Today’s engineers are just as good as the ones that came before, but that should not be the case and there is massive room for improvement. Improvement that can be realized by looking for the best of the world to come and the one we left behind.
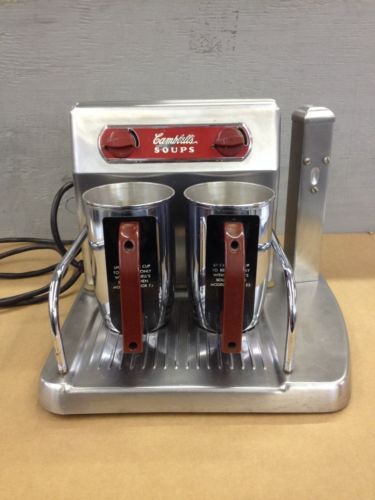
Survivorship bias is real. When we look at the accomplishments of the engineers that came before us we are forced to only look at the best examples. It first really occurred to me that this was real when I saw what I still consider to be the most atrocious piece of consumer oriented engineering the world has yet seen: the Campbell’s soup warmer.
This soup warmer is a poor combination of aluminum and Bakelite forged into the lowest tier of value engineering during its age. Yet it comes from the same time that put us on the moon: we still remember and celebrate Apollo. It’s possible that the soup warmer is forgotten because those who owned it perished from home fires, electrocution, or a diet of Campbell’s soup, but it’s likely that it just wasn’t worth remembering. It was bad engineering.
In fact, there’s mountains of objects. Coffee pots whose handles fell off. Switches that burned or shocked us. Cars that were ugly and barely worked. Literal mountains of pure refuse that never should have seen the light of day. Now we are here.
The world of engineering has changed. My girlfriend and I once snuck into an old factory in Louisville, Kentucky. The place was a foundry and the only building that survived the fire that ended the business. It happened to be where they stored their professional correspondence and sand casting patterns. It was moldy, dangerous, and a little frightening but I saw something amazing when we cracked open one of the file cabinets. It was folders and folders of all the communication that went into a single product. It was an old enough factory that some of it was before the widespread adoption of telephony and all documents had to be mailed from place to place.
The communication itself was regular as far as engineering goes. In fact, if you converted it all to email you’d hardly notice the difference. What was incredible was the timescale. Months and months for a single part. Time scales that would be unthinkably slow today were the norm. A month to get the drawing. A month to get the approval. A month of waiting until a train came into town. With this much time it’s not surprising that engineers and teams of draughtsman could do the work in time. The work that a single engineer is expected to do today in a week.
Now, when you have that much time on a project two things happen. One, you have to be really really certain that the part you’ve designed will work because you don’t have another year to spare. Two, you have plenty of time to catch an error or redo the calculation before anything happens. This slower time scale let engineers do better work. Engineering is still a mind game and the mind needs time.
Timescale aside, another thing that’s changed is the type of technical knowledge needed to make a simple machine. Not so long ago every fastener in a product was made for that product. There weren’t so many off-the-shelf components. Nor were there such rigid and reliable standards. An engineer had to have a more fundamental understanding of materials to do basic work. Now there are so many off-the-shelf components that a more valuable skill in an engineer is the ability to quickly and creatively put them together in a cost-effect pattern.

It’s not that one is better than the other, but many people disparage as seemingly uneducated engineers by a traditional standard climb quickly in the ranks. It’s because the value that’s needed is different. When you can statistically trust that a bolt will perform to its specification that deep knowledge of the crystalline properties of a metal become less necessary. Likewise being able to hand calculate the hoop strength of a hook is not as important as being able to get software to assist in the simulation and quick iteration of that same hook.
So it’s easy to say that there are some hard skills that today’s engineers lack. Skills that can only be won by many hours of rote study that’s no longer common. In the past it was without question the place of a junior engineer to spend days at the drafting board, checking numbers and producing drawings. Only after an engineer had proved himself at these menial tasks would he be allowed to participate in the design process. These days with CAD there’s not much of this work to do and a technician is cheaper than an engineer if you really need to offload the work rather than waste a freshly minted engineer.
However, part of this is simply because the technical landscape of the world is changing so dang fast.
These are just some examples of how the world has changed. In my mind it, at first, paints a pretty bleak picture of the modern engineer. The common stereotype sprouted by the old curmudgeons in the comments is of a person lacking in deep technical understanding who basically only knows how to use software to get the job done. However, I think there’s a new creativity today. It’s important to note that new engineers who become quickly familiar with the software packages, standards, and have a cursory understanding of mechatronics can do some amazing things in a fraction of the time it used to take. They have to have a broad field of understanding. We can’t just know about mechanics anymore. To be fair, it’s not giving enough credit to the schools. We do know all the basics. We can do the hand calculations. There’s just not enough daily exposure to it in our work place and it takes us a while to eventually get that deep understanding too, but the approach is circuitous.
If any of the old engineers long dead could get their hands on today’s tools there’s no doubt in my mind that they would be disastrously effective compared to most alive today. There’s nothing like hard-won skill and they had to win it the hard way. However I think that modern engineers can match them quickly. There’s just a few skills they’d have to get on their own.
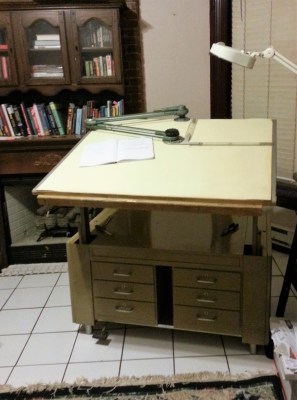
The first is drafting and art. CAD just can’t teach spatial reasoning like hand drawing can. That mind-body relationship of being able to visualize a part and then draw it makes an engineer phenomenally better. Also when an engineer had to spend an entire day or two on a single drawing an enormous amount of thought had to go into the layout of it. In the end it’s all about communication. If a manufacturer can’t read your drawing then it’s useless. If an engineer can’t get up and draw the idea out on the board then it doesn’t matter how good of an idea it might be.
The second is math. The more math an engineer learns the better. Simulation software is one thing, and a really good thing that saves a lot of time. However, anyone who understands the underlying math and can do the calculations by hand is much better. That’s really the definition of an engineer anyway. Any technician can learn the basic formulas, but an engineer understands them. Since a lot of work is done for the modern engineer it’s easy to avoid being tested on this sort of knowledge, but everyone has their day of reckoning and the one who can do the math does better work.
Third is not using the internet. The internet is the Cliff Notes of technical reference. There are whole volumes out there compiled by people who dedicated their lifetimes to a study of that niche. To think that the internet somehow has the same quality of information on a shitty three page document with advertisements taking up most of the real-estate is preposterous. A modern engineer should collect both a full and well-understood library of books as well as being deeply familiar with her local library. The internet is a shitty quick reference and to rely on it is to cheat yourself.
Last is to avoid ageism completely. Especially in the hard science fields like engineering experience truly matters. The more a new engineer can attach themselves to experienced greybeards the better. There’s an art to the craft and it can’t be learned without a master. That is for certain.
Really though, I’ve met old idiots and I’ve met young idiots. Heck, I’ve been (and by engineering standard likely still am) a young idiot. In a hundred years we’ll look fondly on the rocket ships this generation built and look disparagingly on the crappy neural interfaces that won’t even hold together for a month. Only the best will survive time. However, if we pick the best from the past and use the best of today, we can reach greater heights than both can offer.
What do you guys think? Am I on the right path? Is there no hope for engineers of the future? What is a skill that might be lacking?
Absolutely right. The skill most lacking in modern h/w and s/w engineers is the ability to debug.
In the past, you stuck with something, because if you didn’t, you’d wasted large amounts of time and money on components, so debugging was necessary.
Now? Well, if the internet can’t help, you can always just find some new widget, or buy a couple of different boards/components from China for a couple of bucks…
I can’t speak for the hardware side, but I do agree WRT software. I’ve had discussions about such things w/other graybeards, and one conclusion we’ve come to is that at times it might be *too* easy to compile software nowadays – in a lot of cases there’s a tendency to just edit and recompile software rather than to spend time desk-checking it before even compiling it the first time, and tracing things thru in a debugger when something isn’t correct.
Cranks have existed throughout the ages.
Many post secondary institutions have essentially become trade-schools & paper-mills where many students ultimately get ripped off.
