As anyone who has experimented with their own home-made CNC machinery will tell you, precision isn’t cheap. You can assemble a gantry mill using off-the-shelf threading and kitchen drawer slides. But it’s a safe assumption that if you put the tool at a particular position it won’t be quite at the same position next time you return. But if you take your budget from dirt cheap to reasonably priced you can do much better. [Adam Bender] designs high-precision automation systems for a living, so when he needed a precision linear stage for a personal project he achieved micron level accuracy for under $500.
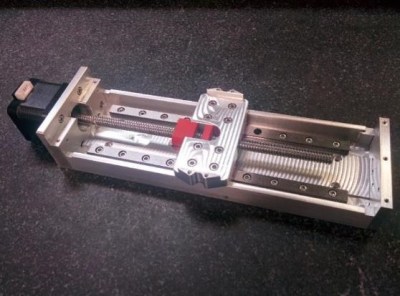
He explains the problem of backlash with an inexpensive lead screw — the wiggle between threaded components that cause positional chaos. His solution uses two nuts preloaded against each other with a spring. There is still a stick-slip issue; a tendency to move in lurches due to differences between the coefficients of static and dynamic friction between the materials. Careful choice of machining stock for the nut to picking materials in which these coefficients were almost identical reduced the stick-slip to as little as possible.
He goes into significant detail on the design, manufacture, and testing of all the components of his stage, its body, sealing system, and control. If you are a precision CNC guru maybe you’ll find it interesting as a cleverly designed component, but if you are a mere dilettante you’ll find it fascinating to read a comprehensive but accessible write-up from a professional in the field.
This build probably goes a step beyond most we’ve featured in the past, but that’s not to say we’ve not seen some pretty good efforts.
Seems like a great candidate (along with, maybe, a peizo element) to create a scanning electron microscope that has a wider field of view than just the deflection of the crystal. Maybe that doesn’t actually end up being a problem when you are looking at something so tiny, though…
Great writeup by Adam!
Thanks!
I wonder what the nuts are made of, nothing in the referenced post except this:
“Ever try to push something across a rough table very slowly?
The object will resist motion, and then all of a sudden lurch forward. This is the difference in material coefficients of static and dynamic friction. This is aptly named stick-slip
Well if you want to move a lead nut a few micron along a lead screw, the same thing will happen.
So the lead nut was made from a special material with coefficients of static and dynamic friction that are almost the same. The greatly reduces the stick-slip phenomenon.”
Here are some commercial versions with detailed spec sheets. I randomly saw this company at a trade show so I don’t know if they are any good.
http://www.helixlinear.com/Product/ProductLine/Helix-Precision-Lead-Screw-Products
I made the nuts from Turcite X, although as another poster mentioned, (in great detail), Delrin AF would work great as well. Most self lubricating plastics have similiar properties. Turcite is a popular material for applications like this, many older CNC machines even use to have a thin layer of Turcite applied to their ways.
Stick-slip is exacerbated by solution used against backlash, because with application of force, friction becomes much larger.
However, this apparatus probably could get through a process of break-in (like a new car engine), where repeated constant position change, with lower tension force between lead nuts, and frequent lubricant change/cleaning of the thread and nuts surfaces should further smooth them down and reduce the friction, thus turning down the stick-slip behaviour.
This might come in handy for those designing a 3D printer.
Use DELRIN AF for the nut material.
Eliminate the slip-stick by preloading two pieces of Delrin AF, tapped to match the threaded rod.
– NOT Delrin!; yes to Delrin AF, any Delrin AF.
– The dynamic friction is somewhat higher than the static friction, so no slip-stick.
– The preload eliminates the backlash AND reduces friction. (Delrin AF likes preload against steel)
– Delrin AF performs better and lasts longer when the steel is harder.
– (and steel that is flatter & smoother, if you’re using a puck of Delrin AF on flat steel bar as a zero slip-stick floating linear bearing; hint hint. And if you puck both sides, and add another such setup rotated 90 running along the same axis, you’ve now got a zero slip-stick debris tolerant registered linear bearing.)
– Delrin AF is self-lubricating (embedded ptfe) and a lot more tolerant of milling debris than steel or other bearing materials (except a couple of exotics from Germany that run on polished Al).
Note: after cutting, drilling, tapping or milling Delrin AF, there is a heat-treatment protocol to follow to “temper” the final piece of Delrin AF. This appears to condition surfaces ‘torn’ by cutting, tapping or milling. So don’t tap it properly and then think it’s too tight or doesn’t behave as expected when you test it. Do the heat-treatment first, then confirm that your tapping matches the tolerance of your threaded-rod.
