To grind or not to grind? What a question! It all depends on what you’re really trying to show, and in the case of welded joints, I often want to prove the integrity of the weld.
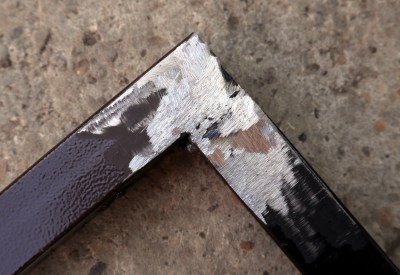
Recently, I wrote a piece in which I talked about my cheap inverter welder and others like it. As part of it I did a lower-current weld on a piece of thin tube and before snapping a picture of the weld I ground it back flat. It turns out that some people prefer to see a picture of the weld bead instead — the neatness of the external appearance of the weld — to allow judgment on its quality. Oddly I believe the exact opposite, that the quality of my weld can only be judged by a closer look inside it, and it’s this point I’d like to explore.
What Lies Beneath
A weld is a balance of several different factors to use an arc to melt a steel filler into the gap between two pieces of steel, shielded from the oxidation by some kind of non-reactive cover. In the case of my stick welder the cover is the molten and gaseous phases of the flux covering the welding rod as they are heated by the arc, while in the case of a MIG welder it is whatever shield gas the operator is using. As the operator I have control of a few factors such as the current setting on the welder, the size of the arc I draw, and the speed at which I move it across the metal. These affect the temperature and thickness of the molten metal and the integrity of the shield, which will in turn affect the metallurgy of the resulting weld. It may be brittle, it may have inclusions of flux, it may have internal tensions that could cause cracks, or it may not have proper adhesion to the pieces of metal it’s trying to join.
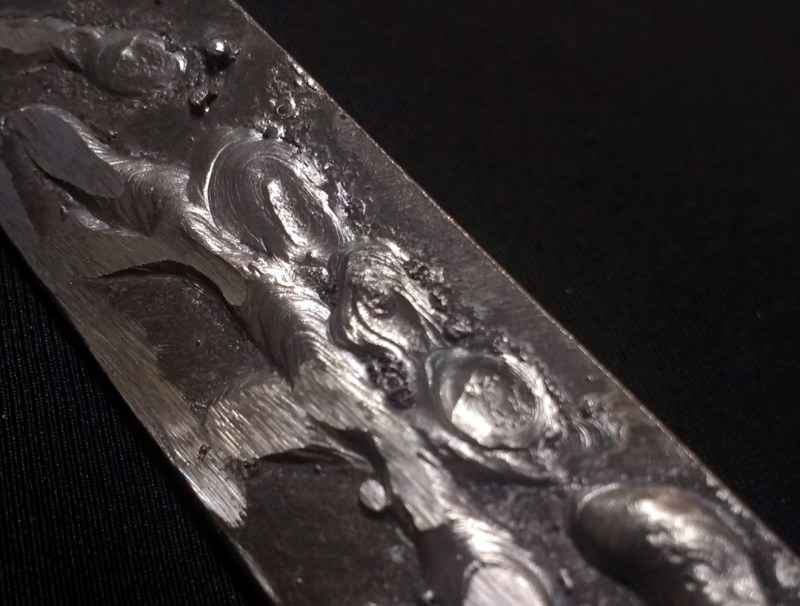
Among Hackaday’s readership will be a few elite-level metalworkers whose welds are works of art. I may sometimes approach that level of skill with soldering, but when it comes to welding I am not one of them. I suspect I share this with many readers, while I have a basic handle on the job I am still pretty inept. I’ll get the welding current wrong, I’ll sometimes get my arc length wrong, and I’ll move across the work at the wrong speed. Despite that, I will often manage to produce welds with a creditable outward appearance once I’ve knocked off the flux, but which may still conceal fundamental flaws beneath them.
