[TinkersProjects] experimented with making their own flexible PCB for LED modules inside a special fixture, and the end result was at least serviceable despite some problems. It does seem as though the issues can be at least partially blamed on some knockoff Kapton tape, which is what [TinkersProjects] used as a backing material.
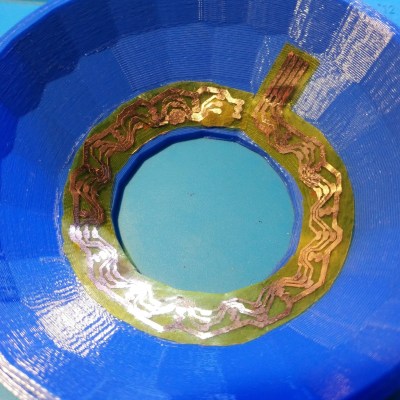
The approach was simple: after buying some copper foil and wide Kapton tape, simply stick the foil onto the tape and use the toner transfer method to get a PCB pattern onto the copper. From there, the copper gets etched away in a chemical bath and the process is pretty much like any other DIY PCB. However, this is also where things started to go wonky.
Etching was going well, until [TinkersProjects] noticed that the copper was lifting away from the Kapton tape. Aborting the etching process left a messy board, but it was salvageable. But another problem was discovered during soldering, as the Kapton tape layer deformed from the heat, as if it were a piece of heat shrink. This really shouldn’t happen, and [TinkersProjects] began to suspect that the “Kapton” tape was a knockoff. Switching to known-good tape was an improvement, but the adhesive left a bit to be desired because traces could lift easily. Still, in the end the DIY flexible PCB worked, though the process had mixed results at best.
Flexible PCBs have been the backbone of nifty projects like this self-actuating PoV display, so it’s no surprise that a variety of DIY PCB methods are getting applied to it.
DuPont Kapton FPC.
See IPC6013.
Fake Kapton sounds bad. I recently purchased one online so I should also check mine.
It might be a worth a try to switch to using a vinyl/craft cutter instead of etching. If the required features are not too small, which looks manageable from the photo.
yea, i want to try the vinyl/craft cutter. i was going to make one but just need some time to add the final touches into the cad model.
Great. Please post back here when you try. Curious how well it will go.
Been there, done that. The main problem i encountered was the adhesive on the copper foil. I could not find any copper foil with an adhesive that could withstand the heat. Some were better but none were perfect, far from it.
Modern flex PCBs bond the Polyimide without adhesive, but I don´t know if this requires a special treatment of the copper surface of PI surface, or both, and / or if it´s thermally bonded…
I wouldn’t be surprised if commercial flex PCBs skip the adhesion layer between the copper and Kapton tape.
Since if one deposits the copper onto the tape, then it has a fairly good bond to start with due to the depositioning process being far more adept at conforming with any surface imperfections.
Adhesives are generally temperature sensitive so are nice to avoid if one can.
But fake Kapton tape is also not a nice thing.
Though, Kapton tape will degrade if exposed to more than about 400 C, and a lot of soldering irons goes well above that, and some people like running their irons that hot, so could just be a PBCAK. (Not saying that this is the case, poor quality Kapton tape is a thing, I have stumbled over it myself.)
I made a “pcb” using 5 mil thick kapton tape and copper tape several years ago. The idea was to use it to connect DC powered 3D printer bed heater to the power supply – the tape would flex better than a thick cable. I calculated the copper tape width required for the current, then stuck two strips down next to each other on the adhesive side of a piece of kapton tape, then covered them with another piece of kapton tape leaving copper exposed at the ends of the strip for soldering.
I never pressed it into service, but it has been sitting in a box for a couple years and the tape is still stuck together and the copper still looks clean inside the tape.
https://1.bp.blogspot.com/-aD8XX-ZEXng/X_tT5X6KeqI/AAAAAAABTVE/aawEEPnEBBs3fYU5GNTaszbsG-h_WCZWwCLcBGAsYHQ/s16000/PXL_20210110_184214524.jpg
The problem with copper foil on Kapton is the adhesive that comes on the Kapton, which will melt when soldered. Traces will crash into each other when they float on molten adhesive. Still, it is possible to hand solder but requires a very steady hand and caution to keep traces away from each other.
Also, you can’t use acetone to remove the toner because acetone will dissolve the adhesive and lift off the traces.
The best solution would be to remove the factory adhesive that comes on the Kapton and replace it with one that is resistant to heat and acetone.
Proper kapton tape should handle soldering temps if you’re quick with the iron or use reflow soldering. Another option is high temp silicone, which will bond to both Kapton film and copper foil and easily handles soldering temps. Some of the higher temp silicones have metal fillers which can cause problems with circuits though.
IIRC, copper is an inhibitor for at least some types of silicon adhesive.
Let me guess…Made in China
However, they do produce quality viruses, 1,936,436 dead and counting, so do support them by buying stuff from them just to save a few coins.
That’s why you either get “Kapton” or “Krapton”.
ie. “DuPont” Brand or “Seagull” Brand.
Ha! I recently got a roll of import Koptan. I knew this going into the imported tape purchase. But when it arrived it said Kapton not Koptan. I never tested it’s heat resistance but will before assuming it is real PI.
How did you apply the toner? I was thinking here to print directly on top of the tape since it is flexible instead of using a hot iron.