Sales of electric vehicles continue to climb, topping three million cars worldwide last year. All these electric cars need batteries, of course, which means demand for rechargeable cells is through the roof.
All those cells have to come from somewhere, of course, and many are surprised to learn that automakers don’t manufacture EV batteries themselves. Instead, they’re typically sourced from outside suppliers. Today, you get to Ask Hackaday: why aren’t EV batteries manufactured by the automakers themselves?
Experience and Infrastructure
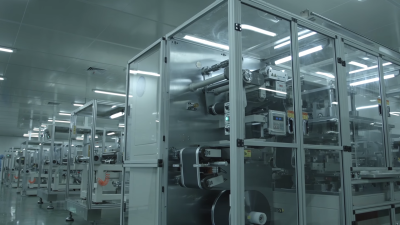
Automotive manufacturers actually outsource the development and production of many components of their vehicles. Your car rides on tires from companies like Bridgestone, Goodyear, and Falken, not Ford, Dodge, or Volkswagen. Similarly, FOX shocks are prized in off-road trucks like the Ford F-150 Raptor, and if you dig into your fuel management system, many of the pumps and sensors are probably made by Bosch.
The fact is, automakers don’t have the capacity to design and manufacture every single little component of their cars. Doing so would rarely make sense, either. Take oxygen sensors, for example. These delicate electronic components are complicated to manufacture, and require specific expertise. Any automaker designing their own would have to cover the full cost of R&D, and economies of scale would be limited by their own vehicle output. However, pretty much every car needs an oxygen sensor, so an outside company that supplies many automakers has an advantage. Their economies of scale are much larger, as they can offset R&D costs across millions of units sold to equip vehicles made by several different manufacturers.
Furthermore, automakers were not in the business of producing batteries by the time electric cars started to hit the market en masse. Starting a battery manufacturing effort from scratch is no mean feat, and would only have added to the difficulty of bringing an electric vehicle to market. Simply purchasing working batteries from an experienced supplier eliminates a whole lot of work, and most automakers have taken this path thus far. Even Tesla has gone this way, sourcing batteries from Panasonic and CATL among other companies over the years. Indeed, Panasonic invested heavily in Tesla’s Gigafactory, and runs much of the production equipment there.
Specialist battery manufacturers have the benefit of decades of experience in both battery chemistry, as well as the fundamentals of manufacturing cells. Batteries are delicate things, and getting their construction even slightly wrong can lead to dangerous fires. Scaling up production is difficult too, and with EVs often requiring hundreds or thousands of cells, monumental effort is required in this regard.
Thus, when it came time to produce electric vehicles, automakers had a choice. They could purchase cells from existing suppliers, with a known-good product and production lines ready to go. Or, they could start building their own factories, hiring battery experts, and begin the process of manufacturing their own cells. The latter route is fraught with hurdles, and requires years of effort to get a usable product available in real numbers. The former choice gets batteries in cars practically from Day 1. For automakers, the decision was easy.
What Could Go Wrong?
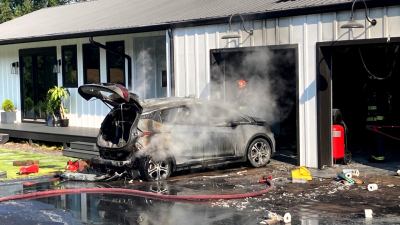
Even the experts get it wrong sometimes, of course. The current Chevrolet Bolt uses cells sourced from supplier LG Chem. Torn anode tabs and folded separator materials in some cells lead to battery fires that destroyed several cars and prompted a huge recall effort. Over 140,000 cars have been recalled, causing brand damage and a huge headache for General Motors. However, as the fault was with the battery supplier, GM were able to point the finger outside, and LG agreed to pay $1.9 billion to cover the costs of rectifying the problem.
Thus, for a whole host of reasons, automakers typically source their batteries from external manufacturers. Car companies didn’t have the knowledge in house to make their own cells, nor did they have the factories to produce them en masse. Sourcing them outside also often provides a cheaper product with R&D costs essentially amortized across several customers. It also means that automakers were able to get to market sooner, and also provided companies with an opportunity for restitution if they were inadvertently supplied with poor product.
There are drawbacks, of course. Doing battery research and production in-house can net competitive advantages. If, for example, a company unlocks the secret to a new battery chemistry, they could produce cars with longer range and more performance than their rivals. However, it’s a risky game with no guarantee of success, and it can take many years to go from a successful lab-built cell to batteries that are ready for automotive use. Then, there’s the sticky problem of kitting out a factory to churn out millions of your special cells a year.