Many people who have received professional instruction on welding will have had their teachers devote countless hours in the pursuit of drawing a perfect bead. It’s an entirely appropriate skill to acquire because by repetition it teaches those skills of maintaining arc length and cover integrity that are the key to producing consistently good welds, but it shouldn’t lead to the conclusion that it is the bead that’s important rather than those arc skills. An inept welder can produce a surprisingly good-looking bead that conceals a less pretty weld, I should know this because I have done it.
Do You Have Ten Thousand Hours?
I thus make full use of the angle grinder when I weld, though I don’t always grind my welds as far back as I did with that 1mm tube. The sight of good metal exposed under that bead is the confirmation that the weld is a good one, and if I see any anomalies it’s my cue to take it back all the way and try again. If you take a look again at the tube you’ll see just such a flaw in the join, if it wasn’t simply a test to see whether such a thin piece of stock was possible with that welder I’d be doing it again.
I think professional welders would universally consider this welding gear a toy — as an Easy-bake oven is to a professional baker. So for you pros out there, let’s see those pristine beads, for those weekend welders, by all means, grind them down and show us what they’re really made of.
Man welding header image: Jorge Barrios [Public domain].
Ha. I think my welds are perhaps a touch better than yours, but not by much. I still have a lot to learn.
Wasn’t there a retraction of the ten thousand hours statistic? I kind of remembering reading somewhere that it was totally made up, not sure. Well I mean of course it was—too nice and round a number to be true, but there was more elaboration on why setting a time limit for practice isn’t actually useful to strategize and/or achieve mastery, and in fact it ends up needlessly discouraging people. I’ll try to find it again, it was interesting.
It’s not that the 10,000 hours (or so) metric is wrong per se but that it’s too simplistic. To obtain mastery of a thing (which is completely objective!) depends entirely on the skill, how many people practice it, how long it has been around, individual ability, and so on. Further, those thousands of hours only lead to mastery when combined with intentional improvement, experimentation, and usually coaching. And then finally, most of the world does not have the social or monetary resources to put 10,000 hours into any single pursuit, regardless of the rest.
Welded for 35 years, a good bit of that time MIG Production welding Aluminium, I used a 120 lb spool of 1/16 wire, 5356 alloy a day and I can’t say I had 10,000 hours of welding time.
at 20 hours a week it only takes 9 and a half years to get 10,000 hours. i would bet you did.
I am a welder and even on the job you probably don’t spend 20 hours a week welding. I sometimes go 20- 30 hours just fitting up and tacking pieces together before spending 5 hours welding out. 10,000 hours seems a bit excessive. I’ve been welding several different types of metal for 5 years now. Im proficient but it takes a need to constantly improve every bead and if your not getting better quality welds then your not trying hard enough. Practice makes perfect
The 10,000 hours rule was from Malcolm Gladwell’s book “Outliers”, where he studied masters (in a lot of fields) and what it took to attain that mastery. He uses historical examples, as well as modern ones (Tiger Woods, Beatles, and so on).
Mastery, in the context of the book, means “world class”, which means roughly top-10 in the entire world. “Mastery” in any regular sense of the word meaning “very good” would take considerably less than the 10,000 hours.
Gladwell is also careful to point out that it has to be the *right* 10,000 hours – it’s 10,000 hours of constant challenge that’s just outside of your comfort zone. There are *lots* of people in dead-end jobs who have put 10,000 hours into something – but are not very good at it because they don’t challenge themselves for constant improvement.
One way to do this is to always have a teacher: even though you could be very good at something, an outside perspective can often point out flaws and areas of improvement that you wouldn’t notice yourself. Tiger Woods still takes lessons from a golf pro, even though he’s probably much better.
Assuming a full-time job of 2,000 hours a year (50 weeks x 40 hours/week), most masters spend 20 hours per week working on their vocation, which works out to about 10 years of side-study to become world famous at something.
That seems to be the rule for mastery: someone obsessively interested in something (violin, writing, chess, whatnot) spending all of their spare time learning to do something – and it takes 10 or so years for this to pay off. See: “On Writing” by Stephen King. He did exactly that.
