The January 16th “Green Run” test of NASA’s Space Launch System (SLS) was intended to be the final milestone before the super heavy-lift booster would be moved to Cape Canaveral ahead of its inaugural Artemis I mission in November 2021. The full duration static fire test was designed to simulate a typical launch, with the rocket’s main engines burning for approximately eight minutes at maximum power. But despite a thunderous start start, the vehicle’s onboard systems triggered an automatic abort after just 67 seconds; making it the latest in a long line of disappointments surrounding the controversial booster.
When it was proposed in 2011, the SLS seemed so simple. Rather than spending the time and money required to develop a completely new rocket, the super heavy-lift booster would be based on lightly modified versions of Space Shuttle components. All engineers had to do was attach four of the Orbiter’s RS-25 engines to the bottom of an enlarged External Tank and strap on a pair of similarly elongated Solid Rocket Boosters. In place of the complex winged Orbiter, crew and cargo would ride atop the rocket using an upper stage and capsule not unlike what was used in the Apollo program.
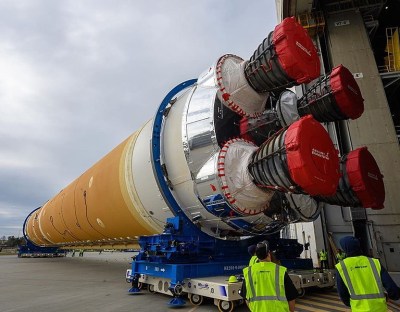
There’s very little that could be called “easy” when it comes to spaceflight, but the SLS was certainly designed to take the path of least resistance. By using flight-proven components assembled in existing production facilities, NASA estimated that the first SLS could be ready for a test flight in 2016.
If everything went according to schedule, the agency expected it would be ready to send astronauts beyond low Earth orbit by the early 2020s. Just in time to meet the aspirational goals laid out by President Obama in a 2010 speech at Kennedy Space Center, including the crewed exploitation of a nearby asteroid by 2025 and a potential mission to Mars in the 2030s.
But of course, none of that ever happened. By the time SLS was expected to make its first flight in 2016, with nearly $10 billion already spent on the program, only a few structural test articles had actually been assembled. Each year NASA pushed back the date for the booster’s first shakedown flight, as the project sailed past deadlines in 2017, 2018, 2019, and 2020. After the recent engine test ended before engineers were able to collect the data necessary to ensure the vehicle could safely perform a full-duration burn, outgoing NASA Administrator Jim Bridenstine said it was too early to tell if the booster would still fly this year.
What went wrong? As commercial entities like SpaceX and Blue Origin move in leaps and bounds, NASA seems stuck in the past. How did such a comparatively simple project get so far behind schedule and over budget?
The Rocket to Nowhere
Arguably, the most pressing problem with the SLS program is that it has no clear purpose. As a congressionally mandated project, NASA must continue on with its development regardless of whether or not they actually have a use for it. Critics have often referred to the program as the “Senate Launch System”, as they believe the Shuttle-derived concept was conceived primarily as a way to make sure the manufacturing facilities used to build the engines, propellant tanks, and solid rocket boosters for the Space Shuttle would remain in operation even after the program was retired.
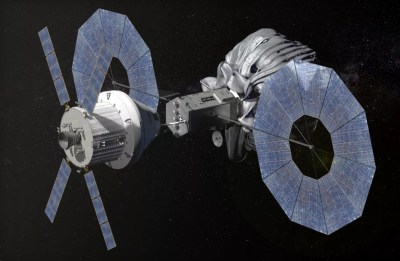
Without a clear mission for the SLS, it’s been difficult for NASA engineers to make any long-term development plans. What payload does the booster need to carry, and to where, are key questions that need to be answered. NASA is no longer pursuing the mission to recover a near Earth asteroid, and a human mission to Mars is still decades away. The SLS is scheduled to launch the Europa Clipper to Jupiter in 2025, though the Falcon Heavy is already being considered as a backup should it not be ready in time.
