines stood out to me; one by a company called FormAlloy, the other by XJET. The FormAlloy machine uses a powder/lazer nozzle to lay down the material similar to a conventional 3d printer, while the XJET machine is closer to an inkjet printer than anything else. Again, both were no where near the type that a hobbyist could afford, but both demonstrated technology that in my opinion could be adapted and scaled onto a hobbyist level.
FYI, Direct Metal Laser Melting is not the same as Direct Metal Laser Sintering. In sintering, the metal never melts. This distinction does not exist for polymers, as they don’t really melt. This is why people use the terms SLS and SLM interchangeably in the polymer world. In contrast, in crystalline solids there is a very important distinction, as solid state diffusion is much slower than capillary action in the liquid state.
It is also worth mentioning that processes like DMLS require removal of metal supports. Note how the pictured impeller is built welded to a plate. Supports must be built in in some of these processes due to thermal stresses. Electron Beam Melting is also quite a bit more efficient than any process that uses a laser. It takes the same amount of energy to make a unit weight of titanium with EBM than it does to make the same amount of weight of plastic with laser sintering.
Not to mention, these processes for additively manufacturing metals are unlikely to be used in consumer 3d printers because one must take special precautions to remove and recover metal powder after printing. Metal powder is highly explosive so powder must be removed in a special inert gas sand blaster.
Could electrodeposition be used to cement the metal grains together? It would be incredibly slow even by 3d printing standards, but there would be no need for expensive lasers or high vacuum pumps.
All the closed voids in the part would end up full of a potentially corrosive metal salt solution.
If a part had closed voids then the metal powder would be stuck in there.
Yes that is an issue, but not one that caused the destruction of the part over time!
Will be really cool when this stuff comes down in price — that video made me think of additively manufacturing PCBs — and not just PCBs, but multi-layer PCBs. — Not to mention 3D PCBs, or parts / enclosures with the PCBs embedded in them, shaped to fit, etc. — And if they can print semi-conductors, well, fuck, that’s a whole new ball game for hobbyist electronics… — even if you can’t print them as densely as modern manufacturing, if you can print them in 3D layers, it kind of makes up for it… — Man, the future is going to be fucking cool. B-)
The problem is how do you validate one off structural pieces to prove they are safe? If you can’t do that in some sort of systematic way you may have trouble selling the items, while finding somebody to offer you liability insurance, which in some jurisdictions may mean that you cannot legally offer such custom parts for sale.
So how could you even devise a framework and method for safety critical custom part validation? Mini CT scanners to reverse engineer the actual finished part for finite element analysis checking (virtual destruction testing) using standardised software? You can’t just check the 3D data the part is generated from as that makes dangerous assumptions about the reliability of the 3D printer. NASA will have the same problem with or the proposals they have for inorbit fabrication.
I’m not sure that this would be a problem; I would be surprised if the the usual inspection and testing tools would not suffice. X-Ray imaging for flaws, metalurgical analysis for composition and physical testing (pressure, tension, compresion, bending, etc).
“Metallurgical analysis for composition and physical testing” are destructive processes best suited to large batches where your parameters are well controlled, enough to make assumptions about the entire batch from one or two test cases, but you cant use those methods on a 3D printed part as each one is different. I guess you could just ignore the risks and if anything goes wrong do a “Richard Branson” and blame the pilot/user and not the process, but it really is a matter of process so simulation and verification is a must. CT is X-Ray, it is just done from more than one angle so that a 3D voxel set can be constructed using tomography.
Yeah I was thinking about that too, and then iI read you earlier! You can even buy a x-ray machine for not so much on e-bay today, use a robotic arm thereby creating a tomograph, with appropriate custom software, and, as you said, run cfd analysis, computational test, actually there is this exemple of the 3d printed turbo by koenigsegg, and they’re trying to homologate their car for the US market by simulation only. I think in the aerospace area it’s a bit more sensitive, but I also think the FAA took some time to homologate the parts because nobody wants to destruct the market for 3D printed metal part, they already invest so much money in it (GE, CFM, etc).
For one-off parts destructive testing is of course not possible.
But most parts will be made in small – but >1 – batches. So you can do some destructive testing on a sample to verify the design and you just need to ensure, that the other parts are of same strength/quality. This can be done by X-ray or CT. You could even print some small bits on the part, for example at start and end of the printing process. This could be cut off for chemical analysis after the printing process to verify the alloy composition.