I have a real hard time with this number. Some people are just predisposed to be good at some things. It is nice to know that I should be able to get good at something should I put 1K hours into it, and I may be in the minority of thinking there are few things that I could not do, if I were willing to spend the time. However I have friends who very naturally take to things. I have a friend who can do the most beautiful work with my mig welder. This same person is also very artistic, and seems to have a very good concept of control. He can also make nicer cuts freehand with my plasma cutter than I can make with a template to follow. I have friends who are just amazing musicians and again, this seems to come very naturally to them. My work is cruder, but I do not let that stop me. The more you do something the better you get at it, and even more so if you look at why something did not go so well and how to get around that in the future, But at the same time, I believe that some people just have natural talents.
BTW, is regard to the OP, I am a fan of grinding welds. I find it hard to tell how far below the surface the weld has penetrated and how tight the joint is without grinding the surface bump off. IMHO the weld is what is below the surface. The metal you can see on the surface might as well be epoxy.
I started welding with a buzz box at 10 . Got a new one for Christmas at 12.: Welded 12 and 16 inch well casing (thousands of feet) when I was 17-20. My boss told me I was the best welder he ever saw. I still weld most days as I own a general repair shop, I still don’t grind much, and the last 8 or 9 thousand hours my skill did not improve much. I could out weld most people the first few hours. Some people can weld and some can’t. My son (32) is the only person I know who can outweld me. He can see much better than me. 10000 hours means nothing, except you probably want be able to see by then. You keep grinding.
The book tells the anecdote of The Beatles playing in Hamburg for 10,000 hours before they got famous.
One of the Beatles members read the book and pointed out that there were many more bands who did the exact same thing, playing in clubs and pubs night after night, and never got a break.
There’s this thing called kinesthetic intelligence – it’s a property shared by people who become masters of musical instruments, or who learn to weld like it was walking to them. What is known of intelligence in general is that on average, 80% is explained by heritance and 20% by education/training. If you don’t have it, training for 10,000 hours won’t make you a master. If you have it good, a thousand hours will get you there.
The Beatles may be a poor example. Yes, they were great musicians, but as a band they had four members that could write and sing (each one had a solo career that would be the envy of any starving artist).
So just playing pubs for 10,000 hours and getting good at performing is not enough for commercial success. As you pointed out, other bands were “equally good” and never made it. It was the writing that made the difference, and in their case, it was a rare combination of having multiple writing talent in one band.
You seem to be one of those people with a natural aptitude for welding. I am truly very happy for you. I wish I had as clear an idea of what was going on under the bead as you do. I don’t. Grinding the bead off lets me know if I am truly welding base metal together or just tacking the parts with a bead stuck to the top surface. I wish I had your talent.
That being said, I seem to detect a bit of rudeness in your last comment. Please do try and understand that there are a lot of people who lack your skills.
Welded over 40 years my old time boss always said it takes 6 years to train someone. If you figure 40 hours a week plus overtime equals about 2000 hours a year minus some here or there 10,000 would be about correct
A grinder and paint make a welder what he aint!
Ah, this article is very timely! I actually just finished building a welding cart for a new-to-me MIG welder. I figured it would serve two fold:
– Be a good thing to practice on – especially welding 1″ square tubing.
– Make it easier to move the welder around in the garage.
Some of the welds turned out nice, while others… were not so nice. I can totally understand what you mean about a weld looking good on the surface, but being not so good inside. Toward the end I was running low on gas, and a few welds had some porosity, which wasn’t apparent from looking at the outside of the weld. It was only after I ground them back (to make things fit better) that I noticed some bubbles in the weld.
In a recent welding video I watched on YouTube, the person said that it was possible to make a poor quality MIG weld and still have it look good (but be structurally unsound). The person said the same was not true of TIG welding – that if it looked good, it was probably good. I’ve never heard this anywhere else. I’d be curious to know if anyone could back up this claim.
