After a decade in development, the Boeing CST-100 “Starliner” lifted off from pad SLC-41 at the Cape Canaveral Air Force Station a little before dawn this morning on its first ever flight. Officially referred to as the Boeing Orbital Flight Test (Boe-OFT), this uncrewed mission was intended to verify the spacecraft’s ability to navigate in orbit and safely return to Earth. It was also planned to be a rehearsal of the autonomous rendezvous and docking procedures that will ultimately be used to deliver astronauts to the International Space Station; a capability NASA has lacked since the 2011 retirement of the Space Shuttle.
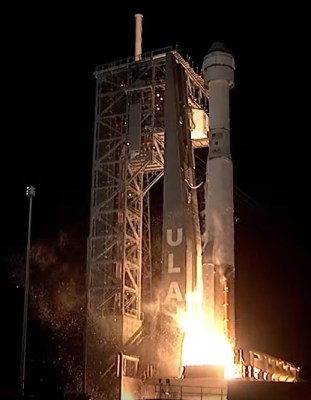
Unfortunately, some of those goals are now unobtainable. Due to a failure that occurred just 30 minutes into the flight, the CST-100 is now unable to reach the ISS. While the craft remains fully functional and in a stable orbit, Boeing and NASA have agreed that under the circumstances the planned eight day mission should be cut short. While there’s still some hope that the CST-100 will have the opportunity to demonstrate its orbital maneuverability during the now truncated flight, the primary focus has switched to the deorbit and landing procedures which have tentatively been moved up to the morning of December 22nd.
While official statements from all involved parties have remained predictably positive, the situation is a crushing blow to both Boeing and NASA. Just days after announcing that production of their troubled 737 MAX airliner would be suspended, the last thing that Boeing needed right now was another high-profile failure. For NASA, it’s yet another in a long line of setbacks that have made some question if private industry is really up to the task of ferrying humans to space. This isn’t the first time a CST-100 has faltered during a test, and back in August, a SpaceX Crew Dragon was obliterated while its advanced launch escape system was being evaluated.
We likely won’t have all the answers until the Starliner touches down at the White Sands Missile Range and Boeing engineers can get aboard, but ground controllers have already started piecing together an idea of what happened during those first critical moments of the flight. The big question now is, will NASA require Boeing to perform a second Orbital Flight Test before certifying the CST-100 to carry a human crew?
Let’s take a look at what happened during this morning’s launch.
A Matter of Time (and Fuel)
It’s important to understand that there was no catastrophic failure aboard the CST-100 this morning. The spacecraft and the United Launch Alliance Atlas V that carried it into space were operating normally during what has been described as a perfect launch. But upon separating from the booster rocket and continuing on its own independent flight, the CST-100 failed to achieve the necessary altitude to rendezvous with the ISS. While the craft is still fully functional, it simply doesn’t have enough propellant onboard to correct the situation.
Boeing currently believes the failure lies with the spacecraft’s Mission Event Timer (MET), an internal clock that starts running as soon as the spacecraft leaves the launch pad and is used to orchestrate automated systems during the mission. For reasons that are not yet known, the MET either failed or was not properly synchronized, which led to the engines not firing according on schedule. To make matters worse, the CST-100’s Reaction Control System (RCS) depleted the vehicle’s propellant reserves by attempting to make maneuvers that were unnecessary at the time.
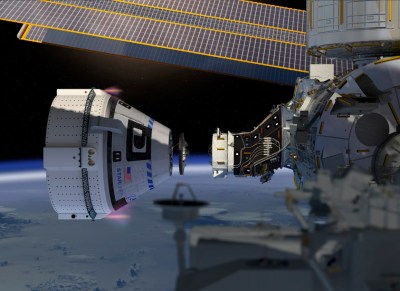
Quite simply, the Starliner was confused about what tasks it was supposed to be performing after separation from the Atlas V booster. Normally, ground control would have been able to see the error and intervene, but as luck would have it, the event occurred during an expected communications blackout.
Once ground control reestablished communications with the vehicle and got it back on course, it became clear the planned rendezvous with the Station was out of the question. Both NASA and Boeing have been quick to point out that, had there been a human crew aboard this mission, they would likely have been able to switch over to manual control and resolve the issue on their own.
Because of this, there’s some debate as to how this situation will play out in terms of the CST-100’s certification for human flight. While issues with the autonomous systems obviously need to be addressed, astronauts are trained to handle precisely these sort of computer glitches. For better or for worse, there’s a long history of human crews having to take over when their vehicle’s systems have gone haywire.