Winds of Change
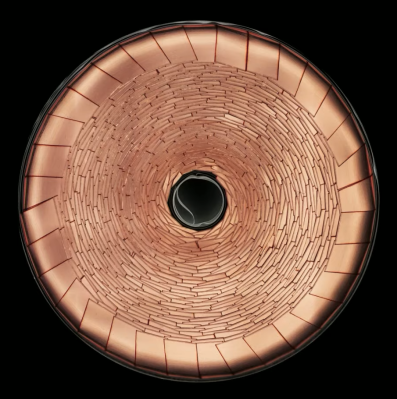
Competition in the automotive world has been fairly level for some time, with emissions regulations and mature engine technology meaning that no one automaker had any wild advantage over another. However, being the only company with access to a new class of battery could be an absolute gamechanger. It’s easy to visualize now—imagine if only one company had access to lithium cells, while everyone else was stuck with nickel metal hydride technology. Cars with lithium batteries now have ranges that can exceed 400 miles. A car built with NiMH cells would be lucky to have a third of that, while being heavier and unable to deliver anywhere near as much current for hard acceleration.
Tesla are starting to look into vertical integration by producing their new tabless cells in-house, a step that it took after over a decade in the EV industry. BMW are doing much the same, investing deeply into solid-state batteries. These technologies could provide range gains in the double-digit percentages, and if built by the automakers themselves, could be unavailable to rivals, providing a major advantage in the marketplace.
As automakers grow more familiar with electric vehicle technology, expect more players to make steps towards producing their own batteries. However, others will continue to see the value in partnerships with established players, investing in new technologies and production capacity at arms length. There’s no one right way in business, of course, but there are always plenty of wrong ones. Traditionally-conservative auto companies will tread carefully as always, while hot upstarts like Tesla will be the ones making the drastic moves.
“Automotive manufacturers actually outsource the development and production of many components of their vehicles.”
For instance, BCS (Body Control Systems -Formerly TRW) develops/tests/manufactures the switches and stalks (turn signal/headlight controls) as well as HVAC and other center dash controls for a variety of automobile mfgrs.
Oh! and lets not forget Takata!
(tongue in cheek)
Oh there’s a blast from the past!
Lucas (the prince of darkness)
Q: why do Brits drink warm beer?
A: Lucas refrigerators…
(literally)
Most, if not all, automakers use subcontractors and “off-the-shelf” parts. This isn’t anything new, or unique to battery operated vehicles.
I think that’s why the oxygen sensor example was given, to show it’s not unique to EVs.
When I read the headline, I thought it was kind of a silly question. Most packaged products integrate components that are outsourced. Apple doesn’t make all the components in their phones (although, they are pulling more and more in-house), HVAC appliances use pumps/compressors/sensors/controls from third-parties, etc. I wouldn’t be surprised if a car manufacturer built only the chassis and *maybe* the engine.
My old employer (an iron foundry) made impellers for GM and valve guides for Caterpillar. They were just two of many customers we took orders from. We could do very small runs and were often used to make OEM replacements in cases where inventory is short. (because we were expensive)
True story. My buddy Ed grinds cams for auto makers at his shop here in Los Angeles.
Some call him “Isky”, but his first name is Ed.
https://www.iskycams.com/shop/
He’s still alive???!!!!
I know he’s getting old.
(Someday I might be able to afford 2 of his cams for my Ford Flathead V8)
Yes, still alive..
Will we start to see standardized batteries for EVs?
In the way that trucks, heavy equipment, forklifts, and golf carts now use large (lead acid) batteries?
Such as Diehard, Optima, and others.
Car engines, transmissions, etc were never standardized. Why should car manufacturers cripple their car designs in this way? Batteries have size and shape, no design will be suitable for every vehicle. Just like brakes and engines and transmissions and windshields and seats and just about every other car part.
Besides the batteries are made up of individual cells and those are standardized.
“Why should car manufacturers cripple their car designs in this way?”
(I should know better than to respond to a comment by X)
…Because they would be crippling themselves if other EV mfgrs decide that the batteries could be “modular” (as Pat mentioned) and easier to replace, if standardized (somewhat)-making the purchase of an EV by one of the other EV mfgrs a more sensible purchase.
You know the only result would be ten competing standard form factors with every car manufacturer making their own.
At least in medium and heavy duty trucks (class 6 and larger) you’ll encounter a somewhat small number of flywheels and bellhousings. I’m not going to say it’s all plug-and-play, but it doesn’t take that many transmissions and interchangable bellhousings to cover 80+% of the heavy trucks out there in the US. But yes, in the consumer space, it’s not that simple.
The battery is big and heavy enough that it has to integrate into the chassis, which makes standardization difficult if not impossible.
The cell geometries are pretty standardized, and the fact that the chemistry gives you the voltage range also means the voltage of each cell is standardized.
The whole-battery assembly makes little sense to standardize, since batteries make up a significant amount of the overall vehicles’s mass and hence have to be mechanically designed “into” the thing. Not to mention they need cooling!
