Ho-hum — another week, another high-profile bricking. In a move anyone could see coming, Humane has announced that their pricey AI Pin widgets will cease to work in any meaningful way as of noon on February 28. The company made a splash when it launched its wearable assistant in April of 2024, and from an engineering point of view, it was pretty cool. Meant to be worn on one’s shirt, it had a little bit of a Star Trek: The Next Generation comm badge vibe as the primary UI was accessed through tapping the front of the thing. It also had a display that projected information onto your hand, plus the usual array of sensors and cameras which no doubt provided a rich stream of user data. Somehow, though, Humane wasn’t able to make the numbers work out, and as a result they’ll be shutting down their servers at the end of the month, with refunds offered only to users who bought their AI Pins in the last 90 days.
failure29 Articles
Blame It On The Sockets: Forensic Analysis Of The Arecibo Collapse
Nearly three years after the rapid unplanned disassembly of the Arecibo radio telescope, we finally have a culprit in the collapse: bad sockets.
In case you somehow missed it, back in 2020 we started getting ominous reports that the cables supporting the 900-ton instrument platform above the 300-meter primary reflector of what was at the time the world’s largest radio telescope were slowly coming undone. From the first sign of problems in August, when the first broken cable smashed a hole in the reflector, to the failure of a second cable in November, it surely seemed like Arecibo’s days were numbered, and that it would fall victim to all the other bad luck we seemed to be rapidly accruing in that fateful year. The inevitable finally happened on December 1, when over-stressed cables on support tower four finally gave way, sending the platform on a graceful swing into the side of the natural depression that cradled the reflector, damaging the telescope beyond all hope of repair.
The long run-up to the telescope’s final act had a silver lining in that it provided engineers and scientists with a chance to carefully observe the failure in real-time. So there was no real mystery as to what happened, at least from a big-picture perspective. But one always wants to know the fine-scale details of such failures, a task which fell to forensic investigation firm Thornton Tomasetti. They enlisted the help of the Columbia University Strength of Materials lab, which sent pieces of the failed cable to the Oak Ridge National Laboratory’s High Flux Isotope reactor for neutron imaging, which is like an X-ray study but uses streams of neutrons that interact with the material’s nuclei rather than their electrons.
The full report (PDF) reveals five proximate causes for the collapse, chief of which is “[T]he manual and inconsistent splay of the wires during cable socketing,” which we take to mean that the individual strands of the cables were not spread out correctly before the molten zinc “spelter socket” was molded around them. The resulting shear stress caused the zinc to slowly flow around the cable strands, letting them slip out of the surrounding steel socket and — well, you can watch the rest below for yourself.
As is usually the case with such failures, there are multiple causes, all of which are covered in the 300+ page report. But being able to pin the bulk of the failure on a single, easily understood — and easily addressed — defect is comforting, in a way. It’s cold comfort to astronomers and Arecibo staff, perhaps, but at least it’s a lesson that might prevent future failures of cable-supported structures.
Continue reading “Blame It On The Sockets: Forensic Analysis Of The Arecibo Collapse”
Books You Should Read: Why Buildings Fall Down
People with long commutes usually come up with tricks to stay focused and alert and avoid the dangerous tendency to zone out during the drive. One trick I used to use was keeping mental track of the various construction projects I’d pass by on my way to work, noticing which piers on a new highway overpass were nearing completion, or watching steelworkers put together the complex rebar endoskeletons of a new stretch of roadway.
One project I loved to watch back in the 80s was a new high-rise going in right next to the highway, which fascinated me because of the construction method. Rather than putting together a steel frame, laying out decking, and covering each floor with concrete, the workers seemed to be fabricating each floor at ground level and then jacking them up on the vertical steel columns. I was fascinated by this because every time I passed by the floors were in a different position, spreading out vertically as the building grew.
And then one day, it just wasn’t there anymore. Where there had been columns stretching nine stories into the city sky with concrete slabs lined up ready to be jacked up into their final positions, there was just an enormous hole in the ground with a ghastly gray cloud of concrete dust rising from it. It was April 23, 1987, and what was once going to be a luxury apartment building called L’Ambience Plaza in Bridgeport, Connecticut lay pancaked into the ground, entombing the bodies of 28 construction workers.
