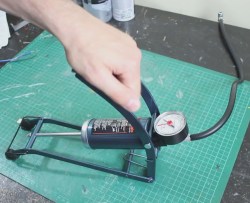
[James Bruton] is well known for making robots using electric motors but he’s decided to try his hand at using pneumatics in order to make a fighting robot. The pneumatic cylinders will be used to give it two powerful punching arms. In true [James Bruton] fashion, he’s started with some experiments first, using the pneumatic cylinders from foot pumps. The cylinders he’s tried so far are taken out of single cylinder foot pumps from Halfords Essentials, costing only £6.29, around $8.11 US. That’s far cheaper than a commercial pneumatic cylinder, and perfectly adequate for this first step.
He did have to hack the cylinder a little though, besides removing it from its mounting and moving it to a DIY frame. Normally when you step down on a foot pump’s lever, you compress the cylinder, forcing air out the hose and into whatever you’re inflating. But he wanted to push air in the other direction, into the hose and into the cylinder. That would make the cylinder expand and thereby extend a robot fighting arm. And preferably that would be done rapidly and forcefully. However, a check valve at the hose outlet prevented air from entering the cylinder from the hose. So he removed the check valve. Now all he needed was a way to forcefully, and rapidly, push air into the hose.
For that he bought a solenoid activated valve on eBay, and a compressor with a 24 liter reservoir and a decent air flow rate of 180 liters per minute. The compressor added £110 ($142) to the cost of his project but that was still cheaper than the batteries he normally buys for his electric motor robots.
After working his usual CAD and 3D printing magic, he came up with an arm for the cylinder and a body that could fit two more valve activated cylinders to act as a working shoulder. A little more 3D printing and electronics, and he had 3 switches, one for each valve and cylinder. He then had the very successful results his experiment. You can see the entire R&D process in the video below, along with demonstrations of the resulting punching robot arm. We think it’s fairly intimidating for a first step.
This isn’t the first time [James] has done interesting experiments like this before embarking on a big project. One that comes to mind is the time he spent working out what motors and electronics were needed for human-like shoulder and arm movements for his Ultron robot, before even starting work on the robot.
I hope those pumps work better as pistons than they work as pumps. Using one to pump a bike tire, you get in order of 100 actuations before the piston rod eats it’s way through its flimsy collar or the frame is too twisted to be usable.
One that I purchased had the air hose break on the second pump!
I replaced the hose with one of sturdy material, also good for -20 F. I keep it in the trunk of the car for emergencies.
I’m surprised he hasn’t tried to put two cylinders at apposing actions so, say one pushes the arm out and the other will retract it. Also, given the idea of using foot pumps as a cheap source, I’m surprised he’s not also tried (similarly cheap) bicycle pumps (think small hand pumps), which might need a few more 3d-printed parts to hold it but will probably result in a more compact actuator.
Probably he needed more force. Bigger radius = more force from the same pressure.
A second opposing piston seems like overkill when a spring does perfectly well in this application.
For cheap cylinders I feel like it would have been better just to make them. a trip to the hardware store would easily net you the parts for much better cylinders for about the same price.
Requires a lot more work though. And a lathe.
True, I suppose it’s about perspective. This project is based on ‘cool factor’ (not that this is a bad thing), so It really only needs to last long enough for interest to fade. Dunno, building something that won’t last for years to come doesn’t mesh well with my mind. :p
They sell ready-made stainless/aluminium pneumatic cylinders at the usual Chinese sites like aliexpress/banggood.
And for a very doable price.
Love the video. I work for a large pneumatics manufacture called Aventics and your project here is brilliant. It lends itself well for school projects and simple robotic contest in the area. I’m here to help if you guys have any questions or if I can supply you with some low cost pneumatics. Also do you have a BOM and some 3D geometry you can share on the parts you made?
Sincerely,
Chris N
Key Account Manager
Aventics
FYI…for lower pressure control you can use an external piloted valve or a direct firing valve. Also you can use proportional control valves as you mentioned to get electric motor/servo type control.
I intend to try car fuel injectors on the exhaust side of a cylinder to allow movement control, a series of rapid pulses for steady stroke ,arduino driven of course. injectors are rapid action solenoid vales, usefull for all sorts of projects.