As for the “10,000 hours” thing, I’ve heard another similar saying: “Practice does not make perfect. Perfect practice makes perfect”. If you keep practicing doing something the wrong way, no matter how much you practice, things won’t improve.
As an amateur TIG welder I can assure you it is possible to make good-looking TIG welds that suck, mostly because (in my experience) they’re way too shallow.
I think you may have misunderstood what This Old Tony was trying to convey in that video. I think he was saying that it’s very often easier to have a MIG that looks better than it actually is than with TIG. There are a number of reasons for this, but a lot of it comes down to brute force vs. finesse. TIG welding involves a lot more control than MIG, so a superficially nice looking (especially to an inexperienced eye) TIG weld is often hiding fewer sins than a comparable MIG. That doesn’t mean that poor technique and/or inexperience will leave you with bad TIG welds that look pretty, more that bad TIG welding is often more apparent, since you don’t have wire feed concealing poor puddle control and filler use. Also, a lot of people (I suspect most, really) learn MIG, stick, and/or oxyacetylene welding first, so they tend to come to TIG welding with some basic experience in surface prep, work holding, and overall approach that they may benefit from.
Just my $.02, refunds accepted.
Grinding your welds depends on the purpose of the project you are building. If your building a frame to mount something, will the welds be in the way? If you grind one weld, might as well grind them all. Lets face it, smooth always looks better. As far as 10k hrs? Depends on the welder. Its an art. A skill that not everyone can pick up. Its something a person must really enjoy to be good at it. I have asked people a few times if they ever considered a different trade. Keep going. Never give up.
I have a titanium bike frame…in the early days the welders of titanium frames had to be poached from the aerospace industry and they don’t grind welds they inspect them with penetrating UV dye, X-ray, and eddy-current methods. A little too much for a bike frame but their experience transfers, but the welds themselves are a thing of beauty.
with a little practice most anybody can make a weld that is half as strong as a pro weld. Just add more bracing.
And appearance is not always a good indicator. Can look sloppy on top but lower penetration is good
“Can look sloppy on top but lower penetration is good”
Standard friday night.
I once knew a welding engineer who told me he was examining welds on a nuclear pressure vessel. The beads looked lovely–until he tapped them with a welding hammer and they fell off. The bead had been faked with putty. The underlying welds were there but the final bead was faked by a rushed weldor. Many heads rolled…
Having been an NDT technician in my younger days, I’ve x-rayed thousands of welds. I can tell you with certainty that there is poor correlation between outside appearance and internal quality. I’ve seen ugly looking welds that were essentially perfect internally and great looking welds that were terrible – inclusions. porosity, misalighment etc – when x-rayed.
I remember going to one site to inspect some field welding on a crane boom. It was rainy and humid (perfiect for porosity problems), difficult location to work in so the welder was stretching his ability to get the job done. The weld looked about as ugly on the outside as any I’d seen. It was essentially perfect when x-rayed.
I respect a good welder. It’s not easy to be consistent under changing weather and work conditions. Some can do it really well – hats off to them.
How do you spot hydrogen embrittlement with x-ray though? If it’s welded under wet conditions, with moisture in the air, wet sticks and everything, it’s going to be a time bomb because the hydrogen cracks don’t form until days later and you’ll easily miss them.
Please tell me they at least heated the bead up afterwards?
Looking at my old notes, hydrogen becomes a problem when there’s
1) tensile stress (in a crane, when loaded)
2) water or grease in the atmosphere, in the seam, in the welding stick, gas… etc.
3) rapid cooling rate and hardening in the HAZ that produces a brittle microstructure around the bead
That’s the hazard triangle that makes a nice “perfect” weld bead crack with an unspecified delay some time later. Sometimes years later. The welds can be annealed to diffuse the hydrogen and release the hardened microstructure, as long as you’re dealing with regular structural steel.
Wait time and load/pressure testing.