Other than that, how much sense would having the same battery for a BMW 2t SUV in a BMW nearly-sports car or a Toyota compact car or an actually small electric car? Aside from the differences in size, weight and capacity needs, the differences in current capacity, longevity and cost mean that there’s simply no “one size fits more than one series from one manufacturer” market, far as I can see.
You don’t need to standardize the whole freaking thing. Group a bunch of the cells together into a module and do it that way, like manufacturers had been doing for years with 9V-ish scale batteries.
It’s not like the car manufacturers are saying “gee, if we scoot this single 2.5″ cell over here, we can fit it exactly in!” The total volume of the battery is *huge* compared to a single cell. Break it up into smaller modules and handle it that way. Many manufacturers already do that, after all!
“there’s simply no “one size fits more than one series from one manufacturer” market, far as I can see.”
Hmm, wonder why that is. Could it possibly be because controlling the production of the pack allows them to cut off older vehicles by artificially keeping the replacement battery price insanely high?
Nah, that can’t be it.
“Group a bunch of the cells together…”
And there in lies a (possible) solution.
Automobile batteries are classified by “Group”, they are standard, but each Group has different sizes, terminal positions or types.
‘Modbatt’ might be a good thing, it’s being developed by Dennis Palatov. Smaller modules, all with full voltage, simply stack until peak output and/or range are reached.
Check it out, and his car, Palatov D8
Modbatt.com
Dpcars.net
This is why automakers invest so heavily in platforms. They did this long before EV’s, and a platform is essentially a rolling chassis (maybe with different wheelbase options) and a known engine output shaft position. Anything else on top of that is free to be designed, with an entirely different option and body.
Perhaps the most well-known of this is Chrysler’s “K”-platform that had almost every personal vehicle body on it, from sports cars to minivans and compact to station wagon. It also came in metric and imperial variants with European derivatives.
Volkswagen invested heavily in the “MEB” or Modularer E-Antriebs-Baukasten (modular electric-drive toolkit), as it says, a modular electric vehicle platform. Basically this is an still as the old platforms: engine mount point specification, frame, suspension and in this case also batteries. But you can still mount more or different types of batteries into this basic platform, whatever your needs.
This platform is not only for Volkswagen (and it’s group brands), but is also used by Ford.
Also, a platform is almost never 100% identical between models, each model will have it’s own little tweaks, especially as time progresses.
But a successful platform range can easily be used in tens of millions of production vehicles
Yup. Honestly, in some sense the question to this entire article is wrong: it should actually be “why DO automakers make their own EV battery -packs-?”
Because if you go and look at ICE vehicles, there’s massive technology sharing, even between companies. Not even just the chassis/frame, too – everything. Definitely between companies in the same country, but there are plenty of other examples (the GM/Toyota partnership lasted for 20 years).
Obviously EVs are in an early stage, so in some sense it’s surprising that there isn’t *more* joint development/production.
I think we will see this happen for heavy trucks and heavy equipment. Being able to quickly swap battery packs on heavy equipment makes more sense than driving them to a charger in make cases. Just like you don’t typically drive heavy equipment to the fuel pump, a battery truck will delivery fully charged batteries to the equipment.
I think it also makes sense for cars too. I don’t need a 75kwh battery for my daily commute. A 20kwh battery would cover me with a good margin. But for that road trip a few times a year, I’d like to have that extra capacity. It would make much more sense to rent the bigger battery than to own it. Also rental batteries could be tied to the grid as grid storage when not on rent.
For the first generation of mass produced EV’s it doesn’t make sense to have a battery exchange. The market just isn’t big enough yet. But maybe for the next generation.
Sure. Except that the battery is SUCH a huge portion of the car, it’s like saying, “I don’t need to drive fast today, I can switch to a smaller engine.”
And there are manufacturers who are playing with making rapid-change battery packs, but this adds weight, because there’s the weight of the battery (which has to be able to support itself) and the weight of the thing it slides into or bolts up to.
Good point, but batteries are considerably more expensive than pretty much anything else in the vehicle. It’s a good idea, but I suppose the market will eventually decide (if a manufacturer dares to step out of the mould and try it).
“And there are manufacturers who are playing with making rapid-change battery packs, but this adds weight,”
Weight doesn’t matter – it actually helps with drivability/stability. The only thing that matters is the resulting range of the vehicle. If you need to make the battery bigger to get equivalent range for a swappable battery, that’s still a win in every sense.
Long term, larger swappable batteries actually require less cell production than smaller fixed ones that are fast charged, because of the longevity loss from fast charging them.
I’m positive the main reason Tesla moved away from battery swap setups is because even though long term it’d be a win for consumers, it’s both short-term more expensive for consumers (battery swaps are more costly than home charging) and long-term a huge hit for manufacturers (cheap battery swaps mean cars last longer).
