It’s fair to say that 2019 has not been a good year for the aircraft manufacturer Boeing, as its new 737 MAX aircraft has been revealed to contain a software fault that could cause the aircraft to enter a dive and crash. Now stories are circulating of another issue with the 737, some of the so-called “Pickle forks” in the earlier 737NG aircraft have been found to develop cracks.
It’s a concerning story and there are myriad theories surrounding its origin but it should also have a reassuring angle: the painstaking system of maintenance checks that underpins the aviation industry has worked as intended. This problem has been identified before any catastrophic failures have occurred. It’s not the story Boeing needs at the moment, but they and the regulators will no doubt be working hard to produce a new design and ensure that it is fitted to aircraft.
The Role of the Pickle Fork
For those of us who do not work in aviation though it presents a question: what on earth is a pickle fork? The coverage of the story tells us it’s something to do with attaching the wing to the fuselage, but without a handy 737 to open up and take a look at we’re none the wiser.
Fortunately there’s a comprehensive description of one along with a review of wing attachment technologies from Boeing themselves, and it can be found in one of their patents. US9399508B2 is concerned with an active suspension system for wing-fuselage mounts and is a fascinating read in itself, but the part we are concerned with is a description of existing wing fixtures on page 12 of the patent PDF.
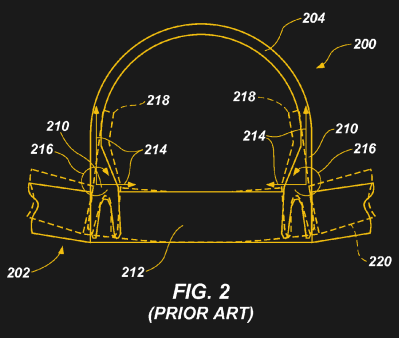
The pickle fork is an assembly so named because of its resemblance to the kitchen utensil, which attaches firmly to each side of the fuselage and has two prongs that extend below it where they are attached to the wing spar.
For the curious engineer with no aviation experience the question is further answered by the patent’s figure 2, which provides a handy cross-section. The other wing attachment they discuss involves the use of pins, leading to the point of the patented invention. Conventional wing fixings transmit the forces from the wing to the fuselage as a rigid unit, requiring the fuselage to be substantial enough to handle those forces and presenting a problem for designers of larger aircraft. The active suspension system is designed to mitigate this, and we’d be fascinated to hear from any readers in the comments who might be able to tell us more.
We think it’s empowering that a science-minded general public can look more deeply at a component singled out in a news report by digging into the explanation in the Boeing patent. We don’t envy the Boeing engineers in their task as they work to produce a replacement, and we hope to hear of their solution as it appears.
[via Hacker News]
[Header image: AMX Boeing 737 XA-PAM by Jean-Philippe Boulet CC-BY 3.0]
I have previously worked at one of the facilities that made the aluminum pickle fork for the 737. When looking at Fig 2, on the right side, the pickle fork starts at the fork tip, and the tail extends all the way at or around the marker indicated by item 200. Without much engineering change, these could be strengthened by using a different material. If titanium, the cost would be significantly higher, but weight would remain similar.
That’s exactly what we are doing. Don’t worry, we’ve got this!
It was actually quite fortuitous. The answer to the problem just happened to come up in my Youtube feed as well as several websites’ ad banners the very day we discovered this problem [and every other day for the last year].
We are going with Mark Forged Enhanced Carbon Fiber PLA!
I would really like to know if this is sarcasm.
It clearly is.
Were accelerated load tests on a full size pickle fork prototype performed?
If so, what conclusions were reached concerning likely failure modes?
It’s a 7075-T73 die forging. How would strength be a problem here? Switching to “titanium” would solve nothing.
Not necessarily a strength problem, but a fatigue problem…there’s a good reason why nobody makes springs out of Al alloys despite hardened 7075 being quite springy, but they do make springs out of Ti alloys ;-)
You haven’t even seen the failure mode or location yet. How can anyone have a solution. The “pickle fork” IS NOT FAILING OR CRACKING!!! The failure location is at the pickle fork, at STA 663.75 at stringer S-18 A. In fact, there is not even a picture of the failure anywhere. IT’S BEING PROTECTED AND KEPT OFF THE INTERNET.
