Over the last couple of years, we’ve seen massive price reductions on consumer 3D printers based on masked stereolithography (MSLA) technology. As the name implies, these machines use a standard LCD panel to selectively mask off the ultraviolet light coming from an array of LEDs. Add in a motorized Z stage, and you’ve got a simple and cheap way of coaxing UV resin into three dimensional shapes. These days, $200 USD can get you a turn-key MSLA printer with resolution far beyond the capabilities of filament-based FDM machines.
But [JD] still thinks we can do better. His project aims to produce a fully-functional MSLA printer for $30, and perhaps as low as $15 if manufactured in sufficient quality. He believes that by making high-resolution 3D printing more accessible, it will allow users all over the globe to bring their ideas to life. It’s no wonder he’s calling his machine the Inspire 3D Printer.
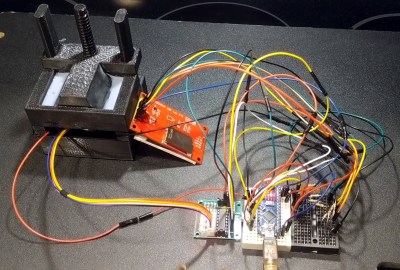
This isn’t just some pie in the sky concept rolling around in [JD]’s head, either. You can order the Inspire Development Kit right now for just $30, though he makes it clear what you’ll receive isn’t quite a functional MSLA printer. By leveraging a common LCD module, the ESP32, and several 3D printed parts, he’s proven his price point for the kit is achievable; but there’s still plenty of work that needs to be done before the machine is ready for the general public.
For one thing, he’s still working the kinks out of the Z movement. The current design is 3D printed, but [JD] says he’s not quite happy with the amount of slop in the movement and is considering replacing the entire thing with the linear actuator from an optical drive. We’ve already seen these parts reused for accurately positioning lasers, so there’s certainly precedent for it. The firmware for the ESP32 is also in its infancy, and currently only allows the user to print from a selection of simple hard-coded shapes as a proof of concept.
We’ve seen DIY attempts at resin printers in the past, but they’ve often been based on more complex techniques involving projectors or UV lasers. Masked stereolithography is much more approachable for the home gamer, and projects like the Inspire 3D Printer show just how little it really takes to pull solid objects out of a puddle of goo.
The kit purchase page requests zipcode. Are you shipping beyond the US ?
Qbert?
Not sure if those optical drive mechanisms will have the force needed to peel the model from the vat surface. I guess for models without much surface area, they may work okay.
Some resin printers have 2 distinct mechanisms – one to advance the Z axis and one to tilt the tray, breaking the vacuum seal against the FEP surface. It might be feasible to use a small solenoid to tilt the plate (small angle, large force) while the CD positioner is used only for the axis movement.
Also, if you’re trying to print a straight and smooth part, why not align it in the direction the printer prints the straightest and smoothest? (ie, not in the Z direction)
The problem isn’t gravity as much as it is mechanical. You’d need some pulling arm on some axis, and that axis would have trouble as long as the mechanical parts are causing the issue.
I was referring to the Z tower in the pictures above. I think this part probably just needs to be metal. Perhaps some kind of roller carriage might work on a metal box section. The stepper could use a belt to raise and lower it. Or perhaps a cable around a capstan.
Until there’s an inexpensive non-toxic resin with no post-print cleaning and trash disposal problems, I’ll pass.
Yup, and the SLA resin is pricey.
I’ve used some plant-based resin from anycubic. It cleans up with soap and water and I believe is non, or at least less, toxic. It’s still expensive (£38 per litre, and went up during lockdown) but I guess wider use and competition would reduce that.
So wash it in the dishwasher and cure it in the sunshine (or under a small array of UV leds for those of us in cold places)
I don’t think the toxicity stuff is a big deal any more.
It’s not non toxic. Maybe read the MSDS instead of just rinsing toxins down the drain?
Water washable and plant based, are really just marketing term BS
I agree toxicity needs to be dealt with correctly. That’s mostly a matter of process and knowledge : there are plenty of toxic substances in use safely with proper procedures.
Certainly ‘plant-based’ can be BS. However, water-washable isn’t. Yes, you may need to dispose of the wash water responsibly but the fact that you’re using soap or detergent and water as the agent is a significant simplification for both disposal and handling compared with the proprietary organic solutions that people like 3D supply.
I have used anycubic plant-based resin. It washes off in detergent and water. Maybe just a dishwasher and a small bank of UV leds is all you need ?
Elegoo now has a water washable resin too.
The Elegoo water washable resin is a great example of the problem. The MSDS is clear that it is toxic to aquatic life, yet the Elegoo ads often show people washing prints in their sink. The water/detergent washable resins make people think this is reasonable when it’s frankly terrifying. At least with IPA rinse, you have to consider the waste disposal (though internet comments make it clear that people still dump this down the sink.) The cumulative exposure issues that are common with resins require education that just isn’t happening as the excitement around resin printing grows.
Many of the MSD sheets require looking up the MSD sheets of the sub components. Anyone interested in learning the scope of the threat shoud spend a few minutes going down that rabbit hole and looking up the results of the standard Zebrafish Embryo tests used to understand the aquatic toxicity. Between recreating the problems that old fiberglassers learned (cumulative hyper-sensitivity,) and making our drinking water toxic, resin printing is dramatically more dangerous than the internet wants it to be.
Some of these resins are toxic while uncured but fine once cured. This just means you need to cure it before disposal. In fact, I often do cure it with a UV flashlight – it makes cleanup of certain problems, such as sticky tools, easier.