In a post-launch interview, NASA Administrator Jim Bridenstine downplayed the issue, hinting that the failure doesn’t necessarily mean the CST-100 isn’t ready to start carrying human occupants:
What it really comes down to is automation. What we were trying to do is make sure we could do this entire mission end-to-end completely automated and that didn’t work. But here’s what’s important, the spacecraft is in orbit, the spacecraft is safe. If we would have had astronauts on board, they would have been safe. In fact, if we had astronauts on board, they probably would have taken over manually and would be flying to the International Space Station right now.
Critical Next Steps
While the Starliner won’t be able to demonstrate the critical rendezvous and docking maneuvers, the test is far from a complete loss. Being the first flight of a completely new spacecraft, the fact that the craft was able to reach orbit and maneuver on its own is itself a considerable success. Indeed, when SpaceX performed the first flight of their Dragon spacecraft in 2010, the vehicle only flew in space for a little over three hours before returning to Earth. The Dragon didn’t even attempt to reach the ISS until its second flight two years later. One could argue that the fact the CST-100 will remain in orbit for several days means that Boeing still outperformed rival SpaceX as far as inaugural missions go.
But that assumes the CST-100 touches down safely on Sunday. Should the vehicle fail to perform its deorbit burn, break up on reentry into the Earth’s atmosphere, or be unable to land safely, NASA will have no choice but to reevaluate the spacecraft’s flight readiness and further delay the Commercial Crew program. As it stands, if the next Starliner mission carries a human crew, it will do so with an untested ability to actually rendezvous and dock with the Space Station; a concerning reversal of the safety-first principles the agency has operated under since the loss of the Space Shuttle Columbia.
I bet that a tube failed. i’m calling it.
I’m no longer sure what gets attention on Hack-s-Day, but Boeing?
It greatly saddens me that Chuck Peddle’s passing this week was not mentioned. Many of us were able to turn our dreams into reality when Chuck launched the 6502. He did more to accelerate the growth of the hacker community than anyone I know.
I owe a great deal to Chuck, and I’m not alone. Think of him the next time you use your iPhone. Without Chuck, Apple and many other tech companies might have never been born.
Thank you for that note.
6502/6510 machine code was the first “foreign language” I learned to speak and write without having to refer to a dictionary.
As for Boeing … when you look at some of their managers’ attitude (towards the value of human life e.g.), the best you can say is “pride will have a fall”.
It seems to me that 737 problems are directly related to airlines that cut corners and do very inadequate crew training, not Boeing manager’s attitudes about safety.
Except sensors that failed and directly led to false MCAS corrections had literally no redundancy unless airlines opted to get the expensive upgrades which is insane for a part that critical to the system–as if it’s your local dealership offering leather seats or satellite radio…
Sure it does comes down to airlines and probably lax government regulation too, all of which are inextricably linked to profit motives being prioritized over reasonable safety standards.
https://www.nytimes.com/2019/03/21/business/boeing-safety-features-charge.html
According to my cousin, a senior pilot for a major airline, yeah the plane has both a physical design compromise (engines low and forward that tips the aircraft up during high throttle) and a poorly-thought-out software kludge to counteract it.
My wife and I flew in a new 737 max in March, before they were grounded. A lovely plane; I hope they sort the problems out.
The root cause of the issues with the 737 Max is (as I understand it) the decision (made for economic measures) that it had to be possible for a pilot of the 737 NG models to be able to fly a 747 Max without needing any additional training.
Correct, they took the old 737 and tried to add much bigger engines on it which required the engines to be re-positioned on the wings which through off the CG which caused them to rely on the MCAS system to do much more elevator correcting than before in order to prevent stalls. But MCAS was a minor pilot assistant so the need for redundancy was minor but now was critical and either they reviewed the cost of making redundancy standard and made a dangerous choice or they completely disregarded the fact they taken a minor system and made it critical without reviewing or testing failure scenarios. Too big to fail, Boeing is.
As someone who follows both electronics and space tech, I’m thinking why not both? Of course they might be waiting for his birthday so as to celebrate his life rather than his death.
When I think of Hackaday I think of space tech… the most improvised, budget-minded, reverse engineered, jerry-rigged tech.