Some kids usually take a year or two to learn practical skills when they leave undergrad, and others believe everything they ever need to know they were told in 4 books.
However, these days everything is already so highly optimized to a point where integration is usually trivial. China is a big place, and doesn’t have the same cultural expectations as domestic programs. And yes, we know on rare occasions some desperate individuals buy translated US university course manuals (with the standardized test set) for $18 in HK. You know, there are many funny folks on face-book colluding with friends to win-at-any-cost just to pass the exams…
The instructors know kids… and you are not as uniquely clever as you may believe.
Most kids are not known for their humility, self-respect, or objective rationalism…
but we all started off that way. ;-)
Mostly, we see fresh grads are similar to:
https://www.youtube.com/watch?v=B1UlnriA3PI
nothing strange as we are drilling children this way from kindergarten up to not think for themselfs and do what the teacher asks.
Yeah. I remember our teachers telling us that to get any cpu time they would have to leave their program (a stack of cards, obviously) at the computer room. The techs would run them through overnight and you’d get the results next morning. If you had made a typo, well, your results the next morning would be a compilation error.
I wonder why they didn’t invent TDD way back then? Write the test you know is going to fail, wait a day to run it…
Absolutely wrong. The skill most lacking in modern h/w and s/w engineers–whatEVER a software engineer is, or pretends to be–is the ability to communicate.
“Besides a mathematical inclination, an exceptionally good mastery of one’s native tongue is the most vital asset of a competent programmer”.–Edsger Djikstra
I kin brain inglish and mouth it gud two.
From a software point of view that statement is so so wrong. The communications failure is often the management staff between the software writers and the client.
I r enginrr
Hmmm I would have the impression that small project engineering, a single engineer would have many on the go, working on them interleaved. Maybe things like drafting only being a third as efficient, but they certainly weren’t going to sit round doing nothing at all for a month waiting for correspondence.
Large project engineering was more of a human wave approach where an engineer would have a bunch of draftsmen and technicians under him and there would be an attempt to have as many decision makers on the same site as possible.
Yes, but the time on other projects often gave insight to the project at hand, and, at a minimum, gave time for things to ferment.
I am maybe 90% in agreement with the premise, but having accrued by intent a collection of things the way they used to make them, only 90%. I like being able to say “good” when someone says “they don’t make things like they used to”. Materials are generally better, parts are generally compatible, and few products outright kill people.
The room full of draftsmen under the chief engineer does not have any bearing on that the engineer *could* do the drawing, and probably worked in that room, at least for a period, earlier in his career. The interaction of the larger teams led to more review and often to overall improvements during the design process. The best products were of generally equal or better quality (given the state of the art) as the best today. The worst were as bad as, and often worse than, todays.
Good designs come from people that know that subject inside and out. Poor designs come from people that don’t know that they don’t know. And they always have. It is much easier to not even know what you don’t know today than in the pre-web days, and I have been told by managers “I can know anything you do in 5 minutes because Google.” It doesn’t go over well when I tell them they are full of……
to some extent you are right when you say the best of then measures to the best of now, but only almost, there is so much that we do today that would be flat out ridiculous back then, if not for being actually impossible then because it would have been far too expensive to do a lot of it.
i suspect that this topic, as so many others is far from the black and white, it was generally better then than now attitude that one often hits upon in various subjects.
I have seven projects going on as it write this, all in various stages. Two are near ready for release, one is in the early design phase.
We normally kick off with the customer present, so all requirements are nailed down as soon as possible. Even with email, phone calls are frequent. When I was a “new” engineer in the early 90’s, phone calls or in-person meetings were the primary method of communicating (at least for me).
Don’t forget the “Engineering Culture” where the new guy/gal out of college is given the task nobody else wants.
This can create a “Design By Catalog” failure where the basic skill set was lacking the math to calculate specs.
Been there, seen that, ate the t-shirt.
Is that a widespread thing, giving the new person unwanted work?
Intuitively it seems like having a new person means lightened workload for the whole team so everyone would have a vested interest in making sure that person feels welcomed and is as productive as possible (the opposite of dumping unwanted work on someone).
Yes. It is common. I worked for a very large multinational company, and barring one of the top engineers leaving, the only engineers they would hire were right out of school. They’d stick them with the grunt work no one else wanted to do for a few months, and wait for the new guy to quit. Then they’d hire another one right out of school. Rinse and repeat.
It got so bad that I got to the point I wouldn’t even bother to remember their names. I even told one of them that one
day, telling him he wouldn’t be around long enough to be worth getting to know. It was a joke, yet not. I was right. He left after five weeks.
And this was a company that did work for NASA on the space shuttle boosters.
Take it as you will, but my experience says it’s not easy to get a good education in engineering and then land a decent job that won’t involve getting the worst job assignments, with no effort made to help make you a better engineer, and no ‘mentoring’ of any kind.
Well, unless you were lucky enough to get hired right when one of the older engineers was retiring. Then you had a chance.
Like I said, take it as you will. I’m just telling it like I saw it…
Even with mentoring I found it hard to find a new grad who wanted to work at all. Given coming in late, morning break, lunch, ice cream at 1:30 and afternoon break they were not worth what they were paid. We usually only interviewed 3.5 GPA or above I had one new hire who asked what RMS stood for several times in one week. Most said they were only interested in moving to upper management.
Turning one loose on a cad program they can turn a 2.00 bracket into a 20.00 part in no time, that’s if they ever finish. I asked one new grad why he chose this company. and he replied “because they said could design right off”
After seeing his first try I am pretty sure he thought a 4-40 screw was a piece of ass at 20 to five.
At large companies (ime ~500 thu 30k employees), it’s very hard to recruit graduates at all. They generally have no interest in starting to learn in long-term careers, believing that they just need to write a killer iphone app, or come up with a social media idea, and they’re sorted for life.
Such is the modern world…
I’ll take a straight B student over the 3.5+ GPA any day. That straight B student understands diminishing returns and is probably going to be a better engineer once they have some experience under their belt. The 3.5+ GPA student already knows this stuff, so why would he learn on the job?
Maybe not unwanted, but definitely not critical path. I don’t want the success of the project to depend on a new person. I’ll have them design test jigs, do experiments on components, or work on features for the next version or minor features that don’t impact schedule, but not critical path. Once they’re up to speed and they’re familiar with everything, then it’s time to bring them into the danger zone.
My first job was a lot like that… did some cost reduction projects on existing design but main task was to find second source for components, and to evaluate samples in existing products. I also understood I was a new guy and that was par for the course. The only reason I jumped ship was my next employer offered me a 25% raise.
Certainly menial tasks.
It doesn’t make sense to have the Department manager annotate machinist prints (if they’re even made at all), run crush, slump tests; or what have you if there’s a fresh college hire or intern around to do that.
It doesn’t require any certifications or judgement to complete and even if they take longer to do it, their hourly pay (even if they’re both salary) costs the company and/or client less money.
Hi Mike,
While I can’t speak to the mechanical engineering culture, in the semiconductor industry a new engineer absolutely gets menial or simple tasks. There’s a good reason for it. It takes time for a new person to spool up on company culture and to integrate into the team to the point where they can be effective. Even then, any new person will need to learn the tools and methods the team is using. Often there are internal tools, and if dealing with software or firmware, the person will need to learn the details of how these work before they are ever equipped to deal with an effective workload.
In the past few years, I’ve seen it go the other way too. I’ve worked with new hires that could write complicated software or quote nuclear reaction tables in no time flat but couldn’t work a camera tripod or use a simple radio. I’ve had to spend over a month training PhD’s in basic lab or factory floor practices. It is a fallacy to believe someone who graduates from college is “ready” to jump into a key position. Assuming they did well in school, they are “ready” to learn how things work in the real world, regardless of their pay grade.
To the original point of the article, I often think about this. I’ve worked with engineers who started in the Navy working on nuclear subs and were forced to learn *everything* about analog electronics, and I’ve worked with engineers who’ve come up in today’s “Here’s the bare minimum we think you need to know” culture, and without exception, the guys and gals who put the time in to learn the basics always seem to do a better job, especially when things go wrong. These folks seem to be more creative in troubleshooting and workarounds than the “creative” new generation.
To ramble a bit:
In my opinion, the key point in this article is as follows:
“Improvement that can be realized by looking for the best of the world to come and the one we left behind.”
