We’ve been following [James Bruton]’s open dog project for a little while now, and with his considerable pace of work – pandemic or no pandemic – development has been incredibly rapid. The latest milestone is the public release of version 3 (Video, embedded below.) This upgrade to the system adds 3D printed cycloidal gearboxes, removing the previous belt drives. [James] had immense fun tuning the motor controller parameters for these and admits they’re not completely dialed in yet. He notes that the wider gearbox body means that the robots geometry needed to change a little, and the previous belt-drive version may have a bit of an edge, but he’s confident he can make it work (and given his incredible previous robotics builds, we totally believe he’ll nail it!)
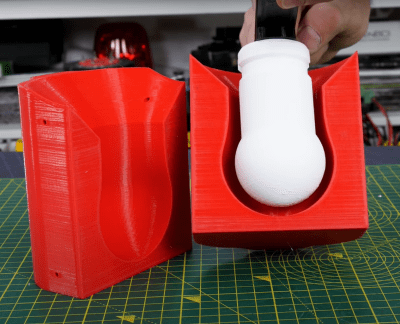
Older versions struggled with slippery plastic feet; the advantage of a predictably smooth contact shape of a rounded foot is somewhat offset by the limited contact patch size, and that means not so much grip on some surfaces. [James] solution was obvious enough – just learn how to make 3D printed silicone moulds and cast a nice rubber foot around a plastic former, and problem solved! Unfortunately he neglected to add some recesses for a lever to get in between the mould halves, so it was a bit of a struggle to separate after curing. A beginner’s mistake that won’t be repeated, we’re sure.
Full source for openDogV3 is now available on the GitHub page. Here’s the playlist for the whole project, as well as direct links for the cycloidal drive development (part1, part2, part3.) But before you all go diving in to start 3D printing your own pooch, [James] tells us that the total cost would be around $2000 all in, with the bulk of that being the motors and ODrive units, so this one for the serious builder only!
We’ve covered robot dogs a fair bit, a particularly nice example is The Dizzy Wolf, and if you’re wondering just why on earth you’d want a robot dog, then Ask Hackaday has you covered as well.
What IF… it was scaled up to the size of something like a horse or ox and the feet modeled alike?
I have my own power “fetish” but power it as you like.
MIGHT it be able to pull a plow or wagon? Or just carry stuff?
Scaling up is much harder than it seems. In fact, it requires a complete redesign. I once tried to explain it in detail here https://hackaday.io/page/1252-small-robots
The materials would have to change somewhat but this core design would I think scale up to that level rather well, its already rather large, pretty heavy, and there is lots of space in the motor hub and gearbox area to add in another gearing down stack if needed as you make it bigger and the motor power to weight and volume doesn’t scale well enough.
I do agree entirely scaling really can make a big difference, but in this case going from largish dog size to something in the lower end of horse sizes at least isn’t going to pose all that much trouble IMO, the design concept can deal with it, just not in 3d printed PLA – I doubt the material is up to the scaled up loads…
One has to wonder if you invert the chassis, could you make spider-like legs instead? Maybe just 6 It would seem way more mobile over terrain.
This is awesome. Cant help think its more robot dog who ate a bowl of crack at the moment. But the quality of the build is phenomenal
“Unfortunately he neglected to add some recesses for a lever to get in between the mould halves, so it was a bit of a struggle to separate after curing.”
Usually, a compressed air supply alleviates said struggle.
I’m actually surprised by the sheer amount of YouTube vids that don’t know this. It also works amazingly well on releasing carbon fiber or fiberglass components from their moulds.
How does that work? Just spray at the mould to get differential cooling? Or do you have to put holes in the body of the mould?
I’ve just used a normal 4in air blow gun, and aim it at the edge of the material in the mold. Maybe a small bit of prying to get the air an edge to peel, but once the air hits it, it’s instantly released.
back in the day, moulded items would have a release agent coating the mould before the resin was cast.
Where is the wiring for this?
The desgn of this version seems to me fantastic. It could be extended to add a dog-like head containing a Ai computer for autonomous operation, lidar and camera sensors with an audio pickup for spoken commands. And what about a wagging tail ?