Bear in mind that many of these resins are based on dental casting resins. Although I think they’re often used as an intermediate stage, so the resin castings are not in fact used orally, it would be necessary to have a cleaning process that satisfies the medical regulatory bodies.
The problem we found at our engineering workplace is that the resin never stops curing and gets more and more brittle overtime. We had a Formlabs Form3 that worked great for a year and then began failing prints. We think a few firmware updates that weren’t tested well ruined it. It is now a very expensive paper weight. Unless you are printing cheesy, cliche figurines, or have a very specific use case like dentistry, I’d avoid resin printers like the plague.
There is definitely some truth in this. But ultimately it’s down to the resin manufacturers. I’m sure if the problem is amplifed they’ll pay more attention to this. UV deterioration of plastics is, after all, well documented.
$30 – Hmmm. So this is the “seed” that spawns an MSLA 3D printer that replaces a $200-$300 ready-to-go off the shelf MSLA printer. Then you still need a wash and cure machine (~$140), a bottle of SLA resin ($35-$40 per 1kg), and gallons of 99% isopropyl alcohol ($19 per gallon for 4 gallons bought at once. A high price due to the SARS-CoV-2 virus.) All the prices are from Amazon and include “free” ConUS shipping if over $25 or with Prime. Ideally you would also need to build a see-through UV blocking cover for the home-brew printer that blocks the correct wavelength. You might be able to use the cover from the wash and cure machine, but who knows if it is blocking the correct wavelength? Also you won’t be able to wash and cure while you are printing. So you are saving around $100-$200 off a roughly $500 ready-to-go off the shelf starter setup with (probably) a larger build volume. And I didn’t even consider a fume hood solution.
You certainly don’t NEED a wash and cure machine, in fact, I’d be willing to bet only a small percentage of resin printer owners actually have a dedicated machine for it.
Spot on. I have one but it’s a luxury and I lived with out one for a year. And the curing is quite frankly rubbish and too short.
At the height of the isopropyl buying spree I was still able to buy bio-alcohol at uninflated prices.
Costco IPA seemed to be back down to 2019 price.
That’s an incredibly elaborate, contrived argument that I’m not sure if you read the article, or you are compulsively driven to impress.
Had you read, it’s a POC (Proof of Concept)… made obvious by the fact it hardcodes certain shapes only. I can’t see how any regular reader of HaD would conflate such an early work against finished commercial projects. You do know that all POC projects – even in established manufacturers – are ugly pieces of specific function designed to test one idea?
I doubt less than half the SLA printer owners have a UV box. You certainly don’t, if you don’t see how unnecessary they are (or that you can just borrow or buy a much cheaper “UV nail station” for $15. (yeah, exclaim “This almost DOUBLES the price of the printer”, nobody expects that!)
What exactly is “ConUS” shipping? Is this some sort of troll dig at the people who work for the USPS? Your post reminds that HaD needs a blocking function.
I think ConUS is just a shortening of Continental US shipping. In other words free shipping to any state but the two hardest, Hawaii and Alaska.
You wouldn’t need a see-through UV blocking cover as there won’t be anything to watch. If you really wanted to build one polycarbonate’s a Home Depot item.
I agree that with any body of work with this stuff your consumables dwarf the cost of the machinery, making this a nice exercise but impractical as a cost saving measure for the process.
I was thinking that. Why would you risk wasting those supplies on failure or a lower quality print when the real printer is $200-$500 and one set of consumables is a significant percentage of that. Mostly this would have to be a project done for novelty, like making an led pov wand.
So, other commenters already pointed out the cure and wash station is not needed. But even if it was, how hard did you look on Amazon? They can be found for $50 on there… And alcohol is just not that expensive. Go to your local walgreens. There are other places to buy things than amazon. Believe it I r not, they don’t have a monopoly on beat available price.
Also who uses GALLONS of isopropyl? You should be reusing the alcohol and cleaning the resin out when it gets cloudy.
While you are correct that the printer itself is not the only expense, it seems entirely reasonable to me to work on expenses associated with one component of the system at a time.
There’s some information about building your own resin printer here https://thedigitalocean.wordpress.com/
[JD] should look into Bart Dring’s port of GRBL for the ESP32, it works well https://github.com/bdring/Grbl_Esp32
The brilliance of Resin LCD printing is that you could use as large a panel you want and the time to build still only goes up my layer size. Why not use a flat screen TV and make a huuuuuuuuuge model all in one go?
There’s an element 14 buid with exactly that idea.
He has many things to say about it but essentially it boils down to it is a royal pain.
Has anyone ever used that basic technique, blocking UV with an LCD, to expose PCB artwork for etching? Board size would be limited to the LCD’s dimensions, but just lay the PCB on the LCD. Very simple.
That’s an interesting idea. My laser printer is currently dead so I can’t make DIY PCBs, but I might be able to try thins with a DLP resin printer. Very interested to hear if anyone else tries it.
I’ve been looking for an excuse to buy a resin printer, but this could also be done, using custom software, by using just a replacement LCD for one of these printers backed by DIY UV LED array. Of course, as cheap as these printers are getting, it might be cheaper and easier just to use one of them for this purpose.
The LCDs are pretty cheap, though, US$24 shipped in this case:
https://www.amazon.com/Creality-2560×1440-Resolution-Compatible-ANYCUBIC/dp/B0882V5KVD
Its pointless trying to reduce the cost of the printer. The main cost of resin printing is the resin. Risking a poor quality print on a cheap machine would end up costing more than just using a reliable machine.
What’s a reliable printer ?
I’m running a $15000 3D Systems printer and have wasted plenty of resin. Development is worthwhile.
Very tempting to read into and feed the desire to learn more… however, that comes with spending more and focusing what I’ve spent on. Though man…, $15-$50… will read at a later date.