How can we expect new graduates to be as good as their predecessors if they do not learn the background of their predecessors? I’m not saying there aren’t things we can let go. How many of us need to know how to make a buggy whip, after all? What I’m saying is, if you’re going to work in the semiconductor industry, you should know how a transistor works. If you’re going to work on circuits, you should understand (really understand, not just be “introduced to”) how to build analog circuits. If you’re going to be a mechanical engineer, really understand the mechanics.
Microcontrollers are fantastic tools. I use them quite frequently, probably more than I need to. They are not the only tool in the drawer though. If you can save a customer a dollar in BOM cost by using an analog circuit, you need to know how to do it! Otherwise, you’re just engineering by google search.
Everyone wants to be important. Schools tell us how great we are, how we’ll graduate and be ready to jump right into that 6 figure leadership position. It’s called marketing, and it’s very easy to fall for it because students are a captive audience. I wish students could go through an internship after their first year, rather than when they are almost ready to graduate. A little dose of the real world early enough in the education process would greatly improve new graduates.
We have a small engineering dept (6 engineers and 7 techs)… we are buried in work that needs to be done. There is a learning curve, so yes, they do get jobs like fixture design and the so. So CAD is a requirement. I have an intern working who really enjoys it here… he is doing product testing, designing an environmental chamber for corrosion testing, as well as a number of smaller fixture projects. Everything we ask a new guy to do has value.
Cultural aspiration is a key component to the development of engineers. When driven to achieve some thing, the sciences improve and those in them improve to accommodate to the needs of the people. WWII is a great example of how engineering had a cultural requirement and advanced exponentially. Today, there is aspiration to achieve any thing more than video games and other jingly key items. Most Americans have no aspirations of space as we once did. Engineers are like any one else, seeking a pay day for their achievements but as is supply and demand, most do not demand as much as we once did. We are lethargic and complacent and until there is a drastic shake up culturally, expect more substandard engineering.
*there is no…
I see your point and feel that for most engineers let alone anyone in the workforce, most poeple’s jobs are unfortunately a “payday” or a faster route to being “the boss”. I think on the flip side to what you mentioned is that how many companies that pay well and are legit can one immerse himself in space travel? Defense? Two, maybe three big players? How about in groundbreaking AI? Humanoid Robotics? How about research, whats the barrier to entry for that, have you taken that into account? I know plenty of engineers who took a grad program because the workforce did seem like “It was just going for the paycheck for monkey work route”.
Your idea is very relevant if there is abundance of places and spots for people to get in and excel at but tough when most of the world is hard pressed to spend money on hardware since that requires a lot of upfront capital. I do have to agree that it’s a cultural thing, and also probably a time thing too. You mentioned WWII and that was the reason for so many great advancements in engineering and science alike. WWII it was basically life or death so anyone who could contribute anything was given a chance.
Nowadays when the biggest places to work are usually larger software companies developing features on larger existing systems or larger integrator of 3d party solutions that get bundled into “design”. Worse off I find that most places want a “Rockstar developer” or “genius” only to give them tasks nobody wants or just something impossible given the time frame of things. This ultimately causes a lot of people to be more risk adverse with positions outside of a few big players in tech since you’ll get thrown through the ringer, get underpaid, money wise, conceptual and career growth but also waste your time. 100k+ Saleries sound lovely on paper and in everyone’s head, but 100k+ without personal growth is the same as 100k to push a button for 8 hours a day. This is why you either have people job-hop before they can make a differences where they’re at or leave engineering entirely and go into finance or some other more rewarding field.
I’m all for the space race v2 or tech but with the job field the way it is, it certainly stops people from really trying to help society and instead only look for whats good for themselves. Requiring a PhD + 5 years experience for some positions is ludicrous and with how jobs can be more miss than hit in tech, it’s just not worth the risk in people’s mind
To touch on the AI and robotics portion; while these are innovations, they do not suit aspirations because they do quench human’s nature to conquer things. AI and robotics is actually aspiration to submit to disengaging entirely and most fear that notion that they will become obsolete. Space exploration drove human spirit because of the human elements. War drove innovation because of the human element. AI is more video games, distractions, jingly keys. We must connect personally to some thing for it to drive us personally. This is why sex robots will likely innovate far quicker than most other fields.
Good engineers exist whether there is product today or not. Application is where we fail as a culture. I have met many in the “maker community” who are brilliant and yet completely misdirected. It is one of my largest griefs with this rewarding LEDs, clocks and useless robot projects today, it redirects the immense power of the common maker to novelties. Going to space, building efficient resources, propulsion technology, these should not be idealized as entrepreneurial ventures as you vastly stated above, they should be cultural aspirations. JFK’s to the moon speech drove a personal stake. Leaders (real leaders, not what ever today’s slobs are) should rather than grieve over the planet, put stakes to us as engineers and common people. We WILL build this. We WILL go faster than this. Some thing intrinsic to conquer because in the end, we are but simple species on this planet and we live and breathe by those biological merits. There is a vast resource of mind power just reading HaD alone that should create a revolution of human grasp innovations. It is not being tapped. Instead I read a full page in PopSci about some one who makes broken things which inspires makers to settle. Humans are sheep, they must be herded in a direction for innovation to lead some where. Right now, culturally we are in an open pasture, wandering aimlessly.
Pretty good comment! Especially about the mostly untapped talent delevoping in the Maker community.
I sort of hoped that climate change would be viewed as the next WW II or moon-race level of challenge, with multi-pronged efforts to make fusion reactors practical, refine wind- and solar generation, find the next battery or other storage technology that will make the renewables feasible as primary sources and redefine the grid requirements, full transition to electric vehicles, and so on. But no, too many think it’s some sort of greenie/lefty plot for world domination…
You missed one thorium molten salt reactors which can put a real dent in carbon emissions now and actually lower the cost of electricity while they’re at it.
This is the best comment I have read on this website in some time. Thank you.
http://farm4.static.flickr.com/3057/3039066351_49673e4212.jpg
DItto. I think that as long as their bellies are full and their cellphones keep working, modern society is not interested in achievement. We used to think manned interplanetary travel would be common by now, and there would be outposts on the moon.
The title should be “Are today’s engineers worse?”. There should be no apostrophe in engineers. Don’t want to be a grammar “nazi” but I mean come on people. At least proof read some stuff.
[title]Are Today’s Engineer’s Worse?[/title]
Yes, they’re worse! They don’t use proper punctuation these days! Engineer’s should be Engineers. It’s a plural form, not a possessive, nor is it a contraction.
Quite right, fixed.
Great. How about the other grammatical errors in the body of the article? I counted at least two.
But… these errors are a perfect metaphor for why so much of today’s engineering sucks. Everyone wants ‘cheap’ and ‘fast’, and that usually rules out ‘good’.
Writing isn’t engineering, and not having grammatical errors doesn’t mean good writing.
Thanks for correcting it.
They are just proving how accurate this shirt is … https://www.spreadshirt.com/i-m+an+engineer+i-m+good+at+math+t-shirts-A14352221
I don’t get it… they spelled emginearing write each thyme…
Number one quality in a good engineer: Pay attention to detail.
Do not use apostrophes to make a plural! Check your article title. ;)
Don’t worry eventually engineers will be replaced by artificial intelligence. ;-)
There’s some validity to this. Have you seen the new software packages based on bone growth algorithms? Unbelievable. I watched, in real time, the software removing bits of material as necessary from a part until it got to some optimum level. It was very disconcerting, actually. I definitely felt a bit obsolete watching the computer that day.
neat, happen to remember a paper title or research group or something? that sounds worth looking into.
Genetic algorithms? Software Darwinism. There is a scientist that is kind of a guru of this stuff. Basically, if you can describe the exact needs of the end design, his software can “evolve” a solution based on an iterative process of trying combinations of simple solutions until a final, complex design is figured out.
Careful with the term, “engineer”. In my experience, there are a large number of people with engineering degrees – and many of them with engineering jobs or responsibilities, but the number of actual, capable engineers is a small subset of that pool.
I made a few comments to this fact in the last “engineer” article.
Honestly, the current mindset is starting to get tiring.There is so much defense of the mere title of engineer that makes people raise them on a pedestal. Yet I can count on one hand, the number of truly capable and talented engineers that I have had the opportunity to work with.
The rest were no better than students, ignorant of simple concepts like voltage drop or cable bend radius, or even worse, mechanical stress and wind-loading. They would draw up elaborate schematics of how the entire system was to be installed, and then group some lines together and label them “power cables.” It was infuriating.