While its ultimate effectiveness is debatable, the design of the Space Shuttle was driven by a very specific goal: to transport large objects to and from low Earth orbit inside of its cargo bay. Every decision made during the program’s lifetime revolved around that core tenet. Without similar guidance, the Space Launch System has found itself adrift.
Put simply, the single defining characteristic of the SLS is the sheer mass it’s capable of putting into space. The rocket’s base Block I configuration is designed to put 95,000 kg (209,000 lb) into low Earth orbit, and the later Block II version 130,000 kg (290,000 lb). But while these are impressive figures, it’s not immediately clear what type of mission architecture would require such massive modules to be launched in a single-shot. The 50 years of experience gained since the Apollo era has taught us that modular systems, launched on competitively priced boosters and assembled in orbit, is the key to creating a sustainable space infrastructure.
Squandered Reusability
From the beginning, the Space Shuttle was designed to be an almost completely reusable architecture. Aside from the External Tank, every component of the system could be recovered, refurbished, and flown again. The idea being that it would be cheaper and faster to reuse the same vehicle than it would be to build a new one for each mission.
Unfortunately the complexity and cost of the refurbishment process was greatly underestimated, due in part to technical and material limitations of the era. In the end, the Shuttle never launched as affordably and as rapidly as its designers had hoped, but the lessons learned during the program helped shape modern reusable spacecraft such as Sierra Nevada Corporation’s Dream Chaser and the Boeing X-37B.
But despite the current trend towards reusable rockets and spacecraft, NASA is taking a step backwards with the SLS by using components which were designed for refurbishment and discarding them the end of each flight. The RS-25 engines installed on the first SLS rocket are not newly manufactured, they are literally the same engines that were pulled from the Shuttle Orbiters when they were put into museums. The same is true with the Solid Rocket Boosters (SRBs); the new elongated boosters are using segments from the Shuttle’s original SRBs, but instead of coming down on parachutes to be recovered, they will smash into the ocean and sink.
Each flight of the SLS will destroy four Shuttle-era RS-25 engines and two SRBs, simply because they were taking up space in a NASA warehouse. From a historical standpoint, this is abhorrent. But more practically speaking, integrating these decades-old components into a modern launcher has proven to be far more difficult than anticipated. While they’ve seen some upgrades since the retirement of the Shuttle, it’s no exaggeration to say that some of the people working on the SLS today were not born when its engines were built.
As of right now, NASA only has enough RS-25 engines leftover from the Shuttle program to support four SLS flights. To address this, the agency has already contracted Aerojet Rocketdyne to produce a new version of the engine called the RS-25E that’s designed to be expendable. Unfortunately, these design changes come at a steep price. Each RS-25E will cost NASA nearly $150 million, which is more than what SpaceX charges for a flight on the Falcon Heavy. With a per-launch price that will easily exceed that of the infamously expensive Space Shuttle, it’s difficult to imagine how SLS can possibly remain competitive with reusable commercial vehicles set to begin operation within the current decade such as SpaceX’s Starship and Blue Origin’s New Glenn.
A Calculated Risk
After examining the data, NASA says the automated abort during the January 16th engine test was due to intentionally conservative test limits intended to avoid unnecessary stress on the booster. In a press conference, Administrator Bridenstine said that had this been a real flight, the engines would have remained firing for the full duration necessary to reach orbit. He went on to explain that there is an inherent risk involved should NASA or prime contractor Boeing decide to rerun the full duration test fire, as the propellant tanks can only be filled and drained a finite number of times.
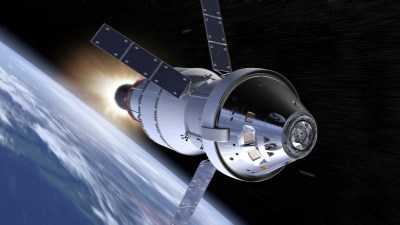
While nothing has been determined yet, these statements would seem to indicate that NASA may decide not to repeat the test fire and push ahead with the Artemis I mission to ensure they make the current November 2021 launch date. Conventional wisdom would say this is unwise, but as the first flight won’t have any human occupants, the usually risk-averse space agency might be willing to roll the dice if it means they can avoid another costly delay on a program that’s already facing fierce criticism.
