One evening quite a few years ago, as I was driving through my hometown I saw the telltale flashing lights of the local volunteer fire department ahead. I passed by a side road where all the activity was: a utility pole on fire. I could see smoke and flames shooting from the transformer and I could hear the loud, angry 60 Hz buzzing that sounded like a million hornet nests. As I passed, the transformer exploded and released a cloud of flaming liquid that rained down on the road and lawns underneath. It seemed like a good time to quit rubbernecking and beat it as fast as I could.
I knew at the time that the flaming liquid was transformer oil, but I never really knew what it was for or why it was in there. Oil is just one of many liquid dielectrics that are found in a lot of power distribution equipment, from those transformers on the pole to the big capacitors and switchgear in the local substation. Liquid dielectrics are interesting materials that are worth taking a look at.
Same Thing, Different State
If you know what a dielectric is, you’ve got a pretty good idea already of why a dielectric in a liquid state would be a useful thing. A dielectric is just a material that doesn’t conduct electricity but can be polarized by an electric field. So dielectrics are just special cases of insulators, where the properties of the material make it easy for charges to separate but not flow. Therefore, all dielectrics are insulators, but not all insulators are dielectrics.
Liquid dielectrics are just dielectric materials in the liquid state, and maintain all the properties of the solid dielectrics commonly found in the capacitors we’re all familiar with. But for practical purposes, the more useful property of liquid dielectrics is their insulating ability as opposed to their charge separation properties. In fact, electrical insulation is probably the most important property of a liquid dielectric, at least as far as their use in power distribution gear.
That transformer I watched explode was likely filled with mineral oil, which is probably the most common liquid dielectric in use today. Mineral oil is just highly refined petroleum – baby oil is perfumed mineral oil – and it’s used in transformers because of its high flash point and excellent insulating properties. Its primary job is to conduct heat away from the windings by convection; some large transformers even have radiator fins to increase heat transfer to the atmosphere. The transformer oil also serves to exclude oxygen and moisture that would attack the interior components, especially the paper used to insulate the windings.
Another reason that electrical gear is often filled with oil is to limit corona discharge and quench arcing. Coronas occur when an electric field ionizes the fluid surrounding it. You can hear corona discharge under most high-tension lines, where the fluid being ionized is the air around the insulators. That’s not such a bad thing high in the air, but inside an enclosure it could lead to disaster. Liquid dielectric, with a lower relative permittivity (the preferred term over “dielectric constant”) than air, solves that problem. Liquid dielectrics are also used in the massive switches that control high-voltage systems, to damp the long, powerful arcs that can occur when circuits are broken in free air.
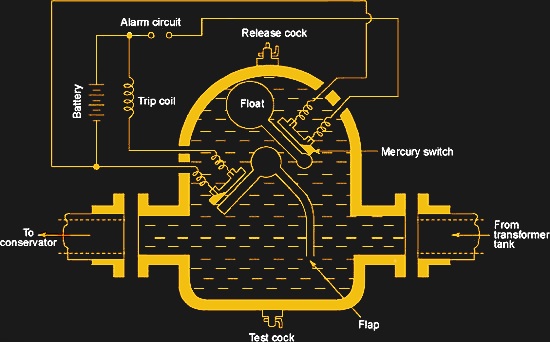
One interesting device that monitors the health of a transformer through its cooling oil is the Buchholz relay. This is an electromechanical device that sits in an oil-filled chamber plumbed to between the transformer and its radiator. It has two mercury tilt switches: one attached to a ball float at the top of the chamber, the other attached to a flap near the bottom where the pipes enter and exit. Minor transformer faults will decompose the oil and produce gas bubbles; if enough gas accumulates in the chamber, the float will drop enough for the mercury switch to make contact and trigger an alarm. Similarly, a major fault will produce a large slug of gas that will move the flap to trigger a circuit breaker to isolate the transformer and prevent further damage.
Better Options
Mineral oil isn’t perfect, of course. As I saw dramatically demonstrated, mineral oil is flammable. The search for a better transformer oil in decades past led to the use of polychlorinated biphenyls, or PCBs, organic chlorine compounds that have excellent dielectric properties and are practically non-flammable. Unfortunately they’re also highly toxic; think Love Canal and Agent Orange toxic. Their production was banned in the 1970s, but a not insignificant number of transformers filled with or contaminated by PCBs are still hanging on poles.
Other substitutes for mineral oil in transformers and switchgear include expensive silicone and fluorocarbon oils, used where flammability is a safety issue, and even oils derived from plants, like castor oil and plain vegetable oil. The natural oils are more easily biodegradable than the mineral-derived dielectrics and work well where there’s a possibility for leaks. Considerable effort has been put into optimizing these natural oils with additives and to using them as the basis for synthetic oils with the desired properties.
[Featured image: Transformer oil under test, KEP Power Testing Blog]
On the same article you tell us that PCBs are horribly toxic, the previous article is ‘Get your PCBs Made at the Mall’. Gah!
Obviously, I know the difference. Just reminded me of an argument someone (probably a chemist) made way back when regarding making your own Printed Circuit Boards.
