What happens when you break a tap or a bolt in a component whose price tag sits in the tens of thousands. Just drilling it out and throwing in a nut insert stops being acceptable. Is there a way to remove the tap without damaging the master part at all?
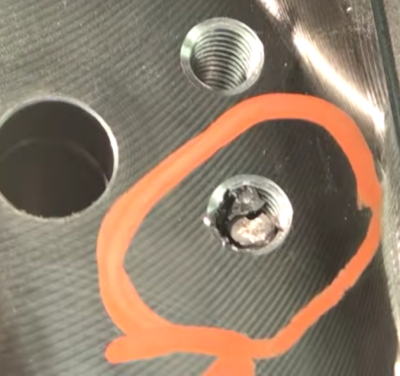
Well, that’s where [Tom Grafton] of Jerry’s Broken Drill and Tap comes in. He’s here to remove taps and chew bubblegum, and he’s definitely chewing bubble gum loudly the whole time. His primary work horse is a Metal Disintegration Machine.
A MDM is basically half of a typical wire EDM set-up. In EDM you used an electrode to punch a hole through the material. Then you thread a wire through the hole, thread it through a sometimes startling array of pulleys, and get going.
[Tom] used the MDM with an appropriately sized electrode to precisely disintegrate the middle of the tap out. After that it’s some careful work with a specially machined magnetic chisel. A quick chase of the threads with a tap and it’s back to the customer.
As you can see in the video after the break, the end result is a threaded hole that’s so indistinguishable from the rest he has to mark which one it was; presumably so the customer doesn’t forget why they’re paying him.
[via r/metalworking]
Ignoring the equpment, you can tell when someone is very proficient at their job when they make it look efforless/easy. I dont have one of those fancy machines but even chiselling remaining thread out after drilling is an art.
I agree, everything he does seems so fluid and calm. People really KNOWING their shit are so damn impressing. I wish I will be like that in 30 years.
It’s always the same: either you do one thing in your life and you get proficient at it after a while, or you are curious and always do different stuff, and you never get highly proficient at anything.
I don’t agree at all. It all depends on the (base) level of skill and how quickly one can adapt to a new technique. In most fields, I’ve found that the more successful people are those that can adapt quickly, and are often extremely proficient at a very wide array of tasks.
Therefore, I’ve always considered the old adage of, “Jack of all trades, master of none” is utter bullshit. :)
Right on, I wholeheartedly agree.
I found that adage continues and completely changes the meaning …
“Jack of all trades, master of none, though oftentimes better than master of one”
Wikipedia also has this so it is somewhat legitimate
I am a Jack of all trades, and I in a bit of soul searching. I can’t find a job where I fit. People always want to put me in a box and for me to stay there. But I hate repetition.
@nraynaud – get into the startup business – they love people who can do everything. Of course you have to live on the edge a bit financially.
Nope. I work in a very high tech industry where being specialized is very important to knowing what the hell you are doing. Even Einstein said “never remember anything you can look up in a reference manual” Meaning, you only have so much brain and so much memory. If you take on more than you can handle, you will fail. Multitasking is a farce invented by idiots who want more work out of you for less $$$.
Those who move from job to job may fake it well, or if the tasks are small and meaningless enough or perhaps the same fucking job, different title.
Look at the medical profession. You don’t want your neurosurgeon doing orthopedics on the side… trust me.
One way to help get that cool fluid confidence in kids, employees, and anyone you are mentoring is to not jump their shit before the job is done where they spend more time concerned about your reaction than the work being done.
Talk and correction can be done later but you are not a time traveller arrived in the nick of time, let them screw up even break something on their own. Fearing the screamer and always watching your back means twitchy and, at least in the presence of a supervisor, never confident low quality work.
I see you’ve met some of my former employers.
Yes. Old equipment != bad equipment.
As a cnc machinist I usually mill the tap out. Leaving the part in the machine.
Using a downward spiral type cut, with a carbide bit, at very shallow cutting depth usually around 0.001″. It usually cleans up the hole nicely. Then chase it with a hand tap.