Titanium alloy springs as used in helis MGB ends up with multiple sheared bolts. So its back to square one. You need to address and distribute the loads to more points.
The root of the problem lies in Boeings total philosophy for wing attachment. As Figure 2 shows, the wing flexes up in flight and the wings are attached to the fuselage by what in effect are hinges. To stop them flapping up completely, the pickle forks brace them against the fuselage. As the 737 range increase in size and load, the flexing of the forks results in higher stresses and fatigue, leading to cracking. The Airbus means of attachment of wings is entirely different. Both wings are one component with spars stretching all the way from one wing to the other. Being composite, the wings are extremely flexible and light, and the bending under load is carried by the wing structure itself, and the spars. The fuselage does not have to oppose the bending loads, and the fuselage just sits on the wing centre section and is lightly bolted in place. Simples!
If we’re going to armchair engineer, I’ll have a go. I’m not a mechanical engineer either, so this is what I can say with my limited knowledge…
Change materials? This part, being as critical as it is, would have been simulated to death. On top of that, this isn’t the new active suspension in the patent, its the “old” way, so it probably wasn’t even redesigned from the “old” 737s. So its very likely that beyond the simulations, decades of real world data likely exists. To recommend a change in materials is to say there is a design flaw in the part. I find that unlikely….
So what then? Well, even in the article they mention a probable “manufacturing issue”. What could that be? Bad metal, improperly heat treated metal, improperly stressed metal in manufacturing, improperly stressed metal in assembly, improperly stressed raw material in transit (used as a shelf), or similar. 1 stress event near the ultimate strength, but still in the elastic zone will drastically reduce fatigue strength if not stress relieved. Stress relief usually changes dimensions of parts, which then requires a finishing step (which will also induce some stress) to get it within tolerance. I honestly don’t know if they do this for aircraft aluminum parts. I wouldn’t think so though. In my limited experience with machining, I’ve not seen this called for in aluminum. (maybe a real mechanical/aerospace engineer will chime in, or at least a machinist who has made these parts)
Could there be a design flaw? Of course. Someone could have been off a decimal place for sure. Could a whole design review be off? would people have noticed a much smaller part in a design review? All good questions, but we’re doing armchair work here, so I’m going to go with a manufacturing issue rather than a design issue. There should have been enough eyes on it to catch a massive design flaw.
Your thinking is outstanding.
“There should have been enough eyes on it to catch a massive design flaw.”.. Except, Boeing is suffering from late stage capitalism corporate mentality manifesting itself in short term “contract” engineers rather than full on long term employees as a cost saving protocol. There’s no historical or tribal knowledge to fall back on. Experiences of past success / failures are lost in the past. Removing any mention of the redesigned MCAS system in pilot manual is case and point.
I worked in 737-300 / 400 overhaul in the 00’s and we had Spar Cracks. Big deal, lots of grounded AC. Fix was beefier spar. My (non-engineer) bet is this beefier Spar was incorporated into the NG without fully examining how the stress / loads would transfer without the spar taking the brunt of it. OEMs usually address issues in fire teams not going to clean sheet reengineering. Just my 35 year aviation management guess.
SOLUTION!!!??? First show me a picture of the exact location and the exact “crack” PLEASE. THEN I’LL SHOW YOU THE SOLUTION.
To the author of this comment, I applaud your reasoning and critical thinking with such limited available information. There is one issue I would offer as food for thought, though, and that is regarding design issue and its oversight….I am always reminded of the Hubble telescope fiasco and I can only imagine how many reviewed that only to find that one group was working in metric, and one in English and no one caught it until after the fact. This is by no means a criticism of you and your thinking but as long as our fellow humans are involved, anything is possible!
Your analysis failed at the word “simulated”.
As an engineer with 35 years of experience, I can say with 100% certainty that simulations do not reflect reality 100% of the time. Simulations are always slanted by the programmer.
was the material Kobe related aluminum
Hey quick question. What facility did you work at? who makes the pickle fork does boeing outsource the manufacturing ?