You were probably joking about acronyms, but he is referring to a different PCB:
https://en.wikipedia.org/wiki/Polychlorinated_biphenyl
;-)
However, there is vintage equipment where the circuit-boards and oil-capacitors still contain traces of Polychlorinated biphenyl. Most people stopped using it early on before 1978, but sometimes there was no alternative or warning labels.
What made it a useful product, also made it extremely difficult to dispose of…. I am not sure if it still bio-accumulates in some northern marine animal predators fatty tissue, as at one time some were classified as toxic waste if they washed up on shore. If I recall, people needed a special arc incinerator to actually do environmental remediation.
I keep a 10 foot poll (3.048m) handy when people start talking about their tube equipment from the 50s, and would never buy a place near old electric company works-yards. ;-)
At a radar base I worked in, the HV transformers and capacitors were filled with a PCB known as “Askeral”.
IIRC, General Electric also had to pay a lot to clean up a river (the Hudson?) because of PCB’s they had dumped in it
years before.
An article about the cleanup.
https://www.poughkeepsiejournal.com/story/tech/science/environment/2018/01/11/ge-groups-await-epa-pcbs/972742001/
I worked at the Air Force Research Lab in high power radar, and used a bunch of different dielectrics. PCB was the safest, because it was much less flammable. Well, actually, demineralized water was safest, and it had a high dielectric constant (81) so it made good capacitors…. but only for a few milliseconds.
Regular mineral oil holds off 40 KV across a tenth of an inch, whereas air needed 4 inches.
The last oil I used was made from soybeans. It performed well, although I don’t know how long it lasted without … spoiling?
You can also find PCB’s in older light fixture ballasts. Nasty stuff.
Yes and when they get old they have a tendency to leak.
I remember some old light fixtures which were replaced when the office were my father worked was renovated, probably in the late 1970ies. We had some of the old ones in the garage and other basement rooms. Occasionally a greasy brown substance was noticed dripping down from the place where the ballast was into the translucent cover (or on the floor when the cover was not fitted). But it took years to think of oil from the capacitors. Then many years later I discovered, that the capacitors really contained PCB oil. But basically my father considered it mainly to be dangerous when burned. He was working in the electricity/utility sector, so he knew the stuff from the big transformers, but he did not knew, that it’s also toxic in unburnt state.
But in the meantime this fixtures are replaced.
Is that really a transformer in the video? I don’t see it – it looks like a fuse burning out and arcing at the last moment.
I’ve seen a transformer blow. What a pretty sight.
Yeah, that’s not a transformer. Looks like a failed insulator.
I’ve had a dubious honor of witnessing three pole pig explosions. One outside my house was benign: a bit of smoke was all. Either a fuse blew or someone killed power before it went too far. The other two were terrifying: the bottom of the can split open along the perimeter weld seam, suddenly releasing a huge high pressure cone-shaped sheet of flaming oil directed at the ground. One of those narrowly missed a couple of pedestrians (the other into an empty parking lot).
Amazingly, all those were each replaced in a 2-3 hours. Gotta keep those meters turning…
Gotta keep those fridges running… And all the other electrical gear we are relying on.
I really don’t think the corporate mind cares much about how cold your fridge is. What they really care about is the few hundred dollars per day of revenue that a single pole pig represents.
The oil in a pole pig is there to be a coolant and insulator, not a dielectric – In that use the dielectric constant is unimportant.
For that matter, the winding are already insulated…it’s really just a coolant with some nice properties in case the wire insulation gets nicked.
On the other hand, the oil in oil capacitors is both. In the big Maxwell caps I have in my physics lab, castor oil is used due to it having both a high dielectric constant (near 4) and a high dielectric strength (good insulating properties in V/mm).
Of course, if you have an uncontrolled arc with one of these 120 uF/12kv puppies, you won’t need castor oil to be “regular”.
“Of course, if you have an uncontrolled arc with one of these 120 uF/12kv puppies, you won’t need castor oil to be “regular”.”
B^)
120 uF @ 12 kV. 8.6 kJ. OK, that will get your attention. Equivalent to a couple of grams of TNT. Or a few drops of motor fuel, about what gets burnt in a single stroke of a single cylinder of a car engine at full power. I’m sure it’s impressive.
Large ball of plasma when discharged through a foot or two of 1/4″ copper pipe. Pipe go bye-bye…ears too…I’m thinking of doing a silly youtube demo out on the shooting range using a bullet to close contacts so I can film from a safe distance….
Interesting. I have no reason to doubt you — I’ve seen what my old 2.4 kJ photoflash pack can do to a chunk of 14ga wire. But I wonder what the plasma ball generation mechanism is. That 8.6 kJ stored is only enough to raise the temperature of a foot of 1/4″ copper pipe about 350C: only about a third of the way to melting point, nowhere near enough to actually vaporize much, if any, of the metal.
Is it the high current leading to some kind of magnetic field instability that physically disrupts the conductor, leading to a mechanical break and the arc actually happening in air, just disrupting the copper, but not actually vaporizing it?
I have seen some of this transformer coils during manufacturing. They were not insulated. They had spacers made from some stuff like phenolic PCB material (the printed circuits stuff, not the toxic oil). But that was only mechanical support. Without the insulating oil they would have arced badly and burnt up at the intended working voltage. Of course it’s true, that the dielectric constant is not important in that application.
