I bet the hand saw really changed some things. One day you’re hacking away at a log with an ax. It’s sweaty, awful work, and the results are never what you’d expect. The next day the clever new apprentice down at the blacksmith’s shop is demoing his beta of his new Saw invention and looking for testers, investors, and a girlfriend. From that day onward the work is never the same again. It’s not an incremental change, it’s a change. Pure and simple.
This is one of those moments. The world of tools is seeing a new change, and I think this is the first of many tools that will change the way we build.
Like most things that are a big change, the components to build them have been around for a while. In fact, most of the time, the actual object in question has existed in some form or another for years. Like a crack in a dam, eventually someone comes up with the variation on the idea that is just right. That actually does what everything else has been promising to do. It’s not new, but it’s the difference between crude and gasoline.
My poetic rasping aside, the Shaper Origin is the future of making things. It’s tempting to boil it down and say that it’s a CNC machine, or a router. It’s just, more than that. It makes us more. Suddenly complex cuts on any flat surface are easy. Really easy. There’s no endless hours with the bandsaw and sander. There’s no need for a 25,000 dollar gantry router to take up half a garage. No need for layout tools. No need to stress about alignment. There’s not even a real need to jump between the tool and a computer. It can be both the design tool and the production tool. It’s like a magic pencil that summons whatever it draws. But even I had to see it to believe it.
Enough Ranting, What Is It?
Shaper Origin is an augmented reality CNC router. The augmented portion is a suite of sensors and an onboard computer. You give it a few reference points on a surface and it uses that to track its position on the surface. It then augments your view of that surface with a rendering of the paths you’d like to create, edit, or cut.
Unlike most AR devices, it doesn’t just augment the data available to you, it actually changes physical things about the world around it. This includes your ability to use the tool. When you use the router to trace the paths it’s projecting on its display, it automatically corrects any errors you make by moving the bit opposite of them. Previously, your best freehand work might have been to stay within a half inch of the path. Now you’re magically able to hit a hundredth of an inch.
How Does it Work?
There are undoubtedly many ingredients in the secret sauce that makes up the Origin. One of them is the fiducial tape used by the system. The tape looks like (and is) a perpetually randomized pattern of dominos. There are only a few hundred possible dominos, but the tool’s computer vision software interprets both the dominoes and their relationship to neighboring dominos. When you consider that the tape is endlessly repeating and randomized, the chance that you’ll have the same segments of tape on the same work piece in the same orientation become virtually zero.
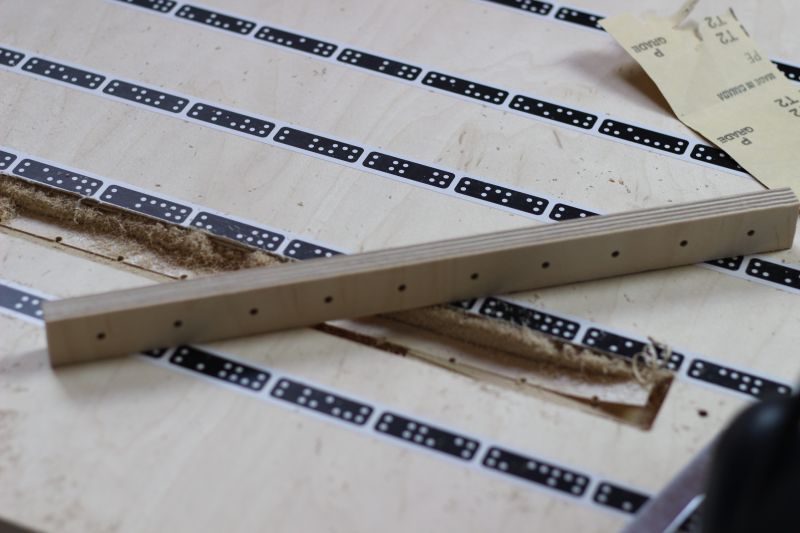
One really cool feature of the tape, which Origin uses to its advantage, is as an identifying marker. Since it is very unlikely that the tape will ever be in the same configuration twice, Origin can use the configuration of the placed tape as a unique identifier for the material. Let’s say you have a bit of baltic birch sitting in the corner of your shop. A few months ago you cut some wooden gears out of it. Well, when you need a new piece cut out of it, Origin will instantly recognize the arrangement of tape on it. It will know where it had previously cut out the gear. It is possible, then, to have an entire library of materials in your shop with very little set-up needed to begin a cut.
As for placing the tape, Origin isn’t picky. It is using only the relative distance to the tape,and so the tape can be placed in any orientation. No efforts need to be made to keep the tape in any particular alignment. Origin can figure out where it is as long as it can see at least six dominos in its field of vision for maximum accuracy.
Lastly. If you cut over the fiducial tape, or find yourself needing more tape. It’s absolutely trivial to add more. Just place it on the surface and rescan. You won’t lose your progress on the workpiece.
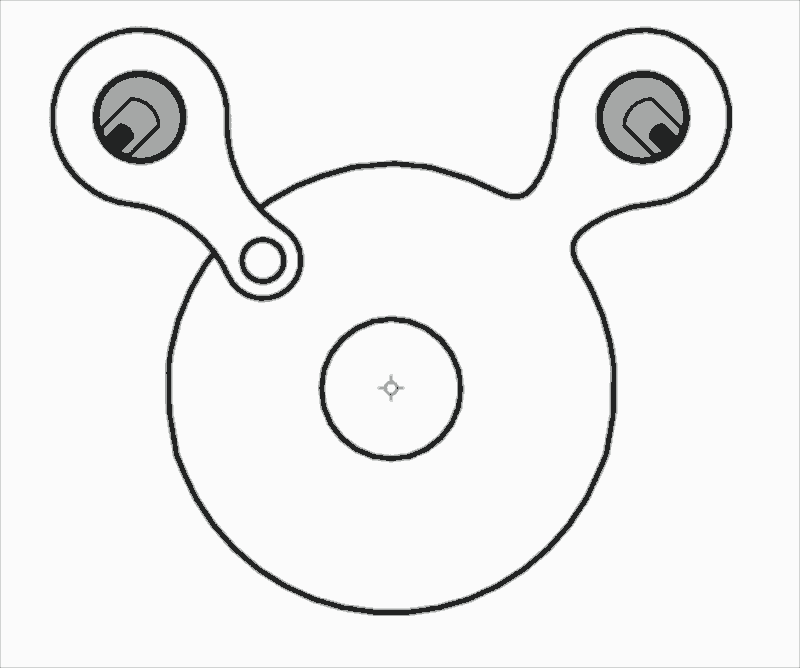
The Mechanism that Fine-Tunes Origin Placement
At the core of Origin is this mechanism. Two eccentric cams are inside of two arms creating a very compact five bar linkage. It’s as non-linear as they get, but fortunately it’s deterministic. Since it’s all computer controlled anyway, this doesn’t matter at all. Any microcontroller could effortlessly perform the required transformation. What it does mean is that there are no bulky linear motion guides, allowing for a compact device.
On top of that the eccentric cams provide a lot of mechanical advantage for fast, compact, and constrained movement. This is especially important when it’s compensating for the unrestrained and uncoordinated movements of a Hackaday writer. Both Mike Szczys and I were able to pick up the tool and cut with it flawlessly, and with minimal training.
There’s certainly a trick to it. Shaper employees were able to hold much tighter tolerances due to practice. Origin actually has quite a bit of feedback to it. Rather than setting the cutting speed in GCODE, the user sets it by moving the device. This is especially handy when cutting a fragile material or getting close to the end of a board. Rather than just accepting that there will be some blowout, you can just slow the cut down and be extra gentle. It offers a lot of control. It’s not a tool that does the work for you, Origin is a tool that makes you better at the work.
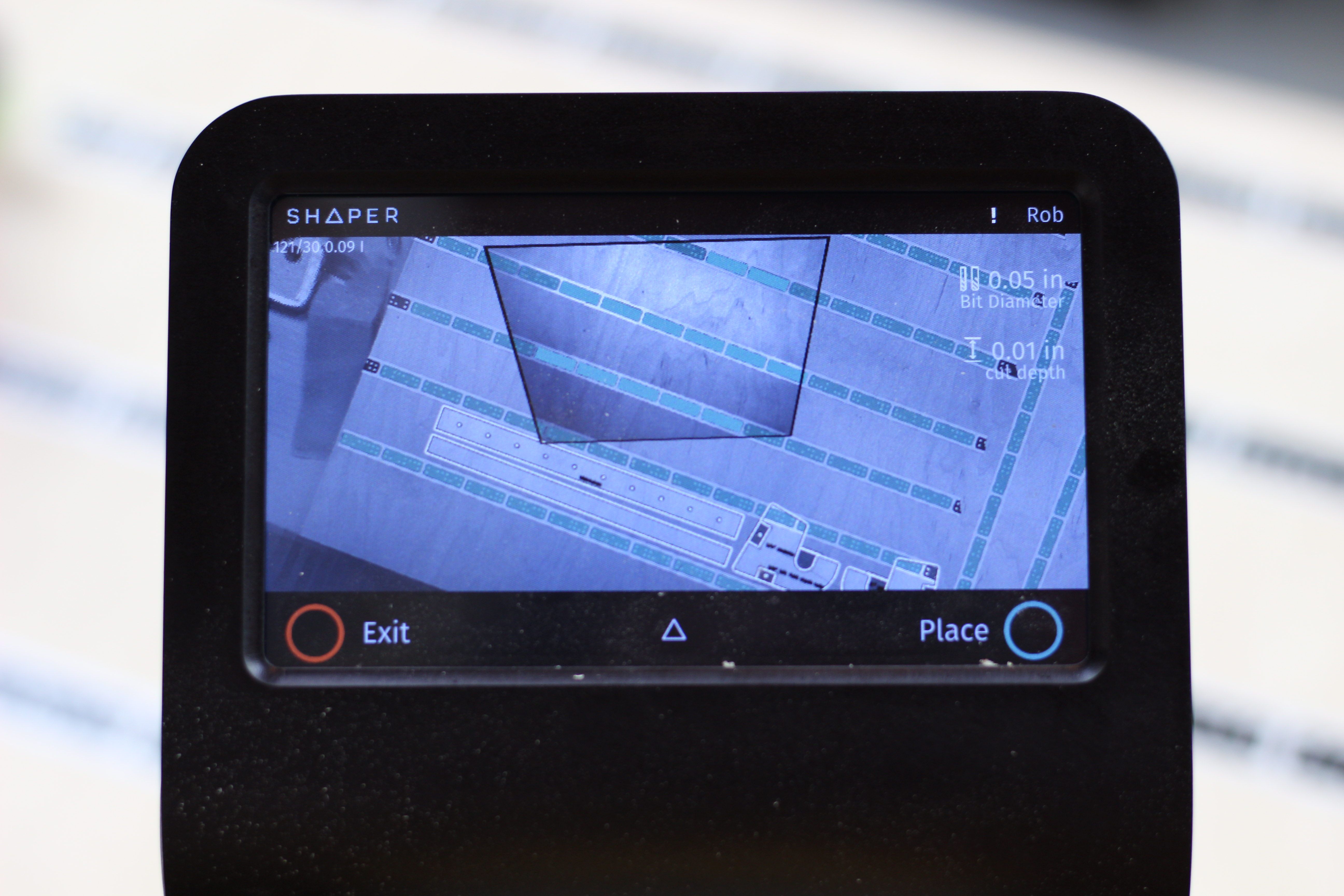
Origin derives most of its tracking power from a carefully mounted camera on the forward facing side of the device. Since the algorithms know the exact location of the camera relative to the cutting tool, it can work its way backwards from the fiducial tape to determine its position. Of course it’s not all so easy. To achieve the accuracy that Origin delivers took years of work, and it will be a while before any of the undoubtedly soon-to-be emerging competition will be able to match them.