I mean, think about it. Tesla worried about range anxiety, so they figure “hey, they can just swap the battery.” Then they switched from thinking about battery swap to a Supercharging network. Supercharging is cheap for consumers (they even do it for free some times) and also shortens the life of the battery (and thus the car). It’s like a freaking dream solution.
Weight matters immensely because the energy density of batteries is actually very poor. It’s another thing that makes EVs more expensive, since they need more stuff all over to handle all that mass. Everything from brakes to pillars in a car have to be built for a heavier car than it actually should be.
The first generation lithium batteries attempted in a car (Nissan, 1996) left the back seats unusable because adding passengers would put the car over its gross weight limit. Since then, the energy density has roughly doubled, but almost all of that advantage has gone into adding more batteries and battery auxiliary systems (heating/cooling/armoring).
The electric shuttle buses in Chattanooga, TN started out in the 1990’s using lead-acid batteries and facilities were installed at the two stations for rapid battery swapping because the batteries (actually a battery of batteries) could not run a bus for a full day of driving and charging took a long time.
Then they switched to NiMH batteries which gave them much longer range and could be topped up fast enough to finish a day’s driving, therefore there was no longer a need for battery swapping.
A few years ago they began the changeover to Lithium-Ion, with enough capacity to drive all day without needing any topping up of the charge.
Aside from an initial Federal grant to get started, the free to ride electric shuttle bus program has been operating 100% on donations and a cut of the downtown parking lot fees. It only runs on a loop of two streets back and forth from the old train station to a second station by the river, and a second loop to and from that station across the river. Wouldn’t want to be competing with free or donate rides against their regular buses that travel around the rest of the city.
There are a fair number of startups/manufacturers tooling up for battery swaps (and NIO has over 100 in China and is spreading into Norway as well) – it’s primarily for the reason you’re suggesting, namely downtime. So main focus is on fleet vehicles, etc. Basically for most consumers, the EV has plenty of downtime anyway so range is the only thing that’s important.
The arguments against battery swapping (other than “swappable batteries makes our cars last too long so we can’t force people to buy new cars”) are pretty hollow, though. The NIO quick-swap vehicles have plenty of range, so if there is a range penalty, it’s a joke. And in the US, the Ample startup works with multiple car models, so the whole “every car is different” thing is just FUD as well.
The cynic in me thinks that the reason that car manufacturers are integrating batteries deeper into the frame is to kill the idea of battery swaps, since they’re a *terrible* idea for the long-term viability of the manufacturer. If you thought they were frustrated with cars running serious maintenance-free for 15 years, an EV would do that in a heartbeat.
It’s also really frustrating because battery swapping can have an environmental benefit as well: you don’t have to super-fast charge the batteries, which is awful for efficiency and the battery’s overall life.
If you look at NIO’s setup in China, it’d be *fantastic* for a low-end consumer in the US, except for the high upfront cost of the vehicle. Shave $10K off the price of the vehicle (don’t need to buy the battery – the cars are still expensive though, since they’re low-volume) and pay $140/month for effectively ~1500 miles of range or so (same cost as gas in the US).
In higher volume, it’d be great – but of course car manufacturers would be in deep trouble if people regularly kept cars for 15 years.
There is no “argument against battery swapping”, but an argument against people who are trying to sell it as an universal solution when it clearly only works in particular cases, such as a bus route where the same vehicles make predictable trips.
In the general case, the number of spare batteries quickly blows out of proportion because you have to stack up for peak demand at each location, not for any theoretical average demand. The main issue is cost of having more than 1 battery per 1 car available, since one battery costs about a third of the price of a new car, plus the cost of the infrastructure, plus the labor costs, capital costs, and private middle-man profits… or, you can limit the service to just a few select locations and routes, but then what’s the advantage? Why bother?
Stacking up for peak demand… yes, but it’s not as if you suddenly start to run low. Every battery someone rent out, you get theirs in return. All you have to do is charge them! Stock levels stay the same.
>but it’s not as if you suddenly start to run low
Depends on what you mean “suddenly”. Already the more popular supercharger stations are getting bogged up around national holidays with lines stretching out for hours because they can’t charge fast enough. The size of your inventory makes the difference whether you can charge up the first battery that came in to replace the last battery that went out.
So, suppose you have a peak attendance of 100 customers per hour. If it takes 1 hour to fully charge a battery, how many batteries do you need to satisfy all the customers? Answer: 100 batteries.
Now, suppose there are about 100,000 service stations around the US that sell gasoline. Convert 10% of those into battery swapping stations, multiply by 100 and you have 1 million batteries just sitting around doing nothing, adding to the expenses of anyone who’s rolled into the swapping scheme in the first place.
Not to mention how much power it takes to charge 100 batteries in an hour. You’re pushing the limits of what the power company can even deliver to a single commercial property without pulling you your own private branch of the electric grid.