Seriously though. When I think of Hackaday I think of Elon Musk and how fanatical the writers and commenters are about him and his companies. Which is why I knew this article would be here.
Well said. Chuck Peddle’s 6502 was used in the BBC micro and inspired the manufacture Acorn Computers to create ARM. I cut my teeth on that CPU at 13 years old
This stack definitely qualifies as a hack. A cobbled together semi-3 stage jerry rig made up of a Russian engine on an old booster that can have an arbitrary set of SRB’s, joined to an ancient second stage with a weird 2 engine configuration with a bell end on the top with some odd added shrouds to make it all work.
“Stupid carbon rod!”
-Homer Simpson
“For NASA, it’s yet another in a long line of setbacks that have made some question if private industry is really up to the task of ferrying humans to space.”
Private industry has built all the NASA equipment for decades, Boeing in particular.
Agree with you but the new generation of managers in private industry today is far different than yesterday’s managers.
Maybe Boeing needs to learn a lesson on how to invest in their engineers again.
Or even just listen to them. A lot of this stuff was known, but you can’t tell a CEO they’re going to have to delay the rollout of or the board will kick them off.
That should have said rollout of “big honking project X”, but I put it in tags so it got removed.
Sure, but previously the contractors were working more closely with NASA, building to a NASA approved spec. Now, they’re letting industry ‘compete’ to meet requirements.
Worth noting that the Atlas V rocket itself it a Lockheed Martin design originally, not a Boeing design like the Delta IV.
(This Atlas was built by ULA, which is a joint Boeing/Lockheed company).
The rocket worked perfectly, it was the Boeing built capsule that had problems.
Evidently it hit the one place where tdrs doesn’t cover and it screwed up the timing. So it was using fuel up quite a bit faster than normal as it was in high precision approach mode instead of in a lower fuel consuming mode. It could still have reached iss but was on the edge of the flight margins. And yes someone in the seat would have easily been able to say wait a minute we shouldn’t be backwards here and flown it manually to dock. The docking was an optional thing and all that it may have affected was unmanned supply missions. Everything else was ok.
– Once again, Captain, what fuel gauge is now active?
– The 2.5 one, as instructed.
– Inch or centimeters?
– …(beep)!
:o)
I’m not sure it was a hole in the TDRSS coverage but rather a place where handover from one sat to another occurs. What bothers me is that this is usually a < 60 sec delay in rerouting the message to the spacecraft. Somehow I think if that was all that was needed, another 60 secs, it would have worked and ground control would have been asserted in time. I have to ponder if the attitude of the spacecraft also somehow misaligned the antenna so coverage was lost ?
Something that also bothers me is that the RCS jockeying the spacecraft about used 25% of the fuel. It's not clear to me why re-orienting the spacecraft and holding attitude should use that much fuel.
FWIW I know that expecting answers this early into the investigation is a sure sign of CSI-itis. Wherein DNA tests take an hour and the forensics show who the guilty party is in 2 days (show-time) max. :)
I have no idea what really happened, but it’s easy to use a lot of RCS fuel if the control algorithm is incorrect, making too large a correction, and keeps overshooting the desired attitude.
“One could argue that the fact the CST-100 will remain in orbit for several days means that Boeing still outperformed rival SpaceX as far as inaugural missions go.”
One could, but it would be disingenuous.
Claiming that a test flight that FAILED to meet its critical objectives somehow outperformed a shorter rival test that SUCCESSFULLY met its critical objectives is like claiming a victory because the one had a better paint job.
Success > Failure
Yeah, but NASA is claiming that docking with the station was never a hard requirement of this flight.
If that’s the case, then pushing all the way to the station and docking was essentially a stretch goal, and the test didn’t fail at all (assuming it lands ok).
Didn’t SpaceX send a DragonCrew capsule to the ISS, dock, undock and return to Earth without issues? They lost that capsule when testing the launch abort system and a valve let liquids mix which should never mix inside of control plumbing and it all blew up. They were using valves because they’d wanted to do propulsive landings on land(like 1st stage). Because that’s not a current requirement or in the schedule, they valves are gone and replaced with one time use plates.
That was the second version of Dragon though, that already had a dozen or more flights beforehand. CST-100 is a whole new spacecraft, so it’s not fair to compare.
Boeing today is where SpaceX was in 2010, at least in terms of in-house design.
Just because the names contain the same word doesn’t mean it’s the same craft….
And this is hardly the first spacecraft Boeing has ever worked on….