It seems that so many people want to be engineers because they will get paid well, but none actually have a solid physical grasp on electronics, or mechanics.
At least in Canada, the universities have no problem cranking out engineers at breakneck pace, and we get bridges that bend and crack, roads that do not line up, and poorly designed light-rail-transit systems, where the trains have to slow down to walking pace in the turns or the lean of the train will rip off mirrors and clip power poles.
I for one, am not impressed by the current state of engineers, and the fervent defense of anyone but them using “their title” just makes me want to change my vocation.
I for one am starting to think that a new career as a “lowly technician” would be perfectly acceptable.
Some time ago in France, they had to do major rework on a new train station platform due to the edge of it sticking out about an inch too far. The first train in went *grunch* into the platform edge.
They wanted as minimal gap as possible. Why not have an air driven sliding or flip up panel with a rubber edge? That could gently press against the sides of the cars for zero gap.
well in that case the ‘zero gap’ specification was successfully achieved! Perhaps that was the engineers revenge for such an impossible task.
I thought bridges that bend and crack are just a matter of tradition in Canada.
That’s right. I just learned on Hackaday that anyone without a PE license will both fly drones into crowds and make bridges that collapse from only 6 bricks!!!
6 bricks? Pshaw, I can do that with 3 bricks and an arduino!
I can brick an arduino.
I can arduino a brick.
Honestly its more of a cultural problem now and then. An old time engineer barely did anything but work and take his work home. When they could get underling they passed the buck downward and took a back seat. Today its much the same, the difference is once the company got their pund of flesh, they will dispose of the gray beard and youngster alike and go into “rerorg” due to budget reasons “Read the CEO needs a new multi million dollar house”. Todays world is designed on attrition and consumption of everyone and everything is made to be consumed. Cynical view.
Why do you think it’s now called “Human Resources” instead of “Personnel”? Resources are meant to be consumed.
I wonder if the % of ineffective engineers is higher today than it used to be. engineering has fractured into many disciplines and its not uncommon for me to find people with ‘engineer’ in their title who have zero ability calculate bending moments, solve ohms law, write even basic software…
It’s almost as though working with people in other disciplines is useful and/or necessary!
STEM diploma mills.
Something I don’t think was mentioned is trial and error, and experimentation. Edison didn’t do much in the way of calculations, he just tried things until he stumbled upon the result he wanted. Not a bad way to solve problems, if you can afford the time and costs.
Software lets us trial and error faster and without any extra costs. I can model two mating parts in Solidworks and check their fit with confidence, rather than imagining it in my head, hoping it will work, and finding out when I build it that it doesn’t fit.
You don’t have to do everything in theory before building, you’re allowed to iterate. NASA didn’t go to the moon on an untested rocket.
Example; the guy who invented the vortex tube that Tony replicated, did so in the 1930s. No flow sims for him, but I’m certain he didn’t sit down at a desk and say “I need to devise and calculate a device which can convert airflow into a heating and cooling effect” and designed it, calculated everything, built it, and it worked. No. I bet he noticed a phenomenon on some other equipment, explored the idea, did experiments, explored the concepts theoretically, and produced a well-functioning unit after all of that. Tony is exploring the concept and design with Solidworks flow sim and a bit of tinkering (tube lengths and stuff) but they are both doing the same process. Tony’s took less time, energy and cost thanks to computers.
Modern conveniences have helped us reduce the costs of development, McMaster-Carr (damn you to hell – sincerely, Canada) lets people have a library of existing parts; that only serves to reduce the cost of production. I can imagine a gear for a purpose, doesn’t mean I have the time and money to make it as I imagine it. Getting a gear off the shelf is smart. We aren’t all building to within 1% of limits like NASA does.
My point is, I think what’s going on in the mind is the same as it always was, just the way it comes out has changed a lot.
Good point re gears. If I am only needing a simple gear reduction in a project, it doesn’t make sense for me to acquire several years of experience in gear design just to pick 3 gears. Much better to outsource to the guys who do have that experience. Now, if the suppliers suck, and many do, then the engineer who can outthink the supplier can eat their lunch, sometimes. Many niche products were developed that way.
If you think things are bad now, you’re not going to like the future at all! I foresee product development taking a strange new path where the generic functions of an object are defined and then software uses a genetic algorithm and trillions of testing simulations to determine the most effective way to build it for your constraints of reliability and cost. Absurd complexity that just so happens to work and cannot be repaired will be the result.
It’s already being done…
Lets not forget about PO (Planned Obsolescence) and its contribution to degradation of the engineering world. Whether you believe the original intent of PO was for good or for bad I believe it has reinforced what you are seeing in the world of engineering.
It’s less planned obsolescence, and more cost-based engineering. In the ‘old days’ many products were over-engineered, either out of a mis-trust in material or “just the way we’ve always done it”. If you look at the first fiberglass boats in the 70’s, they were made with inch+ thick hulls, “just in case”. Today’s performance boats have hulls so thin you can flex them with a finger. The difference is we have a much better understanding of the limits of the material.
In the electronics industry, you must design to a cost target, because you are competing against others and (presumably) actually want to make money and be able to buy groceries next week. This means you build your gadget to meet or slightly exceed the useful life and have the same or a bit less cost of your competitor’s gadgets. Alternatively, you go with thin margins and design something that has a shorter life-span but costs less. As your margins shrink, cost pressure goes up and cheaper parts are used, which reduce the useful lifespan….etc, etc. I personally have never seen a new produce meeting where PO is a point of discussion. The discussion is usually similar to this:
“So, how long is the guaranteed to work lifespan of the product?”
“7 years”
“Ok, so we need to pick parts that will last at least that long”
Much like the boats in the 70’s vs now, as we understand the limits of materials better, parts made from those materials are made to thinner margins of cost and reliability. This means parts don’t have what I would call the “accidental lifespan” they once had. This isn’t a conspiracy, it’s just the natural outflow of cost-based engineering, and as long as we are a consumer society where price is the leading consideration, it is the reality we live in and it’s not going to change.
This. +1 I think this is a major contributor, or symptom of the underlying philosophies. The monster has been created and can’t be killed.
@wilfite – I get what your saying but I think your confusing products that are designed and manufactured with an artificially shortened lifespan not to save in costs but to force customers to buy the same thing far more often then they other wise would have. The Printer industry is well known for doing this; making the life of the printer and its ink cartridges artificially shorter so the consumer has to re-purchase these far more often the they otherwise would need to.
NOTE: While the money in that industry is made via the cartridges/ink (the devices themselves are often loss0-leaders ) the reason for shortening the life of the printer itself is to ensure ever evolving non-backwards compatible ink cartridges.
Every industry would do this if they could. For example If the music industry were able to change the format of how music is delivered every 3-5 years so that customers were forced to re-purchase existing music in the new format there’s no doubt they would do this. Granted the age of digital media has made the physical format a non-issue but the same still applies. if they could force users to re-purchase their product by switching up the file format/type every 3-5 years they certainly would at least try to do it.
A lot of stuff is made to a design life these days because they expect you to buy a new one every three years.
I see some LG devices where the glue holding the front glass to the LCD was stronger than that used to hold the polarization filter to the rest of the LCD.
I feel this was a clear example of planned obsolescence.
Another is soldered on CPUs in laptops or even leaving out simm slots.
I am an engineer — got the degree, and I work making chips. I do have a tangentially related comment about engineering processes.
NASA put a man on the moon in a decade. Could we repeat that same feat with today’s technology? Hell no. The reason is “the process.” Here is my theory:
A bunch of engineers set out to do something, and they do a pretty damn good job. However, one day somebody makes a big mistake (maybe it costs money, schedule, or lives, or any combination thereof). Suddenly we need a new step added to make sure that this never happens again. So a new rule is created that adds a new process on the next design — another design review, another form, another meeting, or maybe even a new job. Eventually another mistake happens, and another step. Eventually, the whole engineering process become a complete mess of extra steps designed to prevent mistakes, but had the side-effect of preventing efficiency.
