It’s no surprise that we here at Hackaday are big fans of Fritzing KiCad. But to a beginner (or a seasoned veteran!) the learning curve can be cliff-like in its severity. In 2016 we published a piece linking to project by friend-of-the-Hackaday [Chris Gammell] called Contextual Electronics, his project to produce formalized KiCad training. Since then the premier “Getting to Blinky” video series has become an easy recommendation for anyone looking to get started with Libre EDA. After a bit of a hiatus [Chris] is back with bite sized videos exploring every corner of the KiCad-o-verse.
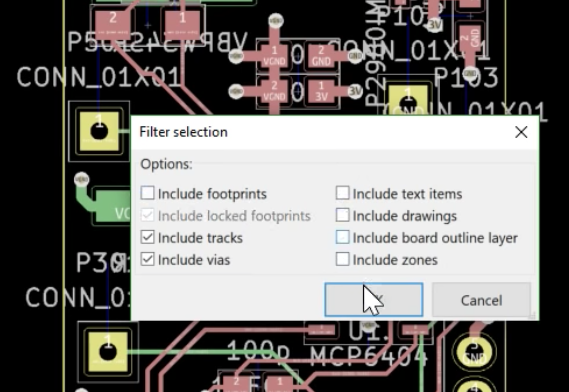
Some of the videos seem simple but are extremely useful. Like this one on finding those final disconnected connections in the ratsnest. Not quite coverage of a major new feature, but a topic near and dear to any layout engineer’s heart. Here’s another great tip about pulling reference images into your schematics to make life easier. A fantastic wrapped up in a tidy three minute video. How many ways do you think you can move parts and measure distances in the layout editor? Chris covers a bunch we hadn’t seen before, even after years using KiCad! We learned just as much in his coverage of how to rip up routed tracks. You get the idea.
We could summarize the Youtube channel, but we aren’t paid by the character. Head on down to the channel and find something to learn. Make sure to send [Chris] tips on content you want him to produce!
kicad, almost as good as 2001 era eagle
ive been meaning to transition away from eagle. the biggest issue with it are those atrocious part libraries which always have problems that require fixing up. also how useless the part search is. cant seem to get through any project without making 2 or 3 new parts from scratch. does kicad have a better way of dealing with that stuff?
Well to be honest, Kicad has improved a little compared too past versions(since 4.X). The component searching is now available in a list without major pc slowdown, because it needed to search directly from Git every time at first. Since version 5.X, all symbols and footprints are pre-installed, meaning that the installation process of Kicad is quite long.
So Kicad still has a way to go when updating footprints and symbols, because you need to manually install the latest footprint and symbols by installing a new Kicad version or pull the latest updates from the Kicad Git repositories*.
At least the positive think about having repos, is that there is a community behind it adding more and more footprints and symbols :-)
Hopefully people will implement the symbol/footprint generation scripts over time. Generating parts like pinheaders are very useful since you can install a single script which generates pinheader 1 to xx in place of 100+ symbols and footprints of the same pinheader with only a different pincount. This can be implemented for other parts as well.
*
https://github.com/KiCad/kicad-symbols
https://github.com/KiCad/kicad-footprints
Try DipTrace and never look back…
The library updates (and the maintainers that are creating parts) has been one of the best things about 5.0 and beyond. The breadth of the maintained libraries are visible here: https://github.com/kicad
I still regularly make schematic symbols for new parts I encounter. However, the decoupled nature of schematic symbols and footprints means I almost always find the footprint I need.
Wonder when KiCad will finally go SAAS like Eagle… Oh, that’s right… Never!
I’m admittedly new, so I can’t speak to the higher end features, but I found KiCad easy enough to learn, thanks to a few of Chris’s videos, and now I quite enjoy using it.
Use what works for you and what fits into your budget.
Beats AutoCAD Eagle by not trying to fuck over users who don’t like renting software instead of owning it.
After many years of Autodesk calling buying there software an “investment”, then making it next to impossible to transfer that investment to another person, and then cranking up the maintenace fee by 10% or 15% for many years in a row, upto the same point as the rent price, making that whole investment a waste of time, I started to actually love Microsoft, just because the whole love scale got moved sideways by an order of magnitude. Even there free stuff is not worth wasting a part of your life on.
Real engineers create schematics in emacs
Real engineers write netlists in ed.
Fair point, ed IS the standard text editor https://www.gnu.org/fun/jokes/ed-msg.html
I gave Kicad a try. Twice. Both times it became too frustrating to get anything done. I’ve been making boards for over a decade with ExpressPCB, because it’s really easy to use, but my need for gerbers finally drove me away.
I switched to Diptrace and the learning curve was small, I was making progress in no time and in a week I completed my board. Never going to try Kicad ever again.
Without knowing what exacly your problem was, I’m asking myself what could have been so frustrating. There are tons of tutorials. The basic stuff is not difficult at all. Never heared about the two tools you mentioned so I can’t compare them. When I was switching from Eagle I didn’t want to go back after a week.
Yes, KiCad is hard to learn, but it is worth it. Switched from Eagle years ago and still not regretting it.