Continue reading “Books You Should Read: Why Buildings Fall Down”
So How Does A Rocket Fly Sideways, Anyway?
It’s often said that getting into orbit is less about going up, and more about going sideways very fast. So in that sense, the recent launch conducted by aerospace startup Astra could be seen as the vehicle simply getting the order of operations wrong. Instead of going up and then burning towards the horizon, it made an exceptionally unusual sideways flight before finally moving skyward.
As you might expect, the booster didn’t make it to orbit. But not for lack of trying. In fact, that the 11.6 meter (38 feet) vehicle was able to navigate through its unprecedented lateral maneuver and largely correct its flight-path is a testament to the engineering prowess of the team at the Alameda, California based company. It’s worth noting that it was the ground controller’s decision to cut the rocket’s engines once it had flown high and far enough away to not endanger anyone on the ground that ultimately ended the flight; the booster itself was still fighting to reach space until the very last moment.
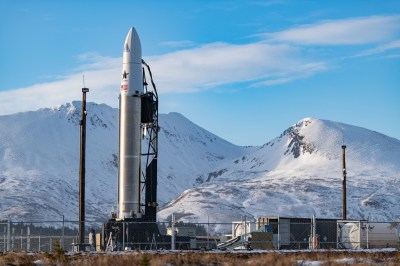
There’s a certain irony to the fact that this flight, the third Astra has attempted since their founding in 2016, was the first to be live streamed to YouTube. Had the company not pulled back their usual veil of secrecy, we likely wouldn’t have such glorious high-resolution footage of what will forever be remembered as one of the most bizarre rocket mishaps in history. The surreal image of the rocket smoothly sliding out of frame as if it was trying to avoid the camera’s gaze has already become a meme online, arguably reaching a larger and more diverse audience than would have resulted from a successful launch. As they say, there’s no such thing as bad press.
Naturally, the viral clip has spurred some questions. You don’t have to be a space expert to know that the pointy end of the rocket is usually supposed to go up, but considering how smooth the maneuver looks, some have even wondered if it wasn’t somehow intentional. With so much attention on this unusual event, it seems like the perfect time to take a close look at how Astra’s latest rocket launch went, quite literally, sideways.
Continue reading “So How Does A Rocket Fly Sideways, Anyway?”
Sirius XM Satellite Failure A Reminder That Space Is Risky (And That Satellite Insurance Is A Thing)
It’s easy to imagine that once a spacecraft leaves Earth’s atmosphere and is in a stable orbit, the most dangerous phase of the mission is over. After all, that’s when we collectively close the live stream and turn our attentions back to terrestrial matters. Once the fire and fury of the launch is over with, all the excitement is done. From that point on, it’s just years of silently sailing through the vacuum of space. What’s the worst that could happen?
Unfortunately, satellite radio provider Sirius XM just received a harsh reminder that there’s still plenty that can go wrong after you’ve slipped Earth’s surly bonds. Despite a flawless launch in early December 2020 on a SpaceX Falcon 9 and a reportedly uneventful trip to its designated position in geostationary orbit approximately 35,786 km (22,236 mi) above the planet, their brand new SXM-7 broadcasting satellite appears to be in serious trouble.
Maxar Technologies, prime contractor for the SXM-7, says they’re currently trying to determine what’s gone wrong with the 7,000 kilogram satellite. In a statement, the Colorado-based aerospace company claimed they were focused on “safely completing the commissioning of the satellite and optimizing its performance.” But the language used by Sirius XM in their January 27th filing with the U.S. Securities and Exchange Commission was notably more pessimistic. No mention is made of bringing SXM-7 online, and instead, the company makes it clear that their existing fleet of satellites will be able to maintain service to their customers until a replacement can be launched.
So what happened, and more importantly, is there any hope for SXM-7? Neither company has released any concrete details, and given the amount of money on the line, there’s a good chance the public won’t get the full story for some time. But we can theorize a bit based on what we do know, and make some predictions about where things go from here.
NSF Releases Video Of Arecibo’s Final Moments
Today the National Science Foundation released a pair of videos that document the collapse of the Arecibo Observatory with incredible detail. A wide shot, apparently taken from the Visitors Center, shows the 900 ton instrument platform breaking free and swinging on the remaining support cables until it smashes into the edge of the dish. The second clip, recorded by an airborne drone, is focused directly on the cables as they failed. Both can be seen in the video embedded below.