Vehicle “manufacturers” are really vehicle assemblers, and it has been this way for 4 or 5 decades.
You have to go back to the days of Henry Ford and the massive River Rouge plant if you want to see true vertical integration of vehicle manufacturing.
Assembly plants are wholly reliant on outside suppliers and just in time delivery.
The supply chain might be lean and efficient but is actually extremely fragile as we have found out over the past few months.
A better article: Why don’t Electric Vehicle makers put more than one charge port on their cars?
1 port = 8 hours charge time
2 ports = 4
3 ports = 2′ etc…?
The port is not the bottleneck in the system. Telsa’s supercharger network comes pretty close to maxing out the charge rate using a single port. It’s something on the order of 50% capacity in 30 minutes, and they don’t support going 0-to-100% in 60 minutes due to heat and battery degradation.
no, it’s that a marginal kilowatt of charge port costs 1/1000th as much as a marginal kilowatt of battery charge power at 250 kW.
Because J1772 connectors can handle WAY more than most vehicle’s onboard chargers can, and upsizing the OBC costs a lot of money that does not benefit many customers, because the cost to a customer of wiring their house for more than 50A 240v (which, using the 80% derate rule for long-term use, leads to 40A for the vehicle) greatly increases past that point.
Note that in Europe, because electrical infrastructure is significantly different than the US (residential 3-phase is a thing there), vehicle manufacturers DO engage in this for Euro-spec vehicles. 11 kW 3-phase (400Y/230v 3-phase with 16A per phase) is extremely common in Europe, with many vehicles supporting 22 kW (32A). In the US, we just have split-phase, so you rarely see more than 9.6 kW (240v 40A), and many vehicles only support 7.7 kW (32A)
For CCS DC charging – in almost all cases, the battery is the limiting factor, because C-rates above 1 for charging get kinda difficult unless you sacrifice energy capacity for power density.
The extended range version of the Ford F-150 Lightning will actually have two charge ports. But not for use with DC fast charging; one port is plenty for that. What the dual ports are for is faster charging for Level 2 charging at home or the office, assuming your location has a hefty enough power drop to handle an 80 amp charging station. That gives a total power delivery of about 19 kilowatts, and will supposedly be able to charge the 150 kWh battery in the extended range model in about 8 hours.
Having 3-phase service does not mean you’re allowed to install a Level 2 charger, because the rest of the house is still connected to the same service and you have to balance the loads between different phases.
I saw a case recently where a customer had bought a car and a charger, but the 11 kW 3×16 Amp charger had to be down-rated to a single phase 3.6 kW because only one of the three phases in the house actually had 16 amps of margin and the power company simply said “no”. In that sense, having a single split phase service is much easier do deal with – if you have the amps, you have the amps.
Balancing the load per house is not really necessary. If you have one-phase power, you will basically just get one of the 3 phases off the local mains, so you’re totally unbalanced. They balance it out for the whole block.
People having residential 3-phase (e.g. for big electric stoves or heating) usually have only that equipment connected to all 3 phases and the rest to only one as usual. So I don’t think this is an issue at all at least not in the Netherlands where I’ve seen this.
It is not necessarily necessary, but the power company wants balanced loads for large equipment such as stoves, washer/dryers, central heating/AC, etc. and the loads need to be distributed such that you’re not popping the breakers all the time trying to turn a vacuum cleaner or a tea pot. Hence you need an approved plan, and you can’t go changing things on your own.
If you have 3×25 Amps going into the house, most likely one of the phases will have a reservation of 6 Amps for a lighting circuit, and the other two will probably have 10 Amps each for room sockets, leaving you with 19 + 15 + 15 Amps margin for installing your stove. A full power cook-top and oven will draw about 10-12 kW with everything on, which would take up the rest of the remaining margin. There’s some rules about how much you can over-load the main breakers assuming not all devices will be on at the same time, but you certainly can’t fit another 3×16 Amp car charger into that setup. You’d need to upgrade to the 50 Amp service, which would require you to upgrade the service box and much of the wiring past that to account for the fact that you can now draw twice as much current without tripping the main breakers (fire hazard). It’s not simply a matter of screwing in bigger fuses.
In many places where cooking and heating with gas is the norm, the electrical connections to houses are feeble and the wiring was never built to support EV charging. This is most of central Europe and UK.
And on the point of wiring: the power company has sized the local distribution circuits according to the size of the main breakers that they’ve sold to all the houses along that circuit, so if people start to upgrade their service amperage, a little bit later the power company starts pulling new distribution cabling, installing new transformers, and increasing the service fees.
EVs in every house of the neighborhood will double or triple the overall electricity consumption and the peak power demand, and, the houses without EVs will be subsidizing the grid system upgrade for houses with EVs, which means income re-distribution from the poor to the rich.
Actually iirc, GM used to own a battery assembly company, but sold it before it became mainstream or profitable. Cheaper to buy battery packs
Making batteries has a lot of potential..