One CANNOT compare human rated spacecraft against non-human rated ones. They are completely different animals. The author’s comparing SpaceX’s 2010 Dragon (non-human rated) to Boeing’s CST-100 (human rated) is not valid.
Somebody forgot about Daylight Savings Time, stupid farmers!
It wasn’t Daylight Saving Time. It was revealed yesterday at the post landing news briefing that the Mission Elapsed Timer (MET) was off by eleven hours. This has to be just about the length of time the Boeing CST-100 Starliner had been powered up since the early part of the count down. Read the entry on Wikipedia here: https://en.wikipedia.org/wiki/Boeing_Orbital_Flight_Test, second paragraph. The question is asked near the end of the post-landing news briefing here: https://youtu.be/kocZnVAbRsk?t=2683. It was a picture perfect landing with all three parachutes firmly attached to the capsule this time.
Probably the Y2K defect.
Didn’t Boeing improve on their Hazards Analysis from MCAS?
I wonder if there was adequate Failure Mode & Effects Analysis (FMEA) done on the METs. It’s obvious now that it could be a critical failure if the timers are off. Then again, Boeing bean counters could have classified it as a lower hazard classification.
Wasn’t there any redundancy like they should have on MCAS? No parallel clock timers in sequence with parity checks in place? Probably a cost-benefits analysis by upper management said no.
This was suppose to be an “automated” system, now its another strike for Boeing…
Maybe their Hazards Analysis team was sent to help out the 737Max team.
And there they saw how parts are forced together with hammers, and how statically unstable planes are made stable by single non-redundant computer. They all died of horror on the spot.
It does seem like the same pattern of failure as the 737 MAX:
A relatively minor failure occurs, and then a control system blindly over-corrects, making the problem worse, until it becomes impossible to perform the original mission/function.
That’s pretty astute. The only missing piece in the comparison is the crew, who to continue the analogy, would have had insufficient training to identify the root cause and disable the control system in time to save the craft
The lack of redundancy is definitely the big issue here. There’s only one clock on-board? It’s not being checked for sync? Its absurd.
Space Shuttle had 5 computers going at any given moment, SpaceX does three. Redundancy is required when there’s human lives in the balance.
Totally agree.
Now to add this, it’s the functional analysis, design, and FMEA classification that all play into determining if a system (or subsystem) gets redundancy or not. Remember, Systems Engineering also involves cost and scheduling. Money does play a factor, but it must be balanced with quality and safety.
Boeing use to get lots of cost plus contracts, but NASA is leaning more into firm-fixed price.
I think Boeing continues to push the boundaries of simplifying complex systems at the expense of reliability engineering based on how NASA funds their contracts. The Apollo contracts are far different than what is going on today.
Boeing seems to be “commoditizing” complex aerospace systems no different than how McDonalds “value chain” their food supplies to squeeze maximum profits out their hamburgers.
Engineers aren’t burger flippers. You shouldn’t get rid of them and replace them with newbies because they cost too much. If you do, you get juniors who cant follow procedures to rig a parachute or code/validate software so it grabs the wrong timer coefficient. Just look at MCAS, another failure of Boeing decision-makers who probably lack sufficient engineering experience and classified an AoA failure as Major vs Catastrophic (thereby not having to implement dual redundancy). Basically garbage in, garbage out. And now 346 people prematurely dead.
Boeing upper management culture needs new leadership and it should have began after it was destroyed by the McDonnell Douglas merger.
Imagine flight timer failure somewhere after 9hr and 6minutes. Damn signed 16bit counters.
MechJeb could probably have handled the ascent properly. ;) https://forum.kerbalspaceprogram.com/index.php?/topic/154834-18x-anatid-robotics-mumech-mechjeb-autopilot-291-15-november-2019/
Obviously Boeing received inadequately lavish bribes/payouts in order to ensure success…
Someone wrote the timing loops thinking the arduino was gonna get 5 volts, when they only gave it 3.3…
My bet was that a windows update happened 30 minutes into the flight.
Thanks for the buggy software! You’d think by WIndows 10, it would be perfect out of the box???
i think i know what boeing’s problem is. their factory is in a state that has legalized weed.
LOL, but it could be booze as well, even with legalized weed, there are probably more boozers than stoners.
Booze and unions don’t mix either, seems unpossible to fire someone for repeatedly being drunk on the job.
