Most Hackaday readers will be a pretty dab hand with a soldering iron. We can assemble surface-mount boards, SOICs and TSSOPs are a doddle, 0402s we take in our stride, and we laugh in the face of 0201s. But a Twitter thread from [Greg Davill] will probably leave all but the most hardcore proponents of the art floundering, as he hand-wires a tiny FPGA in a BGA package to the back of a miniature dot-matrix LED display module.
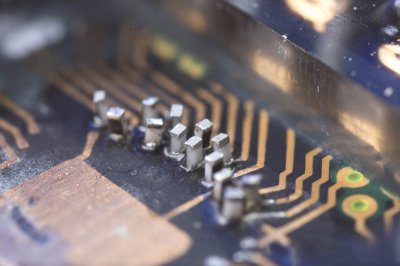
As far as we can see the module must once have had its own microcontroller which has been removed. We’d guess it was under an epoxy blob but can’t be sure, meanwhile its pads are left exposed. The Lattice LP1k49 fits neatly into the space, but a web of tiny wires are required to connect it to those pads. First, [Greg] populates the pads with a set of “tombstoned” tiny (we’re guessing 0R) resistors, then wires them to the pads with 30μm wire. He describes a moment of confusion as he attempts to tin a stray hair, which burns rather than accepting the solder.
The result is a working display with a new brain, which surprises even him. We’ve seen more than one BGA wiring over the years, but rarely anything at this scale.
It’s worth mentioning that [Greg] was behind the FLIR frame grabber that was a runner-up in last year’s Hackaday Prize. We admire the photos he’s able to get of all of his projects and aspire to reach this level with our own. Take this as inspiration and then check out the Hackaday contest for Beautiful Hardware images happening right now.
Thanks [Sophi] for the tip.
If you laugh in front of a 0201, it probably will be the last time you will see that component. These things flow away and disappear just by looking at them the wrong way
I always figure that working 0201’s is the closest i will get to putting anything else into orbit. As they definitely end up on that trajectory quite often with tweezers.
I bought some by accident once. You’re not kidding. It’s like looking at a packet of sand. I couldn’t even see them clearly. They were in danger of disappearing into the grooves of my fingerprint.
I’ve breathed on front of 0402 LEDs and they’ve flown away (ordered by mistake). I won’t touch them anymore. 0201s I won’t even look at them. I’m getting too old to work on these. At my age and even with a microscope I’ve decided not to work on anything smaller than 0805 and I prefer 1206. If things keep getting smaller I’m going to have to get (or make) something to address the problem.
Top 3 toughest soldering jobs I’ve done are probably 3: Reattaching a side button switch to an old Blackberry; 2: changing the battery in an old GoPro wifi module; and 1: replacing the through-hinge speaker wire in a Palm Treo 180. I’ll never forget the two tiny, tiny gold forks involved with that one, maybe 1mm wide and 2mm long. They pinched 2 fine wires into a plastic block, piercing the insulation and forming a 2-pin connector. If one of these forks got under your fingernail you’d have a hell of a time getting it back out, once you found it. Of course I dropped one on the floor too. I’ll be happy if I never do anything to knock one of these jobs off the leaderboard.
I used to be pretty good with an ultrasonic wire bonder and IC chips, but without a microscope I have a hard time with anything smaller than 7 pin tube sockets.
Originally there was not a microcontroller in the display. Microcontrollers wasn’t common then. It originally housed an ASIC – Simple state-machine logic.
Awesome! You could probably use different size resistors and stagger the heights.
“He describes a moment of confusion as he attempts to tin a stray hair” – This wins the internet for today.
>we’re guessing 0R) resistors
That’s a bad guess. They are likely to be series resistors for current limiting. They are driving LED array after all. Given the soldering skill, the person could have soldered wires directly bypass the need for 0R.
I have a lot of single-sided boards that use 0 ohm resistors as jumpers. I suspect it’s because they’re more reliable in pick and place machinery than placing wire jumpers.
Yes, that’s well known. But in this case no pick and place machine was involved and soldering the wire directly to the pads seems easier than “tombstoning” the resistors. So I don’t think they are 0R
For small wire in close quarters I like to use tweezer style sprue cutters instead of the plier handled type he uses in the video. Kotobuki thread scissors work well also and are very inexpensive. The article reminded me of an idea I had for an infrared soldering iron. A car headlight halogen bulb has just about the right wattage and combined with a Zinc Selenide lens could make for a decent diy micro-soldering station. The lenses used to be a bit pricey but now they are less than $20 on ebay.
Thanks for the tip! Yes I thought my side cutter were comically large compared to everything else.
Interesting idea about the ZnSe lens… I’ve been trying to think of ways to melt the BGA solderballs without the risk of wicking away all the solder. I even have some ZnSe lenses sitting around from some LWIR camera experiments.
I’ll just be over here not even considering anything smaller than 0805 and staying the heck away from leadless packages.
QFN may not be that difficult with a hot air gun by surface tension. Here’s my first try sometimes ago:
https://tada.inexacte.science/had.jpg
Looks good! I have a hot air gun, but decent leadfree paste can be expensive. Maybe I’ll try it anyway though. Although considering how mess my 0805s look that might not be the best plan…
Looks for all the world like a DLR1414.
Here’s a DL1414T chip I tried to brutally decap after blowing it up: https://imgur.com/EA9426M (12MiB)
This is awesome work. I wonder if for solder joints so small a laser would work as a soldering iron? At least it WAS possible to get quite strong ones from China, i’m not sure of todays situation and i won’t try it, but somebody?
The smallest i did yet was soldering 100µ wires to a QFN 3x3mm with 0805 decoupling capacitor on top of it. Possible, not even so difficult, but not fun. Will see what stuff gets under my microscope in the future.