But you’ll need Electrical Motivational Force to get things started.
It seems that motor manufacturers are Ampered by the high charge of setting up their own facilities.
This thread needs a bit more power to bring it on ohm!
You’d certainly find resistance, this is a very poor section
Though with swappable batteries, they might gain some traction~
Maximum torque at zero RPM gets the job done.
>Maximum torque at zero RPM gets the job done.
Which job? One that doesn’t require moving?
Traditional auto has substantial investments in engines. The equivalent for EVs would be the batteries. Sure, the motors and inverters are important… but relatively not nearly as heavy an investment as a combustion engine. So it makes complete sense for the car companies to internalize a lot of the battery design and maybe production. If anything, because it’s the most critical path part of the car.
An inability to get enough batteries is going to do massive damage to the non-Tesla companies in the 3-10 year timeframe. That, more than anything else, will define who wins and who loses. You can’t just add capacity if you need more later, it takes a lot of investment and planning. Most of them have ~$30B plans for enough batteries for ~1 million cars a year in 2025. That’s way too little too late. They’re f**ked. It’ll be the chip shortage all over again.
Tesla is the closest to having in-house battery manufacturing. Their current Gigafactory in Nevada produces battery cells in cooperation with partner Panasonic. Those were originally the 18650 cells that Tesla originally used, and now the larger 2170 cells that they later switched to. Tesla is also working on getting their own larger 4680 cells into production; those will first be made at Giga Texas. But they also signed a contract for LFP batteries made by Chinese company CATL; those will be used in the standard range versions of Tesla’s cars, while the other cells go into longer range models.
Toyota is working on solid state batteries, and will likely to produce them in-house if they ever reach production. The company has demonstrated working batteries. Longevity and safety need to be established; Toyota is unlikely to put their batteries into production cars if they don’t measure up in those ways, because it would destroy their marketing position if they did.
I am waiting for the Graphene revolution that may or may not come. I prefer my batteries to NOT catch fire and burn uncontrollably.
Has NSHTA done crash tests to see how the batteries are protected? I mean if the Pinto was an example of a dangerous power containment system in a car, at least you could put that fire out.
Like fusion power, it’s only ten years away.
Whenever you have a lot of energy stored in a small space there will be some potential for fires. ICE cars, especially gasoline powered ones because it’s more volatile than diesel fuel, certainly do catch on fire, though not as easily as they do in the movies.
That said, some battery chemistries are less prone to fire and explosion. Among the ones currently being used in EVs, lithium iron phosphate (known as LFP or LiFePO4) is the safety standout. The big volume producers of LFP batteries are in China; most of the EVs coming from Chinese companies use them. Tesla now has a contract with Chinese battery maker CATL for LFP batteries; they will be used in the standard range versions of Tesla’s car and in the $25,000 car that Tesla is rumored to be developing. The downside of LFP is that its energy density is lower than lithium batteries that contain nickel (and often cobalt), so it’s not a good choice for cars that are designed for 300 miles or more range.
LFP is a good upgrade for cars (especially hybrids) that originally had NiMH. There’s a company selling new LFP upgrade kits for the 2nd and 3rd generation Prius (that’s export 2nd and 3rd gen which are 3rd and 4th gen in Japan since the actual 1st gen Prius was home market only) and some model of Lexus that used the same modules. It’s also possible to fix up an export 1st gen Prius with these though there’s not yet an “official” kit.
The manufacturer of the kit has figured out how to trick the Prius/Lexus battery management system into using the higher capacity. Normally the system doesn’t allow the battery to charge to 100% nor to discharge too much, because either condition will shorten the life of a NiMH (or Li-Ion) battery.
LFP laughs at such abuse. It easily handles charging to 100% and being drained to nearly zero. Thus a 100 amp-hour rated LFP will really deliver nearly 100 amp-hours when other chemistries will only do about half their rated capacity before risking being discharged too much.
The LFP kit for the Prius also shaves off 40 pounds, which could translate to slightly higher MPG (along with being able to delay running the engine any time the system will run on just electric) or carrying more cargo.
But the kit costs almost $2,000 and its a DIY replacement, you have to take apart an original NiMH battery to replace the modules, wiring, and other components.
For $1,600 there’s a NiMH kit that also has higher capacity and uses cylindrical cells which dramatically improves battery cooling airflow. Same DIY process to swap out the modules and wiring.
Both upgrade kits use half as many modules with 2x the voltage per module. That aids monitoring and diagnostics since the system monitors the original modules in pairs.
What is the name of this kit and who is the manufacturer. I’m interested!
“Whenever you have a lot of energy stored in a small space there will be some potential for fires. ICE cars, especially gasoline powered ones because it’s more volatile than diesel fuel, certainly do catch on fire, though not as easily as they do in the movies.”
