Over the past years, additive manufacturing (AM) has become a common tool for hackers and makers, with first FDM and now SLA 3D printers becoming affordable for the masses. While these machines are incredibly useful, they utilize a slow layer-by-layer approach to produce objects. A relatively new technology called Volumetric Additive Manufacturing (VAM) promises to change all that by printing the entire object in one go, and according to a recent article in Nature, it just got a big resolution boost.
The concept is similar to SLA printing, but instead of curing the resin by projecting a 2D image of the current layer into the container, VAM uses multiple lasers to create intersecting points within the liquid. After exposing the resin to this projection for several seconds, the 3D model is built all at once. Not only is this far faster, but it removes the need for support materials and even a traditional build plate is unnecessary.
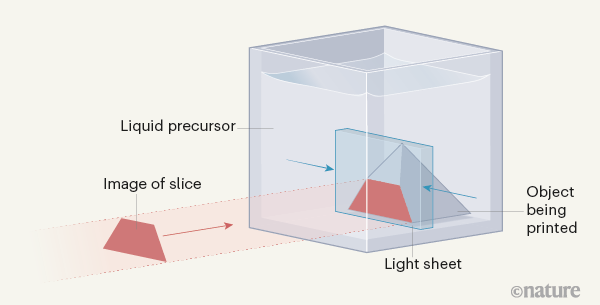
Up till now the resolution and maximum object size of VAM has left a lot to be desired, but in this new research by Regehly et al. claim to have accomplished a feature resolution of ‘up to 25 micrometers’ and a solidification rate of ‘up to 55 cm3/s’. They used two crossing laser beams of different wavelengths, one to form the ‘light sheet’ (blue in the graphic) and a second beam (in red) to project the slide onto this light sheet. They refer to this technique as ‘xolography’, as a mesh-up of ‘holo’ (Greek for ‘whole’) and the ‘X’ shape formed by the crossing laser beams.
Key to making this work is the chemistry of the resin: the first wavelength excites the molecules called DCPI (Dual-Color Photo Initiators) that are dissolved in the resin. The second wavelength when hitting the same molecules initiates the resin polymerization process. The object pictured at the top of the page was a test print; producing such a design on a traditional 3D printer would have required a considerable amount of difficult to remove support material.
While this is obviously not a technology hobbyists will be using to replace their FDM and SLA printers with any time soon, there are still many companies and institutes working on various VAM technologies and approaches. As more and more of the complexities and challenges are dealt with, who knows when VAM may become a viable replacement for at least some SLA applications?
Thanks to [Qes] for the tip.
This would be a whole lot more interesting if they made a resin that only reacted to a frequency that isn’t part of sunlight. The UV sensitivity really reduces the number of possible applications, regardless of it’s precision.
They’re limited one side by the lower power transmitted by lower frequencies, and the size of molecules needed to absorb them, and on the other side by the lack of high intensity coherent sources of reasonable expense, i.e. no top end of UVC laser diodes for cheap.
Not just that but there are other relevant factors at play as well. There are so many different possible resins available and they all react differently before you even start to combine them together. Oxygen inhibition and different specific chemistry to start the curing process are all relevant as well as things like random molecular motion and different temperatures and how the light moves about once inside the specific medium. What is the molecular weight of the materials and how does that impact things? Does curing material make it harder or easier to continue curing more material to the already cured material? Does it move around any as it is curing?
In other words, it’s actually really complicated. Plus if this is patented now, you will not likely be seeing it in cheap resin printers for two decades or more.
Very neat and eventually likely to very, very quickly generate high quality UV material outputs. Medical grade might be a bit harder of a requirement given the chemistry is already not exactly PEG based.
Your refferring to Beer Lambert. This processs does not utilize special amounts of oxygen. It utilized photo switch molecules. When Arnold makes the Predator Bleed Dem are PhotoSwitch Molecules Arrrr. Without the joking around accents these molecules can also store energy in liquid and solid state also which is more energy dense that Lithium Ion.
Once the resin is washed and cured, it is no longer ‘UV sensitive’. It may be UV degraded, but so are a large number of plastics and other materials. The only limitation it entails is not placing your UV-cure resin printer in direct sunlight, rather than any application limitations.
No thanks on resin printers. Sorry the materials are typically hazardous, and not engineering grade without paying considerable expense. And you are left with proprietary blends that are unknown to you the engineer. We have a Form3 printer.
They changed the resin formulation literally every few months (like it was some firmware model). So one month you would have a Tough V2 and then it would be gone and the next Tough V3 you buy would not work similarly. At all. We have a paperweight now we are so fed up with the machine. The mess too is not fun. I don’t see how they get around UV sensitive materials and if it is UV sensitive now it will be too outside limiting applications. People really should read up on UV resin toxicity.
While I understand your feelings on the hazards of working with 3D printing resin, there actually are quite a few good applications that 3D resin printing excels at. It all depends on your needs. For printing art, mold making, finely detailed prototypes, etc. there are few other technologies that can do it so cheaply at a relatively good speed. There are many resins out there, each with their own strengths and weaknesses (some are engineering grade up to a point, and while they cost more than other resins, for a company it is far from cost-inhibitive). Handling them requires proper preparation and protection, but nothing excessive or difficult, certainly not in a professional environment.
The experience you’ve had with Formlabs printers and materials doesn’t surprise me. It is a closed system, where you are indeed at the mercy of the manufacturer. But there are many other, much cheaper printers out there that provide good detail and can handle a lot of different resins, also from other manufacturers. The process might not be as polished as that of a Form3, but the absolute freedom, low price and good to excellent quality (if you make the right choices) make it flexible and easy. Pretty much an engineer’s dream.