Together, they produce an invaluable visual record of what finally brought the iconic radio telescope down. As was predicted by engineers earlier in the month, the failure of another support cable on tower 4 triggered a chain reaction that brought the entire platform crashing down onto the 305 meter reflector. Footage from a drone observing the top of tower 4 shows that the entire sequence, from the first visual wire break to the remaining cables being torn from their mounts, only took five seconds. While some initially doubted the NSF’s determination that it was too dangerous to repair Arecibo, this footage seems to prove just how tenuous the structural integrity of the Observatory really was.
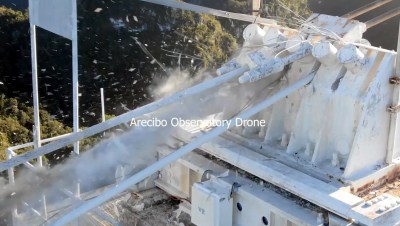
These videos will hopefully help investigators who still need to determine why the cables failed in the first place. The cable in August didn’t snap, it simply pulled lose from its mount. It was suspected that the cable may have been incorrectly installed, but as it was only a backup, the situation was not seen as critical. But when the second cable failed in November it was found to have snapped at just 60% of its minimum breaking strength.
This immediately called into question the condition of the remaining cables, and ultimately lead to the decision by the NSF to proceed with a controlled demolition of the Observatory that would preserve as much of the scientific equipment as possible. Unfortunately, the remaining cables didn’t last long enough to put that plan into action.
Continue reading “NSF Releases Video Of Arecibo’s Final Moments”
Low-Tech Fix Saves Expensive, High-Tech TV From Junk Pile
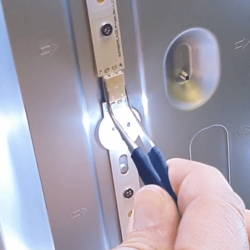
[Tweepy]’s TV stopped working, and the experience is a brief reminder that if a modern appliance fails, it is worth taking a look inside because the failure might be something simple. In this case, the dead TV was actually a dead LED backlight, and the fix was so embarrassingly simple that [Tweepy] is tempted to chalk it up to negligently poor DFM (design for manufacture) at best, or even some kind of effort at planned obsolescence at worst.
What happened is this: the TV appeared to stop working, but one could still make out screen content while shining a bright light on the screen. Seeing this, [Tweepy] deduced that the backlight had failed, and opened up the device to see if it could be repaired. However, the reason for the backlight failure was a surprise. It was not the power supply, nor even any of the LEDs themselves; the whole backlight wouldn’t turn on because of a cheap little PCB-to-PCB connector, and the two small spring contacts inside that had failed.
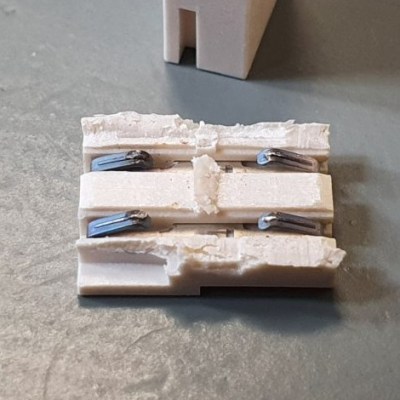
From the outside things looked okay, but wiggling the connector made the backlight turn on and off, so the connection was clearly bad. Investigating further, [Tweepy] saw that the contact points of the PCBs and the two little conductors inside the connector showed clear signs of arcing and oxidation, leading to a poor connection that eventually failed, resulting in a useless TV. The fix wasn’t to clean the contacts; the correct fix was to replace the connector with a soldered connection.
Using that cheap little connector doubtlessly saved some assembly time at the factory, but it also led to failure within a fairly short amount of time. Had [Tweepy] not been handy with a screwdriver (or not bothered to investigate) the otherwise working TV would doubtlessly have ended up in a landfill.
It serves as a good reminder to make some time to investigate failures of appliances, even if one’s repair skills are limited, because the problem might be a simple one. Planned obsolescence is a tempting doorstep upon which to dump failures like this, but a good case can be made that planned obsolescence isn’t really a thing, even if manufacturers compromising products in one way or another certainly is.