This is a bad analogy. Drive around with 4 humans in a car, and there might be more energy stored in the humans’ body fat than the gasoline. Hell, if the frame of the car’s aluminum, there’s *way* more energy stored there!
The reason why lithium batteries are dangerous is the same reason why a tanker truck full of liquid oxygen’s dangerous: when you’re carrying around a bucket-ton of oxidizer, *that’s* when there’s potential for a very bad fire.
Arguably the one EV manufacturer (Tesla) is building their own batteries. The rest are just dabbling in EV production.
Forgetting the primitive electrical grid, (100 years old and no upgrades in sight) total EV transportation is a fantasy.
Sorry to burst yore bubble.
Yes, it sure is a big problem, but not as dire as you portray.
Manufacturers are already making ‘smart’ batteries in their vehicles that can take and give power. Combine that with some smarts on the grid that say “this grid section is underutilised – put cars into charge mode” vs “this section is overutilised – put cars into feed-out mode”.
In addition, most EV chargers are currently in very specific locations, and there are very few of them (in comparison). If chargers (even small ones – like those that run off your wall outlet) were everywhere, you could charge your EV whenever you were stopped (ok, parked). At the office. At the shopping centre. At home. A dozen amps over a day, instead of several hundred amps for a half hour. The grid might be able to cope with that…. maybe….
Sorry Charlie..
(No, really, sorry)
The grid simply will not support 100% EV build out, (Trucks and Cars) Not possible.
California has stated they will ban IC engines, and require all vehicles to be electric.
I’m not sure this was well thought out.
Hybrids still use gas, so are they banned?
Hydrogen Fuel Cell cars derive fuel from crude (See what I did there) oil.
CNG cars, (Honda) derive fuel from Crude.
Electric vehicles use gasoline in two forms.
One, parallel, as in the Prius. Electric and gas powers the car based upon need.
Two, the Chevy solution, as in the Volt with a small IC to just support charging.
The CNG from Honda requires higher compression and forged parts to equal the power output of gas cars.
Fuel cell cars (Today) have limited range and refill locations.
It’s difficult to destroy a extremely large infrastructure and replace it with another one.
Who pays? The government only has funds stolen from the taxpayers.
Ban sales of *new* ICE vehicles. Not banning ICE vehicles. Huge difference.
Cars in California last a long time; longer than they do here in New England because they don’t have to survive winter. It’s common to see cars that are 30 or more years old on the road there, not as cherished collectibles but as daily drivers.
Even if sales of new ICE cars are banned as of 2030, quite a few will still be on the road in California in 2050 unless use of them is also banned (or restricted to limited circumstances, analogous to a registration for an antique car), or unless gasoline becomes unavailable (which is effectively the same as banning their use).
CA banned 2 stroke motors decades ago (simplified, they actually set a maximum displacement for 2 strokes and lowered it over the years).
They will get my 2 stroke mower from my cold dead fingers. It’s awesome. I might have to start buying the oil in Nevada.
Also older cars in CA last a long long time.
New ones fail and are uneconomical to fix at about 10 years old in CA, same as the rest of the world. Granting some car companies are behind VW/Benz/BMW with regards to warranty timer technology. They’ll catch up.
You’re only looking in the rearview mirror.
Because companies are run by finance geeks not engineers.
When you manipulate the numbers and that’s pretty much all you care about you end up running a business in a certain way.
Since finance people are all about cash flow, out sourcing everything makes sense for the share price.
It’s why China now manufactures everything for the west.
Go work for a fortune 500 company with your eyes open. Look beyond the BS they feed you.
“Follow The Money” comes to mind.
Engineers also cut corners on TCI and ROI.
County and state government is often are run by engineers, and not business or finance trained individuals.
Water department, sewage, trash disposal, are all controlled by engineers.
As a public entity, they are tasked with charging for the service based upon actual cost to provide the service.
Then, politicians decide to punish taxpayers by charging above the actual cost, based upon some arbitrary “Excess Usage” boondoggle.
The result is an excess of cash in the old general fund, and “Special” projects get approved based upon financial donations into the politicians kitty.
A story as old as time.
It depends very much on your definition of a “battery” to determine if they are made by the automakers or not.
In the EV world, EV batteries are made in 3 categories:
1.) Cells such as 18650, 21700, or Tesla’s proprietary larger cells. At this point, only Tesla is attempting cell manufacture in house.
2.) Battery modules. This is a bunch of individual cells combined with some cooling/heating mechanism, ready to be assembled into a larger unit. At least Tesla, Lucid Motors and Ford are making their own modules. I haven’t personally seen the other manufacturer’s processes.
3.) Battery packs. This is the final construction, typically a structural frame that the modules are assembled into with interconnects for electrical and cooling/heating, as well as mechanical means to join to the vehicle components. Tesla, Lucid and Ford are making their own packs.