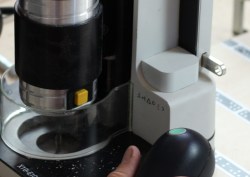
In the photo above we can get a really good look at Origin’s display. The triangle in the middle is a menu button. When cutting, the bit location is shown with a circle centered on the screen. If you look at the bottom of the screen you can see some outlined parts. These have yet to be cut out. To place a part you simply move and rotate Origin until the part is oriented properly underneath it on the board — Origin works just like a mouse.
The trapezoid in the middle is the actual live view of the camera. All the highlighted dominos are the ones that Origin is using to hold its position. Everything around the trapezoid is blind to the device, it is rendering a picture it scanned earlier. This way the user gets a very high level overview of the workpiece. Pretty cool.
Origin can store a wide array of paths on its internal memory. It can also take vector paths from the cloud, generate them directly from the tool’s touchscreen interface, and thankfully, it can read designs from USB Drives. (Looking at you Glowforge).
One of the coolest features, mentioned earlier, is that Origin can actually be used to draw the needed paths. Want to cut a 30mm hole? Mark an X with a pencil where you want the center of the hole. Move Origin until you can see the X on the screen. Place the center of the circle on the X and then drag Origin to change the size. Optionally, just type in the dimension of the circle using the onscreen keyboard. More than outlines are possible. You can easily do things like layout a pocket for a hidden hinge without ever having to open CAD or vector software.
The best part about the Origin is its responsiveness. A lot of work has gone into bringing it below the threshold of human perception. Robert B. Miller first wrote in 1968 that any user interface element must respond within a tenth of second or the user will notice the delay. Considering the amount of heavy processing involved in this kind of machine, it’s nearly miraculous that they manage to stay under this threshold.
What Went Into Its Development?
We only got a glimpse of the thousands upon thousands of hours of development that have undoubtedly gone into Origin. Thankfully they gave us a great set of highlights.
The origin of Shaper and Origin began with a frame. Not a machine frame or anything technically difficult; Alec Rivers, one of the founders of the company, decided that he would very much like to properly frame a photograph. From what we understand, a few hours into the project… perhaps even a few tears of frustration later, the founder became aware that woodworking was absolutely not his thing.
However, no shortcoming can survive unmolested by progress for long. Engineering is always waiting there in the shadows, ready to solve a problem. “Surely one can just build a robot to do this, ” Alec thought. “It would be simple, just move opposite of all the mistakes I’m making,” he followed the logical progression; thoughts unhindered.
We’ve been told that it’s been five years and the picture frame has not been built yet, but instead we have the Shaper Origin as we see it today.
It started with a machine vision camera and a portable x-y platform. This platform used regular lead screws and linear bearings to perform the translations. It was assumed that the user would take care of the Z depth. The next iteration was the first one to feature the mechanism that is used today. The Z depth was still managed by the user. They’d have to manually plunge the router.
It is at the next point that Hackaday first interacts with Origin at a Makerfaire. The device starts to evolve. Gone are the clunky handles and better industrial design begins to have its influence. Still it’s a long way from the machine we see today. You can see how far its come from the following video (Shaper changed its name from Taktia to Shaper in 2015):
Further user testing and development added the Z axis control. This is an important development. Not only is pocketing possible, but Origin can now retract when it senses error or the cut has been finished. Finally, Origin begins to look like the machine we see today. We’re not certain if the commercial version will look similar, but we imagine it will be close.
It was quite a challenge to find a manufacturer who could produce the fiducial tape. Not only does the pattern have to infinitely randomized, it has to be extremely accurately printed or Origin will have errors in its positioning. Ilan Moyer, Shaper’s other co-founder, confided that the their original fear was that they’d have to make it themselves. To that end he constructed a rather cool set-up. An industrial ink jet head would print a continuous pattern on a carefully reeled spool of tape. A python script controlled it all. Thankfully, they did eventually manage to teach the production process to a professional tape manufacturer, who is now supplying Shaper with the magic tape.
Testing and More Testing:
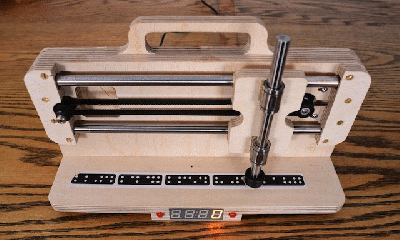
Naturally a device this complicated needs extensive testing. The Shaper team has come up with a lot of interesting in-house solutions for testing their machine.
For example, the tape needs to be optimized for workshop use. It needs to stick to a variety of surfaces. It needs to be cheap. It needs to come off of the surface without leaving residue. It also has to be durable. A machine tool is going to be scraped over its surface multiple times in use after all.
Shaper had ordered their first run of professionally manufactured tapes. They’d also ordered the entire assortment of abrasion coatings offered. It was time to finalize the tape specifications, but they came to the realization that their testing up to that point was too unscientific to have produced a clear winner. So they did the only thing that made sense. They built a testing machine from what they had around.
The machine is simple. An Arduino drives a floating head with some sandpaper glued to it back and forth. It counts the cycles. The tape with the least amount of damage would come out the clear winner.
Another problem was that of the spindle. While the Dewalt router that everyone seems to use is fine and dandy; there are hundreds of router spindles out there, and Shaper wanted to find one that would provide the best power, control, quality, and cost to integrate into Origin. The only way to know for certain is to test the options – all of them. But there’s a problem. How do you test a spindle anyway? Do you have an intern route wood all day long, keeping a subjective log of the spindle’s performance?
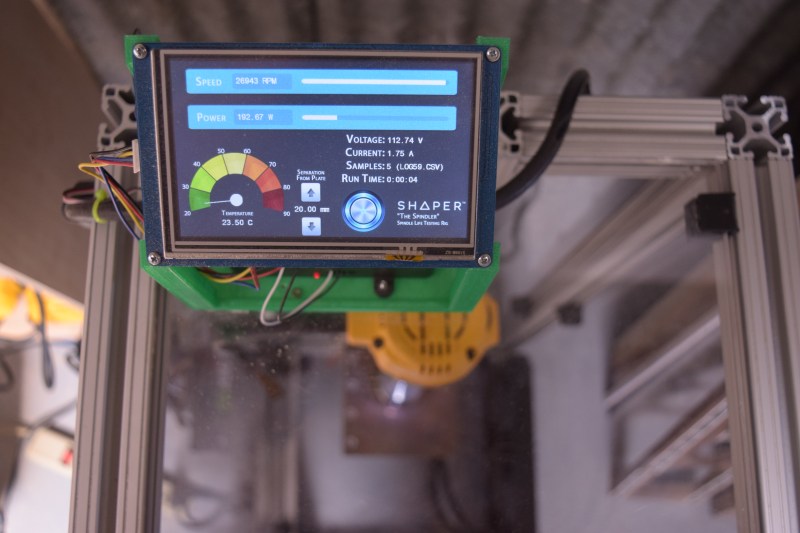
We were kind of blown away by the testing device, but then again these guys are very clever. They came up with a way to place an arbitrary load on the spindle. They do this by attaching a really strong magnet to the end of a shaft attached to the spindle. The magnet hovers over an aluminum plate. By moving the magnet closer and further away from the plate they can dynamically adjust the load by inducing eddy currents in the metal. Naturally, this heats the plate up quite a bit when it’s eating 500 watts of power, but it gave them a way to test any of the spindles out on the market. A bit of off-the-shelf watercooling meant for CPUs and the machine can run indefinitely.
Jeremy Blum threw together a simple touchscreen control panel that logs spindle metrics in real-time, and allows them to push the spindles until they break. We’d love to see their data for all the routers in the market.