This is a nice video showing true craftsmanship made to look effortless.
CNC is nice and makes it easier to mill out a broken tap…but that MDM is bad ass.
I’ve done it on a Bridgeport with a 4-flute carbide endmill, $5K casting with a tap that was broken with the part off the mill. The first time had a pucker factor of 11. The problem is that if you break a carbide endmill off in the tap your in real trouble… certainly have to send it out.
I remember form by days working for GE Transportation that when a tap was broken off in an engine casting, they’d send it to another part of the plant where a guy would weld a stub to the end of the broken tap. Supposedly, the heat from welding and subsequent cooling would cause the tap to shrink slightly, allowing easier extraction using the stub. Might also help that the taps were high-speed steel, and the frame cast iron.
I’ve heard about that trick too…never tried it before, I’m better with a mill than a TIG box
You can also weld a nut onto a broken off bolt, even if it’s flush with the deck of whatever it broke in. It sometimes works, best to clamp the ground to the nut you’re welding so you don’t end up arcing through whatever the bolt is stuck in and actually welding the bolt in!
If you have an interference fit bearing race inside a cast housing you need out. Mig weld a few seams inside the bearing race and the whole thing shrinks and the race will fall out.
This is also used to straighten misaligned piping in industrial processes. If your flanges aren’t parallel just weld one side a bit.
BTDT for pulling pin bushings on heavy equipment.
You can induce movement in parts by laying down welds but it needs to be done prudently. Heat input where the engineer didn’t expect it in his design can effect the performance of the workpiece and create internal stresses(or remove them from cold formed parts). You can create stress risers with your weld beads or simply create extra clean up work.
Having said all that, it’s a very handy work method at times.
Ole biker freaks know how to it.
I inlaid a piece of hacksaw blade into a slot on a piece of dowel rod to saw into a broken spark plug base in a gas fired water furnace. Victory!
Very interesting! I’ve always wondered what a company does when you can’t just make another hole. Well now I know that it can be ‘zapped’ to pieces.
I wonder how badly it has to be jammed that a simple “easyout” wouldn’t work.
Well nevermind, Jerry has the answer! http://www.brokentap.com/easy-outs.html
(another vote for editing comments please, HaD!)
Ez-outs will only extract a bolt which has sheered but able to turn free in the thread, given most bolts sieze due to corrotion or galling and snap on removal, an ez-out is garonteed to snap in the hole, they are banned in my workshop lol as the always do more harm than good. You can heat treat a snapped extractor with oxy acetaline in situ and get it soft enough to drill a few mm at a time, its a horrid process tho.
I have banned ez-outs on my shop floor too…to much heartache. I’ve found that a left hand drill works better if the bolt isn’t seized in the hole…even if it is they just drill out then.
What on earth are you doing to the ez-out that you snap them? I have used them on many a seized bolt (head bolts and trans bolts mostly) and have never snapped one.
On the other hand it is a bad habit to assemble (new) part without the right lubrication (like C-, MoS2- or ZnO-based stuff). Saves a penny and your hands don’t get dirty.
They should be poked all day long with a very sharp stick.
It wasn’t a broken bolt, it was a broken tap…whole different ball game boss.
10th word in the text is bolt. So I’m fine, we all know this rule.
Most people read at least half the article though. :/
So nobody gets poked with a stick today; well, no one referenced in the video.
The University of North Carolina at Charlotte’s Mechanical Engineering Department had (probably still does but I cannot confirm as I am no longer there) a plunge EDM that used graphite probe instead of wire. It worked similarly to the machine above, with a few differences. First, the part being worked on would be completely submerged in coolant. Second was the bed size was much smaller than this machine. Lastly, it wasn’t manual. You programed the machine and it ran a cycle similar to peck drilling where the probe burned a bit then backed completely out of the hole to allow the coolant to cycle through the affected area. It was a very slow process, but it was very satisfying to fix rather than scrap a part. They also had a wire EDM. Very cool machines.
