If you move as a hardware hacker through the sometimes surprisingly similar world of artists, craftspeople, designers, blacksmiths, and even architects, there’s one piece of work that you will see time and time again as an object that exerts a curious fascination. It seems that designing and building a chair is a rite of passage, and not just a simple chair, but in many cases an interesting chair.
Moving Charis From Artisan to Mass Market
The new materials and mass production techniques of the 19th and 20th centuries have brought high-end design into the hands of the masses, but while wealthy homes in earlier centuries had high-quality bespoke furniture in the style of the day, the traditional furniture of the masses was hand-made in the same way for centuries often to a particular style dependent on the region in which it was produced.
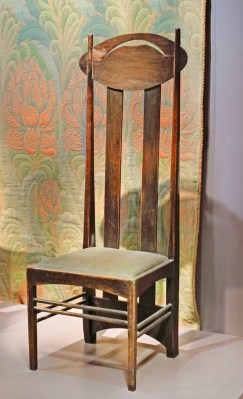
I’m at a hackerspace in the English county of Buckinghamshire, so for example the traditional local chair design here is the classic English Windsor chair pictured above. Its legs were hand-turned on a temporary pole lathe in the beech woodlands of the Chiltern Hills by a traditional craftsman known as a bodger. Its seat and chair back parts were made and assembled by other specialist craftsmen in an industry localised around the town of High Wycombe. Windsor chairs gained some features such as a steam-bent rear frame over the several centuries in which they were made in this manner, but they did not otherwise significantly change in design. They evolved to meet a need using the available materials of the region and stayed that way until the artisan industry died out in the face of mass production. In the case of Windsor chairs, the traditional trades have been revived in the last few decades, but if you buy a Windsor chair today the chances are it was made on modern machinery in a factory.
As furniture moved from being a bespoke product produced by local craftspeople into one of fashion and manufacture driven by an emerging consumer class, its design shifted from those craftspeople to a new breed of artists. Industrial design as we know it today might not have been formalised into a profession, but artistic movements such as the 19th century Gothic Revival and later Arts and Crafts and Art Nouveau movements included furniture designers whose work had a heavy influence on the mass-produced pieces that would have graced the homes of the masses. My grandparents had more practical dining chairs with a visible mass-market influence from pieces of furniture in a similar style as the Charles Rennie Macintosh chair pictured here.
Modern Materials and Techniques Have Changed How We Sit
It is impossible to spend much time in the 21st century without seeing the influence of Arne Jacobsen’s 3107 chair; the original was manufactured using formed plywood and its echoes can be found in many others in different media. Stores such as IKEA have immersed us in high-quality design in cheap materials to the extent that we take it for granted, but somehow the signature form of the domestic industrial designer hasn’t made it into our world of makers and hackers. As an engineer I find this puzzling, because a chair is simultaneously a thing of universal need and engineering challenge.
There may be some left-field Hackaday editors who prefer to use a standing-up desk, but the majority of us spend our time seated. Our chairs need to be stylish, practical, and supremely ergonomic, while also being without inherent design flaws that might cause them to collapse while someone is sitting in them. If that doesn’t throw the gauntlet down to the hacker as much as to the architect or the industrial designer, I don’t know what does!
Chairs: Your Engineering Challenge
You can use MakeHuman or similar modeling software can to create a virtual you. From there, detailed measurements of the seats you find most comfortable can be compared to your virtual MakeHuman character to establish guidelines for your most comfortable seating position. Choose your materials, and get started on the prototype.
I’m both a textilist and a metalworker so my ideal chair uses a forged and welded steel frame and an upholstered seat. Again, modern tools make this much easier than in the past as a 3D seat model can be flattened to produce a two-dimensional fabric patterns.
As the plan comes together you can even run finite element to design a steel framework without weak points such as the meeting of the two legs at the side of Robin Day’s HilleStack polypropylene and steel chair. The frame also must distribute weight evenly onto the floor such that it doesn’t damage the floorboards. I think I could do that, but I suspect the weight of a forged steel frame would make my particular dream chair less practical. And so you can see the challenges stack up: comfortable but beautiful, beautiful but strong, strong but not overly heavy.
Fine Examples of Hacker Chairs
I said we had a couple of examples in Hackaday’s library, and it’s worth bringing them up as a bit of inspiration. The first is Talon Pascal’s very well-executed copy of Henrik Thor-Larsen’s iconic Ovalia egg chair from 1968. This demonstrates very well that to have a design chair of your own you do not even have to design it, if there is an iconic seat that does it for you it’s always possible for you to make a copy. In Talon’s case the copy uses different materials from the original, instead of fibreglass he’s used thin strips of wood. This is hacking at its finest, and from what we can see we’d be hard-pressed not to believe it was the real thing.
Another standout project in the Hackaday ecosystem is Eberlin’s interlocking plywood chair. This is much more in the vein of the one-off design chairs listed above, and ticks all the boxes of using innovative manufacture and construction techniques. Having never sat in one I have no idea whether or not it is comfortable, but this chair could be manufactured and sold tomorrow drawing from just one single material. If it had come from a noted designer it would be instantly famous and considered a design classic, let’s hope by pulling it up in this article it gains a little bit more attention.
Having spent a while looking at chairs and understanding that there is more to them than meets the eye, I hope some of you have been inspired to follow in the footsteps of those famous designers and have a go at creating your own. This topic may not be the usual Hackaday fare of microcontrollers and robots, but that makes it no less worthy of your consideration. I look forward to seeing (and sitting in) your creations.
Eberlin’s chair is attractive and looks sturdy as hell, save for the legs when it comes to side loads, perhaps. Maybe creating some notches and adding a perpendicular piece of plywood to create a T-beam would help? All that’s left is a nice finish.