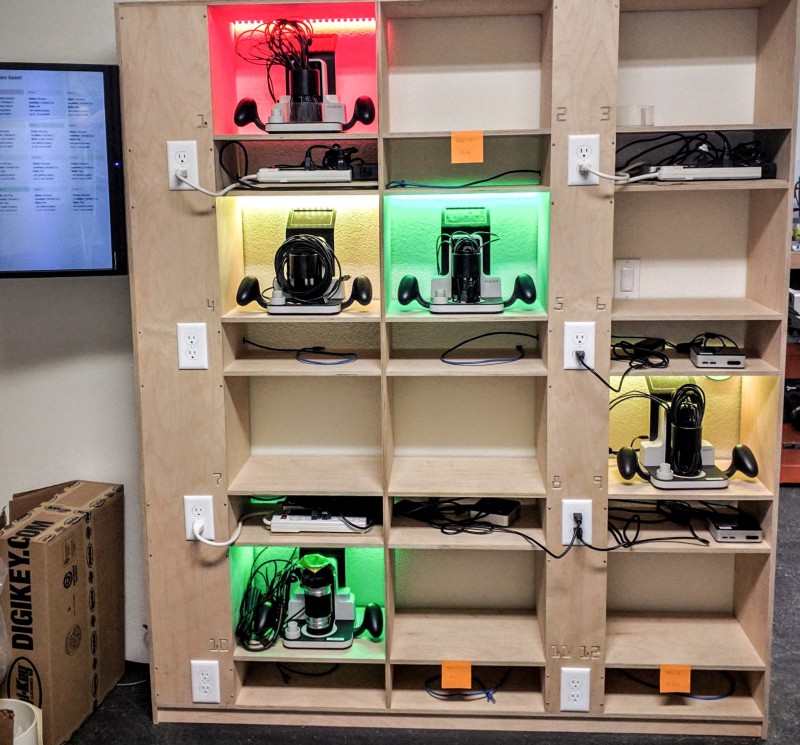
They go into it in some detail on their behind the scenes blog, but another reason for their success is their excellent system for tracking bugs and testing results. The device above is called “The Basket” — they like to joke that all their “eggs” (their hand-built beta prototypes) are in one basket. The basket employs purpose-built software for checking units in/out, and logging detailed bug reports for each unit.. The shelf is, of course, also entirely made with Origin. We feel that its ability to cut properly sized holes for plugs is worth it alone.
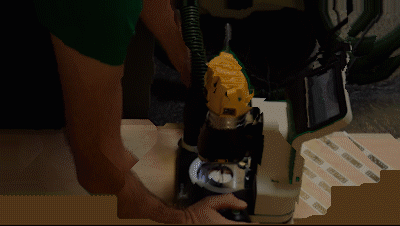
The Basket can track who’s using the tool, who broke the tool, its current status, and much more. They even use it to keep track of beta testers. All the data is seamlessly pushed to their internal beta logging system. One problem any engineer faces when performing tests on a newly designed hardware is whether or not the problems they are seeing are a fault of the design, or just a fault of assembly. Having nicely organized logs is the best way to make such determinations.
What can I make with it?
Fortunately Shaper has recently begun posting more videos of the device in action. The simple answer is, anything you could imagine building with a Shopbot or Shapeoko is fair game. But, you can also do much more since there is no limit to build envelope, and you cut non-sheet materials, like existing desks and already installed panels, etc. Shaper currently recommends that Origin be used for wood-like materials, soft metals, plastics, and composites. However, they’ve been doing a lot of testing on tile and granite. Since all it requires is the fiducial tape, it can make anything from the size of a matchbox to something as big as a thirty foot conference table. Most of the test rigs shown in this article were made using the device. Below is a playlist showing way more example videos.
The Future:
After a long wait, Shaper has opened up pre-orders for the device. They hope to have the first production units in people’s hands next year. Keep in mind this isn’t a Kickstarter where they’re, “pretty sure it will work, we know a guy”, they’ve been at this for five years now. So we’re betting on a good chance it will turn out well for them. There are some early bird discounts rising up to the final estimated retail cost of $2,099 US dollars.
Having used Shaper’s Origin, there’s no tool I want to add to my personal shop more. I’ve fantasized about owning a Shopbot for years, but even if I could afford it, the chances that I’d have a place big enough for it are even less. This just opens up so many possible avenues for making. For most of the things I’ve used a CNC or laser cutter for, this will do. For most of the things I’ve wanted a full wood shop for, this will do. It’s the size of a breadbox, easy to use, and enabling.
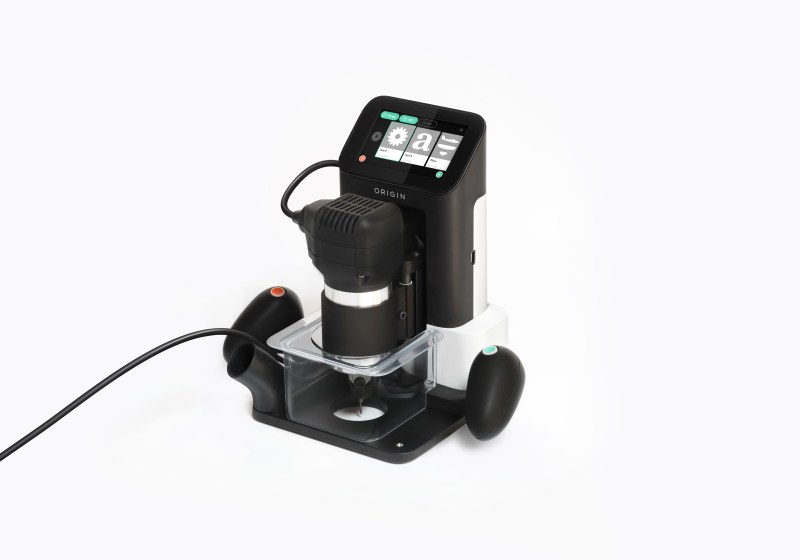
Sounds like a new variation on the inkjet printer scam to me.
Yup! $10-15 for enough tape to cover a 4×8′ panel, and you can only get the tape from Shaper (they claim it’s not possible to make it yourself). What happens when they (or their third-party supplier) go out of business or decide to charge twice as much for the tape?
Also, given all these nifty demos, why are they quoting delivery in ???????????????????????????????????? ?????????????????! The “early bird” prices are suspiciously low, making me think that the actual shipping price won’t be anything like the quoted $2,100.
I’ll hang onto my money until after I read reviews of the shipping units, and possibility ’til the overhype crash drives the price down to a more rational level. But I think I’d feel a lot more comfortable with an ordinary gantry machine, even a small one in the $5k range, that doesn’t depend on anyone else to keep it working.
If there is demand they will be available on alibay at $2 a roll. Don’t be cheap an buy the $0.75 ones tho, quality is terrible and they leave residue that is a pain to remove.
I tend to agree with Daniel. There is really nothing that is secret about the fiducials so third-party tape should be pretty easy to come by if there is demand.
Shaper has a vested interest in keeping the cost as low and as available as possible. The inkjet model only works because the printers were free with every computer sold for many years. They’re not just giving away the tool in this case.
And I doubt people with this level of skill are driven by the dream of making their living selling tape.
Indeed – all of us at Shaper are here because we want to improve tools that allow people to make amazing things. All of us are Hack-a-Day readers, and all of us spend our time building stuff (when we’re not designing Origin). We want to put ourselves out of the tape business by constantly improving the tool so it needs less and less tape to be accurate.
-Jeremy @ Shaper
The tape seems like how machine vision was handled in 1980s, mark up the thing you want to see with reference points. It’s like they learned all they know from the tech behind the original optical mice, that needed an indexed pad.
This could lead to the hypothesis that either level of skill is low, or intent to generate recurring revenue stream is high. Or a plausible alternative is to generate a quick and dirty system that’s really cheap to implement…. and it doesn’t look cheap.
RW, I challenge you to bring a standard optical mouse from drawing board to box in store. You know, manufacturable mechanical design, deal with contract manufacturors, plastic tooling, FCC and CE certification and so on. I assume that you are aware that when you get that fully functional circuitboard fit perfectly in the 3D printed casing you are about 0.3% on your way there?
So you agree that this is about 0.3% of a finished product. ;-)
Touche
And medicine manufacturer CEO’s didn’t’ grow up dreaming of making epi pens $600, but they sure did..And it isn’t an accident.
@Jeremy Blum – If the tape is precision-made and the markings are random (or pseudo so), and if the device reads these precision points to get its bearings…WHY can one not just dot marking patterns along a path/grid/box/straight line with a black marker and have the device find its way from these?
RW – I’d like to point out that the early indexed mouse pads were absolute position, more similar to today’s graphics tablets than an optical mouse. An optical mouse has no idea where it is, all it reports is delta XY position. It’s very easy to tell which way you’re moving and at what speed with far less sensing than it takes to know where you’re actually located in space.
Well I’ll be more comfortable with the idea when I see it second sourced without ensuing sue-age.
Residue wise though, hope they have something special there, considering your unconsumed materials may sit around a couple of years, and maximum non-residue guarantee on masking tape you can get is 60 days as far as I know.
It’s reasonable to assume that if I leave tape on my stock material for a couple years that there will be the possibility of residue being left behind. It’s unreasonable to ask Shaper to design around this scenario – a scenario that seems unlikely to happen given that there’s simply no advantage to placing the optical tape on your stock any earlier than when you’re actually going to be making cuts.
They make this amazing material just for such applications… it’s called sandpaper. You should check it out.
and by “they”, I mean any number of companies all around the world.
So we should interpret Gerrit’s claim of reducing use of a sander, as increasing use of the sander.
I had some Scotch blue painter’s tape on a wood floor for around 8 years, came off with no residue. Similarly, I recently used some to tape up the gap in the mirrors of a car I had sitting outside being worked on without moving it from April until second week of August. (I found the tape works well to keep wasps from turning the mirrors into homes. Keeps them out, keeps me happy.) When I was done working, that tape came right off as well, again, with no glue, and it had been sitting outside in the driveway getting sun through all that time. If storage conditions of your materials are somewhat reasonable, I don’t see why you’d have a problem.