I design chips for a living. One of our steps is a process called “formal verification” where we run it in two steps: One step is to compare the Verilog to the synthesized netlist, and the other is to compare the synthesized netlist to the place-and-route netlist. I have only been in the chip business for a decade, and only have a handfull of tape-outs. However, I have NEVER seen a case where the formal verification tool has ever caught any real error, and I have not heard any “water cooler” talk of any real errors either. I suspect that the early synthesis and PNR tools did occasionally make mistakes, so running formal verification was considered good practice to detect these mistakes. However, as synthesis and PNR tools have improved, the need for formal verification is becoming unnecessary, but nobody will stand up and say “we don’t need this” lest they loose their job in case of the unlikely event of an error.
Now, formal verification IS a cool tool when you need to verify that a RTL optimization has not broken functionality, or when you want to manually do an ECO, and want to verify that the netlist hack matches the RTL change, but those are the corner cases.
> However, one day somebody makes a big mistake (maybe it costs money, schedule, or lives, or any combination thereof).
columbia jacked the costs of nearly every nasa mission that came after it. even all the ones that didn’t involve heat shielding tiles, people, shuttles, reentry, etc, etc.
Its not like people didn’t die early on in the space race. But back then, those guys were all WII vets and battle hardened men’s men (for what ever that’s worth of means). They faced down death as there were being burnt alive in a sealed space capsule or were crashing to earth in “it might work” kinds of experimental aircraft with the financial backing of a country with a mission to stomp out communism no matter the cost. Death wasn’t a deterrent. It was a risk that was respected, but risk wasn’t as adverse and nasty of a thing as it is today, because people want to live to see another day… And worse yet, other people don’t want to get sued out of existence for letting you die or even risk letting you die…
The culture has changed kids. A LOT.
Lawyers and risk adverseness to the point that we are effectively a culture of pussies…
Mmmm, no. Your thesis doesn’t explain why our dryer has a crap control board with way inadequate pullup on inputs (and blobs of epoxy on the board as an ineffective hedge against humidity triggering them), or why the lettering on the washer and dryer comes off when you touch them.
While the whole litigious landscape is a problem (in some countries more than others) it doesn’t account for plain incompetent engineering. Cheapness does.
You want to see some GOOD engineering? Airplanes. Regulated to hell and back, but seriously dependable, now.
Airlines isn’t just regulations — regulations are for things like maintenance. The actual engineering that goes into aircraft, IMHO, is just because of the extreme consequences that come with failure.
If you completely deregulated the airline industry then the maintenance might slip at the airlines, but the engineering would not slack off at companies like Boeing. It is one thing when a part fails and your clothes stay wet. It is another thing entirely when a part fails and 100 people die.
The failure of American Airlines flight 96 and the subsequent crash of Turkish Airlines flight 981 is clear evidence that without regulatory pressure, manufacturers have no incentive to correct flaws in their systems.
Douglas already knew about the flaws in the cargo doors on the DC-10 but it took a fatal accident (flight 981) and action by the regulators before the problems were fixed.
“While the whole litigious landscape is a problem (in some countries more than others) it doesn’t account for plain incompetent engineering. Cheapness does.”
Well said. I work for a large semiconductor company who happens to sell microcontrollers to companies that make washers/dryers, etc… I’ve listened to the engineers bitch and moan at trying to harden the micro’s against huge transient electrical spikes because the washer/dryer manufacturer didn’t want to spend the money on a full bridge (4-diode) AC rectifier to feed into a regulator of some sort before powering the micro. They figured a single diode and capacitor was good enough and then pushed us to make our IC’s more robust – which ultimately costs more money since it requires more silicon area to harden the thing against voltage spikes….. So yeah – cheapness does result in inferior engineering. All of us cheap consumers bare some blame. Think about how many product choices you made in which you chose the cheaper version and then ultimately regretted it.
Cars have really gone down hill in the past 15 years as well though I blame feature creep and trying to meet the same BOM though some cases.
They really seem to be skimping badly on the materials such as not using galvanized and using plastic parts in locations with high temperatures such as intakes with coolant passages and water pump housings etc.
Kevin Harrelson: Guess what happened this year? The thing you predicted against came true. Boeing slipped at engineering. A part failed and over 100 people died. And there weren’t even any regulation changes that caused it.
Well timed article. In 35 years in this industry, I’ve worn a number of hats and have had the honor of meeting quite a number of really good, capable engineers. Then again, I’ve encountered a number of really bad ones as well.
After observing the careers of a number of them, I think what makes the difference isn’t so much one of pedigree or education, as it is of “stiction.”
Stiction, or the ability to remain focused and doggedly determined to make something work; to fix it, to solve the problem in the face of overwhelming pressures, to push through a mental barrier and force yourself to understand what is often the incomprehensible.
Some might call it fortitude. They’d be right, too.
While education, knowledge and a general ability to add things up are important, they won’t carry one through the years unless you have stiction. Oh sure, there are ‘floaters’ – those who have drifted like so much wind-driven sea foam between projects and employers who are only at a place for 18 months or less and are never faced with the mountain of technical debt they create.
The gray beards all have a couple things in common – stiction is one of them, great war-stories are another. Patience, fortitude, a willingness to learn and change one’s mind even after years of experience, and a kind of surreal determination when their ‘gut’ defies the group-think that’s endemic with today’s “engineers” – all these things and more.
Oh, and a final parting shot. “IT Engineer” is an oxymoron ;-)
> “IT Engineer” is an oxymoron
I’m glad somebody finally said it.
They’re kind of like sound engineers for data aren’t they? Check levels, plug in jacks, fondle knobs.
Is software engineer ok? I’d hate to have to reprint my cards ;-)
That’s why I keep trying to get management to let me put “Miscellaneous” as my title.
You know what IT stands for, right?
I Tried… To get a real ___ (degree, job, whatever!)
Yeah, keep degrading the careers of others, and in a few more years, when you are getting open heart surgery from a robot, controlled by a doctor in another state, and the network goes down?
But it would never be caused by a poorly designed network switch, or a server whose design team made the cost trade off to get cheaper power capacitors because the warranty is only for 5 years.
I hope your “real ___ (degree, job, whatever!)” helps you through that situation.
That would be terrifying.
I’d be interested in seeing a teardown on that soup warmer and possibly some other examples of forgotten “how not tos”.
No no… Just take their word for it. That’s the Hackaday way!
It’s worthy of mentioning as the leading example of crappy engineering, but not a single reason or technical shortcoming is given. I’m not saying they don’t exist, but don’t make me go look up why you don’t like something. poor poor poor.
To Matt and AC: I actually poked around on the web, trying to find out why the author considers this rather attractive looking deco soup warmer, made substantially from bakelite and bright metal, to be an examplar of terrible design and the most appropriate lede for his story. I can only find that it was probably made over 65 years ago (1949 is an oft-cited date), many examples soldier on in working condition to this very day, and there were several reissues of the same concept over the decades for the Campbell Soup Company (and a less styled version for Heinz) to put in restaurant environments. I googled Campbell’s Soup Warmer + fire , and Campbell’s Soup Warmer + danger, and got nothing. Somebody help me out?
The “good old days” aren’t what they used to be! It is not a matter of better or worse but different. As technology has become more powerful, fewer people can create much more complex objects in much shorter time but that is possible because they can call upon an infrastructure and components built by others. You become removed from the raw materials. I am in awe of the power of the building blocks I can buy for a couple of dollars. I don’t need to understand how they achieve that to build something with them, just how to use them. I would argue that what makes a good engineer is not technical knowledge but the ability to understand what is wanted and how to deliver it managing risk, cost and time. This involves some simple heuristics that are rarely taught, such as the ability to estimate in your head. I have seen people be several orders of magnitude off in their calculations because they couldn’t or didn’t do a quick estimate in their head to do a reality check. They just plugged numbers into a calculator or program. Similarily, people often do not manage risk properly by asking “what it the worst that can happen?” and then “it that acceptable?” and then having a “Plan B” to cover unacceptable risk. There are many morer valuable heuristics like this. An interesting question to me is whether the use of complex components and hence the distancing from the “fundamentals” is making engineers worse at these important heuristics and so tend to assemble things and hope for the best, sometimes leading to expensive failure.
That was a part of applied physics finals back in the day. Whole exam full of “get in the right ballpark” spitballs and “what’s the right tools to throw at this” kind of problems that you had to do in quickfire mode, designed I guess to test basic “feel” and intuition for the subject rather than being a rain man fact repeater. However, I cannot remember ever getting an individual mark back for that, or remember if I ever knew how much it counted to final grade. I remember the bastards put a couple of questions in there which were “Too much fun” i.e. problems that were too interesting and got your brain taking off on a dozen tangents… I wrote something to that effect on one of them, “well basically blah blah blah, but implications implications implications, not enough time to fully explore, kthxbye.”