On the other hand, live streaming the explosion of their first Space Launch System rocket to millions of viewers all over the world is hardly going to improve matters. A catastrophic failure during Artemis I would also very likely result in a delay to the crewed Artemis II that’s tentatively scheduled for August 2023. The resulting domino effect would likely make it all but impossible that NASA could make the already ambitious deadline for putting the first woman and next man on the lunar surface by 2024.
In other words: Orange Rocket Bad.
Orange is sus (still)
Leave it government agencies can’t do anything right
I can’t believe there going to destroy historical artifacts and literally rip the engines of museum space shuttles. Go Starship. And as for the Senate luanch system; GO HOME!!
Ever have a project, that seems similar to something you recently abandoned, and think I’ll just re-use that.
Hours turn into days, and about 80% of the way in you realize it would have been quicker to start from scratch. Some of the stuff is like 90% right, but of course, the last 10% takes 90% of the time.
So here we are, a bunch of reused parts adapted for something they weren’t intended for and it doesn’t quite work.
My experience is that the last 5% uses up 95% of the time.
So now I always focus on the edge cases or the outliers, the real time sinks near the very start. I filter the work required into easy and very difficult and start. With enough experience you have a extremely good feel for what is going to be trivial and what is not. And then I focus my attention on that last evil 5% at the start. It actually helps you find where the problems are that you were not expecting in the 95% faster. And then at the end of a project when you do 95% of the work in 5% of the time, people think you are a miracle worker. But the flip side is that at the start of the project people think you are twiddling your thumbs, because progress is almost glacial.
The last 5% takes 95% of the time. So does the first 5% and the middle 90%. It’s the NASA way. Take an incompetent prime contractor mandated by politicians, excuse all failures and give them the full fee regardless of success or failure or late delivery or cost overruns. Today’s NASA is not the same as the the one that got us to the Moon.
After 40 years of doing software engineering for NASA, etc., I can say that you are exactly correct in describing the successful development process. Been there, done that.
SLS not working for them?
Maybe they should try a different 3D printer type.
+1
I am not the only translating it that way in my mind….Why NASA thinks a plastic rocket will not catch fire is beyond me.
What about FFF
Hmmm solid boosters that have a documented history of failing, re using old technology, insulation falling off the fuel tank… WHAT COULD GO WRONG?
If you want NASA to resume it’s world class prestige, treat it like a world class agency not like a 3rd world ugly red haired stepchild.
Think about what you said for a minute, solid boosters, fuel tank.
The issue was solid boosters next to a fuel tank (especially if they are using NOS o-rings to save money)
The space shuttle did not explode. It tilted out of axis with aerodynamic forces due to the lower bracket on the right SRB being melted away and released the pressurized fuel into the atmosphere in a rapid way. Had it exploded it would have been a nuclear bomb like force and would have been felt on the ground.
Dale, if you believe that, then you either weren’t there or don’t remember what you saw. I saw it with my own eyes in the sky. It was an explosion. The craft was far out over the ocean when it happened. It was also high enough that it was way above the tree line from my viewpoint on the WEST coast of Florida, in the town of Lutz.
“solid boosters that have a documented history of failing,”
Only one SRB, singular, failed. It’s a history of one failure that was documented and the cause resolved, not an ongoing failure.
“insulation falling off the fuel tank… ”
Missing insulation on the fuel tank was never a problem. A thermal protection system in the path of falling foam was the problem. Orion’s thermal protection system is on top of the SLS, out of the path of falling foam. SLS/Orion does not repeat the STS mistake of side mounting the spacecraft.
Looking at previous missions before the “one that failed”, during the refurbishment of the boosters it was well documented that the o-rings were getting worn down more than they should have, and it was only a matter of time before they completely failed. It was not a completely unexpected situation when it failed; not to the engineers that knew about the problem (and they had to hold their breath and hope it didn’t fail when their superiors told them to show proof as to why it will fail, rather than an indication that it could fail)!
Yes. There was more than one “unexpected venting” doxumented before Challenger. Those thankfully veneted in directions away from the SRB and Orbiter.