I love this software…
I love KiCad. I was using Eagle for years. The free version is just too restrictive (100×80 mm, max. 2 Layer, can’t place parts outside of the pcb). I tried CirciutMaker. But I don’t like having everything in the cloud and beeing forced to publish everything. Having every file online also felt slow without a good internet connection. Switching to KiCad takes a bit of time. (But I didn’t get into CirciutMaker very well too.) Now, after working with KiCad for some years I’m really happy with it. And I don’t have to create more custom parts than I had to with Eagle.
Now that I look back on it, I think the “can’t place parts outside the PCB” restriction was a huge part of what drove me to KiCAD in the first place. It was infuriating to pick up a component that EAGLE automatically placed outside the PCB, try to put it back down for later, and then be told “BZZZT! You can’t do that! Put that part somewhere on your PCB to clutter everything up!”
This! This bzzt is the best encouragement Eagle could do to make me spend an hour and learn KiCAD. Thanks Eagle!
Out of interest are there any written guides? I find video guides harder to follow than something in text. I’ll give these a go though as I have an amplifier that is almost out of the proto stage and I want to make a nice pcb for it, I think it might be larger than Eagle will allow though lol
The formal documentation on their website is not the best, but it generally is the best place to look for information first. KiCad is getting quite a few updates and a lot of the tutorials are outdated, so I found you have to look at the official documentation to check the newest way to do something.
As a companion to the official documentation which explained all Kicad features, I found the following ebook (pdf) ( https://techexplorations.com/product/kicad-like-a-pro-2nd-edition-sample/ ). Unfortunately the ebook is not under a GPL-like license. But regarding the efforts with the author put into it, I do also understand that the current authors’ decision.
I found the e-book very helpful, as it showed amongst others how to handle a project from the beginning to the end. There are multiple projects with different complexity described, from a very simple project to more advanced projects. Also it has a dedicated chapter called ‘Recipes’ offering practical help on separate subjects, which I did not find in the official documentation. As a long-time user of Eagle, I was also very unhappy with their SAAS model and decided to switch to KiCad. And yes, it is likely possible to make PCBs without a manual at all, using just common sense and experience from other PCB design software, but starting directly from the beginning with doing the right things will help to prevent pit-falls. (Like how to handle libraries, setting up and using the autorouter, the PWR-FLAG, creating parts and symbols and many more basic things, which I knew how to do that in Eagle but not in KiCad.)
Rather than watching videos, I preferred something to read and pick-up from there. I would use the videos as something as a last resort.
I would love if a KiCad fundraising could be initiated to have formal documentation freely available as good as the ebook is.
sooooo gooood …. thanks Chris
KiCAD? Hard to learn? Your not doing it right then.
Ok, let me give you a tip here. Do what I did. Try to learn gEDA first. I mean really try hard, get yourself convinced that it is the only solution for you and put some real time and effort into it.
Then when you finally can’t take it anymore break down and switch to KiCAD. Trust me, KiCAD will feel like a piece of cake!
Good luck and enjoy!
Learning KiCAD isn’t hard.
The trick is to try to learn gEDA first. Give it a real effort. When you give up KiCAD will feel like a piece of cake!
At a previous employer, the engineering department was reduced from 6 engineers/2 technicians/2 drafters/1 clerk to two engineers and a clerk when most stuff was moved to Asia. As part of this restructuring, we dumped mickeysoft, altium, solidworks, and other licensed products. KiCad was the only ‘cheap’ board design system considered reliable. We did test Eagle (and others), but could not make it be useful per our needs. And specialized tools not part of KiCad were quickly done in Python. Windoze was easily replaced by Linux servers and desktops, but up to the point where I left the company, there was never any suitable replacement found for solidworks.
Should note that while KiCad was free, it was not a zero-cost system. It took two weeks to migrate parts libs and designs and DFC work-flow stuff to KiCAD. The one-time cost for ‘buying’ KiCad was approximately $65k USD.
That is a great thing to point out, no system is truly free. In fact, paying for CAD tools, you’re often just paying to offload much of the work! Are you still in touch with them? Any word on how it panned out?
Most of the Python stuff I wrote is still being used. KiCad in general is mostly being used by this company to support legacy product lines. Import and export of libs and all other stuff remains fully automated and has not changed. DRC has changed, and I recently completed a consulting project for my former employer to update and add new scripts for this stuff. The remaining people do not see any of this as permanent infrastructure to be adopted by other parts of the corporation because this company, like many others, probably wants to shut down all U.S. manufacturing and engineering. So when the local part of the company goes to just sales, will probably try to GPL the code and send to CERN, although am not certain that they would want to implement my Klingon language support files.
I learned kicad on getting to blinky vids, thanks for the most concise series of tutorials on board design, and for keeping it renewed and refreshed.
Previous versions of KiCad was bad, very bad. The UI wasn’t consistent, different tools acted differently, and you couldn’t place things like thermal vias without a trace connecting them. Not to mention the library management was terrible.
But within the past year it has improved dramatically. I’m no longer reluctant to use it, and was able to make difficult designs with a few python scripts.
As the creator of https://github.com/pointhi/kicad-footprint-generator I can tell you at least half of the footprint library is created by those scripts. In case of 3d-models almost all of them are script generated (by a different project).