The pickleforks that had the cracks were previously made by a different manufacturer than who makes them now. The repairs and current pickleforks are being made at LMI Aerospace in Washington MO. The issue was the holes that are reamed to a certain size were oversize causing the pins that go through them to take the impact and hit the sides of this hole. After numerous landings the pin and hole isue caused stress fractures. The fix was to remake them with correct sizing. I was one of the main guys who rebuilt the new replacement pickleforks at the Washington Plant. I have a distinct experience with these and all the information needed.
The 737 MAX engines are twice the weight of the 737 NG. Was this new weight considered?
Not even close 800 pounds heavier than the CFM56-7b
Can you show me a “crack”? I read it is at STA 663.75 and stringer S-18 A, but i cannot find a difinitive drawing or sketch of this location or any picture of any failure. The public need the data of FAILURE MODE AND LOCATION.
NG != MAX
As previously noted… 737NG != 737MAX.
But more to the point… engine weight is borne by the pylon hung under the wing, so the pylon has to be beefier. But the wing is not suspended from the fuselage – the wing carries the fuselage. The fuselage is the load, not the wing.
Until the plane lands…….Heavier engines, a few harder than usual landings…………
Even on the ground the fuselage is a load tansmitted to the undercarriage by the wing
Unless the aircraft is sitiing in a parking lot for an extended period of time due to the FAA grounding said aircraft. On the ground the wing becomes the load.
Not on a 737. Take a look at a head-on photo of a parked 737. The landing gear struts are at least 2-3 feet outside of the fuselage footprint — in the wings.
Not just weight but torque of the engine. We re-engined our fleet due to lack of compressor blades. A slightly smaller engine but more thrust we had to de-tune it for obvious airframe related stresses. Guess what happened later on… cracks appeared on spars.
Well, it looks like Boeing and the FAA are serious about failure reports again.
And this is why they have schedule inspections. Stop big dealing something don’t understand especially when you don’t have any fking clue.
Didn’t I say “the painstaking system of maintenance checks that underpins the aviation industry has worked as intended.”? The article is about what a pickle fork is, because like a lot of readers I had never heard of one until I saw the story.
Another historical use of the term was two-tined wedges used to separate suspension elements on automobiles. They were shaped like short tuning forks but where tuning forks have uniform tines, these tapered towards the end. They were placed between two metal elements held together by one being pressed into a rubber or polyurethane bushing in the other, and then hammered on the end to separate the parts. (Particularly used for anti-sway bars and the joints used to attach the control arm to the steering rack.) This may be only a rural American usage of the prhase.
You can go to any AutoZone and rent or buy the pickle fork smellsofbikes is referring to.
Looks like tuning forks. Behave like tuning forks. That would mean vibrations would be amplified at these areas. Apart from load stress, has vibration stress been factored at these areas? I got a funny feeling the answer is no.
Ps..coming from experience on fixed and rotary wings.
It is a big deal because pickle forks are designed to last the lifetime of a plane, but they’re found to be severely cracking after only about 1/3 through it. Needless to say a failure of a part that helps attach the fuselage to the wing could result in a catastrophic tragedy if happens while in flight. So, yes, it is a big deal.
They are not severely cracking, The crack is a small crack going from one fastener hole to the other and would probably fly the life of the airplane with it. It basically self stop drilled itself and more than likely will not get any bigger. Boeing will come up with a fix and the force will be back in balance.
Was it designed to crack? No. Any crack in a main support part is serious. A crack between bolt holes transfers the load to the next area between holes. Will it fail? who knows. Even very strong metals will fail under fatigue conditions like wing flexing where the load is applied and removed thousands of times during every flight.
Its not supposed to crack in the first place. So yes its a big deal considering the fact it was discovered not at scheduled maint but by a fluke because of a conversion program. This is of grave concern for the Max too because this is indicating the same is going to happen at lesser cycles due to the adverse difference in engine configuration.
Calm down dear. As the article itself says, its purpose is to highlight and understand better something that many may not have had a clue about. Nowhere in the article does the author say anything out of place for their position.