$100 OFF for both you and me if you use my link. Cheers!
https://preorder.shapertools.com/ref/4KQMTPE3F
Anyone need a referral code to save us both $ 100 on the Shaper Origin, here is the link: https://preorder.shapertools.com/ref/G4N0G71PN. They still offer pre-orders for $ 1499 from which you can deduct the $ 100 using the referral link here. The retail price will be $ 2099.
Look forward test it out on some wood.
This is an interesting tool. But…
The ~$2k price tag is a good chunk of change for a tool that the human still has to drive… ;)
I’ve thought about this a lot, but have come around to being OK with the price point.
Consider a machine like the X-Carve (which I own). Fully loaded, it costs $1200. I think it’s safe to assume that the Shaper Origin can produce parts of equal quality as the X-Carve in the same sorts of materials.
But then the Shaper Origin really starts to look attractive when you consider things beyond what they’re capable of making.
The X-Carve has a working area of 800x800mm. The Shaper Origin has no theoretical limits on work area.
The Shaper Origin is portable. The X-Carve is less so. Frankly, it’s a chore to avoid, moving the X-Carve. I’ve done it, and prefer not to.
The Shaper Origin takes up very little space. Consider how much space any CNC router than can handle a full size sheet of plywood takes up. Can you just store that machine on a shelf when its not being used? Not a chance. But the Shaper Origin quite easily sits on a shelf.
The workflow for the Shaper Origin looks a lot simpler and appears to require a lot less setup than something like the X-Carve.
Also, the X-Carve requires a human to drive it. You don’t get to just set it up and walk away. It’s not a closed loop servo driving machine oozing with safety mechanisms. It can skip steps, crash into clamps, get buried in the dust it creates.
My biggest problem with the Shaper Origin is that I’m desperately wanting to work on bigger projects than the X-Carve can handle. I either need to wait for the Shaper Origin, or spend a chunk of money on a bigger router. If the Shaper Origin were available right now the problem of needing more work area would be easy to solve.
+1 for the X-Carve requiring a human to run it. I’ve used a number of hobby-grade and commercial grade CNC machines over the years, and the thought of leaving one unattended for long periods of time is just silly. These machines have the capability to destroy themselves, why risk it?
For a really expensive machine, it’s better to have a paid technician monitoring at all times. $20/hr equates to ~ $40,000 a year. How much does a new commercial-grade CNC cost? How about the workshop it’s housed in?
Opinions do vary luckily…
The idea that it would be silly to let a CNC machine do it’s thing unattended is a bit silly in itself.
Some time ago I worked in a factory which handled a lot of sheet metal and near the end of the last shift we used to load one of the CNC machines with a pallet of sheet metal. And with a bit of luck there woud be 20 to 30 stacks of nicely punched and cut steel plates on a few other pallets. Without that luck the machine stopped somewhere during the night if one of the gazillion safeties was triggered…
I think this machine would qualify for “the really expensive kind” in your view.
I know it was big (20m long with material handling), heavy (made of several cm thick steel plate) & Orange. Italian brand… Strange, can’t remember the brand name… Gosh, this was 15 to 20 years ago…
And no, you do not give a $20/hour worker responsibility over a multi million dollar machine.
—
Down to the hobby stuff:
Depending on the work piece of course a single person can supervice multiple X-carve class cnc’s.
Not so with a machine you have to hold in both hands while using it…
They are just differen machines for differend way’s of working. It seems a bit silly to make a list of the differences between them…
Yah, way back when, when I was in and around a lot of light industry, a lot of them seemed to have Italian CNC machines, I can’t for the life of me remember the manufacturer either. It was semi familiar, like Piaggio or something. They were pretty reliable at running themselves. It was one tech between 3 or 4 of them.
“The Shaper Origin has no theoretical limits on work area.” I’ll bet dollars to donuts that isn’t true. The larger the area, the larger the error. Also, the tool has to memorize the fiducial tape pattern, and there is surely a limit to that.
But anyway, that’s nit picking, If it’s usable over 4’x8′ (and it is, right, Jeremy Blum?), that’s good enough for most purposes.
Correct – we can only process so large of a workpiece before we simply run out of memory in the system. We’ve done 4×8 without any problem.
Just for fun, what would be the theoretical maximum?
I actually don’t know. We haven’t been able to hit it yet. Could probably be computed, but haven’t done that since we haven’t run into a practical limit yet.
If you or anyone need it, you can use my referral link and we both get $100 of the preorder price.
https://preorder.shapertools.com/ref/YELGJ4TJK
Really? You pre-ordered one a year (at least) in advance with so many unanswered questions? If you’re looking for investments, I have some land in Florida…
For what it’s worth, the X carve is open source. The machine is made from common aluminum extrusions, so if you want to make it larger than the stock 1000 x 1000mm you can. Quite a few people have made 1000 x 1800mm machines, and and Inventables sells the maker rails in that size, as well as 20 mm x 40 mm support rails. You could certainly make a drop-down table, as many have done as well.
I think the shaper origin is really going to be a big hit with people who need to take something to a jobsite, but It’s not going to replace an X carve or similar in the workshop. Why? There are some CNC projects that can take many hours to produce. Are you going to want to bend over a 4 x 8 sheet of plywood for seven or eight hours guiding a little circle over a line? How long you going to hold up before your back starts screaming at you and you develop eyestrain? Presumably you would want to be wearing some ear protection and despite the dust extraction, I’m sure it’s probably a good idea to be wearing a dust mask. So, again, how long are you going to be comfortable moving a hand-held router over a piece of wood while wearing a bunch of personal protection? Speaking for myself, I get fatigued pretty easily, and could not imagine using the shaper for more than an hour, let alone, three or four or five hours. The more complex the design, the longer that machine is going to be running.
This is where a dedicated automatic CNC really shines. So, I think each machine has its strengths and weaknesses, so hard to compare. it’s kind of like comparing a track saw to a table saw. Both have their place.
I’m glad that they’ve finally got to (pre)releasing it to the wider world, even if I still can’t get access to it in the UK :-(
Ever since it was first mentioned on HaD and watching the few videos by Ben Krasnow (he successfully used it on thin metal), I’ve been lusting after such a device (one that is not constrained by a gantry system, like traditional CNC rigs, so can be used in-situ or over massive areas).
can you configure it to use metric units?
Nah, the embedded processor is way too busy with the vision system and inverse kinematics to convert units at the same time.
Only if you want it to fly right out of your hands and crash into mars .
“… more accurate the slower you go …”
right now I call that ‘use a chisel’, and the only design input requirements are a pencil.
Looks like they are really investing into promotion, Diresta got one too: https://www.youtube.com/watch?v=R3ahfDFHo3g
So, is this a PR article?
No.
Well, not a paid one. I appreciate you genuinely loved it, and the company are “one of us”. And it is relevant to some of our interests. The article wouldn’t be out of place though as an advertorial in some magazine aimed at technically proficient, intelligent people.
I’m not objecting, but I can see it is a bit advert-ish.
I’m looking forward to the drama in 5 years when half the company splits off to make the Original Origin vs Genuine Origin. Sure you’ll cover that.
I’ll admit this is by far the most glowing product endorsement I’ve ever seen in a Gerrit article. I suppose I could interpret that as suspicious if I wanted to. Or I could interpret it as a legitimately exciting, functional product.
Hmm, I would think this one is on par with the othermill article
http://hackaday.com/2016/08/02/the-othermill-vs-import-a-technical-comparison/
The Tested youtube channel put up a video on this the other day. Other youtubers have been receiving free units as well all around this time. It’s a pretty clever marketing campaign though, you get direct access to hundreds of thousands of subscribers who trust who they subscribe to for very cheap. I’d bet this Hackaday article is similar – not paid, but a free unit.
Not overly dodgy, just very well coordinated. Expect to see the Shaper Origin all over the internet this week.
No, we did not get a free Shaper. Nothing was exchanged for this article.
You should’ve stuck your neck out, you might have got one.
The product looks great.
But the tone is so enthusiastic that it really looks like some sort of advertorial (publireportage in french), or sponsored post.
Is it?
If so, should’nt there be some warning about it?
We don’t do sponsored posts. So nothing to warn about.
It’s unbridled hyperbole that’s the problem.
My wife’s embroidery machine has the “find the X” or in its case the crossing on an 8. Google Babylock Enterprise. Otherwise, awesome idea and good luck.
So first off, this post is much closer to an advertisement than I like to see on HaD. If you want to review the thing, that’s fine, but this isn’t a review. This article literally claims this device is as transformative to woodworking as the saw blade. Come on.
Second, I honestly don’t see the excitement here. If you ended this article saying it was $399, maybe. But it’s 2K AND I have to move it around by hand? One of the whole points of a CNC router is that you don’t have to do it yourself, the machine can cut shapes out of flat stock all day while you just keep an eye on it.
This device is like those 3D printer pens compared to an actual 3D printer. Yeah it’s cool and looks like the future, but at the end of the day if you still have to move it around manually it’s never going to be as useful.
Well, despite my snarks about the machine (above), I have to disagree with you about it being less useful because you have to move it around by hand—this is actually the ???????????????? reason I’m tempted to buy one. With a gantry router, you have to move the material to the workbed, and it has to fit. With the Origin, you can take the machine to the work, even if it’s on a wall or ceiling. Not often needed, but when it’s essential your only alternative would be a less-accurate manual router.
So, the Origin is tempting, but it’s going to have to be a ???????????? less expensive and there is going to need to be a backup source for the fiducial tape.
Remember all the hype about the Glowforge “3D Laser Printer”, another gimmicky product that’s in perpetual preorder status? I wouldn’t be surprised if the Shaper Origin turns about to just as vaporous.