There were many close calls with the srb’s too and problems were lucky didint occur.
The shuttle program was predicted to fail with loss of the entire crew on one out of 25 missions. From wikipedia: STS-51-L was the twenty-fifth flight of the Space Shuttle and the tenth flight of Challenger. The Columbia was lost on the 107th mission overall and was Columbias’ 28th mission. We should not have been surprised that either of these happened.
I wouldn’t say the SRBs were unreliable.
The key is that the insulation hit the part of the ship that needed to reenter the atmosphere. If the crew capsule is above or more accurately forward of the fuel tank it makes no difference if foam or ice falls away from the fuel tank. In fact if you look at the classic Apollo launch film it reminds one of an iceberg calving. There’s probably a literal ton of ice coming off.
Counter intuitively, one of the problems they had occasionally was that the humidity in Florida was too LOW as high humidity would produce water and low humidity would produce ice.
Software problems with another Boeing product? Who would have thought that? God help any astronaut flying on this frankenstein fossil which exists solely to funnel money into specific states. They have to delay to keep the gravy train flowing. However, astronauts will probably need to speak Chinese when they visit the moon.
Reminds me of the torpedo fiasco of WWII (in the U.S), the manufacturer was “protected” by their Senator, so they had no incentive to improve the lackluster performance of their product.
The Germans on the other hand, had state of the art torpedoes with all the latest technology. They still lost the war though.
And Operation Paperclip happened, the spoils of war – kidnapping people.
“kidnapping people”
They intentionally moved within Germany to be captured by the Americans instead of the Soviets, so it wasn’t “kidnapping.” Who wouldn’t gladly move to the untouched US mainland rather than stick around in obliterated Europe? And who was going to have the big bucks available to further develop their favorite toys? Based upon what happened later, they made the right choice.
The rocket goes up and where it comes down is no concern of Werner Von Braun.
That was because while they made better materials, they couldn’t manufacture it in quantities greater than the US could. In this situation, ULA can’t build their archaic parts faster than SpaceX can their new parts that work as well if not better.
When your opposition can not only build better than you can and build more, you are going to have a hard time. SLS is just another example of what Senators can keep alive with enough graft to line their pockets.
It’s also due to a legacy aerospace manufacturer’s bloated infrastructure and bureaucracy accustomed to cost-plus military contracts. Besides the direct issues that causes, new engineers who want to think and do outside the box don’t want to work there.
Actually the Germans had state of the art acoustic torpedoes and somebody figured that hauling pipes on a robe behind the ship would decoy the torp, let’s not discount Allied technology (and cleverness.)
A big problem is that Boeing is not the same company it was during the height of the Apollo and Shuttle eras. It used to be a company run by air plane people not cost cutting MBA’s who live a thousand miles away from where the factories are and come up with a disaster like the 737 MAX and using cut rate foreign programmers to write the avionics s/w and importing 3rd world foreigners to manage the company day to day.
While companies like Space-X that are not infested with institutionalized stupidity and greed just keep having one success after another.
+1
Building a new race car? Great!
We’ve got a warehouse full of Model T engines and crate of Model A transmissions. Save money by using these…
Back in the day in Formula 1, the BMW team used to take engine blocks out of used street cars and leave them outside in the rain for a year, and the pit workers would piss on them for good measure, before they were finally taken in and bored and honed etc. into racing engines.
Point being that the engine was taken from the middle of the bathtub curve for failure – not too early, not too late, and it was stressed with water ingress, corrosion and and freezing to find any residual faults like microscopic cracks that would develop into bigger cracks during a race.
Citation please. I’m very doubtful that since it’s founding in 1950 no F1 engine has even shared an engine block design with a road car. The idea that they would them deliberately abuse is sounds ridiculous.
This sounds like another dude special load of bs
The engine he’s referring to is the BMW https://en.wikipedia.org/wiki/BMW_M10 in its https://en.wikipedia.org/wiki/BMW_M12 variant.
The story about peeing on the blocks is repeated endlessly in BMW circles, but I’ve never seen a good reference, just internet stories.
