On occasion I have encountered portable soldering irons and my impressions of them have ranged from nearly usable to total rubbish. While using a popular butane powered model and pondering if it was really any better than a copper wire and a candle a thought occurred to me. A regular old Weller station runs on 24 volts AC and performs all of its temperature regulation in a magnetically activated thermostatic fashion and all of that goodness occurs within the hand piece itself. It stood to reason that it could perform just as well with a DC source.
In this instance we are ignoring the negative effects of switching DC current over AC current on mechanical contacts. After all we are “In the Trenches” wherever we might have need for such a device. Using a couple of gel cell 12 volt 7 amp hour batteries freshly removed from a UPS I strung them up, and there you have it, a totally battery operated iron with performance equal to that of the one at my bench.
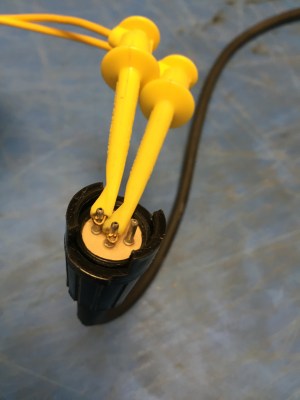
Right at 24 volts the iron Thermocycles at the same rate as it would be while using the bench top supply for it. Just sitting under no load it cycles about every ten seconds and there was no perceptible difference in heat capacity or performance. A fully charged pair of batteries will last all day. The on state current draw from a full charge (13.5 volts on each of the batteries) yielded about a 2 amp draw. As the voltage began to decrease the current off cycle would get shorter as one would expect, but no drop in heat transfer was noticed until the batteries were well depleted and that took most of a work day.
For this instance I used the hand piece from the venerable Weller WTCPT station. For ongoing use I would not recommend this due to the use of a mechanical contact within the unit and switching of DC can reduced the life of most mechanical switches. Currently I am awaiting the arrival of some cheap eBay Hakko handpieces; I am sure they are knockoffs, but fine to experiment with a simple PWM with a feedback loop controller as the basic Hakko design also utilizes a 24 volt source. An automatic shut off timer would also be handy to avoid premature battery abuse due to a forgetful operator.
I’ve thought about replacing the heavy transformer/stand with a little 40W, 24V switching wall-wart so the whole thing would be easy to just throw in a bag or tool box. Just re-terminate the end with a standard DC Barrel Jack.
Anyone done this?
I use a cheap Chinese knock off of a Hakko 936 with a micro-controller regulator (PID) and a laptop power brick (19V 6.32A) and it works perfectly.
In most cases you could probably use a lower voltage than is rated for the iron and it would just have a higher heating duty cycle but don’t skimp on the Amps or the power brick wont last long.
More data please. I’m dubious about the ‘all day’ claim, given a 10s cycle time (at what duty cycle?) at 2AH from a 7AH source and the need to constrain yourself to 20-50% depth of discharge tops for any longevity (see battery data sheets).
Empirically found. the heating duty cycle is actually rather small. Well below 50% when its just sitting there. Also I was turning it off when it was going to sit idle for more than a few minutes. I happened to be wiring a pair of 24 channel snakes at the time. The batteries used were MK brand ES7-12SA types which can be found at http://www.mkbattery.com/documents/5725MK_AGM_SmallSealed_v5.pdf and battery longevity was not a concern because I just needed to get it done. I was more concerned with destroying the little contact inside.
Your mileage may vary.
The Hakko clones require a base station to do the PWMing. I threw together a controller for one, once, out of scrap and crap I had lying around, when my Sparkfun station wimped out — but I don’t have schematics or anything. Runs off a Dell 20v brick from an old laptop, and a really simple circuit, and there’s no temperature monitoring or anything — it’s basically a rugburner with cycling, lol.
Note for anyone with a Sparkfun station — if it’s the “937b” model they sold for a while — the manufacturer you’re looking for is ATTEN (yes, it’s supposed to be all caps).
Off grid solar folks should print this out for the hint, for the day their charge controller dies leaving them with unexpectedly dead batts… They can tear into it with an iron jumpered straight from the panels.