This is a very fascinating process. I once worked in a shop that had an EDM, but I never got to see it run, even though I was the one that did the PM on it.
I guess that’s what I get for being a technician instead of a machinist.
The hack build for this is a solenoid rigged as a vibrator with a car battery for power driving a piece of gas welding rod electrode with a small pump for water. Super simple. There are many accounts of guys doing this impromptu in a repair or machine shop. Lindsay’s Books used to sell at least a couple of books on building super simple and cheap EDMs for tap and bolt removal.
It seems his eyes re getting like mine. Use a nice accurate vernier to measure hole depth then use a ruler to measure how far out the tang on the vernier is sticking. :)
WHAT?!
That caliper doesn’t have markings so that he can read the length, he has to use a ruler. Such an odd thing to comment on when he does so much more than measure a caliper.
Back to reddit with you.
“That caliper doesn’t have markings so that he can read the length”
What do you mean it doesn’t have markings?
What sort of vernier caliper doesn’t have markings?
Did you even watch the video? Idiot
He must have watched the video otherwise he wouldn’t have known that the caliper was a vernier caliper and therefore had markings on that can clearly be seen even by those of us with failing eyesight.
Ah, so your eyes are like the rest of us then.
+1
The depth of the depth bar is the same as the distance between the jaws. You can read the depth the same way you read any other measurement.
But sure, Reddit, whatever.
and what an akward measuring system he uses…
At 61 I am off an age where everyone talked metric and used Imperial. I think the US is going through the same crap at the moment. I can now use either for anything but Imperial leaves metric for dead in all aspects of engineering. Base 10 is such a really crap system for anything with bases 12 and 16 being much much easier.
I find anything other than base 10 a pain. I don’t see how anyone can think adding 7/32 to 5/8 in your head is easier than adding .125 and 0.250
It gets automatically converted to decimal after working the same job for 8 years.
7/32=.21875
5/8=.625
It’s still base 10 for me. :P
All about multiplying by two really
7/32 + 20/32 = 27/32, that is much easier than any decimals.
Mechanical engineers discovered bases 2 and 16 long before electrical / computer engineers that’s why drill sizes at 1/8, 1/16, 1/32, 1/64 etc. They never called it that but it is essentially what is happening,
We could do with one of those in depth Hackaday articles on it all really.
Did not know of these processes or replies, most taps work fine with the correct lube for the materials. The tap that surprised me it the latest spark plug taps that pass the bad threads, assemble on the inside and tap from the cylinder side out.
A man with infinite patience. I’m surprised that tap wasn’t totally destroyed by the person who originally broke it trying to remove it before giving up and sending the part to Jerry.
Maybe that person has become skilled enough to know it’s cheaper to send it to Jerry right away then risking- spending all morning on trying to get it out, pushing back the line up of jobs waiting to be fulfilled, and maybe destroying the piece or having to send it to Jerry anyways…
Time costs a lot of money if you look at a busy shops management of it in a holistic manner. It’s not just a matter of saving money on one job, it’s about getting that one job done as well as all the other ones ready to go. If you don’t have another one lined up that day, then you can afford to putts with it for a while, but if your busy you need to quickly assess the situation, accurately predict you ability to fix the issue without making it worse and then make a judgement call to make the problem as cheap as possible not on an individual job scale but on a month end, year end, and business life cycle end. If your going to loose another customer because you’ve pushed their job back to fix something, that is potentially a huge monetary loss. Thus Jerry can run a successful business, because people are skilled enough to know that other people are better at doing things then they are.
Fascinating. Love this guy. However, note to self…never make a video while chewing gum.
Didn’t even notice it.
This won’t work for him, but if you break off a tap in a piece of aluminum that you absolutely must have, here’s a neat trick. Get some Sparex, aka sodium or potassium bisulfate. (It’s the sodium salt of sulfuric acid.) Put a bit in some water and put that in a crockpot on ‘warm’ and put your part in there. Come back the next day. The aluminum will have a layer of gray scum on the surface. The broken-off tap (or anything else made of iron/steel) will be gone: completely dissolved. That’s saved me a bunch of times.