Thing is with this, the “gantry” is your body, which is something you bring with you everywhere. Meaning the bit you have to carry is hand-portable. The unit manages machine-precision with human muscle. That’s the genius. This can bring CNC precision to many, many work sites and applications, where it wouldn’t be practical to take a wall out of a house and load it onto a traditional CNC machine. It’s a brilliant idea, and I bet wasn’t simple getting it to work.
Agree 100% with this. Been thinking a lot about this machine; firstly that it’s completely unaffordable for me, but mostly for the possibilities. No need for dowel joints or Domino loose dowels; you could place dowels and sockets wherever and whatever size and shape and spacing you want. I will be making a 12m floor to ceiling bookcase with a stepped from and drawers at the bottom – if this works as advertised, I could imagine making up the pieces with to finish quality with all joints built in. Mallet and glue to assemble. It would bring the ability to design items with complex connecting shapes and be able to do so the same every time. Slow – yes. But likely faster than multiple machining steps and multiple assembly steps.
Hackaday doesn’t do advertisements or sponsored posts. If anything I spent more time on this article than I should have; considering I get paid the same regardless we can construe that this article actually cost me money to write. I stand by my review. Sometimes reviews are positive. Sometimes they can be overwhelmingly so. What would be the point of only reviewing things I hate just because people have an easier time trusting grumpy cynical rants than they do the opposite?
I like it, both the product (except the tape) and the review, enthusiasm shouldn’t be a disqualifier for an independent review.
Cynicism is the prevailing wind blowing through this site and it stinks.
Being passionate about whatever is what makes doing stuff worthwhile for me at least.
Tell me I can’t turn the dials up to eleven and I won’t turn them past three.
One of the things I see and like about this tool is that while it can’t replace a production CNC router where you want to cut flat stock all day, it does allow you to do one-offs using much less space. I can’t see putting a decent-sized CNC router in my Makerspace (1000 sq.ft. total space), but one of these can go on a shelf and still let me route 4×8 sheets when I need to.
Although obviously put jokingly, in actual fact the saw predated blacksmiths, since they were first made from flint and bone and all such natural materials I read. But even if you don’t want to call that a saw, in the woodworking discussion sense, it still is the invention-foundation.
it also mentions: “[T]he identities of the axe, adz, chisel, and saw were clearly established more than 4,000 years ago”
That’s what I thought.
The point is, I can store this in my garage, next to my other tools. While a router would take up a considerable amount of space, this takes up the same amount of space as a circular saw.
But as always, I’ll wait till the pre-order phase is over and see if the actual product lives up to the hype. (And if it does metric)
I dunno if I’d be storing this $2000 unit in my garage next to all my other tools. I’d be thinking about storing it inside, in a safe.
While 2k isn’t cheap. It’s more likely that thieves will steal all my bikes and leave the tools. As we’re not keeping our 1k bike in a safe.
I dunno, it looks somewhat like a conventional power tool, so they might grab it. Compared to say a 3D printer, that looks like a science fair project :-P
@RW, Just finished upgrading my reprap the other day! Who wouldn’t want to steal this?
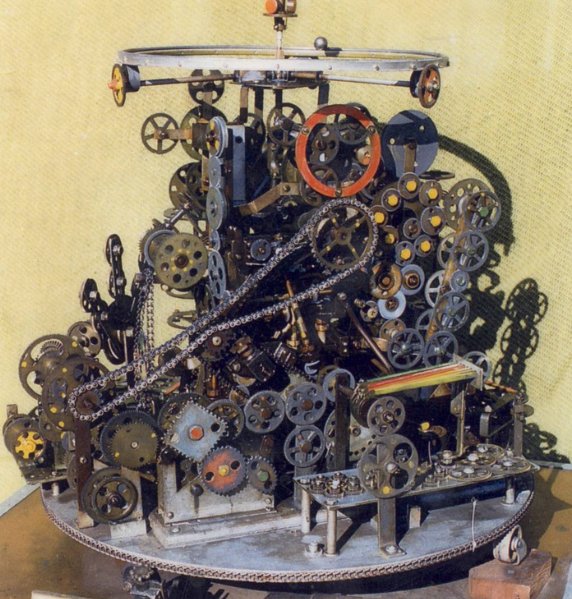
Only got twenty eight thousand dollars of parts and man hours in it too. Sure it wobbles a bit on the Z, but I’ll fix that soon enough…
“Who wouldn’t want to steal this?”
Heh, anyone who already has a hernia or back injury for sure.
So a Dremel tool with a magnifying glass with some basic cams put in place to reduce motion. Wouldn’t it be cheaper and easier to get a CNC mill like the Shapeoko, remove the bed, and attach a RaspPi running OpenCV?
A rocket ship is just a cylinder with some explosions behind it. Wouldn’t it be easier just to put a bomb under my car? The seats are comfortable and it would even have AC!
Excellent retort! :-)
Insensitive! I broke some ribs wrestling yesterday and reading that comment was pretty painful.
yeah I wrestle with some days too sometimes.
you guys kill me…lol
machine looks great, don’t let the folks with preorder vapor fatigue get you down
https://youtu.be/pJdrlWR-yFM?t=430
That nearly worked. Most likely a connection to the explosive bolts to disconnect the “fuel tank” came loose on launch. Wind tunnel tests of a model of the car with wings showed it should have been capable of gliding and being remotely piloted.
I know I was so bummed they didn’t have the funds/time or whatever to get it right, seemed pretty close.
Hahahahahaha! Perfect.
A fantastic tool but i KNOW i see one of these a good 10 years ago somewhere on the interwebs?
Covert advertising. Not a single critic, it´s all wonderful for 2k$. Pathetic HaD, we don´t buy it.
You don’t speak for all of us, buddy. I personally am salivating at the thought of what is basically an entire workshop in handheld form.
It’s nowhere near an entire workshop. The way it is described, I can’t see it doing more than 75% of what a normal hand router could do with an experienced operator. You can knock that down below 50% if you have a table attachment for router.
The particular problem areas would be, narrower material, smaller pieces of material, “swiss cheese” material that you anticipated that you could get a lot of small parts out of yet, edges of material. Due to the material memory, sounds like you can’t even have a set of over run boards, to allow you to get close to edges, because the second time you use them it will think you’re cutting thin air. All down to needing to see an approx square foot or two in front of the tool. Sure you can jig and rig and workaround, and use fre$h tape every time, but if it’s getting to be more of a PITA than the manual tool, then it’s not justifying itself well.
It’s a router + more, how can it do only 75%? It should be > 100% by your logic.
Where’s the more??? It’s an accurate router that can’t go as close to edges and needs a rather large minimum amount of area for it to know where it is. Doing fiddly bits might be less frustrating, but it can’t achieve finer detail than the bit it’s spinning will allow… and it basically only works on materials that you don’t use if better than plus or minus half a millimeter is really that important.
That’s how I see it too.
Yeah HaD clearly loves this thing and it’s the 3rd or 4th time it’s featured on HaD.
And it must go back years at this point, and it’s still not released? Odd.
Commenters be crazy. From reading most of what is above it seems we’re not allowed to actually like anything. Do you actually prefer if we hate on everything all the time?
Of course you’re allowed to like things, but when blog posts start sounding like product brochures you’re gonna get some snark from people who think you should be 10,000% impartial.
When a positively charged body A is brought into proximity of an uncharged body B a negative charge will be induced in B equal and opposite to the charge in A.
No. Overly positive articles triggers the gloomy naysayers which in turn brings out the best of the witty commenters. It’s fact that a blog’s standard is set by the quality of its comments.
We’re not that bad.
Next time they try to cut a complex shape into a wall with their X-carve they will change their minds on this thing.
Cut a guide on the X-carve, use the guide on the wall with a flush-trim bit?
People are used to “review” meaning a consumer reports critical analysis of some random thing like a refrigerator. Hackaday writers don’t review random stuff, they pick things they like and then write an article reviewing them. The reviews are almost always positive because it seems writers don’t go out of their way to find and then complain about equipment that totally sucks.
Well this isn’t a “We took it to our shop and put it through 7 kinds of hell.” proper grown up review, it’s a “We went to their controlled environment and drank the kool aid.” tech preview of unfinished product.
maybe address the most plausible complaints up front? and limit your breathlessly hyperbolic editorializing to posts where you’re not discussing a commercial product?
I don’t get it.
The Augmented reality work is really cool and I’m sure it took a lot of smarts to get operational, but this seems to be a solution in search of a problem.
I get that they wanted something less cumbersome than a full on CNC router table, but that’s about the only thing this seems to really have going for it. Sure, you can go from working on an end table to carving a viking long ship but I don’t think many people work on things that big. Who is their target demographic?
I get that not everyone wants to take 10 years to become a master wood worker using a chisel and coping saw but for a quarter of the price of the Shaper Origin I can buy a trim router, spray adhesive, and a laser jet to print templates and do at least 99% of the same projects. Maybe my imagination is just stale, but I don’t see the void that the supposedly Origin fills.
Will someone who ‘gets it’ help me understand?
Now Michael J Fox can use a router too?
Leave that crap on 4chan.
Not sure how much I can help you understand but I can see that it won’t be that beneficial to a lot of “hobby” level users.
If you want to make something out of raw material that is “desktop sized” to start with then it’s far cheaper to pick up a cnc router table as you suggest. Where it comes in to its own is with things like furniture, something where the raw material and the final parts are larger than a desk but the user still wants the same level of results.
Yes, on large material you might be able to get away with stuck-on templates and doing it entirely manually but this will keep a high degree of accuracy in the results without having to take ages tidying up or going very slowly.
Think more large format CNC machine (8’x4′ sheet) except it can also be used in any orientation and it can be taken to the material (e.g. on walls, floors or ceilings that can’t be taken off and put in a machine). Plus, unlike a large format cnc machine, it’s incredibly portable so if you wanted, you can take it with you on a bike rather than needing a van.
The Origin seems to use template tracing, they’re just digital & you’ve got some slop built in with the CNC aspect of the tool. The correction is cool, but again, tracing patterns is easily accomplished by hand for most people.
