Would you believe the multi-tiered toolbox pictured here started its life as a piece of bog standard PVC pipe? It certainly wouldn’t be our first choice of building material, but as shown in the video after the break, it only takes a heat source and something suitably flat to convert a piece of PVC pipe into a versatile sheet material.
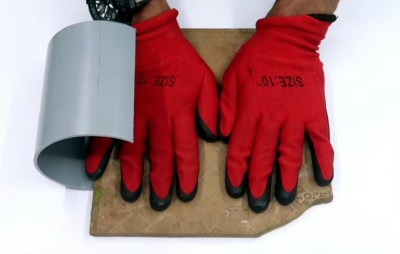
Unrolling the PVC pipe and getting it flat is covered in the first minute of the video, while the rest of the run time is dedicated to building the tool box. Each and every piece you see here, except for the screws and lid hinges, is carefully cut from the PVC sheet. Though we suspect a few more chunks of pipe went into this build than the video would have you believe.
Would we build such an elaborate box if we had to cut each piece of the thing out by hand? Probably not. But then, we can’t deny the final results here are pretty impressive. Incidentally, if you thought those hinges on the top looked a lot like links removed from a watch band…you’d be correct.
Admittedly we’re a bit late covering this one, and under normal circumstances we might have let it slip by given the several million views it’s amassed over the last year. But the central theme of reusing a common material to build something unexpected is solid Hackaday territory, and aligns closely with this year’s Hackaday Prize challenges.
Thanks to [Keith] for the tip.
Can’t believe this get posted and gets bumped on your twitter timeline without some warning about the dangers of heating PVC in the post itself. Not saying there is not a way to do this safely but you should be presenting your audience with that additional safety detail, because without this the project is deceptively simple and safe.
yeah i could smell it through the screen
Isn’t PVC a producer of cancerous fumes? I had a teacher who ranted about how poisonous they are to produce.
PVC=Polyvinyl chloride
“vinyl chloride” it cancerous, which is what is used to produce it.
However, burning it (and maybe heating it?) produces hydrogen chloride, which creates hydrochloric acid if combined with water (and water is everywhere). And that’s nasty stuff that eats everything.
So basically stomach acid? Kinda gross but still low on the ole Dangerous-stuff-ometer.
Stomach acid outside the stomach is pretty dangerous. You certainly don’t want it inside your lungs.
HCl is not a big health problem in the amounts generated by burning. It’s an irritant, but not especially poisonous. It’s the same acid you have in the stomach.
HCl definitiely *will* eat away at things, especially the aluminum gantry in your laser cutter, and for that reason PVC is one of those things that you should never cut in the laser. When you try to laser cut PVC it’s also very smoky and smelly.
And it eats away aluminum very fast, and it’s very agressive. You shouldn’t pour it down your drain either, because it will attach the surface finish on your faucet. And don’t use it near your car because it will attack the chrome coatings, etc. etc.
Burning it in the lab is right out…
PVC cuts very well on a metal shear, so there’s that.
Also, regarding laser cutters, if you want to cut PVC using the laser cutter you can still cut out a template in something else – such as cardboard – and use that to guide a hot knife or other traditional cutting methods.
In reverse, panes of glass used to be formed by a glass blower making a bubble, cutting it open and flattening it with tongs.
On second thought, it isn’t the reverse, it’s nearly the same thing…
(smh)
With flow through ventilation I’ve heated PVC over the slow gas burner and flattened a few pieces to make the languid of flute pipes I make now and then. The flat smooth countertop makes for a quick put another flat on top to flatten and cure with a wet cloth. I have also bent the tube into 180 bends.
Like cooking heating plastics is not harmless some use the oven some stovetop. Electric or gas. Some grill outdoors.
Definitely only for situations where you’re locked in a cave and making a suit of armor using limited available materials.
Looking at their video list, that poor soul has probably made their house, their car, their clothes and most of their food from PVC pipe. “Top Maker” indeed.
Heating PVC above an open flame is quite atrocious.
Not only because of the high risk of over heating , discoloration and very unhealthy fumes, but the heat will also be distributed very unevenly.
It’s much better to heat it in an oven, which has both much better temperature control, and by letting the heat soak in for a bit of time also results in an even temperature.
Apparently PVC has a glass transition temperature of 85 celcius, and in my experience it gradually gets softer at higher temperatures. At 130 celcius it’s consistency is somewhat comparable to the inner tube of a bicycle.
I just did a bit of reading on the ‘net and serrious decomposition starts above 200 celcius, but some websites state it already starts at 135 celcius. I’m not sure what to think about that.
I noticed he used cyanoacrylate ‘super glue’ for the joints. Wouldn’t he be much better off using a PVC primer (clear) and PVC adhesive?
Cyanoacrylate would make for real brittle joints. Drop that box, and it would break apart. Using a PVC glue would actually chemically melt and bond the joints together.
I agree with others here, put that pipe in the oven to gently heat it before flattening. Using an open flame or heat gun makes it hard to distribute the heat evenly.
I like that they helpfully labeled the sandpaper, but not the shiny new microplastics on it.
I’ve heated and shaped pvc a few times with no problems. That being said, once I found vinyl fencing materials at any big box hardware store, I never bothered with reshaping or flattening pvc again.
PVC pipe is a nifty material. The other part of the process is that it returns to the molded (or however it’s made) shape when reheated. You can flatten out a length of PVC pipe, then reheat it and it will return to its original cylindrical shape. Poor man’s memory metal?
Hmmm I thought that was only if the deformation was purely mechanical, if you use heat to reshape it, it stays there.