An engineer once said to us (class full of eng. technologists): “You can’t say – I can’t do that. As technical people, we must say: I’ll investigate the problem, and I will get back to you when I have a solution.” Quite inspiring, and essentially a statement that there are no unsolvable problems. I agree with him, and I will add that given enough time, money, and resources, every problem is solvable.
Today’s engineers would be perfectly capable of sending people to Mars in 10 years just like those in the 1960-ies did with Moon. But I’m not noticing that anyone is showering them with $100 bills, except maybe Mr. Musk.
I find it hard to believe they could even complete the paperwork for such a trip in 10 years.
“We can lick gravity, but sometimes
the paperwork is overwhelming…”
~Wernher Von Braun
As an engineer working for Elon, I can say we aren’t getting showered with $100 bills either.
He’s really good at pushing things that are technically possible but just don’t exist yet. If physics says it can’t be done, then that’s a legitimate answer. If it’s possible within the laws of physics but we just don’t have the technology yet – well then get to work!
No, we aren’t.
We’re just driven by greedy managers, to constantly produce “innovations” cheaper and faster.
Even if we wanted to work meticulously, we wouldn’t have the time.
And good luck staying focused in an open space office, that has the sound level of a call center.
You need to phrase everything as “doing due diligence” and then to every short cut and corner cutting request say. “I’m going to need a memo ordering me to skip due diligence on that”
I am one of those dirty technicians. And what I witness almost daily is having young, fresh out of school engineers being thrust into the world with a pretty piece of paper called a diploma, but with absolutely ZERO practical knowledge to back it up. In college, I not only had to design things, but also make them work in a practical way, and fix them when they didn’t.
Like I thought that they teach electronics in electrical engineering school, but apparently all they teach is theory and never seem to make a connection between the math and how things actually function in the real world.
Often times, things “should work in theory” but they do not. Kids today don’t seem to get that part of it. They say “I ran the fucking numbers 15 times already!, it SHOULD work!” And then I say, “hmm, shouldn’t there be a pull up resistor right here?”…
I feel like a sergeant mentoring a young commissioned officer a lot of times. They have a lot of school, but they tend to know jack shit about things should actually work. But treat me like shit, like its my fault THEY don’t know electronics and that I should teach them, when they get paid 3 times more than I do… No wonder they get replaced with people who know what the fuck is going on so often…
You can also thank the vanishing act that ‘shop’ classes did from our public schools in the name of litigation relief. I routinely build prototypes and am in sheer amazement that none of the new engineers know how to use a power tool, much less a soldering iron. (I had one intern ask me one day, pointing at my old Weller iron, “Where do I put the solder in?”)
I had to run to the bathroom I was laughing so hard, I almost peed my pants.
You’re on to something big here.
Earlier comments on this post have pointed out that as we become “more advanced” we get father away from raw materials. I would posit that without a working (or better) knowledge of both the raw materials and the basic/essential tools, a neophyte engineer (or anyone else, really) will not be adequately prepared to grasp with success the more advanced concepts of engineering that follow on.
Simply knowing how to wiggle the complex bits around in order to end up with a working solution does not mean you’re qualified to tackle big problems without being a danger to yourself and others! Basics are anything but. Ignore them at your own peril!
Heh, wait until the ones come along that had a 3D printer in grade school, they gonna think they’ve been banished to Mogadishu or something if you show them a hand tool.
I had a few engineers asking me for advice. They did things like use 10 KOhm collector resistor (and they want fast Ton/Toff time). They used LabView and complained of system slowness. They used C on an 8-bit PIC (5 MIPS) and were wondering why the 1 microsecond timing is off. And on it goes.
In my opinion there is no substitute for hands-on experience. Book knowledge is good, but insufficient by itself.
Gerrit, you’ve touched a raw nerve or two here…
A large part of my responsibilities over the years has been with failure analysis, usually circuits but with materials as well. Most young engineers have never been taught – formally or informally – how to troubleshoot. They don’t understand the process of “analysis”. They’ve been taught to read, listen to a lecture, memorize(usually temporarily), and regurgitate. They don’t know how to work through a problem, solve the puzzle. Most answers to life have just been handed to them. It causes frustration on the side of the graybeards since the younger generation is too into quick gratification to stop and work the problem. Understandably the younger generation gets extremely frustrated by the slow pace the graybeards take to come to a conclusion. Maybe it’s the video game generation, maybe it’s an ADD thing, maybe there is no real interest in learning the science of how things work and why they don’t. Everyone gets frustrated and everyone looses on the opportunity to learn.
The graybeards hold a share of the responsibility here too. Since they don’t understand the younger engineer’s generation, they shy away from working with them. There is no “connection” since they can’t quickly find common ground to work from. They’re not looking for it and since they can solve problems, they feel that they don’t need the newly minted engineer. Thus the case where the new engineer gets the work that no one else wants to do. And is not mentored. And makes mistakes. And gets frustrated. Then moves on.
Part of the puzzle here is for both sides to honestly and humbly reach out to the other. Look for that common ground, which would hopefully revolve around engineering, and cooly and patiently work together. Let the graybeards teach the real world lessons and the young engineers learn from them.
Case in point: Once upon a time not that long ago, a group of seasoned, very talented engineers had two newly graduated EE’s hired in to work with them. While everyone was cordial, none of the graybeards took it upon himself to get to know these fine young engineers. And neither of the fine young engineers felt comfortable to reach out to get to know the graybeards. Everyone was busy with multiple projects, so no one really noticed what was going on. The young engineers made quite a few really boneheaded mistakes that frustrated the graybeards. They were far from incompetent, they just lacked experience. No one took the time to calmly work things out. It drove the young engineers into their corner of the cube farm deeper and the graybeards wanted less and less to do with them. Eventually the young engineers left, bitter about the experience. The graybeards forgot they existed.
How familiar is that story?
Familiar. I’ve made it a point in my career so far to go absolutely out of my way to, bordering on harassment, talk to every greybeard I’ve met. It’s really paid off. Hell, the first time I made a huge idiot mistake the senior engineer looked at me with pity and said, “Gerrit, I approved this purchase, all engineers have made mistakes like this, it’s okay. Now we solve it.” I have none of the Zuckerberg syndrome after that. Greybeards have earned their place and it’s up to us to find masters, not for them to find us. Uselessness is a choice.
(As for the mistake, I never measured the startup current of an LED light, when I ordered a disturbingly expensive set of milspec cable assemblies (You know, Amphenol Bayonet connectors, Alpha Wire….) I had the gauge really wrong. The LEDs would absolutely not turn on on a cable length of more than 10 feet. There may have been actual tears of shame in a corner somewhere from that one, but I admit to nothing.)
The really GOOD experienced engineers will welcome anyone, especially a less experienced engineer asking questions and getting involved ( sans ridiculous deadlines). They value the opportunity to kick around ideas for they understand that two or more heads are better than one in resolving problems. Someone else’s experiences probably don’t match his, so the value of groupthink is understood. I’ve seen more problems because an engineer designed in a vacuum than I ever have with multiple opinions being involved. Who knows, maybe the “new guy” has a better idea, you’ll never know unless he’s a part of the group.
And typically you won’t see too many “disinterested” engineers in those groups, the hard core “love the thrill of the puzzle” types tend to stick together. These are the ones worth seeking out.
Like you, I harassed some of the graybeards coming up through the ranks. I kept an open mind and listened to the stories, asked stupid questions and learned. I feel it is now my RESPONSIBILITY to allow the same thing to happen to me, for the new engineers to ask questions, tell them the old stories and let them make suggestions. It is my duty to pay that forward, to mentor those who want to be better engineers, and hopefully because of a little attention and teaching my next cell phone won’t fall apart like this one is!
Yes, but times have changed. When I was a newbie, I too feared the greybeards, but would never have thought to approach them unless I had investigated enough to be able to at least stand up to scrutiny and have at least some idea of the outcome of my questions.
Now, on the other side of the fence, I find people approaching me without even cursory forethought – “Can I use I2C to talk to this device?”. “What does it say in the datasheet?” “I don’t know, where should I look”.