Russians make it look so easy and routine with their Soyuz that people forget how hard it is to get stuff to ISS.
SpaceX makes it look pretty easy and routine to get “stuff” to the iss.
It’s getting “people” there is a bit harder.
It’s amusing, with all the high tech advances in engineering and materials we still can’t put a man into orbit like we did with Mercury, Gemini, etc.
Now we’re stuck using Russian rockets and motors because our scientists and engineers are so stupid they can’t build anything anymore.
We’d be better off giving those simpletons Etch-a-sketches and putt them in a corner so they stop wasting taxpayer money.
As for Boeing, they gave us the 737Max which is a abortion and poster child for management and engineering stupidity that has managed tol over 300 people. Way to go Boeing.
Read Peter Theil 0 to 1, I tried writing something but then realized I was just parroting his exceptionally well thought out work.
Quick summary, the best engineers are not going to be coming through our current antiquated education system. Literally everyone is cheating in engineering schools today, there is way too little focus on scientific computing and computer programming in general, it’s a big fucking mess. Case in point, we still use classical math (idealized world) to solve thermodynamics problems, rather than PID loops and statistics (real world) and engineers typically get 0 training in Chaos Theory. This is because our institutions have protected themselves with excessive regulations. Until those regulations are eased, these failures will continue.
My take is that earlier space missions were constrained by weight and technical limitations, so that well-trained, and highly motivated and disciplined people performed the role of high-level control systems, and these people were not prone to massively over-correcting for relatively minor and localized failures.
Now that modern systems are so cheap and capable, there is a tendency to overuse them, and program cost control considerations limit the scope of engineering and testing.
The core issue is that modern control systems lack awareness of the big picture, which humans took centuries to develop.
“One could argue that the fact the CST-100 will remain in orbit for several days means that Boeing still outperformed rival SpaceX as far as inaugural missions go.” Given the difference in billions of public funding and a decade of separation, It’s beyond sad that the author elected to try to make such a pitiful comparison. So far beyond sad that it is pathetic.
Yeah, I don’t know how Boeing continues to make screwups and still gets a pass. The launch abort test also had a failure, but Boeing and NASA announce it as a success.
Sadly, there are many other large companies like Boeing, sitting on their reputation and skimping on engineering, which is the actual source of their IP. OTOH marketing, PR and lobbying gets a generous budget. They continue to exist because the barriers to entry are so expensive.
Monopoly. And this is the reason they should not exist.
The problem is all the subcontractors and testing the intergration. And sub-ing to very stoned contractors in Silicon Valley and Seattle, where it is legal.
It cracks me up how many people are still scared of the hippies.
They don’t realize how different marijuana is compared to other drugs when it comes to testing.
There is no way any significant percentage of factory workers subject to drug tests are smoking pot. It lasts too long in the system, if they do it on the weekend they already get fired, they’re certainly not doing it at work.
Ditto on “pathetic”
This statement by the author is quite laughable. SpaceX’s Crew Dragon launched to ISS 2nd March this year, docked and landed safely. It was unfortunately destroyed in a LES test in April. So how the ding-dang is Boeing out performing SpaceX.
Pray, do explain?
“At Troposphere, make left turn”
“Left turn now”
“recalculating……”
“Turn around when possible”
Initially I was fairly happy with the Boeing/NASA explanation, until it occurred to me what might happen if the flight computer had decided it was time to de-orbit during (or even after!) docking maneuvers…..would definitely be reaching for F9 in that case :v
I’m sure they tested the bejaysus out of it but for such a key piece of technology on the spacecraft they should have performed (and probably did perform) simulated failure tests. Wait and see what the results say.
I’m a bit surprised that none of the above remarks even considers an obvious possibility. The success of this launch system would cost Roscosmos, a quarter billion dollars or so per launch.
>> For NASA, it’s yet another in a long line of setbacks that have made some question if private industry is really up to the task of ferrying humans to space.
Say what? You think private industry hasn’t been involved until now? Surely that would be a surprise to McDonnell (Mercury, Gemini, Skylab), North American (Apollo), and Grumman (Lunar Lander). Not to mention Lockheed-Martin (Atlas, Titan).
Rockwell (Apollo).
I just saw “Apollo 11” in iMax.
Could not set up a clock properly.