I guess “it depends” as I’ve seen youtube videos of pole pig manufacture and the wire is indeed insulated when they wind it. Lots of ways to skin a cat. Volts/inch even on the HV side isn’t so great as to need much insulation turn to turn – I haven’ seen one that would have arced in air, actually (but I haven’t seen the really high voltage one innards – just pole pig class stuff).
Here’s a link – the windings are already insulated in this video (probably not definitive but easy to find in search): https://www.youtube.com/watch?v=1DuDZ3JXjyQ
When I was a teenager, a friend of my dad had a transformer and motor winding factory. They specialized in mine equipment — really big stuff, like thousand horsepower motors the size of minivans, and similar size transformers. After winding they would put the coil, still on its form, into a huge vacuum impregnator: that’s where the insulation went on: some kind of lacquer or resin of some sort. Then it was baked in an equally huge oven. With a setup like that, whatever insulation was on the wire was just superfluous, functioning as spacer: what came out was monolithic windings.
Great article.
“Transformers, more than meet the eyes!”
Dan,
Engaging and competent writing, but this one is kinda thin on the meat, don’t you think?
And one item desperately needs correcting: “Liquid dielectric, with a lower relative permittivity (the preferred term over “dielectric constant”) than air,…” is simply wrong. Air is pretty close to the minimum possible (real) relative permittivity, a fraction of a percent more than the 1.0 of vacuum.
Transformer oils are in the 2 to 2.5 range, but their permittivity is one of the least important properties in that application, as permittivity is essentially irrelevant to the function of the transformer.
A benefit of liquid electrolytes is they are “self healing”. If a capacitor with liquid electrolyte arcs internally, the electrolyte will flow to fill the space and if it’s a type that doesn’t char or produce debris when arced through, the capacitor will be OK. OK if long as the arc didn’t also blow holes in the electrodes or cause them to warp and short together.
Internal arcs in capacitors with solid or paste electrolytes permanently damage them. If they short then that can cause damage to other components.
An arc isn’t going to make a gas bubble except in fumes from breaking down the oil in the first place, plus carbon probably isn’t the nicest thing to have mixed into your dialectric
One exception: thin film capacitors. With a high enough capacitance or a strong enough current source, an internal short circuit will vaporize the spot in the metal film around the short, thus clearing the short. It’s not a property that can be relied on.
Another important property of dielectric fluids for transformers is how tolerant to moisture they are. Mineral oil for example degrades quickly after absorbing only a small amount of water and moisture in the fluid will break down cellulose often used for insulation.
In my experience the main fluid I see used these days is some form of Midel, which according to the SDS is made of 99.5% Fatty acid tetra esters. I have seen it used as a cooling fluid in high powered power converters, cooling/dielectric fluid in naval ship transformers and as a dielectric in 60kV bias tanks for electron guns. It now seems to be industry standard (in the UK at least) due to its high performance without any of the nasty side effects.
https://www.midel.com/productsmidel/midel-7131
Disclaimer: Reading this post back I’d like to say I have no affiliation with the company Midel it just seems to pop up everywhere I see a fluid needed in an electrical system.
“This is an electromechanical device that sits in an oil-filled chamber plumbed to between the transformer and its radiator.” From the diagram and from experience, a Buchholz relay is connected between the main transformer tank and the conservator (an oil tank located above the main transformer).
“Liquid dielectrics are also used in the massive switches that control high-voltage systems, to damp the long, powerful arcs that can occur when circuits are broken in free air.” This is a bit of an over simplification. “Switches” are used in the power industry to disconnect lines and break a relatively smaller amount of current flow (commonly 10,000 amps), oil breakers are an older technology. Newer breakers often utilize SF6 gas.
Dang, beat me to it. It was news to me that switches filled with oil even exist.
I only knew about air and SF6 as ‘insulators’ (both properly with and without other arc quenching technics, like compressed gas to blow the arc ‘away’/out).
I botched that up. Switches 1,000A roughly. Switches no oil. Older breakers commonly used oil.
We used to strip out old transformers and burn the oil to keep warm in the early 70
That’s bad news as incomplete burning of PCBs makes dioxins (any burning that’s not in a high temp incinerator will be incomplete). PCBs are bad, but dioxins are way worse. PCBs will maby give you cancer in 20 years, or kill you through liver damage as your liver struggles and fails to break them down if you’re exposed to it repeatedly. Dioxins will just kill you directly. Also note, over time PCBs in high voltage environments can start to break down to dioxins. As if things weren’t bad enough with old transformer oil.
There have been reports of our neighbours up north in West Africa (I’m in South) using old transformer oil for cooking purposes because it never turns old.
Fantastic deep dive into an often-overlooked topic! Liquid dielectrics don’t get nearly enough attention in mainstream electronics discussions, yet they’re crucial in high-voltage and cooling applications. I especially appreciated the historical context and the balanced comparison of different dielectric fluids. It’s refreshing to see such technical nuance paired with practical insight—great job shedding light on this area. More content like this, please!