Back in the 70s when I started getting interested in electronics, tons of magazines catered to the hobbyist market. Popular Electronics was my favorite, and I think I remember the advertisements more than anything, probably because they outnumbered articles by a large margin. Looking back, it seemed like a lot of ad space was sold to companies hawking the tools and materials needed for wire wrapping, which was very popular for prototyping in the days before solderless breadboards were readily available. I remember beauty shots of neat rows of small, gold posts, with stripped wires wrapped evenly around them.
To the budding hobbyist, wire wrapping looked like the skill to have. With a huge selection of posts, terminals, and sockets for ICs and discrete components, as well as a wide range of manual and powered wrapping tools, it seemed like you could build anything with wire wrapping. But fast forward just a decade or so, and wire wrapping seemed to drop out of favor. And today — well, does anyone even wire wrap anymore?
Where Inventions Were Born
Almost everything we take for granted in the modern world can trace at least some of its lineage back to Bell Labs, the invention factory in the New Jersey suburbs, and wire wrapping is no exception. While wire wrapping may not have been invented there — a good argument can be made that it started in the previous century with telegraph linesmen splicing and securing wires in the field — the needs of the telephone industry, particularly in the central office, propelled the development of tools and techniques that would make connections easier. Bell Labs and Western Electric, the manufacturing arm of AT&T, would perfect wire wrapping in the mid-1950s.
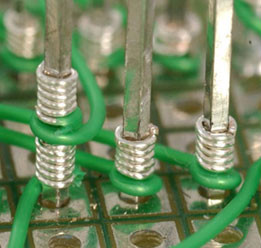
The idea behind wire wrapped connections is simple — make a tight, metal-to-metal connection that’s electrically and mechanically solid, and do it as rapidly as possible. Soldering seems like it would make more sense electrically and mechanically, but it takes time and skill to execute properly, and introduces problems of its own. Wire wrapping, on the other hand, allowed telco techs to make hundreds of connections quickly, with simple tools, and in tight spaces.
Specifics varied between applications, but the basics include terminals in the form of posts with a square cross-section and insulated solid wire. Insulation was stripped to a specified length, with care taken to avoid nicking the conductor within. The stripped wire was loaded into the metal bit of a wrapping tool, which was then placed over the post. A few quick turns of the bit, either with hand or electric power, wrapped the wire snugly around the post for about five complete turns and completed the connection.
Bil Herd did a great piece on the tools and techniques of wire wrapping a few years back, and this video shows what’s involved in making wire wraps:
Where Is It Now?
So what made wrapped connections so great? Part of it was the electrical and mechanical properties of the connection. A properly wrapped post would have at least one turn of the insulated part of the wire wrapped around the post, providing a degree of mechanical support that kept the conductor from breaking if the assembly were subjected to vibration. There’s also the benefits of the square post corners cutting into the round conductor twenty or so times along the wrap. Such connections are gas-tight, so oxygen is excluded from the mating surfaces and oxidation inside the joint is avoided. This also lets the wire and post form a cold weld, significantly reducing the resistance of the connection.
And yet we see precious little wire wrapping these days, at least judging by your tips and Hackaday.io projects. Why is that? Is it the rise of super cheap PCBs and the tools to design them quickly? Is it the increased availability and use of SMD components and the tools to properly handle them? Maybe wire wrapping is mainly used in the industry today for prototyping and has just lost favor in at the hobby end of the market? Or perhaps my perception is wrong, and wire wrapping is alive and well across the board, in which case maybe I should invest in some Kynar and a squeeze tool and get wrapping.
What’s your experience with wire wrapping? Sound off in the comments below.
Wire wrap is (was) still used in telecom sites until I left in early 2000s. Also, the AGCS GTD-5 class 5 telephone office had multiple wire wraps on its shelf backplanes. Cross connects on analog DSX panels still had wire wraps, 5 conductor wire (2 pr plus tracer). Distribution frames still have them. Some outside cross connect boxes still had them when I left.
I could wire wrap a board faster than design and etch boards, much faster on small batch jobs. The tiny manual wire wrap tools for 30 gauge wire are hard to hang on to with my mitts, so I have a telecom type manual wrap gun. Bits and sleeves are way more expensive tho.