The hallmark of DIY chairs is often an overengineered chunkiness.
Yeah. Like the first one ever, a stump :)
That may be so, but if you can’t convince people to sit in your chair for fear of breaking and injury, what chance do you stand at getting them in the seat of your powerwheels with a Tesla drivetrain?
And all this thanks to Simon Chair.
the ultimate hacker chair: https://hack42.nl/wiki/Gebruiker:MacSimski/KKN_stoel
…otherwise known as a ‘Kentucky Stick Chair’. Good find!
I do bentlam panels at work, and I’m not at all surprised that we don’t see more of it here. A bentlam plywood chair seat is like a skateboard deck, only much larger and more difficult to trim to final size. For a one-off project, you’d spend way more time making all the jigs than building the actual piece.
I like my stool warm and squishy :3
I need a chair that can cater for my requirements in terms of high volume gas exchange with the atmosphere.
To me, the best chairs are the ones whose design makes good use of circumstance. Fulfilling the need to a basic level isn’t hard, fulfilling it well but extravagantly isn’t THAT hard, fulfilling it well enough with what you could scrape together is where the chance to shine is hiding.
I have a mishmash of chairs I made or remade from serendipitous scrap (but that people seem to like), from which I infer that (a) I’m only about 1/4 of the way along the road to being _good_ at making chairs, and (b) that doing well enough that others enjoy the result, is within reach without perfection and is worth going for. And that’s the point here, isn’t it? Can you meet a need and delight people at the same time, without needing what you do to be treated as super special. If not, change a parameter and try again.
So, not that different from other areas of design then?
Hard to beat the chair that can be made from only one 2×4.
https://hackaday.com/2011/07/24/hackaday-links-july-24-2011/ (bottom entry)
Moving Charis From Artisan to Mass Market
chairs, like the humble can opener, are lostech.
Being a wood worker from an early age, learned to appreciate chairs early on. The thing that still impresses me about chairs is just how well they can support a load. Even exotic designs like the bar stools that are formed from a continuous tube bent into a triangular strut. The aforementioned design is really nice for how it also springs slightly which is awesome at a work bench, assuming you make your bench high enough for it.
My favorite chair however is the simple office chair. So many interesting mechanisms packed into the base of it and every brand has their own method of replicating those mechanisms. Some aren’t so great, like the one I had to add a cotter pin to a week ago because the seat balanced on the raise/lower lever but that lever could travel too much horizontally to be stable on it’s own. Others really stand up to the test of time like my last chair which lasted from 2004 until 2016 and who knows how long at the office building I rescued it from (was scuffing their floors, just needed new wheels).
There’s also the classic shell chair by Ray and Charles Eames, a truly iconic design often seen in mainframe computer rooms and offices in the sixties. They were clever film producers as well, and this film on this chair is no exception: “How to build an Eames shell chair” from the 1960s https://www.youtube.com/watch?v=PIlTtXrgA0c
Wow, what a find! Thanks for that.
You’re welcome, glad you liked it. They also produced the mind-blowing (for me, seeing it at the theatre before main feature when I was a kid) and famous ‘Powers of Ten’ for IBM:
https://www.youtube.com/watch?v=0fKBhvDjuy0
And the truly whimsical and lovely in its simplicity ‘Tops’:
https://www.youtube.com/watch?v=UJ-VFMymEiE
You know the saying about Youtube watching ‘…that was x minutes of my life I’ll never get back’?. The Eames films will not make you think that.
If you want a nicely form-fitting chair of sorts, I’d suggest using expanding foam and (several) bin-bags. I was introduced it as a way to make a seat for kit-cars (making use of the panelled area one would sit in to contain some of the expansion, you get an assistant to pour two-part expanding foam into a bin bag that you’re sitting on to create a perfect match to your own frame.
They can either be used as-is, painted or coated in something more hard-wearing – just watch out that it can be very much *form fitting* so either wear extra layers when making it, wiggle around lots or never be able to put on weight :-)
I’ve been wanting to revisit the technique but as a way of create a negative mould of myself so I can then create a form to then use as a buck for a carbon-fibre recliner frame that is actually to my proportions.
Maybe one day.
I would add, be careful to use a slow setting foam or have enough layers between you and the foam to insulate from the heat. The fast settings foams can get VERY hot, especially in thicker layers
interesting – what do you consider ‘slow’? :-)
The foam I was working was fairly quick setting (maybe a 5-10 minutes between mixing and it being a firm foam) but I don’t recall there being any discernible heat being given off despite always sitting against it with little more than a plastic bag and a t-shirt between me and it.
It definitely gets a bit warm with that foam – not massively so though. Of more concern was whether the binbag could contain the foam as it expands around the nether areas.
They also last – my foam seat has lasted over 15 years and 30k miles, clad only in duct tape.
5 to 10 minutes is already the slower version. I’ve also seen some 30 minute setting stuff at some point, but can’t find it now. I’ve encountered AB foams specifically intended to make close fitting packaging, that set within a minute of getting mixed. You squirt some into a bag from a machine that automatically seals it, dump in into the box, put the product on top and hold it in place until the foam has set. Then you do it again but dump the bag on top and close the box. Then your product is basically sealed in a formfitting foam insert. However that stuff got HOT. Hot enough that it was actually a concern with some of the plastic packaging and hot enough that you didn’t want to be handling it immediately after setting.
What? Nobody has made a reference to the iconic chair in Woody Allen’s “Sleeper”?
https://www.youtube.com/watch?v=sOyn9MaZGqY
You’re Sitting On An Engineering Masterpiece: Toilets As A Design Challenge
I recommend reading Christopher Schwarz’s “The Anarchist’s Design Book” to everyone, who is interested in how masses designed and built their furniture.