+1 on “Uselessness is a choice”
I love working with someone who knows more than me and is willing to teach, because I get to learn and I get better. I love working with someone who wants to learn, because I get to teach and we both get better. The more I teach, the more I learn. It’s a great cycle. If the answer to your question is “read the datasheet” and it’s the first time? That’s ok. Maybe you didn’t know about the datasheet. If “read the datasheet” answers multiple questions every day? You’re not even trying. If I have to repeat myself more than twice on a simple concept…you’re not doing your own due diligence and are wasting my time.
Graybeards (I’m not one, I still have far to go) aren’t generally arrogant, they simply expect you to do the same due diligence they expect of themselves. Not doing so makes you appear egotistical and arrogant. We all make mistakes, and that is fine. I sometimes find myself saying to a graybeard “I know this is a stupid question, and I should probably know this already, but I’ve looked here and here and I can’t find the answer. Can you help me understand….”
The old saw is right: Give a man a fish and he’ll eat for a day, Teach a man to fish and he’ll eat for a lifetime.
Showing the younger gen skills… I don’t know where to start.. simple tasks of manual dexterity you do slow and their jaw drops like they saw Kris Angel pull an elephant from under his eyelid… tasks they regard like cleaning the Augean Stables, do in a couple of minutes, and they’ve got this shock and awe look… and you’re left wondering where to begin, how to break it down, and if it can be done with pre cut shapes and glue guns like kindergarten art period.
This is a good read. Very well-made points.
I totally agree with what you said about the internet and simulation software. Convenience is a help and a hindrance at the same time. If you use the easy tools and forget the underlying knowledge, the mistakes come easier and more frequently until you’re a “bad engineer”. Don’t fall into that trap. It seems unbelievable, but I’ve met engineers who’ve said “I don’t use anything I learned in engineering school”. And it was true, because they are the WORST to work with. That casual disregard is at least foolish and reckless and at worst dangerous.
The responsibility of learning and keeping sharp relies with the engineer, not with anyone else. My advice to other engineers: Read subject matter frequently and think critically about it (daily-weekly), engage other engineers in conversation about their work and the problems they’ve encountered, and get your hands dirty.
To be fair, that type usually don’t use anything they learned in grade school either :-D
“The first is drafting and art. CAD just can’t teach spatial reasoning like hand drawing can. That mind-body relationship of being able to visualize a part and then draw it makes an engineer phenomenally better. Also when an engineer had to spend an entire day or two on a single drawing an enormous amount of thought had to go into the layout of it. In the end it’s all about communication. If a manufacturer can’t read your drawing then it’s useless. If an engineer can’t get up and draw the idea out on the board then it doesn’t matter how good of an idea it might be.”
The main problem with this paragraph is that in the past, it wasn’t Engineers who did the drafting. There were Drafters. People whose job was to take the descriptions and rudimentary sketches from Engineers and put together the technical documentation. 3D modelling has made it so that Engineers can model their idea and have the 2D documentation created almost automatically, but I still see drawings from Engineers that leave out necessary details, views, dimensions, and callouts because drafting is not their primary role and curriculum these days don’t spend a lot of time on it.
Ok you got me with “Not so long ago every fastener in a product was made for that product.”
Have you seen the latest Apple device ? ;-)
Apple can go straight to hell. Not because their assemblies aren’t amazing, it’s because their processes are too amazing. No I can’t design you a case like Apple’s. Yes, I know apple does it. Apple owns more CNC machines than anyone else. Period. You get a billion dollars of CNC machines and then we’ll talk about “unibody aluminum” and “micro bead blast finishes”. Stupid Apple engineers have a blank check… Not that I’m jealous or anything… Haha.
I completely took apart a dead aluminum G4 PowerBook. Screws EVERYWHERE! Many different sizes and lengths of screws. It had a die cast frame screwed to threaded posts that were welded to the case bottom. Even the latch holding the battery was several pieces held together with a screw instead of being a single sliding piece with a spring, fit into a slot in the frame.
Better yet, skip the die cast frame and use a stamped one then glue it to the outer shell. With the right gauge of aluminum it could have all the needed threaded holes put in, while making the bottom shell stiffer and lighter than the way it was produced.
Every peripheral device had a short flex cable connecting it to the main board, despite having the connectors real close together. Every other laptop manufacturer would simply use connectors on the peripheral and mainboard that plugged directly together. Using a cable looks like an expensive patch for a CAD error.
There’s just an insane excess of parts and pointless complexity inside stuff from Apple. It doesn’t make their products any more reliable. It doesn’t make their products any prettier – the only people who will ever see all those screws and extra parts (that could be combined into fewer components) are the people who designed them and people taking apart the dead ones.
If you’re going to build a computer like an antique watch, make the damn case with windows to show it off, like high end pocket watched used to have.
Step 1 on simplifying that laptop would have been gluing the frame to the case bottom. No need for welded screw posts if a precision gluing jig was used. Step 2 would be to get rid of all those flex cables and have the peripherals plug directly to the main board. Step 3 would be wherever two parts are screwed together, figure out a way to combine them into one, or make them snap together or use glue or sonic welding. Anything to avoid using another screw.
A thorough review of the design and making alterations as needed would have resulted in a higher quality laptop, weighing less, and costing less to manufacture. The retail price could have been the same, thus more profitable.
You think that, but surprisingly often, cables and connectors are cheaper than PCB real-estate to get to the right point in the case. Cost-down for production is a surprising place.
Flex cables are, well, flexible. Having them in between reliefs tolerances on each of the participating boards. It also allows to mount each board first, to connect them after that. It allows to disconnect them for testing while keeping all PCBs in the case. Flex cables act as a strain relief, making the whole assembly more robust against bending of the overall product.
There are a lot of good reasons to avoid rigid connections. In fact, I’d see usage of cables between boards as a plus, as following good engineering practices.
Regarding gluing vs. welding: welding is much much faster. That’s why there’s a strong preference for welding on high volume products.
“Every peripheral device had a short flex cable connecting it to the main board, despite having the connectors real close together. Every other laptop manufacturer would simply use connectors on the peripheral and mainboard that plugged directly together. Using a cable looks like an expensive patch for a CAD error.”
Hm. I actually disagree on that one. Having the connectors on the mainboard makes the mainboard take the mechanical abuse. Decoupling them mechanically from the mainboard makes the shell handle said abuse. If well done, I’d expect that design to be more reliable.
One problem I see is a cultural one. In some cultures, someone might be told something then asked if they understand, they’ll instinctively reply “Yes” when they do not in order to “save face”. The inference being that if they didn’t understand, clearly they weren’t paying attention.
Thus someone goes off on a tangent when really they should have had their misunderstandings clarified.
Then there’s the cultural expectation that you shouldn’t do things that embarrass your employer, such as pointing out their mistakes. The phrase “the nail that sticks up gets hammered down” comes to mind. Mistakes are not reserved for the young, or the old, and they don’t care what level of the management hierarchy you sit. Now, if you’re a manager or senior engineer, ask yourself this: would you prefer one of your underlings to point out your silly mistake, or would you prefer a complete stranger to do it? Which is more embarrassing for you?
We learn from making mistakes. To err is human. Even computers make mistakes: for it is humans that design the computers, build them, and write the software that runs on them. The old mantra: trust, but verify, I think applies no matter where you are.
One thing about drawing. In general, engineers gave sketches to draftsmen; technicians who were experts at drafting. You didn’t waste your engineer’s time on mechanical drawings. This is true today in bigger companies. There are CAD technicians who do that work while the engineers get on with something else.
Engineers build products and tools. The products become obsolete and the new engineers pick up the best of the available tools and repeat the process.
I mostly agree with the math side. I was taught math very well but I don’t do any math by hand or on paper as there are better tools today. I am current doing graphical reverse kinematics for arc or polar delta robotics. I am using JavaScript in a browser. JavaScript for the math and HTML for the graphical output. I could use a lot of other languages like LUA but I am lazy. But in any case I certainly wouldn’t do it by hand or on paper.
Why would anyone want to be a good engineer? Be a good engineer, slave extra-hard so the upper-management can buy a new sportscar every year and “date” those cute interns while all you get out of this life is 16 hour workdays and being a good engineer.
What about trying to live a good life?
Why the would I want a sports car each year? I could buy a full CNC mill for the same price one year and a really nice lathe the next year!
Damn straight!
Dammit Gerrit.. How in the hell we poor laborers are going to afford a sports cars if you don’t purchase new one every year?