Ultrasonic non-destructive testing. Also, monitoring throughout the whole process. Not that difficult.
Show me that being used on complex one-off parts with inaccessible features. It is not a 3D imaging system so it can’t form a dataset to be analysed. Even if it did work it would be very slow and given it is not automated how does an operator learn to tell feature from fault? They can’t, perhaps not even if they designed it themselves. So no, it isn’t as easy as you think. Only an automated system for recording that actual 3D composition of the part and then evaluating it’s mechanical proprieties would allow you to have an efficient and reliable testing regime that could be (and this is the important part) standardised across entire industries.
Koenigsegg has been 3d printing turbochargers, which a valve that when flipped changes the internal volume.
https://www.youtube.com/watch?v=DNedUZxP8NU
Damn, I have been thinking to the compressor stages of a hobby jet engine from lost PLA aluminum casting, that turbo is pretty cool and a turbo is more or less a centrifugal turbojet once you add a combustion chamber between the in and out halves.
This blows on metal powder and laser melts it. It’s also a 5 axis milling machine. https://www.youtube.com/watch?v=Fr_PneeyO34
I can’t imagine a future where hobbyists at home will be able to buy a printer that can replicate the results these guys have had going back even 10 years ago. The cost of the raw metal is much different from the cost of raw powdered metal. As one commenter said, great care must be given as metal powders are highly combustible, so the dangers are pretty obvious. I know some talented individuals will build one, but metal is just one of these exotic dreams for printing. I would LOVE to have the ability to even print aluminum parts. I don’t need expensive metals. It just isn’t going to be feasible.
how about this
a nice production-quality MIG welder
an industrial spare 6 axis welding arm
a bunch of clever programming
BAM, you’ve got yourself a metal 3D printer for $10K, not counting the programming which doesn’t really exist yet.
hey, one can dream
That has been done, though. Cant find the source right now. And you get BIG (!) scale and very LOW quality of the metal part.
“…and it’s interesting to see how and why large industries, well, disrupt themselves.”
It’s not “disruption” [HaD], it’s “evolution”.
to the Aurora labs pics:
Yes, there are prints (with no size reference)
But no pics of a printer (just a “fake” door of some laser engraved parts), so I’m very sceptical..
You guys probably already saw this but This old Tony posted this interesting modification to his CNC, turning it into a sort of metal 3d printer: https://www.youtube.com/watch?v=sFXniBbgbw0
The cost and quality required for the metal powder is often forgotten. This is much much higher than for bulk material. Each metal powder particle will have an oxide layer, that ends up in the build. Finally, many common, well established alloys cannot be build using additive manufacture, they simply crack in the process.
Many presentations and catalogs make all this very nice and shiny, selling it as the best thing since sliced bread, but in reality it is not that simple. We still have a steep learning curve to climb.
Yeah. I’m getting a kick out of expendable wax casting and sand casting. They can do almost anything. 3D printing is sooooo cooooool. But so were red and green 3D films! There is some fantastic work with 3D printed molds. That is what I am looking at. 3D printed mold, cast aluminum piece.
I agree with you completely. Then again, somebody will work out the kinks for rocket engine parts and such as. But it will be for low production enormously complex parts. The media has got to shut up about how great it is, because it isn’t.
There are models that can be 3D printed with plastic and can not be simply created other way. So with metal printing there is some area where high price is not a problem. But the prints quality is a different story. It is not so easy to get parameters equal to high precision manufacturing in terms of physical parameters.
https://www.youtube.com/watch?v=SEaht2tQ8P8
I await our robot overlords to build 3D food printing machines.
Much better than my hot glue replica of Benchoff’s sweater.
I used to work at SpaceX as an intern on their Additive Manufacturing team. Rest assured, they are taking full advantage of the technology and its many unique benefits. However, my experience working there and with other million dollar systems has driven me to build a system with similar capabilities, but at a much lower cost and I have every intent to deliver on that promise. We’re almost finished prototyping our first system, but definitely check out our website @ xmptech.com and contact us if you want to learn more.
For $1600, you can print with a paste that sinters into solid bronze in a $500 kiln. Check out http://www.minimetalmaker.com for details