(I have two M10’s in my garage. I have not peed on either.)
I forgot that hackaday doesn’t like to have links and disappears replies that have citations.
The engine Dude is referring to is the BMW M10, in its M12 variant. They used the same block casting in the BMW 2002 and in Formula One for the Benneton and Brabham teams.
The story about repurchasing used engines, leaving them outside, and peeing on them, is repeated endlessly in BMW racing circles, but I’ve never seen substantial verification of it, just links to other people telling the same stories.
I have two M10’s in my garage, and have never peed on either. They are ferocious engines, though.
BTW it was and remains a source of amazement to me that the M10 was designed in 1959-1960, went into its first car in 1962, and _twenty five years later_, was the most powerful Formula One engine ever raced. The same block that was in every BMW 316, 318, and 320 (which are still all over the road) was pouring out something like 1400 horsepower in F1 in the late 1980’s.
Mine are for sale if you’d like one. Or two.
Thanks, interesting read! So I was at least half wrong :)
If Chinese had to change their plans for the Great Wall every 4 years, nothing would ever get done. Just sayin …
The great wall was built in thousands of sections in an number of different plans under different emperors over many centuries, starting and stopping, until finally the sections grew large enough that they were connected.
https://empoweryourknowledgeandhappytrivia.files.wordpress.com/2015/05/great-wall-of-china-construction-timeline.jpg
Okay, it wasn’t the best comparison. Now, imagine building a rocket in that manner. 2000: we will go to the Moon. 2004: Not Moon, Mars. 2008: Asteroid belt and maybe Skylab II. 2012: Europa! 2016: Moon …
SLS has been in development for about a decade, and Orion longer than that. The plans for what those vehicles should be have not changed every 4 years.
How long did it take from funding approval to Saturn V’s first flight?
Apollo was a deathtrap. Far more dangerous than the Shuttle. However, we had a defined goal and determination to get it done. 3 dead astronauts would not keep us from the moon. The crew capsule had to be redesigned because the way it was wired was dangerous. That was the real story of Apollo, having to redo that in about year.
Twenty billion dollars
$20,000,000,000
That budget would get you 322 Falcon 9 launches, or 222 Falcon Heavy launches.
This is a national embarrassment. They need to end it now.
Comments found elsewhere about the SLS (Senate Launch System):
“$17 BILLION dollars.” and counting. 2011-2019 SLS + Constellation = $28 billion. “Office of Management and Budget Russell Vought estimated the cost of a single SLS launch at ‘over $2 billion per launch’ — and that’s excluding development costs.”
“SLS needs to fail just enough to maintain a credible promise to keep getting funded. It’s primary purpose is to keep ex shuttle rocket infrastructure employed, not to provide a competitive launch system.”
I used to work at the Space Center . This concept was designed using outdated tech. and was really a reason to keep the NASA employees employed. NASA should do what they do best, mainly space exploration, Mars rovers etc.. Private contractors can build and launch vehicles MUCH cheaper.
This is exactly it. SLS wasn’t a practical solution, it was a way to “save” money by using existing hardware, that was paid for already and existing support systems and personnel. SLS has always been a turkey of a launch system, destined to never or barely fly. No way do we go to the moon on this system (should we is another conversation..). All the money…billions spent on SLS down the drain. If our goal was to actually accomplish things, we would’ve taken the money and funded SpaceX, New Origin and so on… But the goal is to create a bureaucratically messed org that is NASA and its companion government agencies. I love my fellow NASA employees, we really are trying to do good work within the boundaries set for us. SLS’s boundaries are far too oppressive and limiting to ever succeed.
“a reason to keep the NASA employees employed”
It was to keep the entire Shuttle manufacturer infrastructure employed including even the Shuttle SRBs.
I fail to see the reason for a super heavy lift vehicle. Mate together whatever you need in orbit. The as yet imaginary SLS Block II will supposedly put 290,000 lb in LEO at an estimated $2 billion per launch not even including amortized huge development costs. Falcon Heavy with recovered side boosters can do 126,000 lb. Two FH payloads mated in orbit gets you 250,000 lb in LEO for $260 million total. Close enough and for less, possibly far less than 1/10th the cost if SLS development costs are included.