But… but… if executives are always buying a new lathe each year wouldn’t that flood the market with lower priced fancy lathes for everyone? Be the change!
First off if you’re that good you better be compensated well…but if I see that I’d be planning leaving for another company or to starting my own company w/ other engineers that not only pull their weight, but that of about at least 3-5 other people.
Constantly being in crunch mode and making your engineers work 16 hours days doesn’t help productivity in the long term.
It just causes burnout and a high turnover rate.
How to disagree with a more experienced engineer. http://blog.grabcad.com/blog/2015/07/17/how-to-disagree-with-a-more-experienced-engineer
Compare the complexity of today’s requirements back to the 1950’s…plus on the subject of getting dirty debugging (which I love when I learn a new way to debug using math, linear circuit analysis, datasheets that just give info, software tools, multimeters, scopes, or spectrum analyzers); how are people going to debug some chips that are too small to analyze w/o more specialized tools? That’s what happening today, look at every industry. You have less generalists that can fix a car like you could in the past, fix everything in a house (AC units, heating units, water issues), fix a cellphone, fix a computer, fix an issue w/ internet access, it’s less money to get someone else to fix it and it’s impossible to know all those domains.
I was joking w/ my SO at 12:30am when she got a flat tire, that I would be a disgrace of an engineer if I couldn’t fix her flat. I had to read a manual (place the jack in right place), obviously loosen nuts before jack, pump up the spare tire to around 60psi, and put on the spare. But now it’s easy and I’ll never forget how to do that.
Heh, like that old joke.
Q: How do you tell a (name of discipline to be insulted) engineer with a flat tire?
A: He’s changing one wheel at a time to find out which one is flat.
Q: How do you tell a (name of discipline to be insulted) engineer who has run out of gas?
A: He’s changing one wheel at a time to find out which one is flat.
People seem to forget that rocket science is way overrated. Point DirectionX at PositionY at TimeZ using ThrustV for TimeT. Now wait. That’s pretty much it. The Apollo tech wasn’t THAT advanced for it’s time, and it in fact had problems. The achievement of the Apollo series was that it was a government program that ACTUALLY ACHIEVED WHAT IT SET OUT TO DO in a REASONABLE timeframe(I’m looking at you, V-22)
Go read https://en.wikipedia.org/wiki/Pogo_oscillation and come back with “that’s easy”, if you dare. And this is just one of thousands of “interesting little problems” which those folks had to understand and handle.
They do have my admiration.
Click bait works even when you know it’s click bait. People worry the asshole spouting shit will be taken seriously, right?
Sometimes I feel this way, but then I think …”meh. What harm can it do”…
Then I realize how we got our current presidential candidates.
Thank you shitty ‘journalists’. Get dem clicks. Haters gonna Hate.
Let the asshole plugging commence.
Seriously though, engineers are getting less capable but working harder and for less. This is due to companies “running lean” and eliminating the opportunities and interactions which previously allowed for learning. It’s also due to colleges not being able to keep up with technology, while simultaneously charging more for their time-sink. Most importantly it’s because of the new grad’s attitude. Most were told that life is simple, they hand you a job after graduation, it’s just that simple! Few have a work ethic or an understanding of their field beyond what’s handed to them. Then they take for granted the technology they glued together. “I designed this circuit”…that looks exactly like the IC application note. “I’m an engineer now, and I have an opinion”!
yes they may be worse but that may be a good thing.
example in point lets say that you are a hobbyist scrap metal person.
before the dumbing of the refrigeration field you could not flag down a technician installing a new air conditioner system at your neighbor’s house and ask for the old one because it is still charged with the refrigerant (freon).
now with the dumbing of the field you can now get the old unit because the technicians are not told not to release the old unit or they remove the charge before scrapping the unit.
“When someone builds a bridge, he uses engineers who have been certified as knowing what they are doing. Yet when someone builds you a software program, he has no similar certification, even though your safety may be just as dependent upon that software working as it is upon the bridge supporting your weight.”–David L. Parnas
“There are no standards for computer programmers and no group to certify them.”
–David L. Parnas
Last time the public and politicos got stirred up about software quality assurance, they invented viruses, then certified their distribution media was virus free.
https://pbs.twimg.com/media/CvTJ3JvUMAACxkI.jpg:large
I do not say engineers are are getting worst but the discipline and job are definitely worst and place the blame on HR an management using BEE as technicians. I talked to some older engineers working for aerospace, then engineers design it then tell his vocational trained technician to build it test it and tell the engineer it works or not. Now companies expect four degree engineers to works as lower paid jobs that the skills do not come close to the disciplines taught in a four year degree. Take this job that popped up in my search.
“Bachelors Degree or the equivalent experience in a technical discipline.
Be able to relate well to others in a professional and knowledgeable manner.
Good verbal and writing skills.
Be able to reach and work on customers equipment while following all safety procedures.
Be on-call and able to travel via car and/or plane on a short notice.
Must be able to meet all customer access requirements.
Must be willing to work multiple shifts.
Able to lift and move equipment within safe limits.
Valid Drivers License. ”
I bet the job can be filled by a vocational or military trained technician. A Bachelor degree is unnecessary and overqualified.
the older I get the less I can see the paper in my hands, but the better I become at spotting and idiot a mile away.
Today’s young “EECS” under-graduates are next to useless out of the box. I earned my EE back when it was “hard” to do – five or (more likely) six years to get it right. This required the full EE core and chosen electives plus a LOT of extra courses and/or audits from (e.g.) the then separate College of Computer Sciences (and others). Just the CORE stuff like Thermodynamics (1-year), Mechanics (Statics and Dynamics, 1-year), Chemistry (1-year plus outside courses in Organic Chemistry), Electromagnetics (1-year minimum!)… It all adds up. Today I prefer hire older Engineers who have the knowledge to deal with diverse problems. In-practice, my experience with these young EECS grads to be a problem. They’re more like “Technicians”. And then there’s the ongoing erosion of “Engineering Ethics” that are not taught at today’s “EECS-Mills”. At all times during my EE education I was reminded: “A Physician may make a mistake and lose one patient. But if an Engineer makes one mistake, many may die”. What’s happening today with the new Engineering Graduate “EECS Product” is terrible. Don’t even get me started on the lack of training when it comes to Mathematics.
What’s modern is that teachers are under pressure to give every idiot good grades, and so they do. The results of that are inevitable.
Combine that with everybody going to higher education, even if they aren’t suited and do the math.
So what we now rely on is employers to do the sifting.
Perhaps why we don’t see as badly engineered products is that we’ve built upon works of our predecessors, with the right techniques/design principles, computer assistance, certification, technology, etc. So not only are the products better than before, it’s also far easier and faster to design. So they simply think “this is what I’ve been taught how to do it, therefore this is the best way to do it” and do not (more like cannot) review design decisions. So the design inadequacies just keep on piling up. These is more prevalent with younger engineers. Young engineers also may not see when ideal simulations (sometimes extremely ideal) and the real world implementation begin and end — when to trust a simulation or not.
There’s also possible caveats with engineers trained decades before. They usually have already settled on doing things in certain ways and might stick to it despite recent advancements in their fields (I’m not just talking about not being able to use CAD or EDA, etc). But, by their more advanced years, they usually are already in charge of teams, leaving the grunt work to younger engineers. So it could have lesser impacts.
“The internet is a shitty quick reference and to rely on it is to cheat yourself.
Last is to avoid ageism completely.”
Those two sentences are right next to each other despite the fact the former is a blazing example of the latter.
One further aspect is that often time to complete dates will be compressed by the management and thus causing short cuts and overtime – this gets dangerous when testing time is reduces. I think it a good idea for young Engineers fresh from the University to spend one year working under an experienced senior Engineer then on to his/her own project.
As an Electrical engineer, I can tell you that today we don’t have to wait *only* one month for “approval”, now its months and months of budget approvals, contract negotiation, certification and Q & A “work”.
The reason we can’t build Apollo today is that while the design would be done in about one year with modern tools, all of the approval processes to fill a rocket with chemicals and put people on it would be spanning several election periods with each reducing the budget, increasing the scope and the final nail in the coffin would be a team of “expert consultants” “value-engineering” the, by now, 10 year old design. Thus re-baselining the whole project, but no change control, and the design team long gone in despair.
Nowadays, if a light switch zaps you, it’s because hackers broke into your IoT switch and someone jumped the mains to the switch body.