Most people are not that good with tracing, myself including. I’ve tried some router work and can tell you that this level of accuracy would be unattainable for me, maybe only after several days of training. Cutting gears manually? Forget about it.
Interesting; while I don’t use a hand-held router every day, it’s one of my preferred tools for heaps things when a near-perfect edge is needed. I don’t’ believe that it’s possible for anyone (except maybe Superman) to follow a line even remotely accurately by hand. Certainly 0.5mm is I believe fundamentally unachievable. It needs templates.
shaper claims your average person can do 0.01″ with the origin.
Quite. Sod woodworking, what about using it for fibreglass – complex cutouts on boats, kitcars etc, or thin metal – instant front panels and the like.
I’d imagine it’s also capable of etching (depending on Z-axis resolution), so that’s another thing it can do.
Definitely a breakthrough tool.
I get it, and I’m excited to see the final product. Some folks don’t ‘get’ arduinos either, and there’s no amount of explaining that will help them understand. I think the same goes here.
What I see is the Arduino of woodworking. Take complex, detail oriented masterwork that would normally take years of diligent practice and put it in a package that anyone can pick up and do incredible things with. I am excited to see what people accomplish with this tool. What will hurt it is the cost and the low likelihood of copycats appearing anytime soon. That price will unfortunately put it out of reach of most.
And to all the people that are bitching about still having to physically move the tool: REALLY?! Believe it or not there is a substantial number of people that actually ENJOY getting covered in sawdust and working with their hands.
Arduino is CHEAP and OPEN-SOURCE
That thingy is closed-source, far from cheap, and its usefulness is still to demonstrate (HaD over-positive blog entry sounds fishy at best)
“Anyone can pick up”
Then bitten by climb milling in a 1/1000th of second. Hopefully this router is a small one with tiny bits. Take a 1.5HP one with a 10mm straight bit and you learn to never do climb milling again even for a couple of millimeter.
A long post that reads like advertising copy.
I think this writer just found his niche in life, especially if he gets paid by the page.
I’m willing to test it. Got one you can send to me (free)?
i think its a neat device, augmented reality routing. pity it doesn’t fit the festool router, though i did see festool hoses. it’d be great for offsite work or places you can’t take the cnc, or when its too big a material.
add some driven wheels to it, line following and there you go
I suppose it is just a first of its class and it will only get better with time.
Once VR gear becomes ubiquitous and VR interfaces standardized, this idea will probably breed universal interface to “wiggly” tools which tend to stay on virtual “grid”, and routers probably won’t be only things. Marrying VR, virtual coordinate systems and e.g. 3D pen, you can throw your 3D printers in the shed and do things manually, almost as good as on a gantry.
It is possible even to draw with your fingers with a system like this, provided it controls exoskeleton arms and gauntlets you would wear. Then I could really use pencil and chisel to make industrial-quality handiwork, or even insert the thread through the needle’s eye at first attempt!
Do you see? The core of this technology is bringing power back to us meatbags, from the pincers of our robotic overlords. New hot thing is (the old hot thing from beginnings of industrialization): human augmentation, this time not just, or not at all, for strength, but for precision.
Or, other way round, it’s exploiting us plentiful clumsy meatbags to carry it around, and take the work off precious robot motors. We’re cheaper to repair, and produce new stock from inexpensive carbohydrates.
Double edged sword. This post anywhere else would give the people working on the project an instant ‘invention of the lifetime’ recognition. But since it is HaD AND the ‘invention’ costs $2K (really ???) I can imagine that someone somewhere is already hooking up webcam to the laptop and tries to prove that this can be done for 10% of the cost. ( worst …. chances are that there are people in China working on it already)
Yes in front of audiences who have never heard of hand routers, or computer controlled tooling, or hype, it’s going to sound like the wright flyer 50 years early.
And another thing: Your laser optical mouse needs no special tape. Later generations of this thing won’t need tape either.
I had no idea hackers hated tape that much. Brian should add a tape tag to use with his filter script.
Your mouse looses track of it’s location when you pick it up. This doesn’t.
How do you loose something?
Your laser optical mouse might need glyphs if it had to return to a fixed point on your mousepad while simultaneously assigning it the correct coordinates on your computer. I mean, this appears to cut a closed path without appreciable error, and can account for rotation and skew of the device as you move it. It’s perfectly fine if your mouse accumulates error, because your brain can correct as needed using the information on your monitor – *you’re* doing the same thing for the mouse as the tape does for the Origin.
I just tested this – turn off acceleration or “enhance pointer precision” in the mouse settings and line your cursor up with a reference point on screen. Put a book or calculator or something on the mousepad so you can return the mouse to the same physical position. Now repeatedly move the mouse away from, and back to, that position, and see how far you stray from your on-screen reference mark. The results will be different every time – fine if you’re aiming at a purely digital target, but totally unacceptable if you’re trying to correlate digital and physical positions.
I vaguely remember SUN optical mice requiring a special mouse pad which was metal and looked like a piece of graphing paper back in the mid 90’s.
It may have had a specifically oriented sub-layer which if you rotated the mat the pointer did some wacky movements.
A mouse is a lot closer to it’s mat than this is. Extreme magnification like a mouse uses only works in mouse-like cases.
Only the cost of this machine will hold me back in buying it. The concept is great, you can do large projects but you don’t require a large machine. If its memory allows it you could make a project the size of a football field with a machine the size of a hand tool and great accuracy. I would not mind moving it by hand and if manually moving it is really the biggest problem, I think that they will come up with a version that has caterpillar tracks and rides across your work piece. But I’m very sure that version will be much heavier.
My father always told me to buy a decent tool, spend a little more money and you can use it the rest of your life. “Quality tools only needs to be bought once”. Now I do not know about the quality, but the concept is solid. Despite of the cost there is another thing that scares me and that is the tape. IF in a few years something bad happens and the tape cannot be bought any more then this great tool is useless. I sure hope that the next version does not require tape or other reference other then the work piece itself. I fully understand that that is a big challenge, with reduced contrast due to dust and dirt. Perhaps a complex configuration of laser lines or projected references from a fixed location (clamped) on the side of the work piece to let the machine know where it is and where it is pointing to.
To the author of this item: I do not see this as an advertorial, just the story of a writer who believes in what he has seen. Please continue in writing with this spirit.
Please do not stop watching TV either.
Tape!! Taaaaape…..
Available for PreSale now! Use my referral link for $100 off! https://preorder.shapertools.com/ref/A8JX6BMBW
Yeah I think that’s crossing a line, you should probably cut that shit out.
Every time I see this tool, it gets better. But what really sells me isn’t the feature list, it’s the evidence of the testing and development smarts exhibited by the company behind it. The backstage stuff is great.
“The backstage stuff is great.” Marketing 102.
Check the coverage of the tool from the “bigger” sites. Wired, TechCrunch, etc. Only Hackaday has any content that is interesting about a new tool that is interesting to most of us. None of them have pictures of the mad hacky original version. None of them have the cool test rigs and hacks that went into it. You’re Welcome.
My comment was praise (for including the interesting “backstage stuff”), not criticism. “Marketing 102” was intended to refer to marketing that’s better than what you get in 101.
Oh! Thanks. Sorry, probably letting myself get a bit too touchy about the subject after reading the comments…
I’m really excited to see this project finally become a product. I got to use an early prototype at MakerFaire sometime ago and was impressed with it then. To see how far its come is just amazing!
I went ahead and pre-ordered mine…for those on the fence and maybe $100 off will tip you over, here’s a link where we can both save. https://preorder.shapertools.com/ref/21JHXJAM7
You have more than a year until it is shipped. I admire your patience.
Early Ultimaker orders took 6 months (when the whole 3D printing thing was new and hype). So it’s not that uncommon for new and different product to have a long waiting time.
Plenty of time for a competitor to see the weaknesses.
Can I somehow use my roomba to drive this thing?
Yes, if you know how to use tape. If not I recommend you to leave it to a professional tapeer. That stuff isn’t something you want to mess with if you don’t know what you are doing.
Can it mill dogshit?
With liquid tape and a crappy bit it is possible.
Available for PreSale now! Use my referral link for $100 off! https://preorder.shapertools.com/ref/A8JX6BMBW
Brave soul.
I think it is neat and I appreciate the hands on information. Since it is not just another 3d printer or cnc mill it is good to see how it operates outside of the labs. I see it as yet another tool that will not necessarily replace anything right away. I want to purchase a CNC router and will probably stick to something like a shapeoko simply because I want to do more, like 3d bass relief. I can’t imagine trying to do complex operations that take hours with a hand operated machine. This tool will simplify making quality stuff (signs, templates, etc) since the computer is assisting. It takes hobbies up a level and makes results more professional with less time or experience. This reminds me of the Silouette I bought my wife, it takes our shirts (and others) from puffy paint cringe-monsters to professional looking items.
The problem is going to be the price tag, I am thinking $900 at max before I would even look at it.
Price wise, the router part looks a lot like a Dewalt DWP611. Which is already $600.
$112 not $600
https://www.amazon.com/DEWALT-DWP611-Torque-Variable-Compact/dp/B0048EFUV8
Either my math is way off or this very page comes in at ~21MB (!) with all its GIF animations and whatnot. Are you serious?!
I don’t know. Why should I count the MBs? Does it load slow because you have bad connection?
What’s holding me is US preorders only, and next year delivery.
However, i find this tool awesome, and every time i see more about it, i want it more.
I’m currently in the process of building a CNC, and it’s quite some work. I may end up between 1000 and 2000$, and i’ll have a 600*600mm work area. Not that big, but still, it’s going to be a big enough machine for me to wonder where i’ll put it when not using it.
If i could buy it now, i’d do it right away (even if i would probably build my CNC, because!), as it would cover the vast majority of my needs. It would handily replace my router (that i’m bad at using), my jigsaw, circular saw, my electric coping saw (i don’t know the English name of this tool, “scie à chantourner”) that takes a lot of room, and whose precision in my hands are much lower.