Also Note: You do not want it loose. A little tight doesn’t hurt, it helps. Delrin AF likes preload and there is less space for debris. So in addition to Delrin AF being debris tolerant, the fit of the Delrin AF to the surface acts much like its own sweeper for keeping debris away from between the load-bearing surfaces.
Using a spring to preload is a great idea, but at some force (changing direction but the momentum is against that?) it could temporarily allow a reduced preload or even some movement, destroying precision in one direction on that axis. Alternately, as the Delrin AF has a tiny amount of deflection, it can be preloaded on the threaded rod without a spring; with both opposing nuts of Delrin AF stock, apply permanent preload. In the post’s design, but with nuts of Delrin AF, consider using an extremely stiff spring or remove the spring. I drill through both “nuts” at four points around the tapped hole, and once assembled, each bolt’s nuts are locked at desired preload with a touch of thread-locker and an additional counter-locking nut.
The quantity of Delrin AF required makes this a very cheap solution with low replacement cost when it wears out.
(I’ve covered this so many times over the years but no one seems to catch on)
You & Delton AF need to get a room
I’m gonna pick up a few samples of the stuff based on this guy’s enthusiasm, but I’m gonna have a hard time not calling it “Delrin As F—“
Thx for the info. Had not heard of Delrin AF.
Canoe:
Pics? Links?
Showing is infinitely better than telling.
No photos.
The project I was developing a CNC for died, so the CNC project got boxed & shelved. It was for milling wood parts, so the recirculating ball-bearing types with their oil are a disaster with saw dust (local business had one-hour tear-down & clean for every two hours of running…). I’d got as far as designing and testing the nut-block, the floating-bearing linear rail, the fixed/registration rail, had cut the parts for the vertical axis and (it was 2000, to get what I wanted) designed my own stepper driver board (I had a new found love-on for V-FETs and low-side current measurements). I made the nut-block out of hard maple (lol), as I was experimenting with threading hardwood to take bolts (significantly stronger than using screws by the way; use a pre-drill one size smaller than for metal). The Delrin AF nuts were cut from some ~2″ rod stock I got cheap as off cuts, so the metal plate for preloading the preload-nut was a fender washer.
I did find the graphics I drew up for someone in 2002 and has been emailed around over the years. I guess it’s time to polish the drawing and publish where others can benefit from it. Only issue now is I’m up to my armpits in alligators on a dead line for a software project.
Here’s the diagram.
https://hackaday.io/project/20002-zero-backlash-nut-block
Eliminating stick slip is not possible. It *can* be minimized and the position error can be eliminated by means of a second actuator and position sensing, but the first order motion will have stick slip if it involves surface contacts. A *lot* of very capable people have battled the problem. There is an excellent series of articles in Scientific American in the late 40’s about the construction of a ruling engine. The articles give a very good overview of how hard high precision is to achieve.
What about air bearings? No contact = no problem right?
Yes that would work, see an example here: https://www.youtube.com/watch?v=sFrVdoOhu1Q
Maybe micron level accuracy across a small (some few microns) travel distance , but not at any great lead length using a rolled trapezoidal screw. Rolled trapezoidal screws have a relatively high lead error over some distance , which is rarely provided by cheaper screw manufacturers, and must be mapped to be usable at these small travels. To get true micron precision over distance a ball screw is required. They are not that expensive these days, and there is no real reason to not use them. Stiction, as well as dynamic friction is greatly reduced with ball screws also. Calling a trapezoidal screw based system accurate is a gross overstatement. It may be repeatable , but repeatability does not equal accuracy.
Hey Wizard! That’s definitely true, the stock leadscrew doesn’t have fantastic precision. To help overcome this, I mapped the error of the leadscrew using a very accurate Heidenhain linear probe. I used this error profile in the firmware to compensate for the linear stage position. I have a bit more detail on my website. Thanks!
From his own writeup he has done some mapping with a Heidenhain MT-2501 which should make the assembly quite a bit more accurate than the leadscrew is on its own. He quotes the acceracy at 13 micron and repeatabilty as better than 2 micron. Using ground ballscrews and laser interferometer mapping you could get accuracy better than 0.3 micron, but at some point good enough is good enough.
I wonder how it will fare under load.
