[Kent VanderVelden] has come up with an interesting AR system to assist operators who are monitoring CNC lathes. (video, embedded, below) The idea is to first produce a ‘frozen’ video stream of the workpiece. This was achieved by placing a high-speed camera above the lathe, and triggering an image capture, synchronized to the rotational position of the workpiece. A high-speed rotary encoder, attached to the tailstock via a belt drive, feeds the current position into an Altera Terasic DE-Nano FPGA eval board. This is then compared to the position from another encoder, doing duty as an angular set point control. The resulting signal is used as the camera trigger to generate a video stream of just the frames where the angle is as selected by the operator, thus giving the impression of a frozen position. The video stream is sent over to a client device based on a Raspberry Pi 4 with a UPS hat, allowing it to be portable.
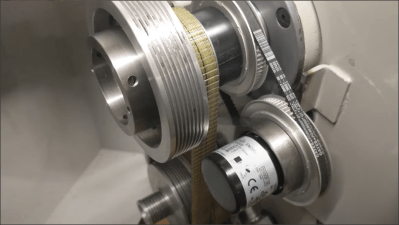
This video stream is overlaid with details of the current machine position, as well as the LinuxCNC G-code being executed and a graphical representation of the operation being performed by the machine. This combined video is then fed to a Vufine VUF-110 wearable, which is minimally invasive, allowing the operator to clearly see the machine of interest. As [Kent] suggests, there are many possible usage scenarios for such a setup, including remote monitoring of multiple operating machines by a single operator.
We’ve seen a few neat machine hacks over the years, here’s a nice project adding a programmable power feed to an old lathe, and since wood lathes are often missing out some DRO love, here’s a nice way to tell them that you care.
I think it’s awesome – such a straightforward way of augmented reality which adds more info but doesn’t get in the way.
While I like the idea, getting the indication that something spinning isn’t spinning is a big red no-no for me in the workshop.
You are allowed to have both eyes open, you know. And you know it’s spinning, as well as hearing and seeing it.
Hearing is easily compromised if you’ve got more then one machine running, and a spinning cylinder doesn’t look very ‘spinny’ at the best of times.
I’ve seen more experienced people then me lose fingertips, and don’t fancy joining the club.
I think a great name for that club would be the
“Tipp-Ex Club”
I almost joined after making a drunken sandwich but it grew back.
I think I’ll have a talk with Doc Edgerton over this.
its designed purpose is for a CNC lathe and it is expressly NOT immersive VR/AR, giving a static view from above. the first fact should start the operator off further away from the spinning part and if the second fact doesn’t clue them in that something is off, then they probably shouldn’t be using machine tools in the first place.
I’m actually not sure what the wearable adds to this project over a fixed display, to be honest.
Well I do not agree personally I run 3 machines 1 lathe and 2 mills as the lathe is running production it would be nice to be able to keep an “eye” on it while running the mills.
So something like this could be quite interesting.
^This!
Having operated several types of machines, can see this actually being used in the machining industries to be honest. Most systems like Siemens and Fanuc already give you a simulated digital picture of what the machine is doing, adding this would give a lot of real sense of what it’s actually doing.
Adding a small indicator on screen would let you see if the machine is running or not, like most have a status indicator(green, orange and red) that does the same.
I can see the value of having the read out build in the glasses, as long as it is not distracting. There are times where I starred at the numbers on my controller when should have been watching the part. Open minded. Also in the future the AR could superimpose the intended part over the stock so one could see if the cutting operation is running as intended.
Love it! The spindle-synchronised camera is a great idea even without the HMD
Personally, I would find this useful, I could view machine remotely while programming simultaneously, but I already have a computer next to every machine the only drawback is I remote in from my office PC which has a better graphics processor which would make this device viable for me but it’s more for the cool factor.
Make this a full machine control override remote and then I’d really want it
5 kilobucks of hardware to do this. Ouch. Nice work, but ouch.
It is a great idea, since at times you want to be able to see the display and the part you are cutting simultaneously.
That is one expensive and complex stroboscope.
This is pretty interesting. I think it would be interesting to monitor the current of the spindle so that if it started you started to take to deep a cut it would stop the machine. also monitoring the cut profile with some sorta probe to do verification would be interesting maybe touch based.