I actually tried this. you really need a high peak voltage. The modules I had peaked out at about 21.5 volts and the iron never came up to thermocycle. It worked, but did not have enough capacity to be useful. Panels that could supply over 24 volts under load should work fine. Just make sure the voltage is not so high that it burns out the element and switch before the thermostat can kick in.
Oh should any thoughts arise as to how useful this would be outdoors, be warned the lightest breeze can really suck the heat out of iron and job. I’ve had to bring the 75W out to the car before for wires youd think a 25 would handle.
I have the same problem, but indoors as well, as it’s not related to wind.
My Atten 938D does indeed reach the right temperature but any mid to small sized copper track sucks a lot of heat ruining the soldering process. setting the temperature very high solves the problem only in part and brings other risks. I thought there was a bad contact between the heating element and the tip, so I tried pulling and setting back the heater in place, changing it then changing the entire hand piece to no avail. The answer to me is simply that the hand piece does not have enough thermal mass to sustain the loss of heat during contact with another surface. This is akin to putting a 10uF decoupling capacitor where a 100 uF one would be needed.
Some beefier tips with additional thermal mass could solve the problem but no way I could find them, so I ended using a Goot solder gun paid 1/5 of the Atten.
You may want to try T12 type solder tips. To use them, you need to adapt a T12 handle to your solder station. The difference in thermal power between M900-T and T12 is very big.
I’ve already observed that relays rated to 200+ volts AC are usually rated only up to 24VDC. Is this due to the negative effects of switching DC voltages? Can you point me to any literature about it so I can learn more? (I’d assume higher voltages -regardless of being DC or AC- should be worse because of greater arcing potential…)
DC contacts don’t break the switching arc because there’s no zero crossing. Hence the need to use such a low voltage that the arc extinguishes itself when the contacts recede.
file:///C:/Users/Owner/Downloads/ENG_CS_13C3236_AppNote_0513_Relay_Contact_Life_13c3236r.pdf
There you go.
oops. Copied local link. Here is the correct one.
http://www.te.com/commerce/DocumentDelivery/DDEController?Action=srchrtrv&DocNm=13C3236_AppNote&DocType=CS&DocLang=EN
Just one problem with DC after a short time you need to reverse the poles as the magnetic temp switch is effected by the magnetism created (rising temp or just going down, depending of the polarity). Have used this in the field cos the transformer was to heavy with the rest of the toolbox to go into the plane as cabin luggage ( i am talking mid 80s).
This is why I am looking forward to trying it with a Hakko type iron.
If the HAAKO is electronically switching AC it’s most likely using a zero crossing SSR which won’t work for DC power because it will never turn off. We use zero crossing SSRs in our mash controllers and boil controllers. Tom
As a matter of fact it does switch the AC current. I will build a suitable controller for DC use. They heating element wont care if its being fed by AC or DC.
If you use an H-bridge you can also correct the DC related problems by providing both a zero switching point and evening out the applied magnetic field.
I’ve had that happen with DC relays.
If you need to solder in a car, buy a 12V to 120V AC inverter – useful for other stuff too..
Weller portasol Just avoid plastics where the exhaust is on the tip
Neat idea!
However I have doubts about the current handling capabilities of those grabber hooks.
3 amps for Minigrabbers. I have used them up to 5 amps and they have not melted. Not recommended though.
http://www.pomonaelectronics.com/pdf/d4233_100.pdf
Oh, number soup. the micro grabbers are 3 amp. the mini grabber (used in these jumpers) is 5 amps
http://www.pomonaelectronics.com/pdf/d3925_k4176_k5522_1_01.pdf
sorry.
That’s some damn good documentation. Pomona FTW
I’d highly recommend their “test lead wire” Really flexible and high current stuff.
Pomona is top notch. Always has been.
Great for when you need to solder something live, but the grounded irons short out.
If it’s live you can make it weld itself :-D
There was an incident report on a contractor before at a place I worked at long ago, he managed to drop a spanner into the 3 phase distribution box and made some magic smoke and got a free trip to the cemetery.
