Regular readers will recognise this as the third part of a series exploring blacksmithing for those who have perhaps always fancied having a go but have never quite known where to start. It’s written from a position of the unusual experience of having grown up around a working forge, my dad may now be retired but he has a blacksmith specialising in architectural ironwork.
So far in this series we’ve looked in detail at the hearth and anvil that you might find in a typical forge, and delivered some pointers as to where you might look to find or even construct your own.Those are the signature pieces of equipment you’ll find in a forge, but with them alone you can still not be a blacksmith.
If I Had A Hammer…
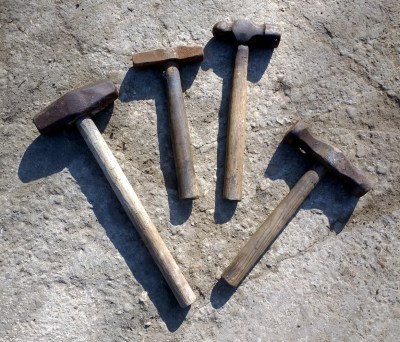
Given an anvil, a hearth, and a vat of water to quench hot work in, and you’re almost set for your forge, but not quite. Most of a modern blacksmith’s workshop is the standard metalworking assortment of welders and angle grinders, but there is a set of tools that remain essential for blacksmithing alone. Your hammers are what connect you to the work, and can be as individual as the preferences of the blacksmiths themselves. There is no “right” answer to the question of what hammer you should use, instead you should use the one that works best for you. I instinctively favour a round-faced ball-peen hammer because that’s what my dad mostly used, but for example my Dutch friends use square faced cross-peen hammers. Blacksmiths will often make their own hammers to suit their needs, for example my dad made more than one using the high-quality steel of vehicle half-shafts as a starting point. Hardening them is a specialist skill in its own right, and I remember quite a few experiments before he perfected it.
It may well be stating the obvious, but the weight of the hammer influences how much energy it can impart to the work, and in turn the size of work that can be done. Casting an eye over my dad’s hammers the three workaday weights were 2 pound, 3 pound, and 4 pound (roughly 1 kg, 1.5 kg, and 2 kg), allowing a variety from fine work to heavier hitting of larger pieces. In a recent project, making a mediaeval nail, I selected an unsubtle lump hammer to draw out the larger square stock, and a much smaller one to finish it up, create the fine point, and relatively thin head. These are only a subsection of the hammers at his disposal though, like most blacksmiths he has a variety for all tasks, up to sledgehammers. I have frequently taken my turn either holding a piece with tongs while he used a sledgehammer, or on the sledgehammer myself.
Tongs, for Hot Gripping Moments
Keeping yourself clean, safe, and not on fire
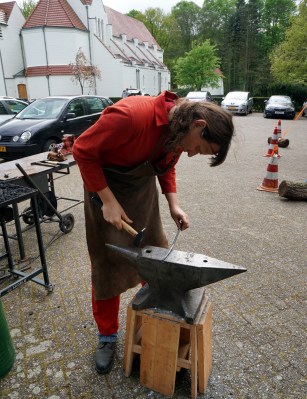
A final moment for today should be spent on the subject of protective equipment. The hazards of blacksmithing are relatively uncomplicated, but some basic protective clothing is still very much worth having. The most obvious hazard is heat, you will be working in a noisy environment with red hot metal and fire. Though you will generate fewer sparks than you’d expect, I have a blacksmith’s leather apron and a set of fire-resistant overalls. Both of these are readily available from blacksmith’s supply stores, and are well worth the investment. There are also a lot of heavy and sharp items involved, not to mention hot particles on the floor. For that reason I also have a set of steel-toecapped workboots rated for hot particles. They aren’t the most elegant of footwear, but they have saved me from a few nasty moments.
I do not have any face protection specifically for blacksmithing, but depending on the work in hand there may be some sparks created. A polycarbonate face shield rated for hot particles should be available from any safety equipment supplier, and shouldn’t cost too much, and is an essential thing to own if you are doing any grinding or rotary wire brushing. Beyond that, there are also leather gloves designed for handling hot metal. I don’t use them because I prefer the feel of the hammer directly and am happy to use a pair of tongs to hold hot pieces of steel.
We’ve taken you through the basic workshop equipment of a blacksmith over the last few episodes of this series, and you should now have a basic idea of the safety kit you would be well advised to own. From this foundation we’ll next take you into the forge and start looking at a few blacksmithing techniques and simple projects, and along the way we’ll see some of the materials involved, too.
Hearing protection?
Good point.I was however thinking primarily in terms of blacksmith-specific PPE rather than more general ones.
WHAT?!
SPEAK UP!
These blacksmith articles are good stuff.
You mentioned the anvil height. Recommended working height of materials and tools relative to the worker?