Appropriate material control and process monitoring are the key to avoiding the issue, but in critical structures, testing is a must. (load test cranes and hoists, hydro test boilers and pressure vessels, and so on)
Years ago, I was told by a boss: “I pay you to weld, not to grind!”. My response was that, no, he paid me to produce completed joints that met the requirements, and that the requirements were flush surface and uniform thickness, as well as passing NDT (radiography, in that case).
Then you get appearance requirements, that usually require grinding and often polishing.
Then there are issues with stress risers at the weld toes, even without undercut, and, in many materials, reduced material properties at the surface of the weld.
And then you have the buried defects, which often show with even a light grind.
For reference, welding has never been my primary career (originally EE/Comp E in semiconductor fab, back in the wet chem days), but has been a significant part of my career, and, at this time, one of my titles is weld supervisor/engineer for a company that does work under ABS, DNV, Lloyds, US navy, and several other marine classification organizations, as well as boiler and pressure vessel repair. Currently lapsed ASNT level 2. By the way: proper hydrostatic tests, load tests, and NDE save lives. Just saying.
A grinder and paint makes me the welder I ain’t.
Quote by the great AvE?
Yup. focus you….
I think he is at least a few decades too late to claim that phrase
Go home AvE, you’re drunk.
“Hey boss some of these things aren’t lining up and there are gaps-”
“Weld it, send it to paint”
True story
Leaving slag helps with weld strength!
Huh?
No, no it doesn’t.
The other 32% are really real – Source: Abe Lincoln’s Twitter
An informative write up over, but respectfully Jenny, 10,000 hours? Hyperbole shouldn’t have a place in technical forum. That figure is about 60 full time weeks. That could be a major discouragement to person considering welding as a career,because they enjoy welding at the DIY level. Best to stick to the facts as you know them in your area. For example a student in the US could enter a welding trade school and exit after six months certified to weld in in many if not most indudtries Of course, the learning and acquiring of experience doesn’t end at that six months. When a welder gets to close to perfect as possible their body is worn out, and they are forced to wrap up the leads that last time.
That’s an established fact on developing muscle memory
The only established fact is that Malcolm Gladwell is full of shit. He writes entertaining, plausibly sounding gibberish. Steven Pinker summed him up pretty well with “generalizations that are banal, obtuse or flat wrong,” and “cherry-picked anecdotes, post-hoc sophistry and false dichotomies”.
He knows the English language better than you!
Oh, please. https://en.wikipedia.org/wiki/Outliers_(book)
I do report it as a saying, not a fact.
In the race cars we build, we can’t grind welds on the cage. If you do, you fail tech as they cant tell how much of the tube material you removed. Could be paper thin.
This is what UT (ultrasonic testing) is for. Many specialty applications are stuck in the 1950’s with regard to NDT. After all, how can they tell if the weld actually has complete penetration from visual at the surface? Or if there are voids?
Just out of curiosity, what sort of things are needed to pass tech, with regards to welds on a tube frame?
It all depends on what the tube frame is doing. Is it going on a airplane or a dune buggy? All this talk.
Well, the original context was about race cars. What I’m really interested in building is a replicate of a concept car, but actually have it functional. I know there’s guys out there who build Dakar, King of Hammers, and Baja vehicles using tube steel frames. I imagine something like that, but not quite the same level of punishment. Ideally it’d be something that could still take a bit of roughhousing but not built to do 100 mph through the desert. From what I’ve seen, most guys will use DOM (drawn over mandrill) tubing, in various diameters. I realize that a lot of it comes down to the design, but even a good design will fail if the joins are terribly welded.
