One of the tricky parts of engineering in the physical world is making machines work with the available resources and manufacturing technologies. [Tom Stanton] has designed and made a couple of air-powered 3D printed engines but always struggled with the problem of air leaking past the 3D-printed pistons. Instead of trying to make an air-tight piston, he added a rubber membrane and a clever valve system to create a diaphragm air engine.
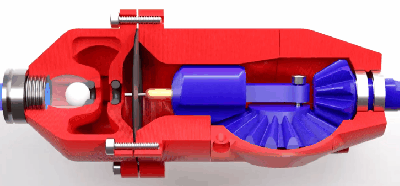
A round rubber diaphragm with a hole in the center creates a seal with the piston at the top of its stroke. A brass sleeve and pin protrude through the diaphragm, and the sleeve seals create a plug with an o-ring, while the pin pushes open a ball which acts as the inlet valve to pressurize an intermediate chamber. As the piston retracts, the ball closes the inlet valve, the outlet valve of the intermediate chamber is opened, forcing the diaphragm to push against the piston. The seal between the piston and diaphragm holds until the piston reaches its bottom position, where the pressurized air is vented past the piston and out through the gearbox. For full details see the video after the break.
It took a few iterations to get the engine to run. The volume of the intermediate chamber had to increase and [Tom] had to try a few different combinations of the sleeve and pin lengths to get the inlet timing right. Since he wanted to use the motor on a plane, he compared the thrust of the latest design with that of the previous version. The latest design improved efficiency by 366%. We look forward to seeing it fly!
Most of our regular readers have seen [Tom]’s array of flying machines, and he has also tested alternative power sources like kinetic energy stored in a flywheel.
“This GIF is worth 115 words”
Am i the only one who selected the corresponding part of the text and checked it in an online word counter app? =)
# I used an offline app
>>> s = “A round rubber diaphragm with a hole in the center creates a seal with the piston at the top of its stroke. A brass sleeve and pin protrude through the diaphragm, and the sleeve seals create a plug with an o-ring, while the pin pushes open a ball which acts as the inlet valve to pressurize an intermediate chamber. As the piston retracts, the ball closes the inlet valve, the outlet valve of the intermediate chamber is opened, forcing the diaphragm to push against the piston. The seal between the piston and diaphragm holds until the piston reaches its bottom position, where the pressurized air is vented past the piston and out through the gearbox.”
>>> len(s.split()) == 115
True
echo “A round rubber diaphragm with a hole in the center creates a seal with the piston at the top of its stroke. A brass sleeve and pin protrude through the diaphragm, and the sleeve seals create a plug with an o-ring, while the pin pushes open a ball which acts as the inlet valve to pressurize an intermediate chamber. As the piston retracts, the ball closes the inlet valve, the outlet valve of the intermediate chamber is opened, forcing the diaphragm to push against the piston. The seal between the piston and diaphragm holds until the piston reaches its bottom position, where the pressurized air is vented past the piston and out through the gearbox.” |wc
1 115 654
Since this gif has 52 frames…
Shouldn’t it be 52000 words? :D
Then again, only the key frame is a full image so, hmm.
Well, the GIF refers to the entire animation, so in this case no.
Brilliant!
I would love to see a transparent version in slow motion. It would be interesting to see if the diaphragm really works and moves in the same way the animation suggests.
Genuine question, why is converting the air flow/pressure into torque and then into air flow/pressure again better than just using a nozzle to regulate the air flow?
“Propellers are most fuel-efficient and rockets are least fuel-efficient. A propeller moves a large amount of air slowly; a jet or rocket moves a small amount of air quickly.”
https://howthingsfly.si.edu/propulsion/engines
That’s why most efficient engines for planes are big turbofans, where jet engine just turns big ass propeller instead of just using more “jet”.
Think about this way – in rocket you can push off from your stored air. With propeller, you can push off surrounding air. It’s like you tried to propel a car by throwing away your fuel (or battery) very fast. Much better to do it by throwing away all of the earth.
This is not applicable here. You’re discussing the most efficient way to turn stored chemical energy into momentum in an air environment. Vitomakes is asking about the most efficient way to modify a confined gas stream, a very different problem.
An engineer (or physicist) should recognize this as a solution to an impedance matching problem (which it is).
This! He’s letting out small bursts of high pressure air, and trading them for large quantities of (moved) low-pressure air. It’s like gearing down a bike.
Exactly. Last summer, when I said that exact thing (bicycle gears are an adjustable impedance transformer that match your legs to the load) to a pair of bright young engineers they first looked at me funny, and then the light went on. Very funny to see.
AFAIK de Laval nozzle does just this. It changes high pressure air into faster moving low pressure air. Why is slow moving lot’s of air better than faster moving but less of air?
Because per Tsiolkovsky’s rocket equation the delta-v of a rocket engine is proportional to the velocity of it’s exhaust gasses.
wait, just re-read your comment. In this case, I would guess that it is easier and less stress on the engine if it exchanges high pressure for high volume. it is also a question of impedance matching. The inertia of the system will not respond quickly enough to the high pressure fast air. As someone pointed out earlier, think of it like a bicycle with multiple gears. if you put it in your lowest gear, you will be forced to peddle very fast to go at a relatively slow speed, there is a limit on how fast you can peddle. shift up and you can take better advantage of your efforts.
I think I understood at least something, please someone correct me if I am wrong.
One thing is converting flow/pressure like an electrical transformer does. This is impedance matching.
But, if you increase flow a lot, you simply end up emptying your bottle very soon and you can’t increase efficience by lowering the pressure further.
So, here the propeller comes into play, because it can push more air than the quantity stored in the bottle.
Now my new curiosity: if some kind of “air multiplier” (like the Dyson bladeless fan) or multi-nozzle arrangement inside an airfoil can obtain a similar effect, without moving parts.
Unfortunately, I am completely dumb in fluid dynamics so I can’t tell ;)
Conservation of Energy and Conservation of Momentum. You have a fixed amount of energy available. If you increase the amount of mass you move, you reduce the velocity you need to push it for the same momentum. Since KE is 1/2 Momentum * velocity, reducing velocity while keeping momentum constant, reduces the KE imparted to the air you’re moving, which reduces your energy expended, which makes your fixed amount of energy last longer.
I believe the it depends on the goal. If your goal is to produce a large quantity of lower pressure air, a nozzle is the way to go, look at the output of “bladeless” fans. If you instead want to create a lower volume of higher pressure air, you’ll need to have some mechanical compressor. If your energy source is compressed air, you’ll need to drive the compressor with it to get higher pressure.
Moving a larger mass at a lower speed gives you more momentum for a given amount of kinetic energy.
p = mv but e = 1/2 mv²
If you could mix a small amount of a volatile fuel with the incoming air and ignite it in the intermediate chamber just after the inlet closes, you could get waaay more pressure…
The hole in your diaphragm will wear out and air will eventually leak. A better design would have you glue the piston to the diagram. Place a check valve for filling and one for discharge, and you’re set.
Sounds like a two stroke engine.
Isn’t this basically how a diaphragm compressor works, but in reverse?
I like the 3D renders he makes, they really look like 3D printed parts just by using a striped texture!
Now I want to see a multi cylinder version.
There’s a three ‘cylinder’ diaphragm engine on Thingiverse, and has been there for a very long time. The problem with it is that the rotating valve that directs pressurized air to each cylinder is not sealed. Most of the air leaks away.
Why the gearbox? Loss of efficiency.
He wanted a design which would allow putting a propeller inline on the end of a plastic bottle.