I worked on the 2010 C1 dragon capsule as well as the 2012 C2+ capsule. It’s inaccurate to say this starliner flight is analogous to the C1 mission. Based on the development schedule, it is analogous to the C2 capsule, which successfully berthed with ISS with few major anomalies. I forget whether C1 or C2 flew a wheel of cheese…
Gentlemen, as one tech who doesn’t normally know as much as the talented and smart people you all are ( I mean this, not sarcasm), I really think I have mailed it. With careful study of all the systems what can go wrong in a flight test like this, I now know what the issue is.
It’s a bad piston rings on the 3rd cylinder of the motor. It’s either that or a loose gas cap that caused the engine light to come on. Please pass this on to NASA and Boeing.
Thx,
Jim
In Spain we call that “la junta de la trócola” :-D
Disappointing failure. I have a hard time imagining how this fundamental a flaw went undetected in testing or simulation. I also think the comms failure during this critical part of the flight is inexcusable.
If I was NASA, I would expect these shortfalls to be fixed, tested hard, and the unmanned flight and docking test repeated, before i would risk any humans aboard.
My bet is that they never ran a full flight test using the real hardware. The Starliner gets MET from the Atlas. It’s been reported that it was 11 hours ahead. The Atlas was powered up 11 hours prior to launch. Coincidence, perhaps. I’ll guess that the Starliner got the wrong time, time since power instead of time since launch. This would have been noticed in all the testing Boeing did except that testing was done with some form of Atlas simulator. In that simulator, the time since power up was never set, it was always zero. The right time is 0 if Starliner got the MET once at launch and ran it’s own timer thereafter.
If my guess is correct, there will be a hell of a battle for blame as I bet ULA provided the SIM hardware and software Boeing used to checkout Starliner-Atlas communication.
Tests in simulators are allways virtual tests.
Look at #Boeing737MAX tested in simulator ok
but failed in real flights due to untested #MCAS vs. #AoA sensor failure
To build an intelligent flight simulator it takes time and money, a lot of money to test every crash scenario
I think you have probably nailed the flaw. In their testing, Boeing perhaps always assumed that both clocks always started at t = 0. Their simulation didn’t allow for the two clocks to have different initial values.
Which means that, as many others here have suggested, Boeing’s simulation tests were inadequate, probably rushed to meet some manager’s target dates.
I just saw the landing coverage. I’ve never seen such a bunch of what looks like unprofessional yahoos pull off such a complex operation. Sure, the coverage was raw and uncut, but the contrast with Nasa’s operations and communications was shocking. Even compared to SpaceX they come off as a bunch of unpracticed louts, spectacularly lucky in spite of themselves.
I mourn for Boeing and the US space program.
… ran five blocks and only farted.
This shouldn’t upset you, what should upset you is that the ISS is in the wrong orbit to launch deep space missions from, oh it’s in the correct orbit the reach from Russia, but not for any other major things, the difference in fuel expenditure rules out using it as a platform. Or so I’ve read.
“Or so I’ve read”
My unsolicited advice is to ask more questions, but read less answers.
Does it even make sense to want to use a low Earth orbit science station as a launch platform for something else?
Is a launch platform useful in space, or is that only useful at the very bottom of a gravity well? Does the launch platform hold its position when you launch off it, or does it fall out of orbit and burn up?
Given a huge amount of the fuel used breaking from the ground to orbit, clearly launching from a platform, and by launching I mean not from a stationary object – it’s not a push off like you seem to be indicating, but for stocking the ship, which would use much less fuel starting from there than from the ground. But if you are launching out of the plane to a planet you waste fuel getting back into it. It also should be noted they wouldn’t really need a multi-stage rocket if they launch from a platform in space, multi-stage rockets are used because the air changes from ground level up, and it also releases weight after the fuel sections are used up. And a stage might work at ground level, but not properly at 10 miles up. I suppose solid rocket fuel doesn’t suffer from the air pressure issue that a liquid fuel rocket does, but they of course are not able to be stopped once lit. Hard to say how they would transport both fuel and stock to a ship in orbit, maybe a large mag-lev to toss the supplies up. Less cost, less dangers since the only fuel used is to slow the payload. Also, for any space based ship, they might use ion propulsion or other similar systems for the major push and fueled control jets for maneuvering – which would require much less fuel on board.