Name has to be bubba
I used to do rally driving in the UK (also did UK-based WRC event 4 times, 3 of which in my self-built car with a cage I welded myself). Tech/Scrutineering consisted of a visual inspection, and checking the certificate for the cage was present and correct. In the case of my first car, it was a manufacturer-made bolt-in cage, where all the welds were done by them. For my self-built car, I got the cage kit (weld-in cage) from Custom Cages, and fitted it myself. To get a certificate, I had to do a welding test piece, which was sent off to them and tested (x-ray and then a destructive pull test, I believe), which once passed they issued a certificate. I guess the inspection at the event is really just checking and passing the responsibility up the chain.
yeh, as show on th picture of the square tube once you start grinding it often doesn’t just flatten the weld but also thins the out the metal around the weld
Good to see a comment regarding X-Ray’ing welds as I was thinking that would be something novel to hack together, i.e. a X-Ray or a Gamma Ray inspection device. Would be rather challenging however, since I’d think those would need to be tracked and inspected by the D.O.E., A.E.C. or N.R.C.. I forget who does the inspection, though I do recall the Electron Capture Detector (ECD) for the G.C.’s needed to be inspected and I do recall the issue of a gamma inspection device for weld testing being a critical issue when they disappear anywhere in the World.
Still waiting on my Dinse connectors and Thyristor/Dual SCR I ordered to start construction of the what looks to be Miller Thunderbolt XL AC conversion as the first upgrade project. Then I’ll do the Twentieth Century upgrade and compare the two to determine which I want to keep since they have the variable shunt transformers that I’m still not sure if they’re called a variac like I initially was thinking and am wondering if there is a specific name for that type of variable transformer.
If anyone need’s DIAC’s I have like 46 or so extra I’m thinking I’m not going to need for a while. On the topic of the DIAC, I need to read into testing and the specifications, as I’ve never tested a DIAC before.
Interestingly, the grinder is probably more dangerous than welding unless you’re not wearing PPE.
I do prefer to grind my welds and inspect if there is a need for aesthetics or there is a more forged/machined look desired.
For the love of whatever you consider holy, please do not hack a gamma source…ever. ARP is a very shitty way to die!
X-ray tube hacks are fine by me, you need a fair bit of power to make it dangerous and the moment you cut it, no x-rays. Also the high voltage part puts a fair challenge on the project, forcing one to do research.
Although if you want to usefully x-ray a weld in metals you need a very high power x-ray source that will definitely be very dangerous on accidental, even if short, exposure.
Imaging plastic welds uses only a very low power source, but that is not the topic of the article.
Well, another thing to consider is that welds often penetrate less than you’d think, and grinding it down often means that you leave less (and often a paper thin) material to hold the pieces together, which means beveling becomes more important if you grind away the excess material.
Startebart got it right
Wings World Youtube channel just did a video regarding this topic when not beveling.
https://www.youtube.com/watch?v=V8fa-F2caLA
Yes, beveling is what I learned to do since you have to prep the weld area anyway if you want the best weld performance and I’m guessing to earn a journeyman’s card… the welds will be tested also.
Grinding is not good at times,it weakens your welding,welding is a skill/ art people mst see the outcome.so if u grind your welding I wouldn’t call you a welder but a grinder.
The most important part of welding is the prep and research you need to do before you start. If you don’t have a clean surface, if you don’t have the correct weld material, if you have not pretreated the metal the correct way, you’ll get flawed welds, even if your bead looks perfect. Give the weld time and stress, and you’ll see those flaws in cracks, corrosion, and breaks.
This is one area where flux-core wire-welding is better, albeit with cleanup after. It welds nicer dirtier.
I don’t think flux core is ever better
6010
I was wrong iment 6011, 6010 good for dirty rusty stuff too
Now I know you’re trolling with that comment.
Nothing welds nicer dirtier
If you building a rocket you are 100Percent correct. If you welding broken farm implements grind it a little , mostly for grooving out for better bead weld the crap out of it with 6013 rod and abuzz box
Reading this makes me very glad for all the excellent adhesives out there!
There is only one way to test a weld without super fancy tools like ultrasonics or x-ray. Break it open or cut a cross section. Then you can see how well your weld penetrated and whether the internal structure of the bead is acceptable. A grinder doesn’t always show bad penetration. It can be very enlightening to just weld up a bunch of scraps and destructively test them.
yes a few years ago i started rebuilding a VW Kombi which was full of rust and needed lots of welding so I bought a MIg and enrolled in a welding course – the only course I could get into was structual welding – 10mm was a bit bigger than the .9mm I was going to be welding on the Kombi :lol:
Nearly every weld we made was tested to destruction in a press. It became quiet evident when your welds wernt up to scratch.