“I fail to see the reason for a super heavy lift vehicle. ”
Haven’t you been reading the comments on the “other” NASA article about how much food and water will be needed to send (and return?) a human crew to Mars?
B^)
Which is exactly why, for the foreseeable future, sending people is nothing but a political goal that has nothing to do with cost effective research
“Each flight of the SLS will destroy four Shuttle-era RS-25 engines and two SRBs, simply because they were taking up space in a NASA warehouse. From a historical standpoint, this is abhorrent.”
This is making me sick… Just pull the plug on this failed project, put these engines where they belong (i.e. : in a museum) and use commercial launchers. I know that this wasn’t yet an obvious idea when the SLS project started, but things have changed and, you know, sunken cost bias and all that.
But then of course, politics…
Great article, thanks.
The irony is Boeing could do the same thing as Space-X by simply creating a walled-off skunkworks.
But bean counter got to count beans.
Much as NASA irritates me with their glacial wastefullness, I do want to point out that it’s not really fair to compare them to Space-X.
Space-X can do what it does because it’s funded by a guy who understands that if you want to move fast and do something new, then shit is going to blow up once in a while. That’s just the ground truth, and he’s OK with that.
NASA can’t do that.
They _used to_ be able to do that, back in the 60’s when we were in the middle of the cold war, and the space race was a thing, but now that spaceflight is “routine” everybody expects their taxpayer-funded rockets to just work. Like an airplane, but pointier.
_Even if_ today’s NASA wasn’t run by craven bureaucrats mostly interested in preserving their fiefdoms (spoiler- it is), and
_even if_ today’s NASA wasn’t beholden to craven politicians mostly interested in preserving jobs in their districts (spoiler- it is), it still couldn’t survive the accusations of wasted tax dollars that come with big public “failures”.
Space-X can push out a YouTube compilation of a dozen of their rockets disintegrating to jaunty music, and everybody digs it.
Elon Musk can go on 60 Minutes and when Lesley Stahl asks him “A lot of your rockets explode” he can shug his shoulders and reply “Yeah, That’s probably because they’re full of explosives”
But Jim Bridenstine can’t do that. If something fails – a project, a rocket, a plan – he gets to sit in front of congress and answer to some smarmy senator dripping feigned outrage about NASA waste, just in time for a 90 second clip to make the evening news in his home district.
Hence, we have the SLS, a rocket sans mission, but, like many things in government, a project that is just too big to walk away from.
They should not have any rockets at all (except of small experimental ones when testing bleeding edge engineering). They should just contract launch providers.
But engineers in states like Alabama would be out of job and would need to move and find new jobs and even if they did they wouldn’t wote for their politicians again so why would the politicians wan’t to commit suicide with killing the SenateLaunchSystem.
Senate Launch System? Brilliant. Launching senators on this thing (all of them, first flight) is a great idea.
reminds me Ark Fleet Ship B
Those engineers could remain employed by NASA to help the rocket companies, maybe. IIRC, Relativity has a contract with NASA to test their rockets at Stennis. Presumably NASA’s engineers at Stennis do, or could, provide some help with the rockets. It could work like that, just with more than one company. Then the engineers would still have jobs, and they’d even have more fulfilling jobs, working on rockets that are worthwhile.
And so it begins – These articles and many like them over the past few months remind me of others regarding a major aerospace program I worked on and supported for several years – As such articles became more prevalent along with a new administration, that program was canceled – Thousands upon thousands of Contractors lost their gigs – This program was called Constellation (CxP) and was the predecessor to SLS – It too was behind schedule and billions over budget exactly where the SLS Program sits now – Seems to me the writing is already on the wall, once again…
Give SpaceX $2 billion to change its name to “NASA.” Fixed.
Now THIS would be a truly elegant hack.
SLS is the perfect rocket, for the 1980’s when it was initially proposed to base a super heavy lift rocket on Shuttle system parts. What could have been done was building a big space station atop an external tank, and permanently attached to it.