While being converted to a freighter isn’t what I would call “schedule inspections”.
News reports say this was discovered during freighter conversions. Does that qualify as a “schedule inspection”?
No its not schedule maint. Sch maint would not have detected it ie D-sch as its not a complete strip down. This particular case was a complete strip down for conversion. Therefore better access for detailed inspection. Even a boroscopic check would be difficult due to lack of accessibility. Unless you had prior knowledge of the exact area to check. But there was no prior knowledge of cracks in that area. So there you have it. I leave that to your critical thoughts.
My wife and I are due to fly on the Boeing 737 700 NG on October 15th and at the moment they are being inspected here in Canada. Will they be safe to fly on or are we putting our lives in the hands of large Billionaires who put money first! We’re very concerned and losing trust in Boeing.
If you fly on a plane that gets this inspection, you should be safe. Beyond that no one can say. Do keep in mind, however, that no 737NG has crashed as a result of this problem.
What caused the crashes of the 737NGs then ?
737NG crashes. Some due to inclement weather, pilot error, a few engine failures.
737NG and 737MAX are different planes.
Pat, I have the same concern. I am trying to make areservation for Oct 23 and can only find reservations on 737-800s. How do iknow if the planes I am flying on are safe?
You get on the plane assuming it is safe. If it isn’t safe, you get a nice amusement ride right before your permanent nap.
Your taking your life in your hands not because your getting on a 737 but because you’ll be traveling to and from airports surrounded by idiots who can’t drive in vehicles that perhaps haven’t been as well maintained as the 737 you’ll be travelling on.
We have been flying a lot during our life (79). Las time Europe to New Zealand and back. Never did flying worry us the least. Have a mechanical background. For whatever reason I have decided not to fly anymore. The industry is too busy and hectic. Overall we see a decline in the quality of engineers. Like someone commented above, no long term commitment. Let’s face it, we are running out of excellent people. There are not enough of them. This we can blame on education at primary schools as well as Universities.
Dont know where you get your data from, but after reading the information by Wretch… I’d say heavy landings are the main cause of the crashes. Its not stupid to say that on a heavy landing, this part could fail. Looking at its history the planes didn’t fall out of the Sky like the MAX, but it is directly responsible for almost as many deaths as the MAX. Some will speculate the odds based over crashes and the number of deaths, the vast majority had no casualties as they were on the ground. One of the major causes of casualties was the collision over Brazil… How a sparrow can take out an eagle?
ive bet my life on many a boeing product and im still here. and im going to be on a 737 again in a couple weeks. im not concerned, mostly because alaska airlines hasnt updated their planes in years and are still flying the same old workhorses they always have. also their shiny new planes do the vacation routes and not the puddle jumps actual alaskans like me use.
lol turns out its an ng, a 737-700.
I am a commercial airline mechanic working in a heavy check environment. We do this type of inspection every day that is why we find these discrepancies cost is never a factor if a part is out of limits it corrected. A heavy check, c or d check, are in most cases are performed every 3 to 5 years. They cost over a million dollars in parts and labor. They take 30 to 90 days to complete in our case we apply 600 man hours a day
. The inspection processes are meticulous and detailed.
Look bottom line is my family flys on the aircraft i service and i would never trade my families safety for a dollar
What is your airline?
I’d consider flying on it.
Mile per mile, statistic are that your personal vehicle is far less safe than flying. The reason folks fear aircraft so much is that there are usually no survivors, unlike cars.
And that the majority of car accidents involve the driver and (if they have passengers), passengers personally known to them. Not hundreds of randoms who got on the plane.
Plus most accidents are due to idiot (drunk etc) drivers, which is a variable most of us control by not being idiots, so the average safety for most people is far higher. Whereas in a plane you can’t control any relevant variables.
I used to work in the structural integrity field. Part of aircraft design involves accepting that cracks happen and ensuring that they grow slowly enough to be spotted at the normal inspection intervals. Some parts that are very hard to inspect have to be safe with cracks in the foot+ range. And some parts of the wings can be allowed a short crack rating as the fuel leaks out and crack detects for you.
Thanks for the info. Very interesting.