If someone else welded it I might be worried about penitration. When I weld ,I set wirespeed and heat right ,weld with penitration as my only absolute must. Staying too long may overheat, so I don’t. Weld usually looks good but that is last concern. My stuff don’t break. 650 feet of steel 16 inch casing held up by 2 4 inch ears welded on the sides, better get Penitration
Well sir I have been at it along time….you have what robots don’t….talent,,self pride and man quality…good jib sir…10.000 hrs…lol..i know I surpassed that..but still have walk away days..do what you do..if you gotta grind it,,to hide the ugly..then it’s a bad weld..but let it be pretty..i like pretty..lol..
Grind it to shine it ..☺ definitely you will get a fine finish.
The 10,000 hours stat is obviously too round, but it equates to about 5 years doing something full-time, which isn’t a bad estimate on how long it takes to get really good at a job.
I see how it could be a discouragement, but I think it’s also an encouragement for those new to a job who don’t seem to be good at it after a few months – of course not; the pros around you have done this for years, you shouldn’t expect to be as good as them immediately.
But as others point out, some people have a disposition towards some skills, or have transferable skills they’ve learnt elsewhere – e.g. artists can often pick up a new medium very fast as they’ve got the creativity and hand-eye skills already.
I’ve been a welder fabricator for longer than I want to remember and for the last 17 years of that time doing mostly tig welding. Since I do a lot of ornamental stainless steel work that requires invisible splice and corner connections I have to comment on your grinding that you did on the first picture that I saw here. When grinding a weld joint where the pieces are flush with each other it’s best to not even touch the surface on each side of the weld with the grinding disc because that is the level you want to finish with. If your grinding gouges the finish surface you will have to take the entire surface around the weld down to get it to look good and that means more weld and surrounding metal is removed weakening the connectiono. Once the weld is taken down close to the finish surface great care needs to be taken to finish the grind. If it’s critical for the joint to be perfect I switch to a 5” 3M roll loc disc to blend it down and then a scotchbrite disc to finish polishing the joint. I hope someone out there can benefit from this advice.
It doesn’t take 10,000 hours to master welding, most people can learn with a few short weeks of practice. If a weld looks bad, it is bad and should be ground out and rewelded. A weld looks pretty because the welder used the right filler, the right amperage, and the right feed speed. Welding isn’t just about skill, it’s also knowing what you’re doing.
Heh….
Reading the above gave many smiles for the “bigger the blob the better the job” attitudes, and icing was then “grind it down to make it pretty.” . Definitely hackers “getting ‘er done!”
Hi Jenny. The complaint that in the first article you didn’t post weld pictures as well as those from after grinding was that for n00bs like me, we’re still seeking basic guidance… and seeing the raw weld from a cheap inverter welder in the hands of someone with your experience would have been helpful.
Of course grinding reveals joint quality and makes for a nicer finished product.
Anyone out there who wants to get better at welding should check out Jody Collier over at “Welding Tips and Tricks” – his you tube videos are some of the best at explaining welding, especially TIG processes.
He will explain how to practice welding, then grind or cross section your welds and “acid test” them – which is one of the best ways to check for weld penetration outside of expensive x-ray equipment.
Of course you wouldn’t want to do this to a production piece. But once you know how to weld, you don’t need to do destructive testing that often anyway, and if you’re doing jobs that require welding inspection, they’d be x-raying them.