Bobby, you said “multi-stage rockets are used because the air changes from ground level up, and it also releases weight after the fuel sections are used up”
It’s true that rocket nozzles perform better in the air pressure for which they are designed, but that’s a small effect. The real reason we use multi-stage rockets is to get rid of dead weight. Once we’ve used all the fuel in the first stage, there’s no good reason to keep carrying the empty fuel tanks, plus engines, fuel pumps, plumbing and support structure — sometimes even computers — that was necessary to get off the ground. This concept holds true for every stage. Ideally, you’d like to dump the dead weight as many times as you can. On the other hand, the docking structures add weight and complexity. In practice, it’s a trade-off between efficiency and simplicity.
As for ion propulsion, we now use them routinely for station-keeping of geostationary spacecraft like comm satellites.
Ruby, it DOES make sense if you’re using a space station to assemble a larger space system such as a manned Mars mission. That was von Braun’s original dream, first proposed in 1948. After Apollo, vB just assumed we’d keep right on going to Mars.
In his scenario, the Space Station would not be for science at all, but more of an assembly plant to build Mars rockets and systems. To deliver parts and fuel to the station, we’d need a SHUTTLE capable of ferrying goods and people to/from the station.
Unfortunately, NASA in their infinite wisdom decided to build the Shuttle, but not the station. Which is why we ended up with a Shuttle but not the space station it would be shuttling things TO. Brilliant.
In 1972 I attended the first meeting at NASA/Marshall, where a NASA team first unveiled their concept of the Shuttle. Not having a destination, they pitched the Shuttle as a ferry that would be able to launch comm and weather satellites, much cheaper than single-use boosters. Their cost estimates were WILDLY optimistic, and were based on the assumption that we’d be able to turn the Shuttle around after only a week or so of refurbishment.
That never happened, of course — I think mostly because the thermal tiles needed a _LOT_ more extensive rework that anyone thought it would.
Another problem with the Shuttle was that it would be unable to boost satellites to GEO altitudes. For that, we needed another booster, which would be called the Interim Upper Stage (IUS), a three-stage solid-rocket booster. I worked on the IUS for a few years, and it did make it into service. Politics caused a name change to
“INERTIAL Upper Stage,” because the term “Interim” implied that we’d soon be building yet another upper stage.
Of course, we finally did get a Space Station, but certainly not the one that von Braun envisioned. No way will we ever use the ISS as a place to build Mars rockets. For starters it’s in the wrong orbit.
A bit of trivia: I also worked for a time on the software for the ISS. At that time, NASA had declared that all the software for the ISS would be run on a _SINGLE_ Intel 80386
It is down. Got it’s butt parked in the right place too!
NASA and Congress have been kissing Boeing booty for years now. That marketing campaign they’ve been running about the CST capsule has been insane. The damned thing was years from launch and they were selling it to us like it was ready to orbit Vulcan!
Between this and the MAX, Boeing is losing its former glory. How in the living hell did they deploy the MCAS system without running a simulation that took a bad sensor into account?? How did they NOT put in a simple piece of code to instruct the system to correct only to a certain descent angle and only above a certain altitude before alerting the pilots that the auto feature was faulty and required manual override….OPTIONAL?? Mein Leiber Gott what kind of madman makes safety OPTIONAL?
SpaceX outperforms Boeing. But the government is going all out to make Boeing the odds on favorite to get us to the Moon and Mars at much higher costs.
Boeing has hired many a government and military person because of their connections. They also have a very active lobbying mechanism. Need more be said?
And in addition, accountants run everything. They may be good at counting beans, but suck at rocket science
https://www.youtube.com/watch?v=1C4d7rUcekE
Exactly. Corporate welfare!
“Need more be said?”
Yes, a lot more, because in the past when they were one of the best engineering outfits on the planet they already hired lots of people with government and military experience, and did a lot of lobbying.
So this says little of what led to their decline. There must be something more.
My try: Maybe when they merged with other similar businesses and “eliminated redundancies” they were actually eliminating their organizational knowledge, which didn’t overlap seamlessly, and regardless that knowledge wasn’t held directly by the stock certificates, but instead it was held inside the actual physical brains of the employees. Since the effort to eliminate redundancies leaves everyone in a slightly different position, none of boundaries between different units of organizational knowledge were maintained. Worse, each eliminated “redundancy” created a gap so that there would be no hope that the knowledge boundaries would be maintained by momentum. The organization at that point no longer could even detect what knowledge it had, and therefore had no way to organize or preserve it.
Could you update your story ?
“Boeing’s Starliner Fails To Reach Space Station
Due its shape it’s hard to implement vector drive control by thrusters