Cells are very common, off-the shelf, not much benefit in an automaker making their own. Tesla could have licensed the idea to Panasonic and had them make them.
Modules are a little more uniform, all the ones I have seen are rectangular bricks, one layer thick made of standard cells. This is done for ease of assembly and so heat transfer can happen directly to each cell.
Packs are very custom, as said before, they need to be designed to fit into the specific vehicle, in many cases, they represent a significant structural component of the vehicle.
I love HAD and visit here just about every day. But this topic is a non-topic. I think everyone already knows that cars are manufactured and assembled by parts built from other companies. It saddens me that HAD feels the need to publish as much stuff as they can without sticking to the original “hacking” topics that made this site what it is today. Most of the information posted here is 1) from other website sources, 2) not relevant to “hacking”, 3) thrown together without much research or content editing. Please don’t insult our intelligence.
At times the good nuggets are in the comments as opposed to the article itself. I would say the purpose pf the article is to get a conversation going by the readers, of which the HAD base is quite diverse, offering various perspectives on the topic. Not everything is DIY and single quantities. The transition from single units to several orders of magnitude, and the associated issues is important.
You are right. This is what makes the difference between a blog and a social platform, and you can think of HaD as a social platform. I’ve noticed something about YouTube: even if a video has thousands of comments, there will be just a few that have hundreds of comments, while the rest have just a few, or none. Now, there’s s structural reason for that happening on YouTube; if you make a comment on YouTube, you get notifications of any responses to that comment, whether they were directed at you or not, so 1st-level comments take on a life of their own. This isn’t the case for HaD, because if you ask for notifications, you get them for all comments on that article. But you still see some sense of that, because all it takes is one comment that brings up an important point, whether the article’s author considered it or not, it can go exponential, and the only thing that saves this from actually happening is that as the number of comments increases, the more chaotic it gets, and eventually people just ignore comments for that article, and may even unsubscribe.
NOT that HaD authors haven’t deliberately written flame-bait articles just to take advantage of this!
Also the HaD notifications don’t always work, so even if you _want_ to know about responses, it might not happen :-)
I think battery technology is not simple when we are dealing with high voltage system, thus it is always safe to have a dedicated team or company for batteries whose job will be standardizing the battery section. Even companies who produces both EV cards and Battery have two separate operating companies inside them for better manageability.
If you look back in history you’ll find that the main reason car makers don’t make everything in house is because that could be a monopoly. Once upon a time airlines made their own planes,engines etc. They were split up for reasons of competition. We seem to have forgotten that these days.
Elon Musk, Gigafactory, scale; think about it…
The answer comes from two decades ago. Back around the turn of the century, the then-Big 3 automakers spun off their parts manufacturing divisions. For instance, Delco became separate from GM. A friend said back then that the auto companies wanted to keep control of car styling, powertrain, assembly and finance. To that I would add, more recently, also control of the driver’s “user experience.” Almost all car parts are manufactured by suppliers as sort of private label products made to exhaustively detailed specifications.
The article makes some good points, but the underlying philosophy of the automakers is that “control the essentials” viewpoint. We’ll see them make their own batteries when batteries are seen as part of the EV powertrain, but not likely before then.
Yeaaaaahhh, no thanks, if Tesla is going to make batteries themselves its going to be subpar quality like the rest of the car, breaking down within 2-3 years? And considering how dangerous ‘breaking’ batteries can be i think i’ll pass. Not that i was really in the market for one anyway, i’m old enough to have learned that any ‘overhyped’ company from the US should be avoided, when im ready for a new & electric car ill go shop in germany, emissions sh*te with VW aside at least they design quality cars and have 100+ of years of experience doing so.
Not hating on America btw, just on their bizarre way of valuing companies/products/people at up to 100x their actual worth & the fact that Tesla’s are now breaking down everywhere, unsurprisingly imho.
Yes, well, I think you’ve bought the hype. I’ve owned two Volkswagens, an Audi, and a Mercedes, and all of them turned out to be junk. Now driving a 24 year old Mercury, that’s been more reliable than any of the German cars.
Now if you want to talk about lithium batteries, the only brand we had problems with when I was working for Apple, were Sony. Not that there were any American brands to choose from, but we didn’t have trouble with “less reliable” Samsung. The point is, company reputations are built mainly on marketing; anybody can turn out trash.
I’m more concerned that Tesla is building computer cars, but doesn’t know how to avoid flash memory wear-out. I’m also concerned that the 4680 batteries they plan to make in their gigafactory seem to rely on pressure contact only, for those many copper tabs to connect to each other and to the terminals.
But if you’re only worried about country of origin, you’re living in a fantasy world.
Everybody wants in on the EV solution.
https://www.youtube.com/watch?v=jCGbbkYLCro
Nissan sells more EVs than Tesla.
BYD make their own battery no?