So with that tool, even at 2K euros, i could replace at least 600€ worth of other tools (i’d obviously keep them, but appart from the drill to drill in walls, i don’t see why not use this instead). This one tool remains compact (as of now, i have bins of tools), AND i can use my skills in CAD design rather than my bad wood working skills.
As of now, i have NO tool that i can use to make perfectly straight and positioned pocket cuts in thin metal sheet (really thin, it’s for frontplates). I’m building my CNC for this purpose, but this would do perfectly.
I could also work on full plywood panels, and the best part is that i could just put it standing up, rather than finding a work area of 2*1m flat. I can reach anywhere on a flat panel when it’s up against a wall, but when it’s flat, i can’t unless i can walk on it.
I can work easily on wood beams without a problem with such a tool, whereas i have no solution as of now to do it.
Heck, i could even go to buy raw materials somewhere, have the tool powered by my car battery, and make pre-cuts in the parking to have pieces that fits in my car, and still maintain the sizes i want to cut later on. And when at home, i get to finish the cuts properly.
I see so many uses for this tool…
And as for the tape being a consumable… well you’ll buy router bits anyway, and those are way more expensive. So what’s the big deal of spending a few bucks on a reel of duct tape?
i’m pretty sure we could make it if needs be, anyway. perhaps even simply printing the patterns on paper, and using clear duct tape to tape it in position. If that’s all you fear, meh, i don’t see the big deal with it.
And whereas i’m all for reverse-enginering, and reproduce this in an open design (i’m all for open design, open hardware and open source -it’s even a purchase factor for me-, so if someone does an open hardware version of this, i’m all for it), while positioning with computer vision is a solved problem, doing it
accurately on a moving ad vibrating CNC, with dust and all is far from easy.
I’m a computer scientist (i have a PhD in machine learning), however this is not something i’d want to start working on
as a hobby. There’s simply too much work. I think that there is a great value in their software work.
All in all, for what it can do, i don’t think 2K is such a ludicrous price. I’d be glad to buy it at pre-order price (it was even 1300 at some time!) but sadly they don’t sell out of the US yet. And i think i’d rather pay more, but have my money until i can buy it to have it actually shipped quickly to me.
Also, hackaday writer : good article. You’re completely allowed to like a product, be enthusiastic about it. I also think of it as a revolutionary tool, as a CNC that could be used in a small apartment, and replace many other tools, as well as open new uses (engraving cool patterns on wood beams in your home!). I don’t see this as a hidden ad, but as someone being enthusiastic about something. Another post was really enthusiastic about the new prusa, and i don’t see the problem.
In the end, we’re all hackers here, and most of us are far from dumb, so even if the product were to end up being bad, or unreliable, that’s up to each to think before buying a pricey tool , read actual reviews, articles, and decide weather or not you have enough confidence in the tool to be good enough.
As of now, i feel like that i’m a little bit too hyped, since i have not much proof yet of it’s longevity, serviceability, etc.
However, what i see is a cleverly designed tool, proper scientific testing of elements, a lot of work in incremental improving the prototypes, etc. All in all, i like what i see, and i think i would have done things in a similar way if i had to (i mean the conception process, not the actual product).
I *FULLY* support everything you say!
$2K is *not* expensive for this tool. Compared to annual salary, it is far less than what a TV would have cost when they were first released to the public. In these days of ‘time is money’, when your average carpenter might charge $100/hr, then s/he only needs to save 20 hours to pay outright for the thing! Having to work slower to stay ‘accurate’, “tidy” up inaccurate inside-the-line work and re-do work because you cut outside-the-line will blow that 20 hours out in a week, not to mention materials if you outside-the-line a 6 foot solid cedar table-top!
The advantages of being so small and so portable are huge! I can’t believe that people would claim a CNC bed is better! Although you could run it from an inverter or generator, would you really take your CNC bed machine out to a worksite every day? I doubt it.
And the scaremongering with regard to the tape! Crikey, get over it! The reviewer specifically says that they (the manufacturer) tried making their own, but it didn’t give them the accuracy they really wanted. So I take from that that (if you were really are that tight) that you *could* print your own and live with a little less accuracy.
It is well priced. I’m saddened to see it is still so far away, both in time, as well as only being available in the US. Otherwise I would go out and buy one this very afternoon.
I agree; compare with other sophisticated woodworking tools, and $US2k is not too much. It is unfortunately too much for me. Damn.
“you’ll buy router bits anyway, and those are way more expensive. So what’s the big deal of spending a few bucks on a reel of duct tape?” With the Origin, you have to buy the same router bits AND the fiducial tape, and the tape costs a hell of a lot more than “a few bucks”.
Oh my god, how will we ever pay for a $15 roll of tape? I could barely afford my $20 roll of toilet paper printed with Obama’s face!
Great tool, if your day to day work regularly requires you to cut complex and precise holes “on site” and in place rather than allowing you to use a CNC in your shop then assemble on site.
They should send one to Norm Abrams. I’d buy one with his endorsement.
He sold out a long, long time ago.
I don’t understand how the device aligns the design with the factory edge of the workpiece. Let’s say for the sake of argument that I want to inscribe the words “Coffee Table” on my existing coffee table, that it measures 24×48 inches, and that I want the bottoms of the letters to be 6 inches from the edge of the table. I draw the design in Inkscape, upload it to the device, put tape on the coffee table, wave the device over it so it can scan and map the tape, mark the center of the design on the table, and set the device down more or less on that mark. Then what? How does it know how accurately I’ve placed the device at the exact centerpoint of the design, where the edge of the table is, and its current relationship to it? Would I draw a box on the workpiece with a pencil to mark the left/right/top/bottom edges of the design, then eyeball the alignment by looking at the screen?
I’d expect that it would only need a mark placed in the center of the table, easy to measure out with a tape measure, and a second mark X distance from the center along a line perpendicular to one edge of the table. Poke in the table dimensions and the router takes care of the rest from its scan of the surface with the rows of tape applied.
Okay, it cuts in 2D, but what about 3D? Could I make, say, relief maps with it as I could with a gantry router? It seems ???????????????? unlikely.
I was really excited about this at first, but the more I think about the likely limitations the less I believe that it has value anywhere ???????????????? the asking price. If it has to cost that much to be profitable for Origin, then I suspect it’s doomed. But, we’ll see what the ???????????????? reviews say.
It has Z axis movement and I would assume adjustable depth of cut. Don’t see why it couldn’t do 3D carving by using a V or round nose bit and ‘scrubbing’ the thing back and forth over the area until the carving is complete.
The limitation to 3D work would be the size of the baseplate. Tipping a side into a hollowed out bas relief would not be good. Solution to that is to have a removable base layer like most routers so larger plates can be attached. The company wouldn’t even have to manufacture them, just provide data files to have it cut out its own accessory bases.
So, I should choose the Origin over a gantry router, then spend loads of time & energy working around its limitations?
If this thing cost $500 I’d buy it for the rare times when its unique capabilities would be useful, but at the asking price I don’t see how it could ever pay for itself over using other methods. Still, I suppose you can’t put a price on impressing your friends with cool toys.
Most gantry routers that are able to cut a full plywood sheet won’t cost just 2K. Even so, you have to be able to fit it in your house. So if i can’t, i’m not allowed to have a CNC? this one allows me to.
I don’t say the gantry router has no use. It’s probably better for some uses, and this tool is probably better for some other uses.
Instead of considering that people only want that to show off, try be less condescending and consider other point of view…
There is NO WAY i could have a full sheet capable CNC where i live, it would cost me way more, and that’s not even counting transportation. And with a classic CNC i have to worry about correct zeroing, securing the piece correctly to the table, etc.
Your comment is similar to someone saying “why buy a large router when a small mill is more accurate”. It’s different uses cases.
And if you need to work offsite? Go at a friend and work on stuff? Or simply want to carve nice patterns on the foot of this massive, but uggly table that you scavenged?
What if you want to work on the surface of a really thick material, that won’t fit your gantry?
But i guess you can’t put a price on refusing anything that doesn’t suit your needs, consider it useless, and, all in all, rehashing the “could be done with a 555, so it sucks”.
I most definitely did not say that it’s useless—I’d love to have one, if the price (including the consumables) were more reasonable given its limitations and if I had more confidence in Shaper (the unexplained long wait, the wide spread of pre-order prices, and the weak details on the fiducial tape all make me suspicious).
As for size & cost, I bought a little gantry machine for $2,200 some years back that has a working area of only 13″x24″, figuring that it would get me started and I’d soon replace it with a larger model. But I’ve only a few times needed to cut something it couldn’t directly handle and have so far always been able to find a workaround, so even though I have the space reserved for a full size ShopBot I don’t see myself buying one in the near future.
Your use cases are a bit of a stretch, with the exception of working offsite where I’ll grant that the Origin could have a big advantage. If you do a lot of complex, precision work in the field (that’s impractical with a standard router), then the Origin is certainly worth considering if it doesn’t turn out to be vaporware (like the GlowForge).
What can it do that other CNC tools either can’t or ones that can cost much more than $2,000 and are larger and more cumbersome to setup, and require the setup to be repeated when moved?
Install a diamond grit cutting burr and carve stuff into concrete. There’s at least one portable gantry device that does this, and that’s all it does. Want to increase the capacity? Pay up more for the longer rails, and you’ll still need the shorter ones for smaller areas.
I assume the sidewalk carvers could be adapted to doing carving into wood floors, or even tables and countertops, but you’d have to work around the space taken up by the rails and working on things too small for the supports to set on would be a problem.
Think of this, a business wants their logo carved into the concrete outside their door. Put on a UHMW baseplate to resist being scratched up byt the concrete, install a diamond burr, throw down some of the tape, put on some kneepads and after spending a minute sweeping it around to scan the area then position the design, start carving.