Hey! Boeing only laid off *half* of its engineers to slash costs and appease Wall Street. What could possibly go wrong? https://newrepublic.com/article/154944/boeing-737-max-investigation-indonesia-lion-air-ethiopian-airlines-managerial-revolution
Why can’t Boeing just leave it as is, and schedule a pickle fork replacement after x flight hours?
The problem is that they’re supposed to last the life of the plane (i.e., they’re not supposed to be replaced). If I’ve understood the article correctly, they can be replaced, but it’s a huge task. There are 4 of them per plane and they’re about 25% the circumference of the fuselage (i.e., they’re not small parts). Plus, everybody involved aren’t currently sure what’s causing the cracking (e.g., manufacturing fault, design defect, installation/assembly issue), so they probably want to know the full extent of the issue before determining a corrective course of action. I’m guessing they’re inspecting all 737NG’s now and grounding all that have developed this crack.
Because if something critical isn’t behaving as it should, you need to understand why. Besides, its a big job to replace them, so they’d rather not do it too often.
My wife and I just canceled our flights on the 737 700 NG, from Halifax, Nova Scotia 🇨🇦 to Toronto 🇨🇦 , then on to DR Punta Cana. We rather be safe! than sorry!! Besides the FAA will stand behind Boeing in my opinion.
Please watch I am a quality professional with over 36+ years
Collusion Kills “BOEING” Quality Auth. Daryl Guberman Explains-Why G-PMC Should Be Required!
https://youtu.be/u2Ilb9YrrXM
Learn PowerPoint please.
I used to work for McDonnell Douglas documenting aircraft builds/tests…. Along with pressurization test of fuselage done to all planes with the potential of rivets shooting out faster than bullets, the most amazing thing I saw was the wing stress tests. Not sure if their planes had “pickles”, although I heard much discussion on the brilliant idea. The main wing test involved attaching cables to the wing tips and with powerful winches and rigging, the wing tips would be pulled towards each other . The wings had enough flex and Strength that the wingtips would come within Four feet of each other and Not break! One time out of maybe twenty did we hear a large cracking sound and test halted for teardown. Wings do not break easily!
I’ve been working on a Dassault Falcon jet after college. One day we had a picture going from e-mail to e-mail, with the rear bulkhead in two parts, separated by a crack… There clearly was a problem with design on that part.
But it appeared the crack appeared on the mechanical test plane, the one which is bring to a great hall, and pulled-on day and night to simulate its whole life. Here they pull on the wings, they put the fuselage under pressure, etc. At the time the problem arose, this particular plane had been trough 60000 simulated flights, three times what an aircraft is given to do on commercial service.
Even if hearing about cracks on any part (and furthermore if it’s a sensitive part !) can be quite alarming, when an aircraft starts its commercial service it has already been trough at least a life of flight on test. Part brakes on test long before they do in real life, and are modified accordingly.
By the way, there are case when parts don’t break on tests while doing it in real life. That was the case with British Airways Concordes losing their fins, while Air France’s ones didn’t. Fin paint was in cause here, and now we take care of sensitive parts color. That’s why wings are grey.
Make sure you use Aircraft paint.
Don’t want to burn up the paint
and have a fire.
I would bet that Boeing shareholders would only travel on their private jets or lush cars, rather than a 737 NG.
Boeing shareholder here. I prefer to travel South West (nothing but 737s).
Cripes the FUD and hate here for anyone who owns stocks or has money. And yes, I do own Boeing shares, it’s not that difficult to invest in companies and save for your future. Yet, for some reason, people like to demonize and say only “the rich” or “billionaires” can do it. Notice to you ignorants, over half the people in the US own stocks. Cut the BS about how “only the rich” benefit from the stock market.
“Boeing shareholders”
If you have a diversified portfolio for your retirement, (or the company you work for), then you probably are a
“Boeing shareholder”
I’m happy for you making the right decisions for your future. I can not speak on the behalf of anyone! only voice my own opinion and it’s called Freedom Of Speech! I respect your Freedom Of Speech!