Magic blue smoke does make people disappear
In safety training we were shown what happens when you drop a shifter (spanner) into a 12KV distribution box … it is equal to about three sticks of jelly. There was no such thing as an arc or blast shield back then. It’s basically a free creation.
Oddly enough people all over YouTube seem to test their spot welders on wrenches, and yet no (known) case of someone dying.
My hunch is the instantaneous ultra high current surge that created some sort of deadly emission. Though it points to ponder what..
Thanks for the interesting story. Its as if you never run out of weird phenomenons in the world of electronics.
Power = Voltage Squared on Resistance.
12,000V ^2 = 144,000,000 and the resistance of a shifting spanner – lets say 1/100th of an ohm.
So that would be 14,400,000,000 Watts – how many spot welders would that run?
The power is not as dramatic with three phase but the death is still the same. Vaporized and extremely vaporized are much the same for a human.
All correct RÖB
Where I was getting to was, the vapors from a
Wrench under a spot welder have not killed anyone
Thus far. Versus the instance mentioned above that did.
That’s why my conclusion was vaporized vs extremely vaporized had a varying level toxic potence.
A wrench dropped into a high powre distribution box is not simply ‘vaporized’, it is plasmatized(Is that a real word?). The plasma travels outward, and will both burn and shock surrounding matter, including a human body.
My portables
http://s.productreview.com.au/products/images/98661_weller_portasol_selflighting_psi100k.jpg
It’s not ideal for every situation and tight spaces are a bitch cause it blows holes through plastics or scorches the side of where there relief escapes, hot blower on this depopulates boards quickly.
http://toolmonger.com/wp-content/uploads/2006/11/post-wellerportasol.jpg
Light duty quick jobs great for sitting outside had it since 1996 still works on the second tip ever.
Have an older Gas one than the black it’s a greyish dried out looking plastic I dare not fill it with butane.
Looks preeeetty similar to the Ersa independent.. Hmmm
Gas irons are a necessary evil for field techs. I have the portasol pro peizo, but I’d still much rather be tied to my bench wth the JBC http://www.portasol.com/img_library/products/standard/ppk1_2.jpg
60W (afair), 24V makes 2.5 amps. You don’t need a soldering iron, you can solder with those thin alligator leads, or at least heat the room in winter
I read a lot of comments about soldering. Get a gun! 100/140watts. None of those eastern imports get it, with 100watts max. When heavy power wires or speaker wires need soldered, I wonder how anyone gets by with a pencil iron when the job needs heat. Now and hot, in 3 seconds. Because in one more second, (with solder) you have achieved perfection.
Indeed.
Then and you can easily make your own tip by bending a piece of
14 AWG aire. (Suggestion by Carlsons Lab)
Those weller soldering guns surely aren’t made quite like they were.
Mine was actually manufactured in Easton, PA
What heating power do you recommend? for light PCB stuff like QFP etc.
A soldering GUN is a sure fire way to totally sodomise your board. Lol.
For SMD work, a hot air (re-work) tool is the best option. Though I wouldn’t recommend the cheap ones where the heating and fan assembly is accommodated with the wand.
I was looking at a heat gun with the idea of building some form of accurate temperature regulation in mind, not that that makes a lot of difference because I have in the past modded products for non-intended uses and given up and bought the real deal. Most of the time I have been successful though.
So if you have the time can you tell me what is the advantage of what you have described? over a modified heat gun with better temperature regulation?
Can I add, without offending you, that the word ‘sodomize’ really has passed it’s use by date. And I am a straight person who has raised two kids by the way.
Has it? Hmm.. go figure.. diddnt know.
Anyways, solder guns are best used for heavy terminals.
Ie, binding posts ir putting a bnc connector on a copper clad board for “dead bug” style prototyping.
Ps, its cool. (Not a triggered SJW shitlord, hehe)
Since those SLA batteries don’t have any protection it would be a good idea to add one of those cheap panel voltmeters for voltage monitoring. I believe soldering iron would still work below 21V, so you wouldn’t know your batteries are close to the point of no return.