Next, the business wants their logo inlaid into the middle of their floor. Same process, just different cutting bits, and the material to be inlaid into the floor can be cut from a sheet of material using the same tool and design file, just cut outside the line instead of inside.
To finish up, the business has a counter covered with sheet metal and they want their logo engraved in it. Same tool, same design. Use a V engraving bit and set the router to cut on the line.
One tool, one design file, three extremely different materials, and the operator does not need to be extremely skilled and precise, while the tool does not allow oopsies. If the operator pushes beyond its range of automatic adjustment it lifts the spindle.
If you want to clamp a fence across a sheet of plywood to run it along, you’d only have to be within about 1/2″ or so of straight. The router will continuously compensate for the crooked fence, even if the fence is a piece of board with a bit of a bow in it. That capability alone has the potential for speeding up work with plywood and drywall a lot.
I could see the company licensing their domino pattern to a drywall manufacturer, and making a smaller version of the router like a RotoZip. Pre-print the back side of the drywall with the domino pattern then set the router calibration by setting it at two corners with its camera facing onto the sheet. Since it has the patterns pre-stored it wouldn’t need the scanning step, the calibration is just to account for offset on any given sheet.
Just buy an actual mill… I see no real point to this over a mill.
let me just grab the mill from the cabinet…..
Or mill the end edge of a 2.4 long shape.
i can easily take the shapper to a job site. a mill, not so much.
This looks intriguing. I am not a CNC expert, but I’d have to assume there a standard (like Gerbers are to PCB fab) for the input file to such a machine and that this device would accept it. Is that the case? If so, I’d further guess that such a thing becoming popular would lead to the 2D version of thingiverse as a public repository for designs.
The input file is simply a vector graphics format. It can be produced by Adobe illustrator, sketchup, or many other applications. The company mentions their own public repository called shaperhub.
What about metric units? We didn’t get the response, for the remaining 95% humans of this world, it’s an important one.
Sometimes I have to convert mm to inches.
Not that big of a deal; maybe the Internet has a way to convert units? :P
I’ll bet they will eventually support Metric if/when this becomes a common product. It would be a simple firmware update anyways.
Of course i convert sometimes, it is not that difficult. But while using such a tool I would not like to be distracted by such a task as converting units. And SI/metric units are around for sufficiently long time that this inch and feet stuff should have died out ages ago. Don’t forget: we have already the 21st century.
So it’s not the question of “big of a deal” but if a >2000$ tool is built the right way.
I asked too when I used it and remember it just being a setting in the software.
Yes, It handles metric units just fine. I do all my cad work in metric when cutting things with Origin.
-Jeremy from Shaper
Careful mate – ‘they’ will burn you at the stake as a witch.
If you’re using this in a shop environment I wonder if you couldn’t just use cheap projector or two pointing down at the workpiece to project the domino patterns onto it, rather than using tape. It’d be easier than placing the tape manually (you could even have a computer generate the placement of the projected dominoes) and not leave any residue or get peeled off during work.
Neat idea, however, it would be impacted by any move of the projector relative to the surface, ambiant lights, and the position of the operator while cutting. But it could be an interesting solution!
Il like the tape however, for the fact that i could just put some tape, start a work, stop when i’m tired, or do another more urgent work, then come back at it later, without having positioning issues.
I wonder about the resolution of the projector, too
Vibration would make the projector impractical–the accuracy would be terrible. Whatever generates the fiducial markings, it has to move with the workpiece. No holddown method is going to keep the work stable within a fraction of a millimeter when someone is shoving a router around on it.
The vibration also makes this guiding system position accuracy terrible, the camera on the whole thing vibrates, there isn’t any video about hard material cutting, even hard wood.
milling aluminum with the shaper origin
https://www.youtube.com/watch?v=q8GFpSCK6Jk
Is it possible to mill PCBs? Anybody tried yet? Otherwise a combination of Shaper Origin (or second gen), Othermill and a From +1 3D printer would be an amazing shop where you could build a lot of things with very little space requirements at a reasonable price (below 10k$).
I’ll bet the Origin’s accuracy will never be good enough for milling PCBs.
Never!
Do you ever get tired of being wrong? https://community.shapertools.com/t/pcb-milling-with-origin/1321
Ok, I did not what to comment on the other advertisement article about that small plastic milling machine with a metal milling machine price tag (hahaha, these articles are like the shopping channel commercials), but this is another thing.
This advertisement campaign should have been at least $2 million, so giving away some of the early products is not a big deal. I clicked through all the advertisement videos, and I can tell you this product is total useless for real industrial use.
When something is pushed so hard on every advertising channel, than you should be really careful about the product.
It’s just a toy hobby machine, with real limitations.
So here are the points:
It’s too expensive. (well if something works great it’s not a issue)
The tape just does not work in real industrial environment. Here the main problems, the camera resolution, the dirtiness of the camera lenses, tape on not straight surface etc.
Real problem is in the a vibrating motor guiding mechanism. The mechanism life expectation IMHO is less than 200 hours, the nuts and the guiding motors wear out from the vibration, so good luck cutting a straight line after 100 (or less) hours usage. The cut surface will be rugged or lumpy but not straight.
Comparing this to a router is just ridiculous. With a router you can set the cutting tool feed rate precisely, rails and motors guide the tool, here your hand movement sets the feed rate, and a low resolution positioning system guides the cutting tool. Adding up all the errors from the camera, the calculation errors, the tape, the vibration of the guiding mechanism, the system delay (you push the tool, it has to calculate the correct position, move the guiding motors while you already moved the tool etc), and you end up with a very very lousy precision and surface cut.
You can’t cheat nature (physics), a cutting tool must be in a rigid fixture and guided by a rigid system, to be able to cut nice surfaces.
So this product as the plastic milling machine is more like a toy, an expensive toy, not a real tool.
That’s my opinion, you may don’t like it, so be it.
Call the wambulance. I’d like to see some evidence for what you’re saying must happen to the motors by default.
I just ordered one for $1500. Use my link and save $100: https://preorder.shapertools.com/ref/79WYV8BW6
Sucker.
What i’d like to see is this cutting metal (maybe V2), not think metal or anything, just 1-3mm. That would be really cool :)
Ben Krasnow actually did this a while ago, using one of their earlier prototypes. Seemed to work well on thin aluminium.
I pre-ordered and I want one of these right now. I have been so close to pulling trigger on a cheapie CNC router, but this is a much better tool because it can work with huge work pieces.
I’m so excited about it I’ve been considering building my own to get it sooner….
Drop an android/iphone on a 3d printed mount (on an existing router) and use the integrated camera for the machine vision and positioning. OpenCV should be able to do the heavy lifting on position feedback.
The cam mechanism is quite clever and makes implementation pretty simple for XY correction hardware. For most people doing thru hole cuts, I think it would be OK to drive the Z axis by hand using on-screen feedback.
I can see an open source router-add on version of this tool come out for a hundred bucks in a couple years. Or, maybe not… they are probably crafting the claims on their patents now.
So why to you pre-order? To ???????????????????? save a few hundred bucks? September 2017, is a long, long time away, and there could be a lot of developments before them. And by the way, patents could not stop an open source version, they would only restrict the ability to sell one (and only partially, at that).
Given the very high price of this tool combined with the possibility of an alternative solution, it seems to me that it makes the most sense to wait and see how things turn out before committing to it. Yes, they say that you can get a refund at any time. But what happens if someone else starts shipping a superior (or equivalent but less expensive) product eight months from now? Or an ingenious Instructables version appears that, while not as finely-tuned as the Origin, gets the job done for many people? Shaper could be under a lot of financial stress and unable to meet the demand for many refunds.
Have the many failed (or at least disappointing) Kickstarter campaigns taught us nothing? The hype is strong with this one, and I predict a lot of buyer’s remorse.
Demos of a ???????????????????????????? machine that looks very exciting but won’t be available for over a year, with no explanation for why. Suspiciously-large discounts for giving them your money NOW—the sooner the better. A referral program that looks just like a classic pyramid scheme scheme (remember Herbalife?).
Anyone else smell a rat?
If tape cost gets too high, someone can easily make a multi-page pdf file to print out on sheets of mailing label stickers. Even an inkjet printer would very likely be plenty accurate, but if not, then a laser printer certainly would be, after calibration. Or it might be as easy as just photocopying a few pages of these stickers. I say a few pages because you can’t just photocopy the same page over multiple times for use on the same project because the patterns probably have to be different across the full field of view on a single project.
I ordered one today, use this link to save $100, https://preorder.shapertools.com/ref/WDCME5Y0D
This thing is amazing! No more circle jigs! I do a lot of design in sketchup for trade show booths and convert different components (complex curves for wall panels mainly) to vector files to cut ribs on on our 4×4 cnc. Before I had to go from vector to a cnc program to g code and was limited by the bed size. With the shaper origin now I can just go straight from vector to cutting and am no longer constrained to a 4×4 bed. Awesome! I just bought mine, preorder yours using my referral link below and we both save $100!!
https://preorder.shapertools.com/ref/U8MX9QGUU
I’ve debated the cost for a long time. But in the end, a lot of what drives my own creativity (and that of the students I teach) is the excitement of exploring a unique take on the tools and materials we all love. I’m willing to support clever ideas. Here’s my pre-order code if you want to save $100 and help me defray the cost of getting clever ideas into the hands of people who make more clever ideas.
https://preorder.shapertools.com/ref/V2XDK3DW2
As a high school teacher I think this is a great tool to use in a high school woodworking design class. Help me fundraise to buy on of these tools for my students by using my code, and you’ll save a $100 as well!
https://preorder.shapertools.com/ref/N98QCM3KV
September 1st this thing jumps to $1899 but if you buy before then and use below link, you can get it for $1599! No scam, it’s a referral program, you save and I get a discount too. Win win! Fyi, this discount is good until September 30th 2017.
https://preorder.shapertools.com/ref/B9D3TY5CA