The lead screw has to be able to push/pull the load, and I fear the (economical) stepper with buit-in leadscrew will have some axial play, ruining the precision. In CNCs the leadscrew is usually supported in precision blocks with preloaded angle contact bearings to avoid backlash
The motor is NOT designed with any significant axial forces in mind, the bearings are just normal single-row bearings, so it will not fare well under load.
Two years ago I purchased a pair of MX80L lienar stages off ebay for $250 a pop. They repeat to +-0.5um and have absolute accuracy/flatness of <16um across their entire travel.
I'm not really sure what to say about the linear stage featured in this post. It is comically mismatched – you have a solid aluminum block with a pair of linear rails constraining motion, but the actuation is provided by a bargain bin leadscrew/stepper combination.
The motor bearings alone will have several thou of play – and the plastic nut just doesn't provide enough rigidity along the travel axis to warrant linear rails.
You are supposed to buy a ballscrew and affix one end with preloaded AC bearings. Its not even that expensive if you grab rolled chinese parts – although there might be periodic error in the lead.
That was my impression. I thought the “right” way to solve these backlash issues were ballscrews. Do you have a sense for what type of accuracy/repeatability/precision you can get out of one of the bargain Chinese ballscrew linear stages?
I’ve measured rolled chinese ballscrews at ~0.008″/ft of lead error which is empirically pretty awful but more than good enough for most applications.
An anti-backlash ballnut priced inline with the other components you are using will essentially be perfect. Even the cheapest c7 nut has 0 backlash under no load and will probably maintain <0.001" under most conditions.
The problem with backlash is that it is the sum of many sources of error. People often focus on the nut/screw interface, but servo deadzone/sticktion, coupler flex, and bearing play are also sources of backlash.
Some people use a literal spring (helical coupler) as part of their linear motion and wonder where backlash is coming from.
Two words- hydrostatic ways. Most accurate positioning method I know of. See Kern Pyramid Nano for example. I would love to see a homebrew version of that…
Just out of curiosity- has anyone priced out the cheapest ground ballscrews? I’m looking at building a 3D printer from scratch and wanted to use ball screws as I know they’re more affordable now but I haven’t gotten any quotes yet looking to use ground ones not rolled let’s just say one foot. Ballpark idea?
Why would you want to put ballscrews on a 3D printer? (that is on the X or Y, Z might have a use for them) It doesn’t see any significant forces like a mill would, so the traditional toothed belt and pulley will do just fine.
If you want to make a better 3D printer, invest in a proper frame that’s actually straight (all the “automatic bed leveling” crap just shows that the traditional 3D printer mechanics suck) and some nice beefy guide rods, but only for the stationary stuff, if it has to move, it should be kept light. Going back to the 1st paragraph, you want to be able to move the print head fast, as that will cut down on print time.
Servos instead of steppers would be nice, but those are still very expensive. However, if you feel you have a couple of grand burning a hole in your pocket, nobody will stop you from trying ;-)
Take a look at the renkforce RF1000 3d printer!
In relation to the given mechanics it is a rock solid price!
Many problems with 3D printing are the horrible mechanics – that’s what most people find out over time.
They start with a really cheap setup, are very happy how nice the stuff is compared to the price – and start investing time and money in improvements. Instead of doing it right from the beginning!
https://www.conrad.de/de/renkforce-rf1000-3d-drucker-bausatz-single-extruder-inkl-software-franzis-designcad-v24-3d-print-renkforce-edition-1007507.html
“There is still a stick-slip issue; a tendency to move in lurches due to differences between the coefficients of static and dynamic friction between the materials.”
While currently eliminating stick-slip is not possible, it can be greatly reduced by exciting the moving parts with the likes of a mechanically-coupled ultrasonic transducer. The transducer in the simplest case can run at a single frequency near resonant frequency and still provide improved results. Ideally the frequency is controlled in a feedback loop. This subject is complex, but well known. Possible drawbacks to “Ultrasonic Backlash Reduction” include added surface wear, cavitation in the cooling/lubrication fluids, and unwanted resonance in the entire device at certain positions (again some frequency control and feedback control can help with this). Note however, the best use of the likes of ultrasonic backlash reduction does require computer control, however, the feedback sensors are typically not directly tied to the positioning sensors in terms of data, only in the sensed frequency and comparison to characterized resonance data of the tool bed itself.
I forgot one thing, where a system has NO feedback control for the ultrasonic excitation, open-loop excitation is still beneficial if the excitation is pseudo-random (noise-like) in nature.