I think the real death-knell for wire wrap was that the chips became cheaper than the sockets.
Putting a $175 6800 chip in a $2 wire wrap socket was a no-brainer, while putting a $4 ATmega32a in a $4 WW socket, not so much…
The boards I built for this Lego lighting project are all wire-wrapped. It’s a one-off thing, though there are 8 copies of one board in the crown that I maybe could have done with PCB instead.
https://blog.adafruit.com/2017/04/11/lego-grand-carousel-with-ht16k33-breakout-leds-slip-ring-upgrade/
For whatever reason, I could never get into wirewrapping back in the 80’s. It seemed to take so long versus just soldering the wires, and those sockets were soooo expensive relative to conventional DIP. I guess there are some cases where it’s the bomb, but those were not mine.
OTOH, I purely loved (and still love) to use the Kynar wire. So I do have a couple small wirewrap tools which I use solely for the stripper.
I missed something (really?)
Why is daisy chaining wire wrap a no-no?
(My unfinished 8008 (or something) wire wrap board from the mid-’80’s I daisy chained the address lines from the processor chip to the RAM and ROM sockets.)
And don’t forget it was used in Apollo….
https://tcf.pages.tcnj.edu/files/2013/12/Apollo-Guidance-Computer-2009.pdf
I confess, I am lazy and cheap. I like breadboards, then reuse components.. If I go to more I solder. (I can, and used to wire wrap, in college and way back but its a thing I always worked around,, And then the virtualized kits for some prototyping are cool. (I still like and would prefer to feel things in my hand, for the effort soldering has a finality to a project and vibrations, jostling, crappy cases,, I like soldering proto work,, if the device checks good)
Is it the rise of super cheap PCBs and the tools to design them quickly?
Yes. WW Sockets are super expensive, you can make several PCB’s today for the cost of the sockets. Sockets often cost 3x-4x the cost of the parts they house. And who uses through hole parts any more?
When I was studying engineering at university, the electronic/computer systems engineering component required that all students have a wire wrap kit. We bought boards from the university specially designed to slot into caddies in the comp sys eng lab, that connected to the PC via parallel port… from there we could wire up various circuits on the board and interface them to the computer.
I guess one of the downsides of wirewrapping is if you want to change a connection that’s connected lower down than the most recent connection on the two pins the wire runs between, you may need to undo and re-run several connections, and then that potentially cascades..
I’d be doing a lot of it if the dip/sip sockets hadn’t gotten so damn expensive.
We have a customer that needs a configutation header wire-wrapped. But, it’s 2mm pitch so, the typical tools don’t work well.
Anyone have a source for tools/bits that work on the 0.5mm square posts?
thanx in advance
Wire wrapping paid my way through college in the 1970s. I worked for a phone company for the duration and must have made tens of thousands of wraps. Later, at my first job, I had technicians to do it for me, but we gave it up as components became smaller and frequencies higher.
I remember programming a PET computer to tmake sure backplanes are wired correctly , it beeped if you had the right pin and checking the result afterwards, A9 #0
As I write this comment, it is 11/15/2020 at 9:00 AM .. And, as soon as I eat breakfast, I’m back in “the lab” to complete more wire-wrapping :-) I think it’s still great for prototyping at least. And, it’s more “permanent” than using a solderless breadboard. I think the worst rip-off is the price of the “Wrap ID’s” that I like to use. They are small plastic numbered identifiers that are pushed onto the socket pins to help facilitate wiring and reduce potential errors. I’ve seen them offered for sale for $3.00 .. a PIECE! Eyeowee!
Wire wrap technology is in the constant use even today, in 2021. It is widely used in ICT (In circuit test) as it is easier and faster and pretty reliable too) to do thousands of connections from the bed of nails to the tester interface. Also, Kynar style wire has sturdy insulation and occupies little space (it is really thin).
I used wire-wrapping in 1983 for my MSc project. It was a lot of work, but the main reason why it is gone today is probably also what hit me in the project:
NOISE!
The wires are long antennas, and they are not in any way matched in impedance or path etc.
So my device worked a bit – once-in-awhile…