^this^
Where does the anvil top work best for you Jenny?
Wrist high? Waist high? I think elbow height would not work for me…
I was taught that the anvil needs to be at knuckle height of your fist
Sounds about right.
But is it? The knuckle “rule” stems from a period when lots of blacksmithing was done with the help of a striker with a sledgehammer. It’s old dogma that sticks around.
When I don’t have to bend down. I’m among the tallest in your average hackerspace, hence this one is a bit low. It’s a matter of personal comfort though.
While I’m no blacksmith, I would think that the proper height would be achieved when the face of your hammer naturally strikes flat on the piece when you swing.
This is where my mind went to. But I still have a lot to learn. Would love to know the best ergonomic answer.
The general rule of thumb is to hold your arm to your side and close your hands enough that you could hold a hammer ( not a fist ) where your knuckles end up, that should be the height of your anvil.
From personal experience that’s a decent place to start, and can vary quite a bit from person to person. I’m proportioned a little off, being more upper body than lower but my arms are not longer in proportion. So if put my anvil at that height, it is too high to be able to hold tongs or stock between my legs so that I can use both hands to work something on the face of the anvil, so I have to set my anvil a bit lower.
Jenny, please keep these coming.
+1!
Indeed I will. I’m not a guru-level smith though, this is the combined experience of growing up in a blacksmith’s business.
Great article, takes me back to our school metalworking classes where we got to use the forge. I’ve still got several bits we made in class including cold chisels and a fancy door handle, and 45 years on, I’ve still got the burn scar on my arm where another pupil wasn’t looking where that bar of bright red hot metal was going. So, yes some PPE would be a good idea.
When you make your first pair of tongs, drill a nice large hole for the pivot. Tongs are pretty much bolt cutters for a rivet, and boy do you regret your choice of a soft steel 12 gauge piece of wire for a pivot when you grab something hot and the tong pivot snaps. (In retrospect, of COURSE that wasn’t a good choice…)
Good point. :)
I made a hammer out of a half shaft once, it was a broken by careless use of the clutch, so it had splines and a pig ugly other end, it came out of a daf 2800 and I just welded a handle welded to it.
not only did it hurt to use, there’s a reason handles are wooden or softish but it was wildly out of balance and the splines left a terrible finish, and yet someone still stole it!
I think the craziest hammer I’ve ever seen was a 1 ton Ford truck axle shaft (They look something like this https://eastcoastgearsupply.com/i-969341-dana-60-70-80-rear-cut-to-length-chromoly-shaft-35-spline-33-5.html) with the end with the bolt holes dunked into a 40 lb ingot of molten lead that was then allowed to solidify around the shaft
Been said before on your blacksmithing topics, which are most excellent btw, but you’re still not doing the proper PPE.
Face shield protects the face but glasses protect the eyes and are worn under it.
I avoided this for years, CBA putting on PPE when grinding, but of late (having kids TBH) I started thinking more and now when I grind I dont my glasses and hearing protectors and depending on teh job the face shield too.
Like it’s my religion.
A couple of fingers have the mark of the holy grinder on them, but I still have all 11 of them thankfully.
“vat of water to quench hot work in”
you say this but on Forged in Fire they all have a conniption fit any time someone quenchs in the water and probs 7/10 it doesn’t go well.
So why water and not oil?
Or why oil and not water?
I’m guessing thermal shock – the oil is heated hotter than the water can be ?
My father never used to wear PPE until he essentially repeated the accident that had caused his brother to lose an eye only months earlier. My father was INCREDIBLY lucky that he didn’t lose his eye. He also has permanent hearing damage because of grinding without ear defenders.
Close calls will do that!
But because it is gradual and the damage rarely painful, hearing loss is far more common. While for some it is genetic, for many it is environmental.
I get to blame genes _and_ too much rock n roll, race cars, and the like.
I do mention that you need a face shield for grinding, up above. Normal forging though, not so much.
Face shield AND goggles.
Face shield is for exactly as read. It’s not acceptable eye protection.
Appreciate it might just be grinding, but that soon turns to cutting and blades do shatter.
I can grind with a face shield and sparks will still find a way around it.
No bravado here, just a case of why not that extra protection if you can !
See the CNC cutting thread with people admiting to poor PPE and having semi-blinded themselves with lasers.
Or do as the nuclear bomber pilots did and wear an eye patch so you get two chances :)
Water conducts heat away faster than oil, so it provides greater cooling per unit time. Sometimes you want that, sometimes you don’t. Water has always been the traditional smith’s quench, but that’s because of cost not performance. (And if you are forge welding and build a coal enclosure to form a reducing atmosphere you traditionally use water to wet down the outside of the enclosure to keep it together, where oil would result in So Much Excitement.)