Have the main engines under the tank, and made to be demounted in orbit and brought back by a Shuttle. With some modifications made to the tank for cutting holes, flanges could be mounted for attaching docking ports. Threaded bungs could have been welded on various places on the exterior, with pop off insulated plastic covers. Either bolt things on as they are or drill through the skin for a pipe connection or screwing in a sealed connector for wiring.
The potential was there for launching a space station in one shot, like Skylab, but with a massive “unfinished basement” that could be expanded into.
But the government wanted the *International* Space Station. Could have sold empty Tank Stations to other countries to outfit as they desired, then docked them all nose to nose, or in a ring, or…
But now NASA is finally sort of pursuing that idea, too much, too late. If they want to see the thing fly AND have uses, privatize it all. One thing it’s huge lift capacity could be good for is launching ships that will stay permanently in space and do things like cycle back and forth between Earth and Mars to ferry cargo and when the trip time is shortest, take people there and back. The ‘cyclers would not, could not, ever land. They’d need rockets like SpaceX’s big one to move cargo and people up and down.
Some kind of massive interplanetary spacecraft is definitely a viable SLS payload, maybe even the only one, but it just doesn’t make sense to build them that way. Why risk everything on a single launch, when you could build it from smaller modules launched on an array of cheaper commercial rockets?
It’s the Skylab vs ISS comparison. It was definitely convenient to launch one massive station on a Saturn V and call it a day, but it didn’t offer the long term upgradability you get with modules.
One thing it’s huge lift capacity could be good for is launching ships that will stay permanently in space and do things like cycle back and forth between Earth and Mars to ferry cargo and when the trip time is …
We will have funded 7 more new rocket projects before we have any need for that. The SLS will be in museums… if that
First off sls is usless cannot send orion and a lander to the moon on one shot Spacex starship will accomplish this when they get final heavy booster and star ship ready plus star ship is large enough to carry a crew to moon and mars and return on its own You cant send orion on a mission to moon or mars without a lander and orion is to small for a crew to spend a voyage of 8 months to mars even with a lander attached food and water orion to small Spacex starship is feasible and will work They have to give spacex nasa funds forget orion lets get going now
In reading the replies to this blog, I inadvertantly hit ‘report comment’ while scrolling. Twice. And once in another blog. I apologize.
Erin
No worries!
“has proven to be far more difficult than anticipated…”
Really?!?! Who anticipated that it would be easy? Seems like any expert they would have asked probably told them it would be at least this difficult.
The SLS is meant for one thing only. To funnel money into the “industrial military complex” and by extension of that to provide senators with jobs on the way out.
Everything else companies like spaceX and the other new companies can do faster, cheaper and better. And in some cases reusable.
It’s my understanding that US astronauts are highly unimpressed with solid-propellant motors, except maybe for small ones such as retrorocket motors. With liquid propellants the motor itself can be examined and tested readily and repeatedly. By contrast, every solid motor is essentially a new motor. Although some parts can be reused, the solids motor underneath that astronaut team cannot be tested. Any tests were done, not with *that* motor, but with an identical motor made and filled with the same propellant.
The propellant is examined minutely, even x-rayed to ensure that there are no significant cracks, bubbles, or other defects. But the larger the motor the more likely it is that a serious defect could be missed.
A friend of mine works in aerospace technology, specifically in solids. For a particular mission to another planet the company made a hundred small solid motors from a design already proven. The two motors that were actually used were selected at random. This increased greatly the likelihood of both motors being defect-free……having a tech pull a bad motor and replace it is kind of hard and expensive when the item in question is orbiting Mars…..
I’m not against solids. In fact I’ve made a fair amount of APCP (ammonium perchlorate composite propellant) myself, and even wrote about prep, construction, and testing of small motors (http://www.compositepropellantbook.com/). I’m unfortunately very aware of what can happen when a significant defect exists in a solid motor. :-(
Large solids do have a place in commercial rockets…but generally speaking, not in a man-rated vehicle.
Well, I don’t see military solid propellant rockets falling very often in a catastrophic way.
At least not outside the intended payload-induced failure at the end of each flight. :)