“Pickle forks” have been used for a very long time by those of us who work on automobile suspension and steering systems–for ball joint and tie-rod-end removal. A good representative picture (they come in all sizes) can be found at
https://www.harborfreight.com/16-in-ball-joint-separator-63420.html
Probably wouldn’t pass FAA certifications, though–much too tough; don’t flex enough…
I wonder if there are any marginally reputable sources out there that claim such an extreme increase in engine weight, e.g. perhaps the same ones that try to pin the requirement of MCAS on center of gravity/center of thrust/total thrust changes (from all of the information available to me, it’s dynamic center of lift as AoA increases above all else) and/or the plane being inherently unstable (it’s not).
I do sincerely hope that this unfortunate situation with Pickle Fork/cracking is resolved! The 737 NG is a daily foot print on the international platform. Mechanical Engineers will come up with a solution and apply it and put this be hind us. I’m rewinding the tape regarding my previous comments and have to be positive! I can’t go through life always worrying especially things I don’t have any professional knowledge of. A shout out to the experienced engineers from the Aero Space and Defence and all Engineers in all occupations, I’m guessing there’s a lot of challenges and hills to climb, but with the intelligent minds and team work, this will prevail with success!!!
Aren’t we overlooking an obvious short-term fix? A temporary Airworthiness Directive to stop serving pickles in-flight will do the trick. Then it doesn’t matter what condition the forks are in. Also, who are these neanderthals skewering pickles hard enough to fatigue and crack the forks?
Its not just the forks. Boing have a really serious problem and slowly the things reveal thenselves .
https://www.youtube.com/watch?v=U6jhp3y1l5M
You remember this video ? those who do know what i mean .
Those wo dont know , go watch the video…
Its more than relevant today after all those troubles with Max and the fact that Ng generation gets older and
faults will slowly reveal themselves .
This is the link i believe: https://www.youtube.com/watch?v=rvkEpstd9os
Any updates on the inspections of the Pickle Fork?
The MAX engines are not significantly heavier. They ARE significantly larger in diameter and circumference (larger fans). Because you can’t make the landing gear longer without a major re-design, in order to keep the larger engines off the ground they have to move them forward, so that they could mount them higher. It’s the moving forward that altered the lift of the wing, which could lead to a stall situation.
Moving the higher-powered engines forward has made the aircraft longditudally unstable in the climb. The empennage is not large enough to damp out the oscillations. Making the elevator larger would have required complete recertification, so Boeing colluded with the FAA to implement a software “fix” which breaks all the usual requirements for commercial aircraft to be inherently stable in all flight modes. This aspect has still been side-stepped. The newer software may (or may not) be more reliable, but it still does not make the airframe inherently stable.
I should like to know if this problem exists in the Poseidon – Boeing 737 maritime reconnaissance
As far as i know, there is a parachute in every military aircraft… Just sayin, :-)
But military aircraft are either fighters, with small crews, or freight or bombers, with small crews. Itmakes sense to give them training in parachutes.
I also assume that most military emergencies are from being hit.
But airline planes have small crews and a large number of passengers. You can’t train the passengers ahead of time, and dealing with that many untrained people in an emergency will be dangerous. All but thecrarest airline emergency is from airplane problems.
So airlines deal with emergencies differently.
Military aircraft have parachutes because of the cost of training pilots (they can build another airplane, but in war time, they can’t train pilots fast enough), Airliners don’t, Airlines accept a loss ratio, indemnified by Insurers purses, they put a dollar value to life whether the person is a senator, president, or baby, the primary industry (aircraft manufacturers) are the only ones who can change the dollar value on someones life, money would change everything in the manufacture of an aircraft that carries people, unless the industry is moved to making a life matter then statistics wont change, their just statistics………profit, loss, statistics.
In the mean time, we have an old design, with turbojets, and now we want hi-bypass, (money again) new design ? no, but lets not lose sight of the ball here, pickle fork ? new run on old, if not tried and true data ? normal cause and effect engineering in the field, they know where the forces are applied, and it’s not an issue in a aircraft design that’s how old? to make a article about a potential risk in the pickle fork is just sticking the knife in to something that may or may not die a death in the public forum any way. and maybe those parachutes……….