A nice weld bead is indeed indicative of a quality weld job- because a bad weld is not going to leave a good bead… And while it is possible to lay down a “nice looking bead” on a surface with little penetration, there are signs in that bead that will be a dead give away of a poor quality weld if you know what to look for. Like solder joints, there are parts of a weld joint, and unless all those parts are right, the overall bead is “bad”
I think Jenny is trying to explain away grinding down her welds as more of an aesthetic thing. Which is legit, in welding, say furniture or things you want to paint and give a seamless look, grinding the bead away and filling low spots with things like “bondo” is an acceptable practice – so long as the welds have enough penetration and structural strength if the joint is not compromised- a proper weld will almost always be stronger than the surrounding material (given the material itself and other factors). But looking at Jenny’s welds. It is obvious she needs some practice. But you’d be surprised how well some people take to welding and pick it up rather quickly if they just keep at it.
I took welding YEARS ago in vocational school and was going to be a professional welder, but the health aspect, like all the the “black snot” and general filth of welding all day in dangerous locations was not for me. I can stick weld with the best of them, MIG is pretty much child’s play, but TIG is something I’m still learning – it is what separates “welders” from “masters”
Those that can, weld. Those that can’t, grind. Here in Ontario welding structural stuff and pressure vessels requires a welding licence. An inspector can come onto the job site at any time, ask to see your licence and then require you to redo your practical test again on the spot. You don’t get to grind it so it looks better or hides any faults.
The application of a weld should suit the purpose if it’s form you’re looking for grind it to Grove it gap it if it suits but always aim to improve all aspects of quality in every way possible every time you lay a bead even if you have no experience as they say if a thing is worth doing it’s worth doing right
i have said for years that “you don’t know how to weld until you have welded your weight in rods”.
Grinding stuff can be very important. Google salesforce center cracks to find out.
After the thing was built, big cracks were found in two major support beams. After a lengthy investigation it was found that on the beams welding access holes had been cut with an oxy-acetylene torch, but only two developed cracks.
What was different about the two beams? On them the access holes had been cut *before* the end of the beam was welded in place. On all the others the access holes were cut *after* the end was welded. It was also determined that the cracks would not have developed had the edges of the torch cut holes been ground smooth before welding the beam in place.
What should have happened was the people who did the engineering work realizing their design would require those access holes to fully weld the ends of the beams, and had them water jet cut, or plasma cut under water then CNC milled or ground smooth.
I can imagine the discussion of the welding crew. “The plan says weld all around, but there’s no way to get at this side of the joint without cutting holes.” So they get hold of a structural engineer who shows where the holes can be cut without compromising strength and away they go with a sign-off on the change. But for some reason on two beams they change up the process order.
Good thing they did things in the right order on all the other beams or it could’ve been a disaster far worse than the Hyatt Regency walkway collapse in 1981 that was caused by an on the fly alteration to the plans because the way the plans were done was inconvenient, but correct.
How was the transit center problem fixed? By sandwiching the two cracked beams with steel plates and a lot of drilled holes and bolts.
I love how you talked about how a weld is the balance of several different factors to use an arc to melt a filler into the gap between steel. My husband has taken a liking to welding the past week and he asked me to find out as much as I can about it and pass what I learn onto him. I will be sure to keep these tips in mind as I search for a professional who can help him.
The most significant piece of welding is the prep and research you have to do before you start. In the event that you don’t have a spotless surface, on the off chance that you don’t have the right weld material, in the event that you have not pretreated the metal the right way, you’ll get defective welds, regardless of whether your dab looks great. Give the weld time and stress, and you’ll see those defects in splits, consumption, and breaks.
When novice welders ask whether they should pulse or not, our usual advice is to focus on their TIG basics. This isn’t because we’re trying to perpetuate some arcane inner circle within TIG welding. It’s simply because, for most TIG welders, pulse welding shouldn’t be prioritised to the detriment of other TIG skills. Indeed, in some welds, pulsing can even be harmful to good penetration – particularly with very thick materials. There’s also an additional risk of reducing current and heat going into the weld –another threat to weld integrity. Generally too, although a few welders are successful, pulsing is frowned upon for mild-steel work. That’s because it can lead to increased oxidation and brittle welds prone to rusting and cracking.
https://proconsumption.com/