For every time theres something that gets on the hackaday blog that people say “aren’t hacks” or “aren’t cool”, there’s something like this they talk about that’s just wicked.
These comments are all well and good for not mission critical parts. Cant do anything except EDM on weird one off space quality very expensive items, the governing body has rules against that. Somebody used the wrong sized drill without lube. Need to fire that person.
agreed even if he has an impeccable record; the best employee. anyone who screws up should be fired without warning and in a shameful and embarrassing way. We cannot tolerate mistakes, ever. what a loser anyway.
Mmm. Threaded inserts and heli-coils are a great way to avoid this problem altogether. Smooth bore a hole, apply the insert and use the appropriate fastener.
Not sure that flies in the aerospace industry.
Heli-coil inserts thread into a tapped hole, so in this case it would make no difference.
Helicoil would never pass inspection for aerospace unless it was designed in the part to begin with. Things get rejected all the time for far less serious issues, I worked at a shop that made a bunch of different parts for the 777 and other planes.
Of course.
You can also use Alum to dissolve the broken tap out of aluminum and some other non-ferrous assuming it is small enough to put it in a bath. Boil the part in a pan with water and alum and the tap will be gone pretty quickly.
+1
https://www.youtube.com/watch?v=fqZYgReuywM
Nice video! Thanks both of you. :D
Skillz. Mad skillz.
No one caught the pun “after the break, the end result…”, or was it too obvious to comment on?
guess the author was bored when tagging this article
This brings back a lot of memories from my last duty station- TRF/Bangor circa the mid-90s I worked in the hydraulic shop, and we often had to “fix” broken taps in valves. 6061 and 7075 Aluminum with “navy brass” (brass with selenium) in a salt-water environment. We had several different methods, from MDM to just using a drill press with tiny carbide drills and careful cold-chisel work, as well as using canned heat and conduction heaters in conjunction with a dremel to score the head and then “unscrewing” after very liberal application of Kroil. Steel wasn’t as bad; you could get more medieval on pump bodies, but hydraulic valve blocks were another story. The old-timers in the shop made it seem like a simple task; it took a few times before us young-guns got that level of confidence.
As someone who has owned three wire edm’s and two “tap disintegrators”, and thus have burned out a fair number of
broken taps, drills, inserts etc, allow me a couple of comments. I always -ALWAYS- pointed out to a customer that his part was scrap when it came in my door, and might still be scrap when it goes out the door. There is always a chance of severe thread damage that cannot be cured by simply running a tap through the cleared hole. Electricity takes the path of least resistance. Under ideal conditions, the EDM chews the substrate into a 5 micron powder (approximate), and an injected fluid flow flushes it away. But a stuck tap tends to shatter, and big chunks can break away. Being conductive, they can divert a surprising amount of current from the EDM electrode straight onto the side wall of the hole and erode away part of the thread. Running a new tap past these eroded areas is not going to put that missing material back. The tap may be gone, but the damage to the thread may be severe enough to reject the part. Most of the time everything works okay, but occasionally the uncontrollable happens. Made aware of this possibility, the customer can make an educated decision about the attempted rescue.
I just started learning the machinist trade myself. Many many 10-20 taps fell victim to my newbish ways first job i was handed. Thank god the shops ran by an awesome father son duo that it was ok, as long as I got them out myself… Im 4 months in and even the owner admits i can burn a better tap than him. I could only aspire to be as talented as this man. Mad kudos.
“As you can see in the video after the break, the end result is a threaded hole that’s so indistinguishable from the rest he has to mark which one it was; presumably so the customer doesn’t forget why they’re paying him.”
Either we watched different videos, or your standards are very low. It was pretty clear which hole had damaged threads and which ones didn’t. Besides this bit of sensationalism, interesting video.
To be fair it was quite chewed up before he started – check around 1:09. I don’t think he did much additional damage.